ID |
Date |
Author |
Category |
Type |
Module |
Target/Number |
Subject |
854
|
Thursday, March 05, 2015, 14:30 |
chad fisher | South Hot-Cell | Development | | | Dissection Box |
Box for dissecting targets almost complete. Should be done tomorrow. |
Attachment 1: 20150305_142144.jpg
|
|
855
|
Monday, March 09, 2015, 09:42 |
chad fisher | South Hot-Cell | Development | | | Hot Cell Table Swiping |
3 swipes of the south hot cell table were taken from the target hall through the roof hatch (2 standard, 1 alpha).
Initial results of the table swipes are pending however swipes of the pool tool and end effector are clean, 0 counts, booties, gloves clean.
Fall arrest equipment has a puzzling 6000 counts, and suit 500 counts.
|
859
|
Thursday, March 12, 2015, 13:04 |
David Wang | ITE | Standard Operation | TM4 | | 5 Shielding blocks have been transferred from ITE to ITW. |
5 shielding blocks have been transferred from ITE to ITW for next week TM4 move. |
865
|
Friday, March 20, 2015, 13:37 |
chad fisher | South Hot-Cell | Development | | | TM2 Optics Tray |
Final assembly and alignment of TM2 optics tray continued today. Front section is "aligned". |
Attachment 1: 20150320_113132[2].jpg
|
|
Attachment 2: 20150320_113018_1[1].jpg
|
|
866
|
Monday, March 23, 2015, 07:56 |
David Wang | ITE | Standard Operation | | | TH Shut Down Activities Schedule Feb 23th- Apr 15th update |
This schedule is following Dons schedule on module moves. See attachments for updating.
2015-03-27: Weekly update the schedule. The shut down job is close to the end. See attachment 3, 4. |
Attachment 1: Target_Hall_shut_down_activities.pdf
|
|
Attachment 2: Target_Hall_shut_down_activities.mpp
|
Attachment 3: Target_Hall_shut_down_activities.pdf
|
|
Attachment 4: Target_Hall_shut_down_activities.mpp
|
871
|
Wednesday, March 25, 2015, 10:37 |
chad fisher | South Hot-Cell | Development | | | TM2 optics tray build |
TM2 optics tray build is continuing. Going well. Hope to have assembly and alignment finished by Friday.
|
Attachment 1: 20150325_101718.jpg
|
|
Attachment 2: 20150325_101735.jpg
|
|
Attachment 3: 20150325_102024.jpg
|
|
877
|
Monday, March 30, 2015, 07:38 |
David Wang | ITE | Standard Operation | TM4 | | TH Shut Down Activities Schedule Feb 23th- Apr 15th update |
Updated schedule this morning after last Fridays ISAC facility support group meeting.
Updated schedule on 2015-April -02. See attachments 3,4. The scheduled all shut down jobs are done on time.The TM2 move to SHC will be delayed to May.There will be a new beam running time TH activities schedule (start from April 15) replacing this shut down schedule on next time weekly update. |
Attachment 1: Target_Hall_shut_down_activities.pdf
|
|
Attachment 2: Target_Hall_shut_down_activities.mpp
|
Attachment 3: Target_Hall_shut_down_activities.pdf
|
|
Attachment 4: Target_Hall_shut_down_activities.mpp
|
879
|
Tuesday, March 31, 2015, 11:36 |
chad fisher | South Hot-Cell | Development | TM2 | | TM2 Optics Tray Complete |
TM2 optics tray is complete.
Master alignment tray: 0 up/down, 0 left/right
Optics tray: Front 0 up/down, 0 left/right. Middle 0 up/down, 0 left/right. Back 0 up/down, 0 left right.
|
Attachment 1: 20150331_OPTICS_FRONT.jpg
|
|
Attachment 2: 20150331_OPTICS_MIDDLE.jpg
|
|
Attachment 3: 20150331_OPTICS_BACK.jpg
|
|
882
|
Wednesday, April 01, 2015, 13:08 |
David Wang | ITE | Standard Operation | TM4 | | Replaced ITE tank to module 42X0.275 o-ring |
I replaced ITE tank to module 42 ID X 0.275 o-ring. The o-ring is changed once a year before the first beam time. The flanges was cleaned and the new o-ring was installed. It works fine. |
Attachment 1: 001.JPG
|
|
Attachment 2: 002.JPG
|
|
Attachment 3: 004.JPG
|
|
Attachment 4: 005.JPG
|
|
Attachment 5: 006.JPG
|
|
884
|
Friday, April 10, 2015, 15:40 |
David Wang | ITE | Standard Operation | TM4 | | 5 Shielding blocks have been transferred from ITW to ITE. |
5 shielding blocks have been transferred to ITE. The ITE is configured to take proton beam. |
885
|
Monday, April 13, 2015, 08:59 |
David Wang | ITE | Standard Operation | | | Target Hall Scheduled Activities April 07 - June 26 2015 |
See attachments 1, 2 for target hall schedule from 07 April to 26 June 2015. The first TM1 move which is scheduled on 16 April 2015 could be delayed because of SHC operator availability. I will update the schedule once Don confirms the move date with Isaac.
Updated the schedule. The TM1 move has been re-scheduled to Friday, 17 April 2015. See attachments 3,4. |
Attachment 1: Target_Hall_Scheduled_Activities__Apr_07_to_June_26_2015.pdf
|
|
Attachment 2: Target_Hall_Scheduled_Activities__Apr_07_to_June_26_2015.mpp
|
Attachment 3: Target_Hall_Scheduled_Activities__Apr_07_to_June_26_2015.pdf
|
|
Attachment 4: Target_Hall_Scheduled_Activities__Apr_07_to_June_26_2015.mpp
|
886
|
Wednesday, April 15, 2015, 09:01 |
Anders Mjos | Conditioning Station | Development | | | Archiver variables added by Controls |
The following variable have been added to the archiver (as per work request)
TCS:TS5:RDTEMP
TCS:TCM1:EE:RDTEMP
TCS:TCM1:COIL1:RDTEMP
TCS:TCM1:TBHT:RDTEMP
TCS:TCM1:TGHT:RDTEMP
TCS:TCM1:MSP:RDTEMP
TCS:TCM1:HVC1:RDTEMP
TCS:TCM1:HS:RDTEMP
TCS:FC:SCALECUR
TCS:COL:SCALECUR
TCS:TK2:RDLEVEL
TCS:TK2:RDLEVEL
TCS:DIF1:RDFLOW
TCS:CHILL:RDHRS
The archiver was restarted.
|
890
|
Monday, April 20, 2015, 07:27 |
David Wang | ITE | Standard Operation | TM4 | | Target Hall Scheduled Activities April 07 - June 26 2015 |
Weekly target hall schedule update.2015-04-20
weekly target hall schedule update 2015-04-27 attachments 3,4. |
Attachment 1: Target_Hall_Scheduled_Activities__Apr_07_to_June_26_2015.mpp
|
Attachment 2: Target_Hall_Scheduled_Activities__Apr_07_to_June_26_2015.pdf
|
|
Attachment 3: Target_Hall_Scheduled_Activities__Apr_07_to_June_26_2015.pdf
|
|
Attachment 4: Target_Hall_Scheduled_Activities__Apr_07_to_June_26_2015.mpp
|
893
|
Tuesday, April 21, 2015, 13:01 |
Grant Minor | ITW | Development | TM2 | | TM2 MK4 Optics Tray - banana plug bore modification (on bench) |
The MK4 optics tray prepared for TM2 (as per ITA6082) had an undersized bore for the banana plug, making insertion of the plug extremely difficult / impossible.
Reference stores parts were collected to check the fit: male plug 3-4/01152 and female jack 1-6/1201. The size of the female jack was checked with a #21 drill at .159".
The bore on the optics tray was drilled out dry using the #21 drill to the same depth as the original blind hole, by Maico and Dan McDonald. Chips were carefully collected in a rag, and the hole was blown out with compressed air.
The fit was checked to be snug but possible, using the male plug and the Remote Handling ultem base (ref ITA6023).
Redlines and photos are attached.
|
Attachment 1: ita6092_redlines_gminor_21apr2015.pdf
|
|
Attachment 2: TM2_Optics_Tray_Bore_Mod_21Apr2015_1.JPG
|
|
Attachment 3: TM2_Optics_Tray_Bore_Mod_21Apr2015_2.JPG
|
|
Attachment 4: TM2_Optics_Tray_Bore_Mod_21Apr2015_3.JPG
|
|
895
|
Wednesday, April 22, 2015, 11:05 |
David Wang | Conditioning Station | Standard Operation | TM1 | | electrical check on TM1 at CS under vacuum |
I did an electrical check on TM1 at CS. The resistance check:A-B 3.918m ohm, A-C 5.905m ohm,A-D 4.070m ohm,B-C5.462m ohm,B-D3.633m ohm. They are very close to the check we did in SHC. The only unusual thing I found during the check is the ohmmeter reading between A and 60 KV common (6.2K )and the Megga reading between them at 250 V which is 0. I repeated 4 times and always got the same readings. However, after so many times check, the Megga reading between A and 60KV suddenly went back to normal(300 M at 250V) at the final check. And,it stays at 300M now. All other measurements are same as we did at SHC before. |
897
|
Thursday, April 23, 2015, 12:56 |
Anders Mjos | Conditioning Station | Maintenance | TM1 | | IG1 Good Vacuum limit changed |
Changed by Dave Morris.
New value is 1E-5 T (old value was 7.09E-5 T) |
Attachment 1: IG1GoodVacuum.png
|
|
899
|
Monday, April 27, 2015, 16:12 |
Keith C Ng | South Hot-Cell | Development | TM2 | | Ceramic Standoffs in TM2 source tray steerer assembly |
On drawing ITA6008 for the Encole 0.5" ceramic standoffs there is a note to match pairs of ceramics to within +/-0.001". This step was missed on the current build of TM2 source tray (ceramics were not measured).
Measured the lengths of the rest of the ceramic standoffs in inventory and they range from 0.5035" to 0.4950" in length. The ceramics have been sorted by length and grouped into bags.
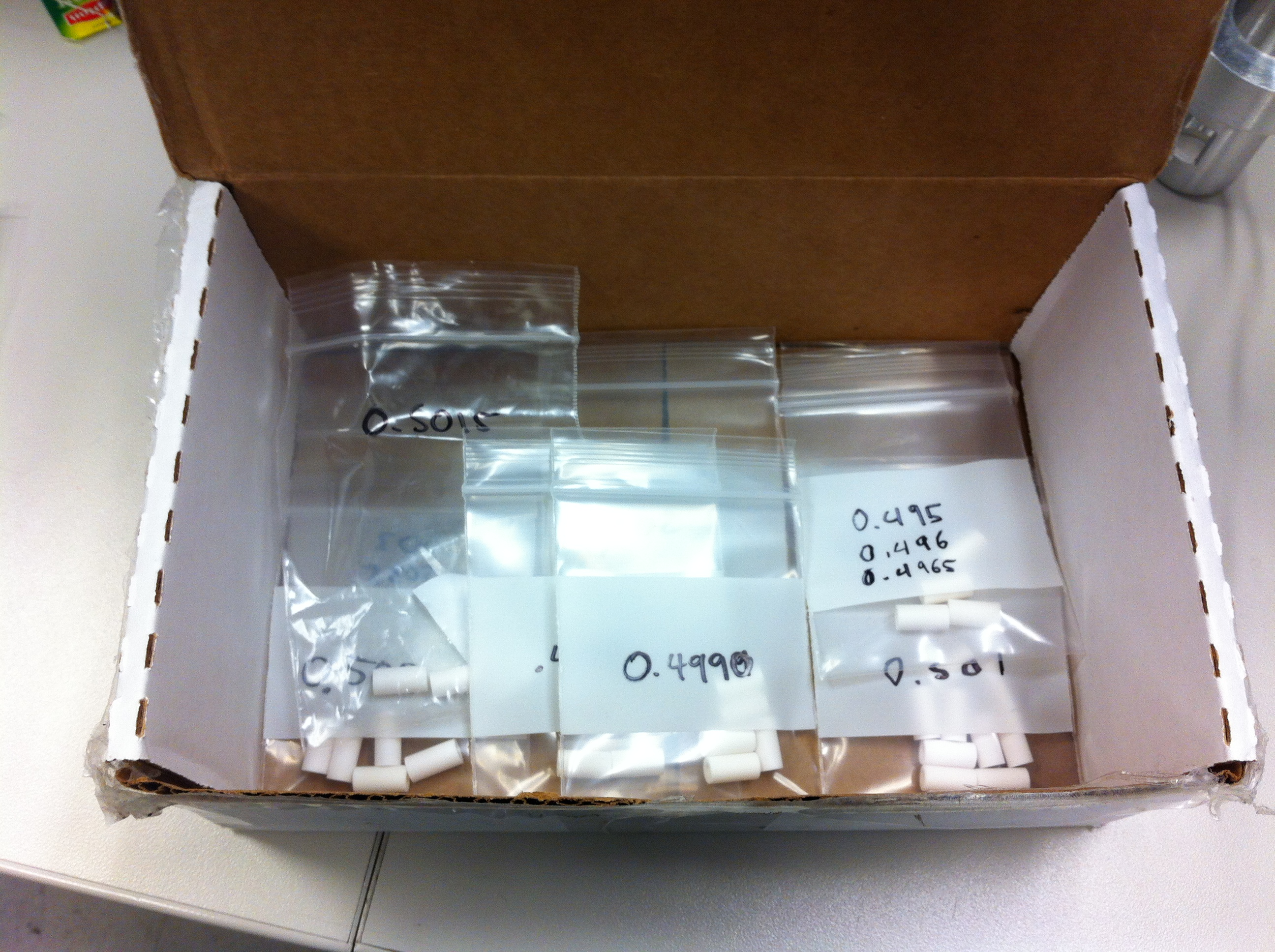 |
900
|
Monday, April 27, 2015, 17:09 |
Grant Minor | ITE | Development | TM2 | | TM2 - New Source Tray - Water Block Seal Groove Inspection Report |
The water blocks soldered to the TM2 cooling lines (see Ref. Assy. ITA6144) were inspected.
See attached inspection reports and drawings.
It was found that only 18% of the seal groove diameters and 55% of the depths were in spec.
The source tray must be tested on the test stand with c-seals to ensure that these blocks will seal properly on the module. |
Attachment 1: IMG_1859.JPG
|
|
Attachment 2: TM2_New_Source_Tray_Water_Block_Inspection_Results_24_April_2015.pdf
|
|
Attachment 3: TM2_water_block_inspect_24Apr2015.pdf
|
|
Attachment 4: TM2_New_Source_Tray_Water_Block_Inspection_Results_April_2015.xlsx
|
903
|
Tuesday, April 28, 2015, 11:09 |
Anders Mjos | ITW | Maintenance | | | Resistance measured of TGHT and TBHT lines to ITW |
The new TBHT and TGHT power supplies were brough up to high current; 350 A and 420 A respectively. The TGHT power supply was limited by PLC to 420 A. The resistance calculated for both the TBHT and TGHT copper lines from the electrical services room to the ITW pit was 1.35 mOhm. See attached spreadsheet for details.
Dave Morris has been contacted to correct the current limit for the TGHT supply to 600 A. |
Attachment 1: Resistance_from_Electrical_Room_to_Target_Station.xlsx
|
907
|
Friday, May 01, 2015, 08:27 |
chad fisher | South Hot-Cell | Repair | TM2 | | Containment Box Removal |
Containment box has been removed in preparation for wire replacement. |