ID |
Date |
Author |
Category |
Type |
Specific |
Subject |
232
|
Wednesday, January 10, 2018, 17:45 |
Isaac Earle | Standard Operation | Target 2 | Target | T2-MK2 beam spot photos, M20BB moved to storage pit |
The T2-MK2 target was moved from the beamline to the hot cell on January 8th. The field at 0.5m was 130mSv/hr. Photographs of the beam spot of the Position 4 target are attached below. This is a 12mm beryllium target (ID: "JUL.06#4). This is the only target on the T2 ladder that has seen beam since it was installed on October 10, 2017. A shielding plug was installed on the T2 flange. A new 5cm target will be installed on the T2-MK2 ladder after fabrication is complete. Regular testing and maintenance of the target assembly will also be performed before it is returned to the beamline.
The M20 beam blocker was also moved from the beamline to Hole #7 in the storage pit. The field at 0.5m was 22mSv/hr. A blank-off plate was installed on the M20BB flange (no o-ring). Seal replacement and general inspection/testing will be performed before it is returned to the beamline.
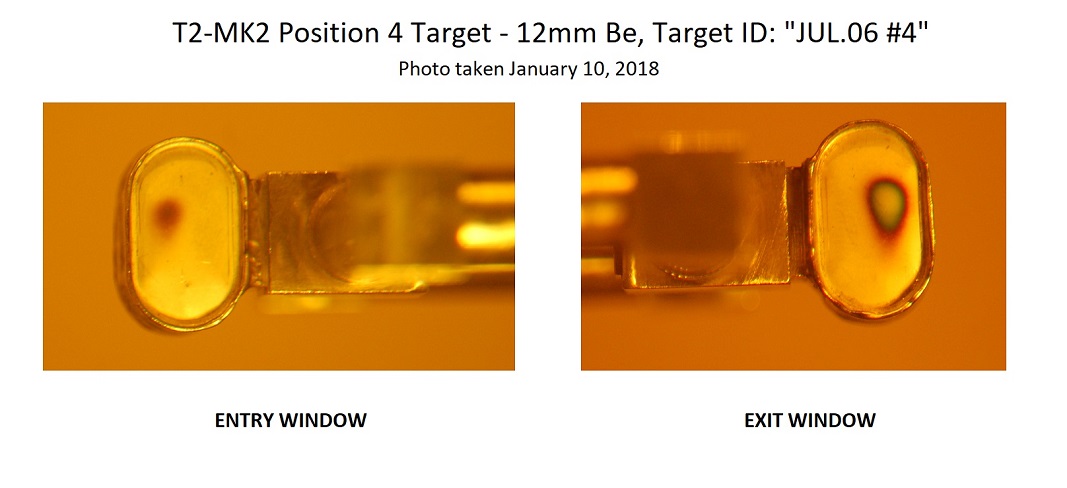
|
Attachment 1: T2-MK2_Position_4_beam_spot_photo_-_12mm_Be_-_Jan_10_2018.jpg
|
|
235
|
Friday, April 06, 2018, 15:05 |
Isaac Earle | Standard Operation | Target 2 | Target | T2-MK2 target MRO |
The following is a summary of MRO work done on the T2-MK2 target during the 2018 shutdown:
Jan 8:
- Target moved from beamline to hot cell; 130mSv/hr at 0.5m
Jan 10:
- Position 4 (12mm Be) beam spots photographed. Spot is slightly high and left (from beam's eye view), also smaller and rounder (less eliptical) than usual - See E-Log #232
Jan 11:
- Flushed position 0,1,2,3,4 with water, then 4,2,1,0 with air
- Left with 10psi air running overnight in Position 0
Jan 12:
- Moved to position 4, 10psi air running through over the weekend to dry cooling lines
Jan 15:
- Pumped out water lines with leak detector
- Frist pump down blanked off tubing and new vac hose (no LN2): ~15 mins to get to 0.0E-10 TorrL/s
- Pumped out target w/ cold trap: ~7 mins to get to 0.0E-10 TorrL/s (left pumping for 2 hours)
April 2:
- Removed plugs at position 3 and 5
- Pressure tested, leak tested, and recorded alignment dimensions for first batch of new 5cm targets (#301, 307, and 309) - Records stored with targets in RH lab office
- Installed new 5cm beryllium target #309 at Position 3, and target #307 at Position 5
- Helium leak check on target water system: Baseline 0.0E-10 TorrL/s leak rate, 1.0E-3Torr, half second helium applications @ 4psi
Positions 1, 2, 3: no response
Positions 4, 5: up to 5.0E-10 after delay (appears to be drift)
Lower 'C' seals: no response
Upper-left 'C' seal: up to 1.2E-9
Upper-right 'C' seal: up to 2.4E-9
Left bellows: up to 6.0E-9
Right bellows: up to 3.0E-9
- Deemed water leak tight and ready for use (based on previous leak check results and operating experience)
- Tested all target position micro switches: all OK
- Tested profile monitor limits: both OK
- Tested profile monitor actuation: off down limit @ 5psi, on up limit at 35psi
- Tested potentiometer: slightly noisy signal from position 0 to 2 (no change from before)
- Measured Position 3 and 5 elevations
April 3:
- Measured Position 3 and 5 horizontal alignment wrt ladder
- Quick repeat of leak check: no change
April 6:
- Target returned to beamline
- Vacuum pulled on T2 area (1ACG4 down to 5mTorr in ~2.5hrs, was 4mTorr before venting yesterday)
- T2 cooling package started with target at Position 0 - no change to T2 vacuum
- Target information sheet and elevations data delivered to Ops
- XTPAGE 7L information updated
|
238
|
Thursday, May 10, 2018, 15:23 |
Isaac Earle | Repair | Target 1 | Target | T1-MK2 protect monitor and profile monitor replaced |
During first injection of beam down 1A problems were encountered with the T1 protect monitor. Testing was done by Probes Group from the mezzanine leading to the following investigation and repair work.
May 9th:
- T1 area uncovered, Probes Group performed testing at the top of the monolith confirming that the problem was below the vacuum flange
- T1-MK2 target moved from the beamline to the hot cell. Measured field 800uSv/hr at ~0.5m
- Visual inspection of protect monitor performed: No obvious issues with monitor plates. Some small impact holes visible on exit side of monitor, similar to damage on the previous monitor from Oct 2015
- Electrical check performed on old protect monitor in hot cell, confirming the previous results
- Failed protect monitor removed, resistor pack installed and tested with expected results
- Profile monitor insulation found to be blackened and cracking, so the profile monitor cassette was also removed
- New protect monitor and profile monitors installed
- Electrical check performed on both monitors at the hot cell: Results good for both
May 10th:
- Vertical and horizontal positions measured for the new protect and profile monitors
- Profile monitor actuation tested: started moving ~10psi, fully actuated ~50psi, monitor limit switches ok
- Measured total resistance of potentiometer: 20.26kOhms
- Target windows inspected and photos taken (stored on Isaac's hard drive), nothing unusual encountered
- T1-MK2 target returned to beamline, vacuum pumped down without issue
- T1 cooling package started fine with no change in vacuum
- T1 profile monitor actuated in and out. Movement smooth and slow
- Electrical check done on protect and profile monitors from mezzanine: both good |
251
|
Wednesday, May 22, 2019, 14:25 |
Isaac Earle | Repair | Target 1 | Target | T1-MK2 target moved to HC; T1-MK1 target moved to BL |
After extensive testing over the last 2 weeks it was determined that the protect monitor on the T1-MK2 target had an issue with intermittent shorting between the high voltage line and ground (movement of the target ladder was causing the short to come and go).
On the May 21 maintenance day the T1-MK2 target was moved from the beamline to the hot cell (102mSv/hr @ 0.5m). The T1-MK1 target was then moved from Storage Pit location #3 to the beam line (as in the past, alignment of the flask to the #3 position hole was challenging, and the flask had to be suspended above the alignment pins to achieve alignment with the hole - In the future this storage pit location should be avoided).
Cameras were mounted on the T1 alignment frame for remote viewing of alignment with the hole as well as flask door position and hook latch position. The camera locations chosen provided useful views and did not interfere with the target or frame. After procurement of additional mounting brackets the cameras will be permanently installed at these locations (already completed on the T2 frame).
The target moves were completed successfully, vacuum pump-down was normal, and electrical checks of the T1-MK1 profile monitor and protect monitor were normal. When start-up of the cooling system was attempted problems were encountered with the control system. Multiple channels on the digital output module were shorting, causing the power supply fuse in the PLC cabinet to blow. This was eventually tracked down to two damaged cables (B1A:T1CS:SVSEC and B1A:T1:SVCOL) which somehow had been crushed during removal of shielding. The cables were replaced and all cables secured as much as possible in the vertical chase leading up from T1. After replacing the cables we discovered that the digital output for the SVSEC signal was stuck in 'drive' status. The module was replaced and then the control system was working normally (approximately 11am on May 23rd).
The T1 cooling system was started (no change to 1ACG2 vacuum), ladder movement through all target positions was tested, and profile monitor actuation was tested. Updated target info sheets were submitted to Ops (attached in PDF format) and XTPAGE 7L was updated.
Diagnosis and repair of the T1-MK2 target will take place in the hot cell over the coming weeks.
Cyclotron Fault #12266 was returned. |
Attachment 1: T1-MK1_target_info_sheet_-_Installed_May_21_2019.pdf
|
|
252
|
Monday, June 24, 2019, 14:29 |
Isaac Earle | Development | Target 1 | Target | T1 and T2 target alignment frames overhauled |
The following work was completed on both the T1 and T2 target alignment frames
- One of the short taper pins on the top of the frame was swapped for a longer version to simplify flask alignment to the frame (now one pin can be aligned at a time instead of both concurrently)
- Three permanently mounted cameras installed to view east/west alignment, north/south alignment, as well as hook, latch, and door position
- LED strip lights installed on the bottom of the frame for better illumination during alignment of target devices
- All video and power signals routed through a single connector (9-pin CPC) for ease of use
- Frame painted with blue Rustoleum metal paint
- Hole positions, alignment orientation, camera position, etc labeled on frame
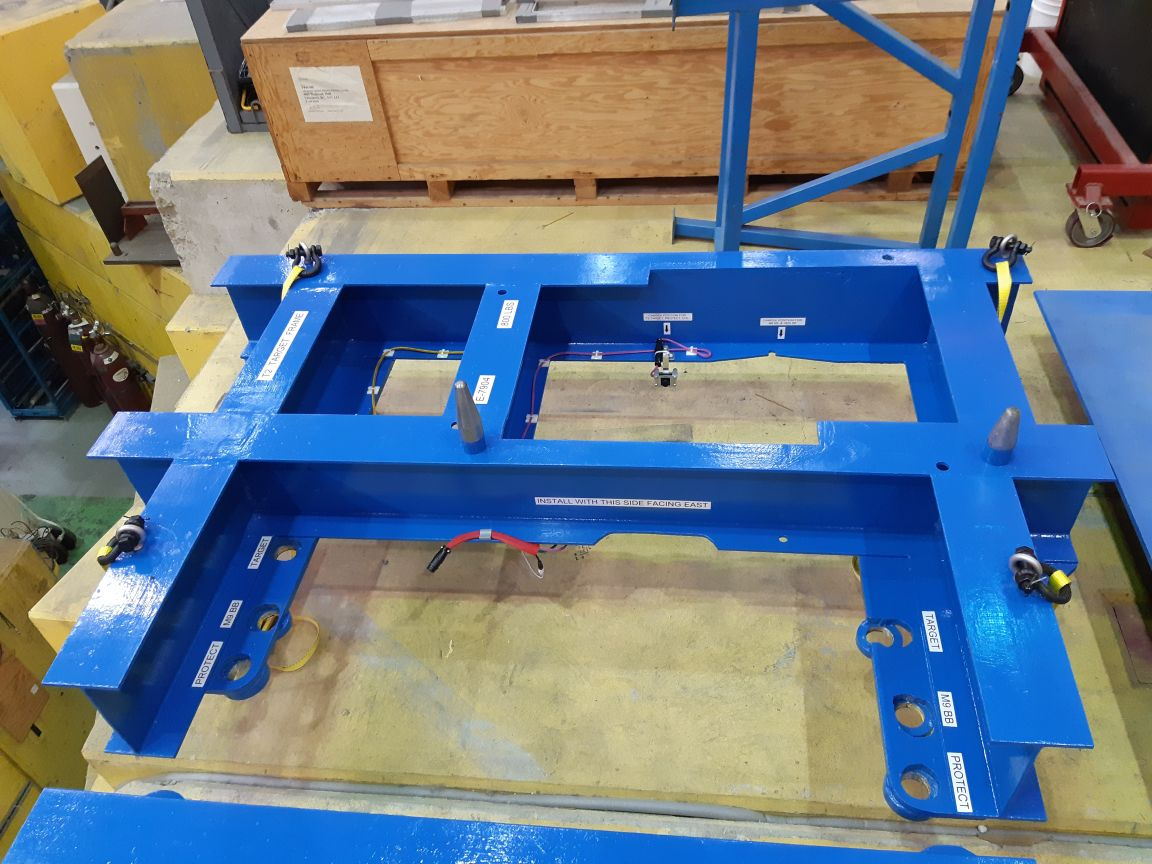
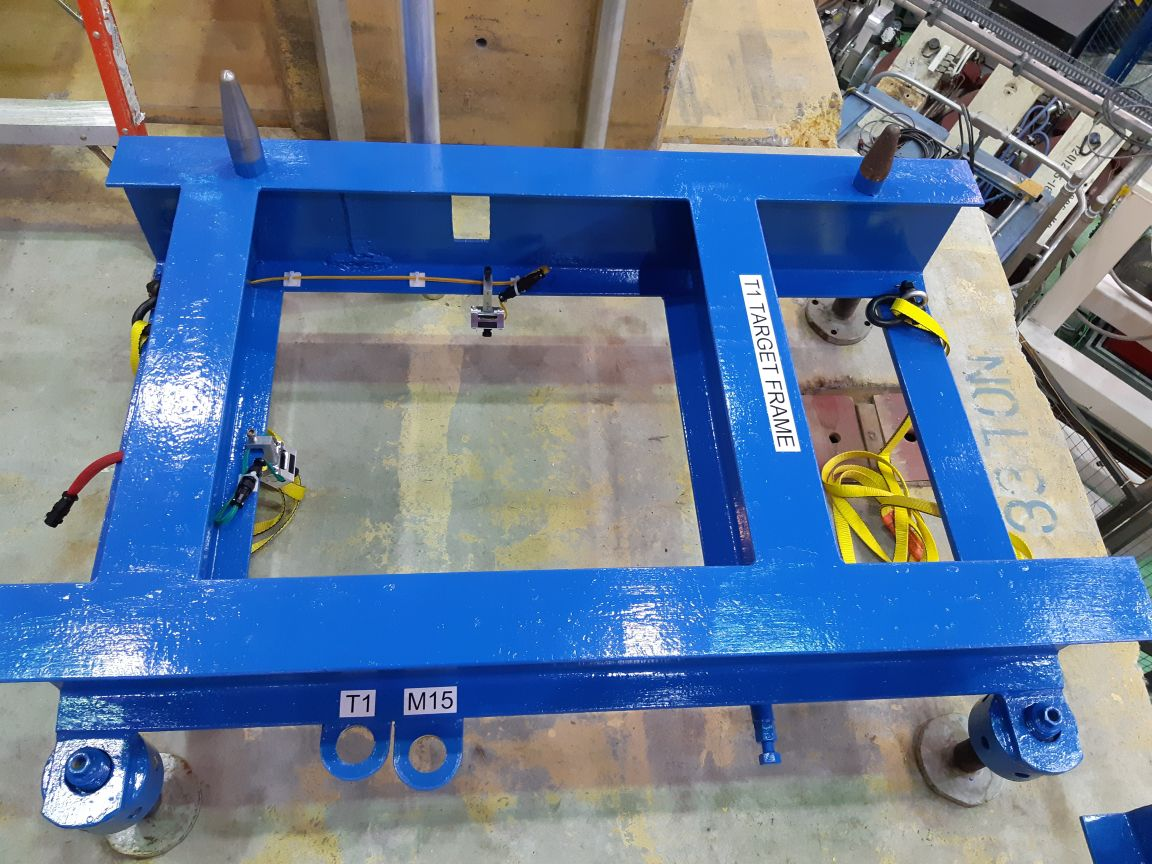

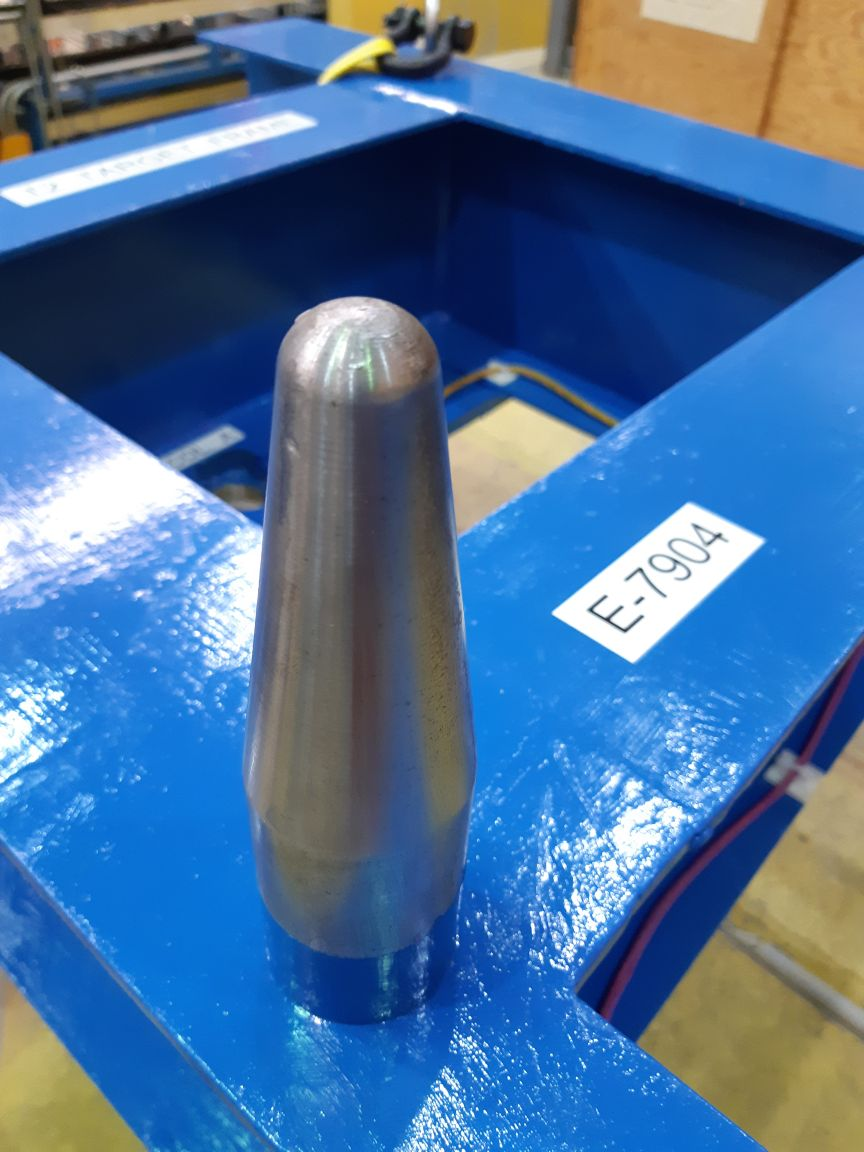
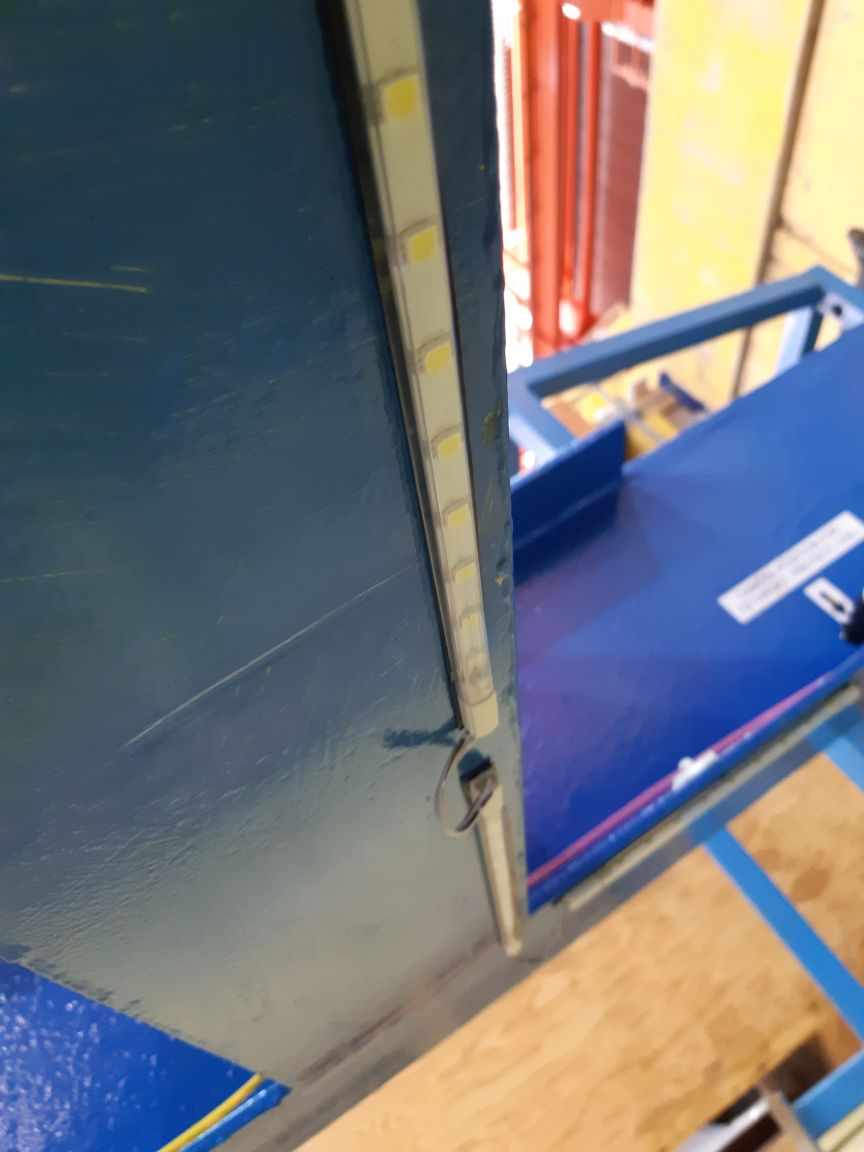

|
Attachment 1: 20190624_095714.jpg
|
|
Attachment 6: 20190624_095701.jpg
|
|
255
|
Thursday, January 30, 2020, 17:55 |
Isaac Earle | Repair | Target 1 | Target | T1-MK2 target assembly repair completed in hot cell |
The following work was done to the T1-MK2 target in the hotcell between the dates of May 24, 2019 - Jan 30, 2020 (See E-Log #251 for further information):
- May 24: Flushed position 2 with water, purged all positions with air. Left air running through position 0 over the weekend
- May 27: Switched to position 5, left air running to dry out bellows
- May 28: Started pump out with cold-trap; Reached "fine test" (TP pressure < 10E-2 Torr) after ~10-15 minutes, left for 2 hours, removed ice build-up then restarted leak detector;
Down to 1.0E-3 Torr TP pressure and 1.0E-8 Torr*L/s after ~10min
Leak checked with 5psi helium, ~0.5s spray: Response at lower delta seal right side (when facing ladder) up to 3.8E-6 Torr*L/s and drift responses from nearby locations
- June 27: Position 1 target removed - no issues, required light tapping with hamme
Position 4 target removed - lots of hammer hits required
Both target beam spots photographed. Saw what looks like hole on Position 4 entrance window (see attached photos)
- July 8: Protect monitor inspected visually using Nikon level by Dave Cameron and Shengli Liu - Nothing abnormal observed
Electrical check w/ multimeter: all OK
Observed ground to HV plates while moving ladder from Position 5 to 0 - all OK
Observed ground to HV plates while moving profile monitor IN then OUT - all OK
Found intermittent short from HV to ground when shaking the target assembly or tapping the protect monitor cassette: must replace
- July 18: Cleaned Position 1 and 4 Swagelok sealing surfaces on the target ladder using the Dremel tool with burgandy Scotchbrite
Ready for new targets to be installed
Plugs installed at Position 4
- July 24: Target #105 installed at Position 1
Started leak detector pumpdown with cold trap; Only pumped down to 4.0E-3 Torr; Big helium response at lower right delta seal (10E-5 Torr*L/s range)
Concluded that the leak got worse during the target replacement (likely from the hammering required to remove Position 4 target
Tightened bolts for lower right delta seal then repeated leak check: same results, therefore must replace seals
Received replacement protect monitor cassette from Probes Group and installed
- July 29: Probes group did blip test on new protect monitor - all OK
We repeated the test for shorts with shaking and tapping on the target assembly and monitor - no shorts observed
Concluded that protect monitor issues is now fixed
- Early Jan 2020: Lower cone and plate removed, ladder removed (old style w/o plate at top)
Removed seal spacers, the one for the lower right delta seal was stuck, had to use a flat edge screwdriver as a wedge with aluminum hammer to dislodge
Removed delta seals, observed some deposits or corrosion at lower right seal location
Cleaned spacers using Scotchbrite on Dremel
Used 3D printed jigs with glued on burgandy Scotchbrite to clean sealing surfaces (no air ratchet or dremel, polished with manipulators until a clean shiny surface was produced)
Had to remove bolts for the ladder flanges to clean the surfaces, and when reinstalling one of them it cross threaded and couldnt be removed
Bolted instead at different hole locations (still at opposite sides of flange) but also had to switch bolt locations on upper seals to do this because bolts will interfere if using same threaded hole
Eventually got everything back together with new delta seals installed (TBP0454B, machine shop order #44138)
Note: the upper delta seals were not disturbed - new bolts installed and torqued before old ones were removed
- Jan 22: Leak check, pumped with cold trap: down to 0.0E-10 Torr*L/s and 1.0E-3Torr TP pressure after 9.5 minutes
Using 5 psi helium, 0.5s spray; No response at any previous locations; Very small drift response up to 0.5E-10 Torr*L/s
Concluded that leak is fixed
- Jan 26: Base plate and cone reinstalled - no issues
- Jan 30: David Kyle and Shengli Liu re-tested the profile monitor and protect monitors - No issues
Measured vertical and horizontal positions for all targets and protect monitor, updated measurements sheet (PDF attached)
Ladder moved to Position 0
Target assembly ready to be moved to storage pit
|
Attachment 1: T1-MK2_-_2020.pdf
|
|
Attachment 2: RHB_8901_Position_1_Entrance_Window.jpg
|
|
Attachment 3: DSC_0047_Position_1_Exit_Window.jpg
|
|
Attachment 4: RHB_8904_Position_4_Entrance_Window.jpg
|
|
Attachment 5: DSC_0022_Position_4_Exit_Window.jpg
|
|
271
|
Tuesday, November 24, 2020, 15:10 |
Isaac Earle | Standard Operation | Target 2 | Target | Additional targets added to T2-MK1 ladder |
The following work on the T2-MK1 target was completed sporadically over the last few months:
Sept 22:
- T2-MK1 target moved from storage pit to hot cell (new camera view to check flask doors and latch engagement works great)
- Rubber pad from storage pit standoffs was stuck under flange - removed and cleaned base of flange
- Preliminary leak check: target positions and delta seals no response, left bellows (facing ladder) had tiny response up to 3.0E-8 with recovery in ~5s, right bellows no response
- Removed plugs at Position #1 and #3
Oct 14:
- Installed 12mm Be target #106 at Position 1 (confirmed with Yuri that it may be useful to have a short Be target on the T2 ladder)
- Installed 5cm target #301 at Position 3
- Leak checked target positions: no response, only mild delayed drift
- Position 4 plugs removed
Nov 10:
- Installed 5cm target #302 at Position 4
- Repeated leak check: no response at all target positions
- Took vertical and horizontal measurements for all new targets
- Position limit switches and potentiometer confirmed working ok
Nov 24:
- Moved to Storage Pit Hole #4
|
273
|
Wednesday, March 31, 2021, 16:15 |
Matthew Gareau | Standard Operation | Target 1 | Target | T1-MK1 target exchange |
March 29 Monday
- moved T1-MK1 target from beamline to hotcell (field from target 15mSv/hr @ 0.5m)
- flushed water through position 4
- flushed air through all positions
- left air running @ 5psi overnight through position 5
- potentiometer reading "O/L" at position 3, all other positions OK
- all micro switches OK
- removed the left plug (when facing ladder) at position 1 , but after reading elogs it was found that the right plug at position 1 was having issues. Will have to replug left with new plug
March 30 Tuesday
- pumped down with cold trap, started at 10:00
- test port 2.0 E-1 Torr after 1 hour
- cold trap removed, cleared, dried, refilled
- 11:10, started pumping, found leak at lab vac tubing joint. Fixed.
- 11:16, started pump again
- 11:24, 1.0 E-3 Torr TPP, 1.4 E-9 L/s leak rate
- preformed leak check, no response at all locations
- position 4 Be target removed (required hammering). Damaged spot, potential start of hole observed at center of beam spot (see attached photos)
- position 5 graphite target removed (required hammering)
- New 12 mm Be target #108 installed at position 4
- New 12 mm Be target #109 installed at position 5
- leaving position 3 plugged as the potentiometer is reading "O/L" as indicated from the multimeter
- New plug installed on left side of position 1
- 15:47, stated leak check pump down
- 15:57, 2.0 E-3 Torr
leak check results
All positions were no response (NR) except
Position 1, Right side plug) 5.9 E-8 Torr
Position 3, Left side fitting) 5.3 E-9 Torr
Position 4, Left side fitting) 4.2 E-9 Torr
All locations should be H2O tight
March 31 Wednesday
- took vertical and horizontal measurements of the new position of 4 and 5 targets (updated elevations PDF sheet included)
tested profile monitor activation
- started moving at 15 psi
- reached limit at 35 psi
- both limit switches OK
- Cleaned base of vacuum flange and top of support ring
- prepared target ready for transport with flask (ladder in position 0)
- contacted MCR to update XTPAGE 7L target details
- emailed Tony Tateyama to have PLC lookup tables updated with new target info
|
Attachment 1: IMG_20210330_140744.jpg
|
|
Attachment 2: IMG_20210330_141059.jpg
|
|
Attachment 3: IMG_20210330_141455.jpg
|
|
Attachment 4: T1-MK1_-_2021.pdf
|
|
276
|
Thursday, February 17, 2022, 13:03 |
Matthew Gareau | Maintenance | Target 1 | Target | T1 MK2 wire scanner and protect monitor test removal and reattachment with pin straightening |
this Work was done on 09 Dec 2021.
Since Isaac Earle was leaving Triumf he was giving us (maico, chad, adam, and myself) a demonstration of how to remove targets, protect monitor, and wire scanner. During the removal it was noticed that one of the pins for the wire scanner was bent and it would not be possible to reattach without straightening the pins.
Luckily the fields from the ladder were low enough (374 uSv/h) and we were able to retrieve the wire scanner and manually bend the pins back. The wire scanner was reattached without incident, and now will need diagnostics to check on the target ladder to ensure all is operational. |
Attachment 1: IMG_20211207_140443.jpg
|
|
Attachment 2: IMG_20211207_140508.jpg
|
|
Attachment 3: IMG_20211207_140735.jpg
|
|
Attachment 4: IMG_20211207_122631.jpg
|
|
Attachment 5: IMG_20211207_142836.jpg
|
|
286
|
Wednesday, April 13, 2022, 12:31 |
Adam Newsome | Standard Operation | Target 2 | Target | T2-MK2 moved: from target station to storage |
The T2-MK2 target was moved from the target station to the storage area (position 3). Upon removal, it was measured with a pole monitor at 0.5 m to be 960 mSv/h. |
287
|
Wednesday, April 13, 2022, 12:33 |
Adam Newsome | Standard Operation | Target 2 | Target | T2-MK1 moved: from storage area to target station |
The T2-MK1 target was moved from the storage area (formerly position 4) to the target station. Services were reconnected in order to prepare for normal operation. |
291
|
Thursday, May 05, 2022, 14:39 |
Adam Newsome | Standard Operation | Target 1 | Target | T1-MK1 and T2-MK1 profile monitor actuation test |
The profile monitor actuation tests were completed for T1 and T2. No abnormalities were noticed in vacuum during either test.
Note: an issue was observed with T2-MK1 - see e-log 290. The issue was resolved. |
292
|
Wednesday, May 25, 2022, 10:15 |
Adam Newsome | Standard Operation | Target 1 | Target | T1-MK2 moved from hot cell to storage area |
The T1-MK2 target was moved from the hot cell to the storage area, in position 5. Note: manual nudging of the flask was required to get it to align with guide pins properly. |
293
|
Wednesday, May 25, 2022, 10:16 |
Adam Newsome | Standard Operation | Target 2 | Target | T2-MK2 moved: from storage location to hot cell |
Target T2-MK2 was moved from the storage location (formerly position 3) to the hot cell in preparation for replacement of end of life targets. |
302
|
Thursday, September 15, 2022, 14:34 |
Adam Newsome | Standard Operation | Target 2 | Target | T2-MK2 target elevations measurement |
The target elevations measurement and beam spot checks were completed on Sept. 15, 2022. This was done after a July 2022 target exchange for target positions 3 and 5.
Updated target elevation drawing can be found in DocuShare (Collection-33652) |
Attachment 1: T2-MK2_-_Sept_2022.pdf
|
|
303
|
Friday, September 23, 2022, 10:51 |
Matthew Gareau | Standard Operation | Target 2 | Target | Target T2-MK2 moved to storage pit |
The T2-MK2 target was transported from the east hot cell to the storage pit at position 3.
As was noted in the past, position 3 is difficult to align. The flask alignment pins prevent the flask from positioning in the correct location, and it is required to have the flask just above the pins to ensure that the pins did not restrict the flask movement.
It is recommended to install a camera system to assist with the target placement and retrieval, which will help reduce the amount of dose one receives during this operation.
|
Attachment 1: Storage_location_state_as_of_Sept_23_2022_(after_target_moves).jpg
|
|
307
|
Wednesday, January 11, 2023, 15:22 |
Adam Newsome | Repair | Target 2 | Target | T2 Target Ladder Motor - Coupling Failure |
It was reported on Dec. 20, 2022 that when Operations attempted to run the target ladder motor, it was unresponsive. A fault report was created: 15477.
During winter shutdown 2023, the T2 area was uncovered and the motor was inspected on 2023-01-11 by Adam Newsome and Maico Dalla Valle. The connectors and cabling appeared OK.
Upon removing the motor from its mounted position, it became clear that the coupling part between the motor and the gearbox had failed. The motor was running properly but not actually connected to the drive shaft and therefore nothing happened when ops tried to move the ladder. We confirmed that the motor runs properly in no-load condition when it is isolated from the rest of the assembly. We were able to move the rest of the drive shaft by hand and it does not appear to have any significant resistance, so it is suspected that this coupling failed due to radiation exposure over a long period of time rather than overload. The coupling part is plastic and designed intentionally to break under high loads (it is thinned out in the middle, where it snapped). Hopefully it did not actually see any high loads (i.e. there is no other root cause of this issue) and it simply degraded so much that it eventually broke.
To resolve this issue, we will fabricate/purchase and install another one (Albert, Maico) and work with operations to test that all target ladder positions are reachable once it is installed. We will also confirm at that time that the limit switches and potentiometer readback function as expected.
It is recommended to consider the following changes to the drive system going forward to prevent this from happening in the future:
- Replace these plastic coupling parts with metal versions
- Replace the plastic coupling part that is thinned out to intentionally fail under high load with another method of system protection. The same end result could be achieved using a clutch or perhaps a fuse/circuit breaker which would effectively inhibit motion if the motor experienced overload. This would be a significant improvement over breakage because it would not require replacing the part (dose-intensive) and would be more easily recognizable.
For now, this drop-in replacement should suffice because it is not likely that the part will degrade so significantly within the next few years that this would happen again (unless there is a different root cause aside from radiation that we are not aware of!).
[update 2023-01-01] The broken coupler has been replaced by Albert Kong and Adam Newsome. The replacement part was tested - DCR operated the target ladder motor, moving it up and down through all of its positions multiple times. Everything mechanically and electrically appeared OK during motion. DCR confirmed they are able to reach each position and the proper readbacks are present - everything looks OK on their end. The issue is considered resolved and the fault is returned.
|
Attachment 1: PXL_20230111_214957143.jpg
|
|
Attachment 2: PXL_20230111_215006211.jpg
|
|
Attachment 3: New_Coupler_-_T2_Target_Ladder_Motor.PNG
|
|
326
|
Thursday, March 30, 2023, 13:17 |
Albert Kong | Maintenance | Other | Target | Air Amplifier Testing: M9 BB (AKA T2 blocker), M20 BB, T2 MK1 prof. monitor, T1 MK1 prof. monitor actuation |
We tested the air amplifiers by actuating the beam blockers and profile monitors on the T1 and T2 target stations.
The blockers and profile monitors were each actuated (brought up/out and down/in fully) > 5 times and vacuum remained stable throughout (see attached).
The cycle rate of the air amplifiers (time between 'puffs') under steady conditions (target devices kept in the out position) was measured to be between 60-90 seconds, with 90 seconds corresponding to when the 'flow control' ball valve is fully shut and ~60 seconds when the valve is opened (either partly or fully).
When a target device is brought up, a cycle event will occur shortly after the device reaches the out position.
This cycle time is much longer than last reported in 2014 (see elog #119), by a factor of 2-3.
The top amplifier sounds different from the bottom amplifier (cycles between being 'rattly' and 'quite' between cycles).
Seeing how the beam blockers and profile monitors were actuated smoothly with the air amplifiers, we will keep the system running off the lower air amplifier with the 'flow control' ball valve kept open (not shown).
At some point we will look into disassembling the top amplifier to see why it sounds differently between cycle events.
For reference, both amplifiers read 20psi at the regulator and 120 psi to the target station. |
Attachment 1: T1_Mar30_2023_Vacuum.png
|
|
Attachment 2: T2_Mar30_2023_Vacuum.png
|
|
Attachment 3: IMG_1907.JPEG
|
|
329
|
Thursday, May 11, 2023, 11:28 |
Adam Newsome | Repair | Target 1 | Target | T1-MK1 - broken target ladder motor coupler repaired |
See Cyclotron Fault 15787. The target ladder motor failed to move to the commanded position during a test. The T1 area was uncovered and the motor assembly was inspected by M. Dalla Valle, A. Newsome, and A. Kong. It was determined that the rubber coupler which connects the motor shaft to the drive assembly had degraded and snapped. This is similar to an incident which recently occurred on T2. The coupler was replaced with an all-metal version. The system was tested by the DCR operators. They ran the target ladder to each extreme (position 5 to position 0) multiple times. The target ladder was also moved to a few positions which had targets installed, and the cooling package was energized to run water through and confirm functionality. All feedback sensors for the target ladder assembly and cooling package were observed to behave normally, as confirmed by the DCR. RH group confirmed visually that there were no observable issues. The system is now considered operational.
It is recommended to change all drive system coupler parts on both T1 and T2 during the next shutdown to prevent this issue from happening in the future. These parts should be inspected during the annual inspection of the T1/T2 assemblies as well. |
337
|
Wednesday, January 10, 2024, 12:47 |
Albert Kong | Standard Operation | Target 1 | Target | T1 target ladder exchange (T1-MK1 to hot cell roof, T1-MK2 from pit to station) |
T1-MK1 was moved from the target station to the hot cell roof.
Radiation surveys report 140 mSv/hr at 0.5m for the bare T1-MK1 target ladder.
On the hot cell roof, fields are 220uSv/h at 0.5m.
T1-MK2 was subsequently transported from the storage pit to the target station.
After the transport operation, the 1A vacuum volume was then pumped down, and reached approximatley 1/10 of the vacuum level prior to venting.
Update: a few hours after the vacuum volume started pumping down, vacuum levels stabilized to the level observed prior to venting (see image) - confirming that the o-ring seal on the target is good and that the transfer operation was a success.
------------------------------------------
During the transport operation we noticed that the chain drive on the target transfer flask was slipping considerably more when powered through the power bar on the camera stand.
This issue was remedied by powering the transfer flask through a dedicated plug, and will be noted in procedures for future transport operations.
|
Attachment 1: T1_and_T2_Beryllium_Target_Beamtime_Spreadsheet_-_(10Jan2024).xlsx
|
Attachment 2: Meson_Hall_Storage_Pit_Target_Device_Location_Record_-_(10Jan2024).pptm
|
Attachment 3: VacuumAt2.56PM.PNG
|
|