Tuesday, July 07, 2020, 15:13, Isaac Earle, Development, Other, M9, M9 Q1Q2 service stand Lemo connector wiring
|
The diagram below shows the wiring for the two connectors on the service stand (the wires running from the stand to the power supplies. (see TB23400 for details)
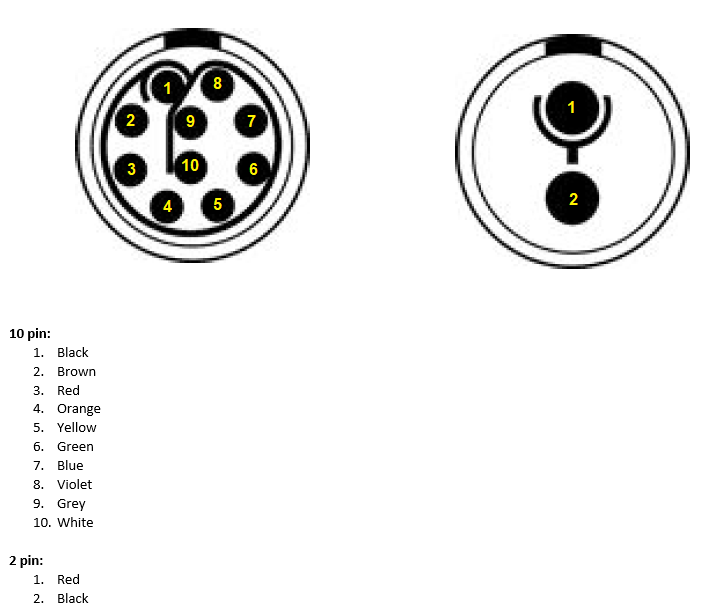
|
Tuesday, July 07, 2020, 13:22, Isaac Earle, Development, Other, M9, M9 Q1Q2   
|
The M9 Q1Q2 magnet assembly lift beam has been installed according to drawing TB23401. The side-to-side as well as beam-axis direction adjustment features were tuned so that the assembly is level when lifted.
Aug 5, 2020 update: All fasteners on the lift beam assembly have been torqued according to the specification on drawing TB23401
|
Friday, June 12, 2020, 13:54, Isaac Earle, Development, Other, M9, M9 Q1Q2 water header installed 
|
The Q1Q2 water header (TB23481) was mounted this morning as per installation drawing TB23400.
Heat shrink tubing was applied to the B1 power cables (two positive, two negative) over the length of cable in the highest field which was showing some signs of radiation damage on the insulation. The tubing used was McMaster-Carr PN 75665K932 (Clear PTFE, 4:1 shrink ratio, 1.0" ID before shrinking), as recommended by Syd Kreitzman. Each piece of tubing is 4' long, and two were used per cable. The first one was shrunk along its full length, then the second piece was only shrunk where it overlaps the first and the remainder was left loose. This was done to minimize time required in the high dose area.
Hand-stacked concrete bricks were removed from the location where the new piping will run to the water header. This is scheduled to take place between July 6-8 |
Wednesday, June 10, 2020, 08:58, Isaac Earle, Development, Other, M9, T2-M9 and M9-B1 flange scan data 
|
Laser tracker scan data from 2017 and 2019 attached as a backup. Original files from Beamlines Group who also keep copies on \\trwindata\experimental support\alignment\T2-M9_data |
Tuesday, June 09, 2020, 17:01, Isaac Earle, Development, Other, M9, Cables and helium leak check line installed to M9 service stand
|
The 10-pin thermal switch wire, 2-pin steering wire for Q2, and a 1/4" copper tube for remote helium leak check were installed through the service chase with the power cables and connected to the M9 service stand. Approximately 10m of extra cable (2-pin and 10-pin) was coiled and left in the cooler section of the service chase after the first sharp bend. The cables and the tubing are currently run as far as the vertical cable tray "waterfall" located near the M11 area. |
Monday, April 06, 2020, 15:02, Isaac Earle, Standard Operation, Target 2, M9, M9 beam blocker returned to beamline
|
The M9 beam blocker was returned to the beamline today using the RH shielded transport flask. The top flange o-ring was replaced before installation.
After installation the "Lift T" assembly was removed, and electrical cable and air supply connected. Correct functionality of the limit switches was confirmed with the control room. Actuation of the beam blocker could not be tested at this time because control takes place through the M9 area ASU.
|
Monday, March 23, 2020, 16:13, Isaac Earle, Maintenance, Other, Other, M9 beam blocker MRO completed
|
M9 beam blocker MRO work was completed in the hot cell today. This included replacement of the main shaft seals and replacement of the air cylinders. Actuation was tested after replacement and the blocker moved smoothly through the full length of travel with approximately 45psi air pressure. It is ready for transport back to the beamline. |
Wednesday, March 11, 2020, 10:29, Isaac Earle, Development, Other, M9, M9 Q1Q2 service stand foot plate installed
|
The M9 Q1Q2 "foot" plate (TB23363) has been installed over the floor plate. A nominal gap between the plates of 1/2" was set before lowering the plate, it was then leveled using the three adjustment bolts resulting in a larger gap. After leveling, the plate was lifted to remove the spirit levels and lock the position of the leveling bolts. The plate was then re-lowered and the tiedown bolt assemblies (TB23383) were installed using 50ft*lbf of torque (about the maximum practical amount with standard 20' pole tools) |
Wednesday, March 04, 2020, 13:42, Ron Kuramoto, Repair, Other, Other, B/L 1A vacuum air leak repair
|
A 4” Marmon aluminum blank-off flange and o-ring were replaced on the south port of the T1 target monolith vacuum vessel. This port was accessed from the 1A Service Tunnel were the repair took place.
See the attached pdf file “1AT1 Vacuum Leak Repair-Feb2020” for a summary of the repair. |
Friday, February 28, 2020, 09:06, Isaac Earle, Development, Other, M9, M9 Q1Q2 service stand floor plate installed
|
The M9 service stand floor plate (TB23351) was installed in the M9 pit yesterday. Prior to installation all 5 threaded inserts were tested using a 1/2"-13 stud tool on an RH pole. The west most hole (shown in red below) had damaged threads and the stud could only be threaded in 2 turns. All other locations (shown in green) had usable threads with 6-8 full turns possible with the stud tool. The plate was installed using RH floor plate bolts (TB23382) at all four locations with viable threads. The bolts were torqued to 30 ft*lbs which on a bench test was shown to fully compress the belleville washer. The standard torque spec for 1/2"-13 stainless bolts (43 ft*lbs) was not used to allow easier disassembly in the future.
 |
Monday, February 10, 2020, 14:51, Isaac Earle, Maintenance, Other, Other, T1-MK2 target and M9BB moved
|
The T1-MK2 target was moved from the hot cell to Hole #5 in the storage pit. The M9 beam blocker was then moved from the beamline to the hot cell for MRO work. A field of 14.4mSv/hr was measured at 0.5m from the beam blocker during removal. |
Wednesday, February 05, 2020, 14:53, Isaac Earle, Maintenance, Target 1, Cooling, T1 & T2 cooling package MRO work completed
|
Annual MRO work on the T1 and T2 cooling packages is now complete. The following tasks were performed:
- Water from both packages drained to the South TNF holding tank (samples taken)
- All Proteus paddle wheels, shafts, and o-rings replaced (5 each at T1 and T2)
- All Cuno filters changed
- Archived data for all sensor readbacks inspected. Only faulty sensor was B1A:T1CS:FGDEM
- Both packages refilled and restarted; Operating smoothly; Inspected for leaks, none found; Demin flow at ~1.0gpm
- B1A:T1CS:FGDEM readback is fixed with new paddle wheel
- South TNF holding tank water released after approval from RPG
- Old filters added to plastic pail with other T1/T2 filters located directly north of the BL1A blocks boot-box area
- Active water from filter canisters dumped into the RH lab active sink
|
Thursday, January 30, 2020, 17:55, Isaac Earle, Repair, Target 1, Target, T1-MK2 target assembly repair completed in hot cell    
|
The following work was done to the T1-MK2 target in the hotcell between the dates of May 24, 2019 - Jan 30, 2020 (See E-Log #251 for further information):
- May 24: Flushed position 2 with water, purged all positions with air. Left air running through position 0 over the weekend
- May 27: Switched to position 5, left air running to dry out bellows
- May 28: Started pump out with cold-trap; Reached "fine test" (TP pressure < 10E-2 Torr) after ~10-15 minutes, left for 2 hours, removed ice build-up then restarted leak detector;
Down to 1.0E-3 Torr TP pressure and 1.0E-8 Torr*L/s after ~10min
Leak checked with 5psi helium, ~0.5s spray: Response at lower delta seal right side (when facing ladder) up to 3.8E-6 Torr*L/s and drift responses from nearby locations
- June 27: Position 1 target removed - no issues, required light tapping with hamme
Position 4 target removed - lots of hammer hits required
Both target beam spots photographed. Saw what looks like hole on Position 4 entrance window (see attached photos)
- July 8: Protect monitor inspected visually using Nikon level by Dave Cameron and Shengli Liu - Nothing abnormal observed
Electrical check w/ multimeter: all OK
Observed ground to HV plates while moving ladder from Position 5 to 0 - all OK
Observed ground to HV plates while moving profile monitor IN then OUT - all OK
Found intermittent short from HV to ground when shaking the target assembly or tapping the protect monitor cassette: must replace
- July 18: Cleaned Position 1 and 4 Swagelok sealing surfaces on the target ladder using the Dremel tool with burgandy Scotchbrite
Ready for new targets to be installed
Plugs installed at Position 4
- July 24: Target #105 installed at Position 1
Started leak detector pumpdown with cold trap; Only pumped down to 4.0E-3 Torr; Big helium response at lower right delta seal (10E-5 Torr*L/s range)
Concluded that the leak got worse during the target replacement (likely from the hammering required to remove Position 4 target
Tightened bolts for lower right delta seal then repeated leak check: same results, therefore must replace seals
Received replacement protect monitor cassette from Probes Group and installed
- July 29: Probes group did blip test on new protect monitor - all OK
We repeated the test for shorts with shaking and tapping on the target assembly and monitor - no shorts observed
Concluded that protect monitor issues is now fixed
- Early Jan 2020: Lower cone and plate removed, ladder removed (old style w/o plate at top)
Removed seal spacers, the one for the lower right delta seal was stuck, had to use a flat edge screwdriver as a wedge with aluminum hammer to dislodge
Removed delta seals, observed some deposits or corrosion at lower right seal location
Cleaned spacers using Scotchbrite on Dremel
Used 3D printed jigs with glued on burgandy Scotchbrite to clean sealing surfaces (no air ratchet or dremel, polished with manipulators until a clean shiny surface was produced)
Had to remove bolts for the ladder flanges to clean the surfaces, and when reinstalling one of them it cross threaded and couldnt be removed
Bolted instead at different hole locations (still at opposite sides of flange) but also had to switch bolt locations on upper seals to do this because bolts will interfere if using same threaded hole
Eventually got everything back together with new delta seals installed (TBP0454B, machine shop order #44138)
Note: the upper delta seals were not disturbed - new bolts installed and torqued before old ones were removed
- Jan 22: Leak check, pumped with cold trap: down to 0.0E-10 Torr*L/s and 1.0E-3Torr TP pressure after 9.5 minutes
Using 5 psi helium, 0.5s spray; No response at any previous locations; Very small drift response up to 0.5E-10 Torr*L/s
Concluded that leak is fixed
- Jan 26: Base plate and cone reinstalled - no issues
- Jan 30: David Kyle and Shengli Liu re-tested the profile monitor and protect monitors - No issues
Measured vertical and horizontal positions for all targets and protect monitor, updated measurements sheet (PDF attached)
Ladder moved to Position 0
Target assembly ready to be moved to storage pit
|
Monday, January 20, 2020, 16:07, Isaac Earle, Other, Other, Other, Second 55-gal drum moved to cyclotron east vault tunnel
|
The second (and final) 55 gallon drum containing active items from the Meson Hall East Hot Cell was transported today from the Warm Cell to the Cyclotron East Vault Tunnel. The updated form is attached. |
Tuesday, December 17, 2019, 12:39, Isaac Earle, Standard Operation, Other, Other, 55 gallon drum and old M9 service stand moved to Rad Waste Pit    
|
The following items were moved today from the Warm Cell to the Rad Waste Pit for long term storage:
1. A 55 gallon drum containing various active components from the East Hot Cell. The drum was labelled on the body and lid with the identification number RWC-55-01-2019.
2. The old M9 Q1Q2 service stand, which was removed from the beamline in the 2019 winter shutdown
Photos taken during the move are attached, as well as a copy of the loading record form for the drum. The form has also been given to RPG.
A second drum (RWC-55-02-2019) remains in the Warm Cell, and will later be moved to the cyclotron vault tunnel for storage. It was resurveyed after the first drum was removed and deemed too low-level for storage in the pit (300uSv/hr at 0.5m) |
Monday, June 24, 2019, 14:29, Isaac Earle, Development, Target 1, Target, T1 and T2 target alignment frames overhauled 8x
|
The following work was completed on both the T1 and T2 target alignment frames
- One of the short taper pins on the top of the frame was swapped for a longer version to simplify flask alignment to the frame (now one pin can be aligned at a time instead of both concurrently)
- Three permanently mounted cameras installed to view east/west alignment, north/south alignment, as well as hook, latch, and door position
- LED strip lights installed on the bottom of the frame for better illumination during alignment of target devices
- All video and power signals routed through a single connector (9-pin CPC) for ease of use
- Frame painted with blue Rustoleum metal paint
- Hole positions, alignment orientation, camera position, etc labeled on frame
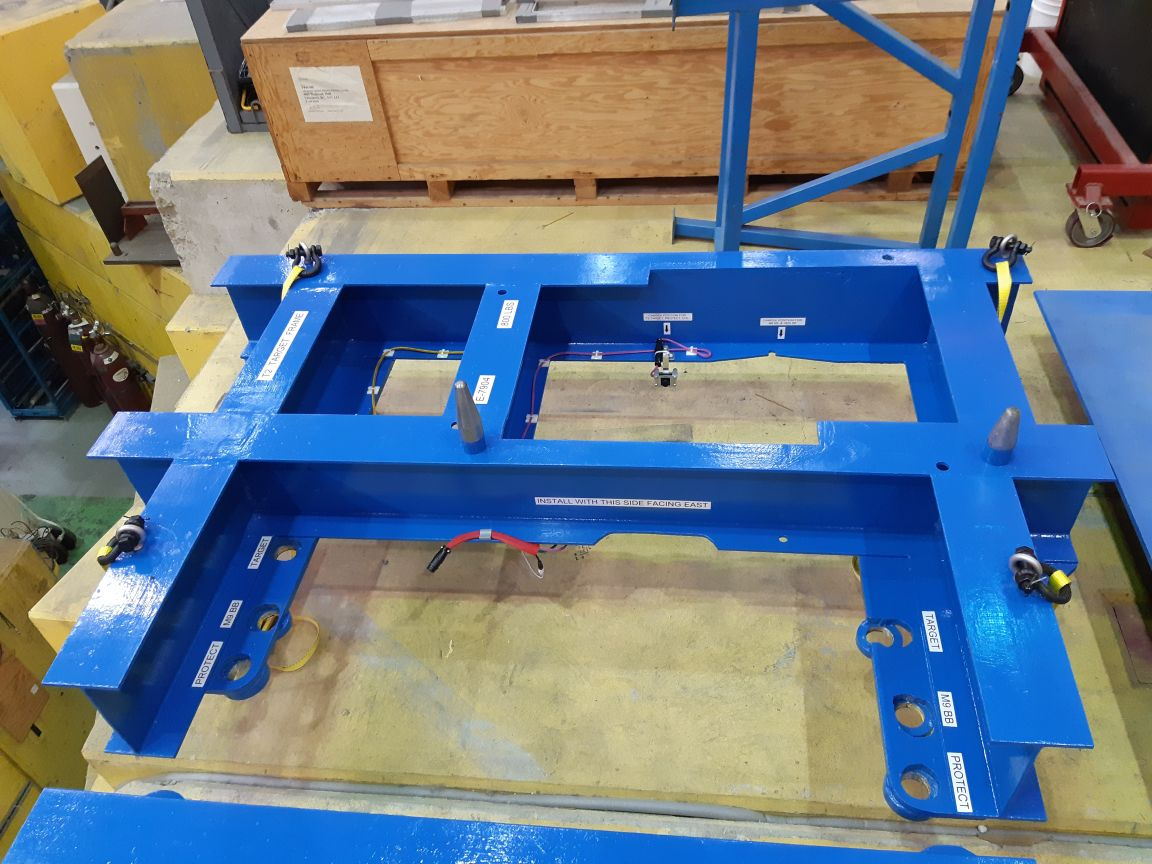
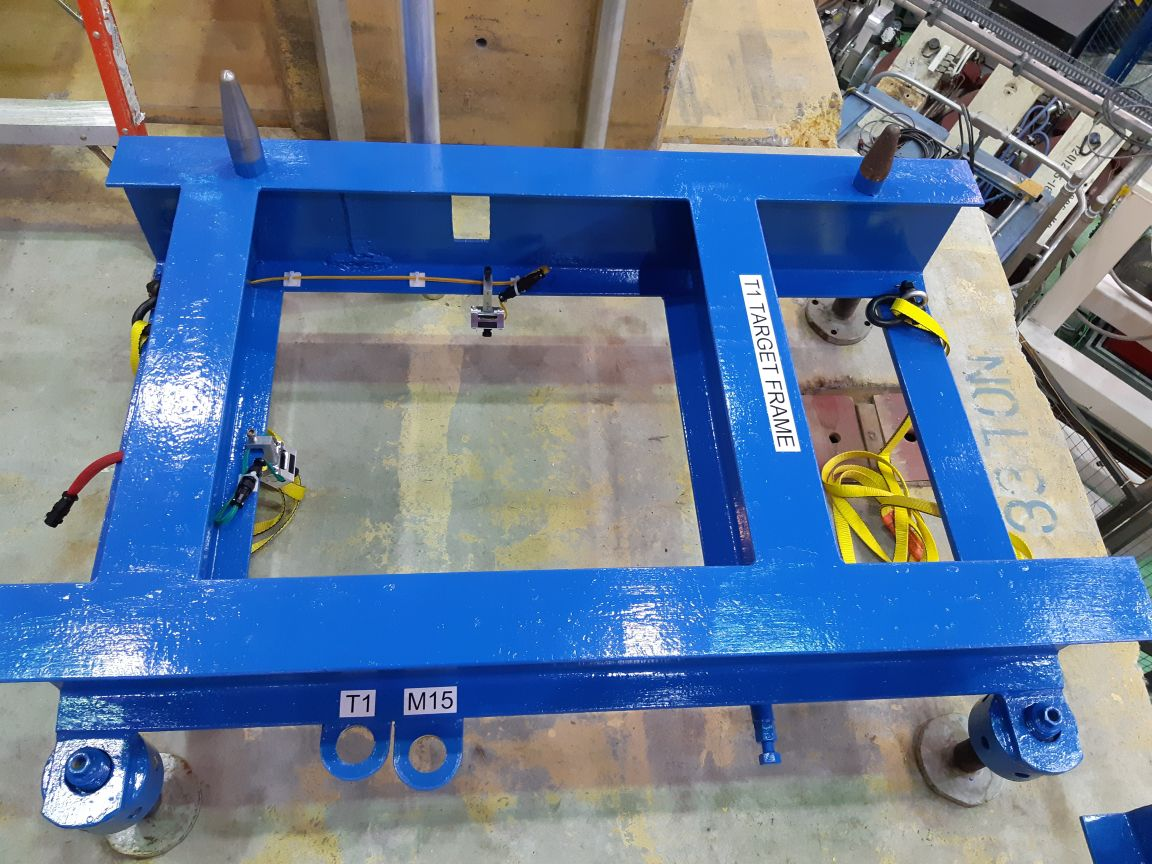

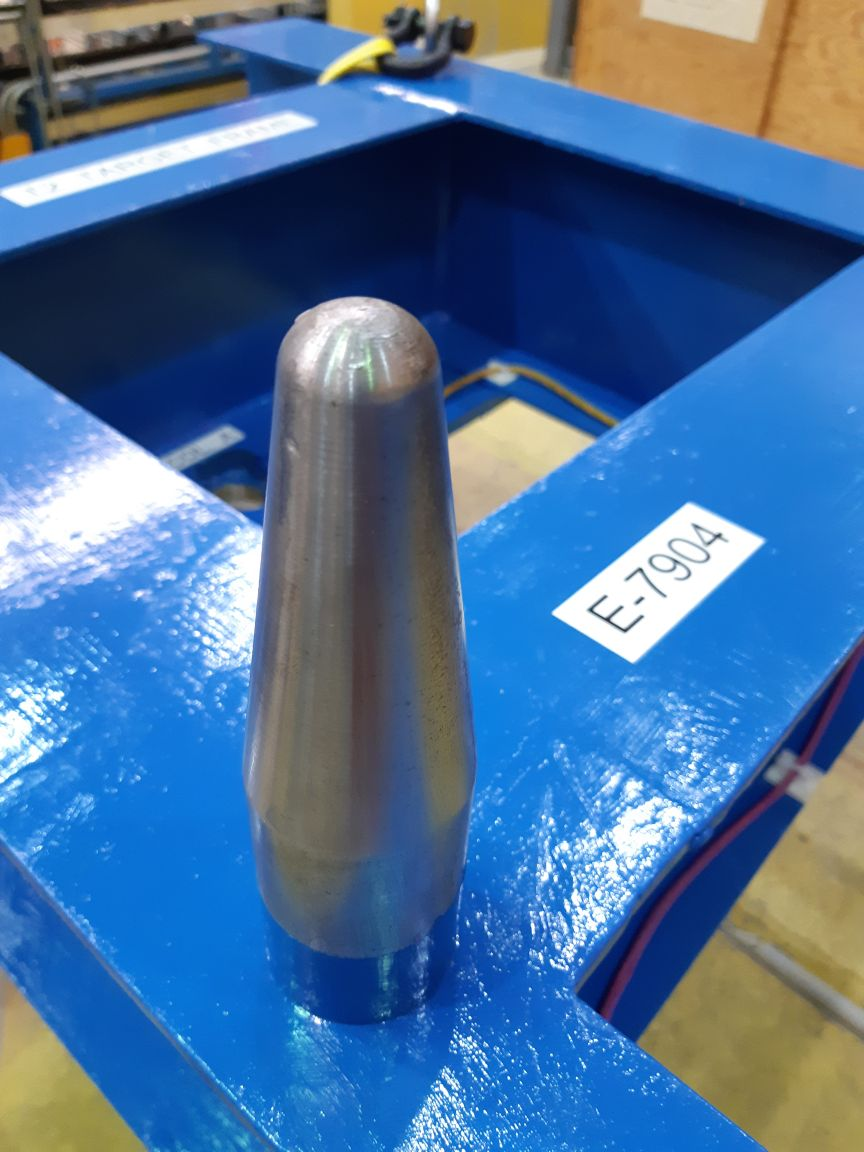
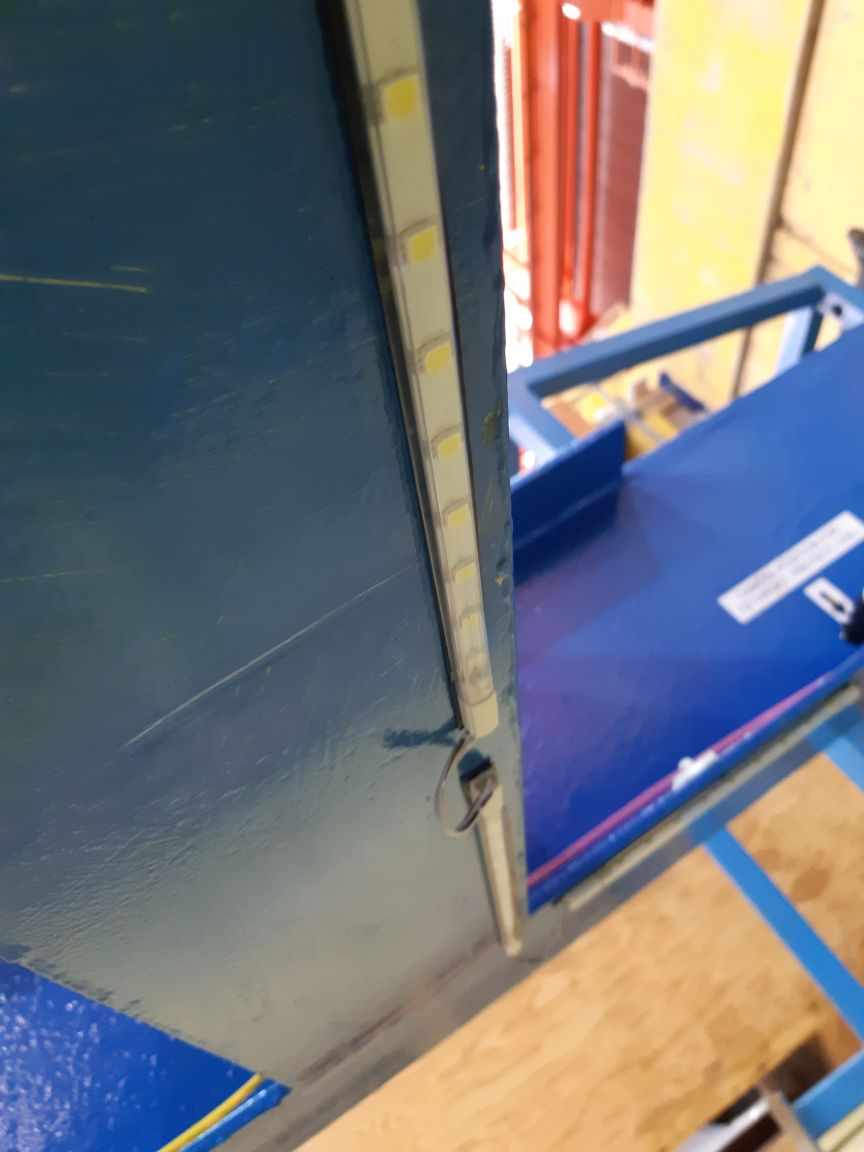

|
Wednesday, May 22, 2019, 14:25, Isaac Earle, Repair, Target 1, Target, T1-MK2 target moved to HC; T1-MK1 target moved to BL
|
After extensive testing over the last 2 weeks it was determined that the protect monitor on the T1-MK2 target had an issue with intermittent shorting between the high voltage line and ground (movement of the target ladder was causing the short to come and go).
On the May 21 maintenance day the T1-MK2 target was moved from the beamline to the hot cell (102mSv/hr @ 0.5m). The T1-MK1 target was then moved from Storage Pit location #3 to the beam line (as in the past, alignment of the flask to the #3 position hole was challenging, and the flask had to be suspended above the alignment pins to achieve alignment with the hole - In the future this storage pit location should be avoided).
Cameras were mounted on the T1 alignment frame for remote viewing of alignment with the hole as well as flask door position and hook latch position. The camera locations chosen provided useful views and did not interfere with the target or frame. After procurement of additional mounting brackets the cameras will be permanently installed at these locations (already completed on the T2 frame).
The target moves were completed successfully, vacuum pump-down was normal, and electrical checks of the T1-MK1 profile monitor and protect monitor were normal. When start-up of the cooling system was attempted problems were encountered with the control system. Multiple channels on the digital output module were shorting, causing the power supply fuse in the PLC cabinet to blow. This was eventually tracked down to two damaged cables (B1A:T1CS:SVSEC and B1A:T1:SVCOL) which somehow had been crushed during removal of shielding. The cables were replaced and all cables secured as much as possible in the vertical chase leading up from T1. After replacing the cables we discovered that the digital output for the SVSEC signal was stuck in 'drive' status. The module was replaced and then the control system was working normally (approximately 11am on May 23rd).
The T1 cooling system was started (no change to 1ACG2 vacuum), ladder movement through all target positions was tested, and profile monitor actuation was tested. Updated target info sheets were submitted to Ops (attached in PDF format) and XTPAGE 7L was updated.
Diagnosis and repair of the T1-MK2 target will take place in the hot cell over the coming weeks.
Cyclotron Fault #12266 was returned. |
Tuesday, April 16, 2019, 15:35, Keith C Ng, Repair, Other, M9, M9 project post shutdown summary
|
Completed work at m9 beam line:
- Removed existing service stand and associated cable and water services. Legacy b1 water services still need to be removed for future magnet installation. Old service stand is currently in warm cell waiting for disposal.
- M9 Q345 and vacuum roughing line were cleaned by CMMS group.
- M9 B1 is disconnected but remains in beam line ready for removal and refurbishment for 2020 shut down. Relevant ports have been sealed off.
- New Q1 Q2 baseplate was test fit and did not fit with guide post bolted in place, interferes with T2 port blank off plate.
- 3d lidar scans of magnet space were done.
- Leica tracker data was taken of the holes in the poured in place concrete pad.
Photos from shutdown are on remote handling group folder, under "\\trwindata\groups\remote handling\Photos\2019\2019 m9 project" |
Tuesday, February 26, 2019, 10:55, Isaac Earle, Maintenance, Target 1, Cooling, T1 and T2 MRO work and solenoid valve change summary
|
The following work was completed between Jan 16 - Feb 19, 2019:
- T1 and T2 cooling packages drained to South TNF holding tank, water sampled and tested, released after approval from RPG
- T1 resin can swapped
- All Cuno filters changed at T1 (3 total)
- T1 inlet (T1CSPGIN) and outlet (T1CSPGOUT) pressure gauges replaced (archived data on EPICS indicated both starting to fail)
- T2 target water Cuno filter replaced
- All T1 and T2 solenoid valves changed to new models without power management circuit which will hopefully solve the problem of frequent failures (SASP0670)
Parker brass body valve 73218BN4UN00 with solenoid C222C2 solenoid used for T1CSSVSEC and T2CSSVSEC
STC stainless steel body valve 2S160-1/2-2-D with solenoid 2W200C-2-D used for T1CSSVTGT, T1SVCOL, T2CSSVTGT, T2SVCOLA, T2SVCOLB
Necessary changes to PLC BOP wiring made by Tony Tateyama
All new valves confirmed operational and leak tight
Cyclotron Fault #11955 returned
- T1 and T2 profile monitor air cyclinder flow control valves replaced with new models tuned to ~1/8 turn open. Part is Rego F125B (see PO #3044305)
- T1-MK2 profile monitor air cylinders replaced (both were leaking through the top seal)
- T1 and T2 profile monitor actuation checked - both move in and out slowly and smoothly
- M20 BB actuation checked - movement is slow and smooth
- T1 and T2 ladder movement checked - both ok
- T1-MK2 male Hansen fittings replaced as well as female Hansens which connect to them (these are the last remaining Hansen fittings to be replaced at T1/T2)
- Both cooling packages filled and started, now running smoothly. Inspected for leaks (none found). No change to 1A vacuum when packages started
Note 1: The T1 package water pump is slightly noisy when running (it has been this way since the replacement pump was installed last year) - Will investigate further at a later date
Note 2: In the week of Feb 11-15 Vacuum Group pressurized the T1 target cooling circuit with 30psi helium to try to find the vacuum load on the T1 volume. This was done twice with the beamline vented for a few hours in between in case water had frozen at a leak location. The conclusion after testing is that the T1 cooling water is not the source of the vacuum load at T1. Helium was also sprayed all around the top of the T1 monolith (T1 target and M15 permanent magnet) - there was no response on the leak detector
My total dose for this work was 0.15mSv |
Friday, January 25, 2019, 10:53, maicodallavalle, Repair, Other, Cyclotron electrical, Cyclotron Elevating system Motor electrical wire repairs
|
2018 Cyclotron lid up problem. Station #9 was found to have the motor wires along the beam plain had damaged wire insulation. There were bare wires in the conduit resulting in the wires shorting out. The wires were repaired with a quick short replacement. Lid went up for in tank work. After lid down the problem was investigated. We checked the radiation levels at all of the stations to come up with a plan to determine witch of the stations had the highest levels. We found that stations 1,3,5,7,9, and 11 had the highest levels. Station 1 was inspected and all wires were replaced to the T elbow. Station 3 all wires were replace to the T elbow. Station 5 all wires were replaced to the T elbow. Station 7 all wires were inspected and were in good condition and put back into place. Station 9 all wires including syncro were replaced all the way to the junction box. Station 11 motor wires were good, but the jog wires and the syncro were replaced to the pull box. All of the jog switches on stations 1,3,5,7,9,and 11 were falling apart when wires were inspected. New switches were ordered and assembled. At the start of 2019 shutdown all jog switches were replaced on stations 1,3,5,7,9, and 11. After all the jack work was finished the jog switches were check and were working well. |
|