Friday, March 06, 2015, 14:38, Travis Cave, Cyclotron, Standard Operation, Shield Removal
|
All shields and ladders have been removed from the tank, all the port holes have been uncovered, the tank seal has been vacuumed, and the copper blockers installed into the cyclotron. |
Wednesday, January 13, 2021, 11:35, Adam Newsome, Shielding, Maintenance, Shadow Shields Inspection - 2021 Shutdown
|
All shadow shields which are remotely placed inside the cyclotron during shutdown were inspected by Adam Newsome and Chris Peterson on Jan. 13, 2021.
The inspection consisted of:
- Verifying feet were damage-free, welds intact (note: only outer feet were checked due to the large amount of effort that would be involved in shuffling shields around to check each foot)
- Inspection of lifting eyes
- Tightening all critical bolts - many of these bolts were slightly loosened from years of vibration (approx. 1/4 turn)
- General check for other miscellaneous damage
It is believed that all shields are fully acceptable for use, except ones which are clearly marked otherwise from previous years.
The inspection was prompted by a shield which had significant damage last year which could have resulted in a high-dose scenario if it were to get stuck inside the cyclotron. That shield has since been repaired. It is suggested that this inspection take place once every year or two years. |
Tuesday, March 05, 2013, 14:11, Travis Cave, Cyclotron, Standard Operation, Setup and the Installation of the HE 1 probe.
|
Setup of the HE 1 probe is difficult has we have no mockup of it to properly setup cameras and equipment for it. This is problem for both extraction and installation of the probe. Also with the setup some of the broken micro switch from the HE 1 was found on the HE 1 probe jig after the jig was deconned and moved up the B2 level. Also for setup required camera adjustment to be made with the heavy contaminated probe being very close to the person setting up the cameras.
Now installation of the probe worked but it was very fiddly and touchy feely on the install, which something one doesn't want for remote installation. It required lots of movements and adjustment and a little luck and the probe went in, even with a air cylinder that did decide to work in the end.
On the extraction of HE 1 was mess and was damaged upon extraction, this was due to improper camera setup (no mock up of probe), and to the fact that removal is very fiddly and not east to the current design of the jig, and the way the probe is locked in place on the lid.
Note on contamination on extraction the probe jig was contaminated with about 20 000 cpm in spots it was removable and the jig cleaned. Contamination was also found on the jig for the installation of the jig it was about 800 cpm jig was cleaned again. Plastic was also laid on the platform of the upper ressonator trolley as to prevent the spread of contamination to the trolley, this appeared to work. AS A NOTE NONE OF REMOTE HANDLING'S TROLLEYS AND CYCLOTRON EQUIPMENT WAS DESIGNED TO HANDLE CONTAMINATION. If the trolley ever get or contamination is ever found on them they will be impossible to clean. |
Tuesday, July 23, 2024, 13:27, Riley Sykes, Carrier, Maintenance, Service/Maintenance checks
|
1,2, 5 Year Service and maintenance package completed on Carrier. All reducers repacked with Molub-Alloy 777-1 ES grease. Main drive train and all bearings relubricated. No issues. Operational. |
Friday, June 14, 2024, 10:04, Riley Sykes, Service Bridge, Maintenance, Service/ Bridge inspection
|
Yearly, 2 Year and 5 Year service completed. All bearings on support frames turn freely and were regreased with Molub Alloy 777-1 ES. Reducer repacked as well. Reinspect pre shutdown and lubricate orbital drive chain before wiping off excess. |
Tuesday, October 27, 2015, 07:50, maicodallavalle, Elevation Jack, Standard Operation, Service to Station # 9 Right side 9x
|
Station #9 Cleaning of discoloration-
The right side Jack screw nut and worm screw (mating parts in the right side Jack) had some discoloration from may years ago it is thought.
These two parts were cleaned with Scotch Brite.
The Jack was reassembled with grease.Station #9 has been fully serviced and is ready for 2016 Shut Down to be put back in place.
|
Wednesday, February 06, 2013, 17:50, Grant Minor, Elevation Jack, Maintenance, Service records compiled by G. Minor
|
Attached is a compiled record showing the years of service of the jacks, upper bearing, and gear reducers, prepared by Grant Minor on December 17 2012. |
Wednesday, July 24, 2024, 14:26, Riley Sykes, Elevation Jack, Maintenance, Service inspection and relubrication
|
Jack 7R pulled apart and inspected for deficiencies, all parts deemed to be in working order, jack was rebuilt and lubricated with Molub-Alloy 777-1 ES. Jack is deemed fully operational for next swap. |
Wednesday, August 07, 2024, 14:24, Riley Sykes, Elevation Jack, Maintenance, Service inspection and relubrication
|
Jack 7L pulled apart and inspected for deficiencies, alignment monitored with prussian blue and deemed acceptable wear. All parts in working order, jack was rebuilt and lubricated with Molub-Alloy 777-1 ES. Fully operational for next shutdown period swap. |
Wednesday, February 13, 2013, 08:55, maicodallavalle, Service Bridge, Repair, Service Bridge/Carrier Hydraulic Jacks
|
On Monday February 4TH the Service Bridge was being lifted into the Cyclotron with the Carrier. It was noticed that one of the two Hydraulic Jacks was leaking. All work stopped and the Service Bridge and Carrier were moved to the Remote Handling B2 level for repair. The Service Bridge and Carrier were separated and the Hydraulic Jacks were inspected. It was noticed that both Hydraulic Jacks were leaking. Two overhaul kits were ordered. Two other Hydraulic Jacks were found and replaced. Work continued in the Cyclotron with the Bridge and Carrier. The two Leaking Hydraulic Jacks were overhauled. Once most of the work in the Cyclotron was done and there was time that the Service Bridge and Carrier were out of the Cyclotron and not in use the two overhauled Hydraulic Jacks would be replaced. They were tested without the Service Bridge and then with the Service Bridge. There were no leaks and all operation was back to normal. |
Tuesday, February 07, 2012, 18:09, Grant Minor, Service Bridge, Repair, Service Bridge Center Post Bearing Maintenance and Orbit Counter (2011/2012)    
|
Repair of Orbit Limit Switch Plastic Belt
During the fall of 2011, Remote Handling discovered that a plastic toothed belt had stripped in the Cyclotron Bridge orbit limit switch mechanism. This toothed belt is supposed to wrap around the stationary outer race/chassis of the center-post bearing on the Cyclotron service bridge. The belt meshes with a smaller spur gear, which connects through a gear reduction system to a potentiometer and a limit readout. The purpose of this limit switch is to prevent multiple continuous orbits of the bridge in one direction around the Cyclotron, which would twist and stress the trolley electrical wires. Below is a picture showing the stripped belt condition as of Sept 23, 2011 (photo by Travis Cave).
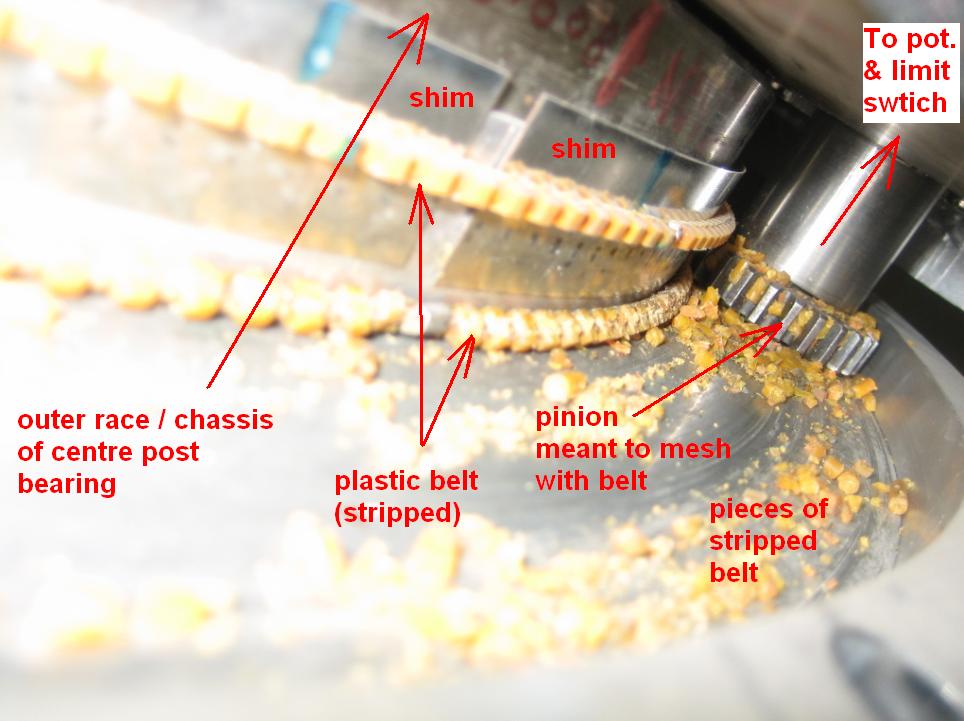
During November 2011, Maico Dalla Valle and Travis went through the drawings of the service bridge assembly and ordered a replacement belt from the original manufacturer (still in business). Maico removed the central bearing assembly, disassembled the bearing, replaced the belt, re-lubricated the bearing, and reassembled the unit into the service bridge. The belt that was installed by Maico was installed with one less link / tooth than the previous belt, to obtain a tighter fit, so that fewer shims had to be used to fit it snugly against the outer race / chassis. After assembly back into the service bridge, Maico commented that a much better mesh was achieved with the pinion. and the system was much easier to turn by hand. This was likely due to re-lubrication of the centre post bearing and and improved mesh / fit of the pinion with the belt. A photo of the serviced assembly with the new belt is shown below:
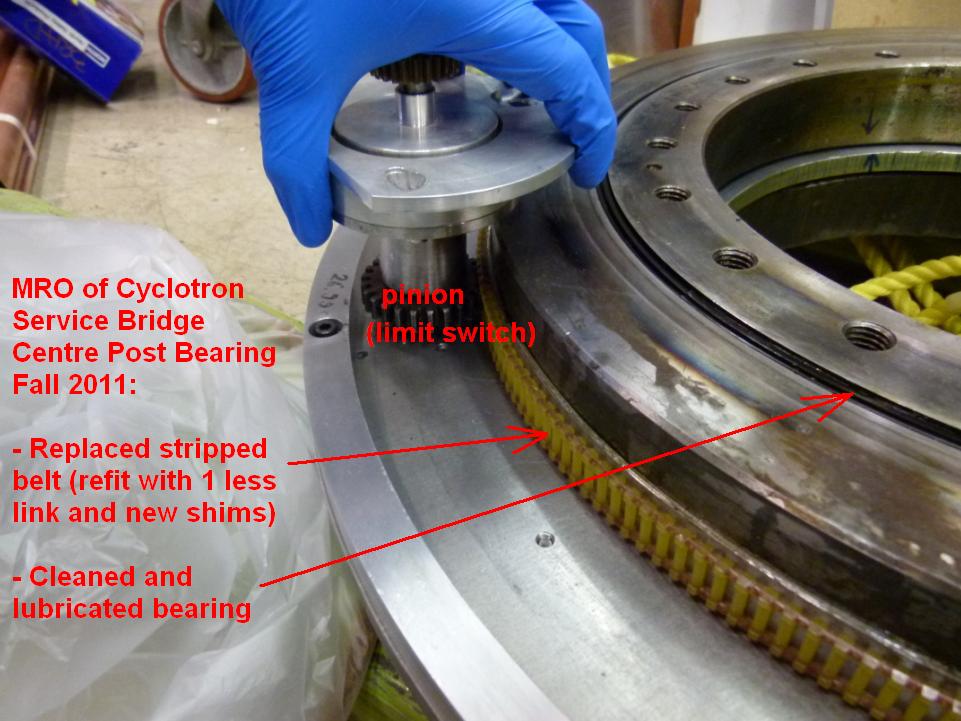
Orbit Counter System - Operational Improvement (mid-Jan to Feb 7 2012)
During the 2011 winter shutdown, there had been some observations of inaccuracy in the orbit counter mechanism used for the automated radiation survey of the Cyclotron. These observations were made by both Remote Handling and RPG staff. The purpose of this orbit counter is to provide an angular position measurement of the service bridge relative to a known reference point in the Cyclotron vault, within a certain degree of accuracy and precision. It appeared that the reading coming from the counter wheel that makes contact with the outer sector surfaces and follows the service bridge along it's orbit was skipping at various suspect locations around the perimeter of the Cyclotron. This skip, at it's worst, was deemed to be sizable enough to invalidate the automated survey of the tank. Several e-mails and reports were generated by multiple parties in Remote Handling and RPG about the problem (attached). The problem was not repeatable each time. A photo of the counter wheel riding along the perimeter sector surfaces is shown below (taken with RH outrigger camera):
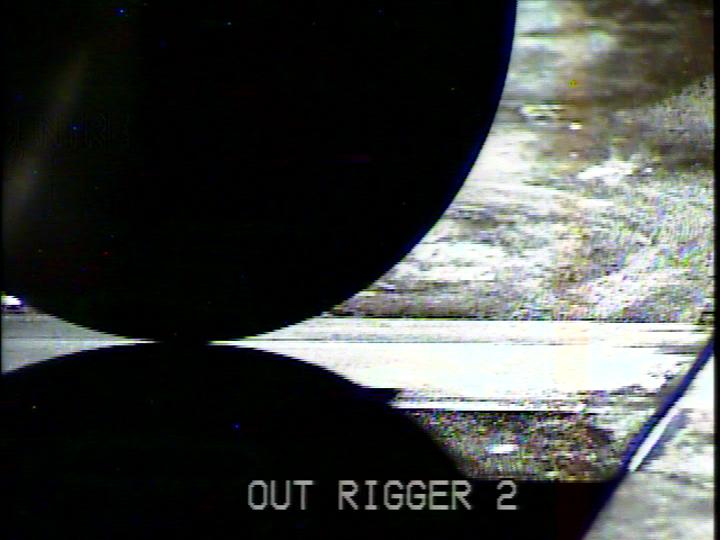
Various theories on the problem and potential solutions were discussed, including:
- Warped aluminum perimeter sectors protruding a small amount into the path of the orbit wheel, causing the wheel to skip as it passes over these bumps (see photos below)
- Insufficient traction between the counter wheel and the perimeter sector surfaces that the wheel rides on.
However, after the center post bearing had been serviced by Remote Handling, and during the routine service bridge work for the 2012 shutdown (copper blockers, shadow shields, photo survey), the following observations were made by RH staff:
- The orbit counter was operating smoothly and accurately and showing no sign of the suspect skips along it's path, throughout the entire range of orbit speeds and along all outer sectors of the Cyclotron. In fact, according to Don Jackson, he could not remember the orbit counter ever working so well.
- The images from the outrigger cameras were noticeably more stable, showing less signs of structural vibration from the service bridge during orbit.
In my professional opinion, I believe this marked improvement in the orbit counter stability is due to the cleaning, lubrication and re-fitting of the center post bearing assembly described in the previous section above. Don Jackson could not remember the center post bearing ever being serviced. I have certainly not been able to find any written record of such service. If that bearing was poorly lubricated and not rotating smoothly, then vibrations, seizing, and sticking would have result during rotation. Any skip, jump, or vibration from such a sticky bearing would be amplified across the 30+ foot lever of the service bridge to the point at which the orbit counter wheel contacts the bridge sector. These vibrations could likely have contributed to false orbit counter readings. See photo below:
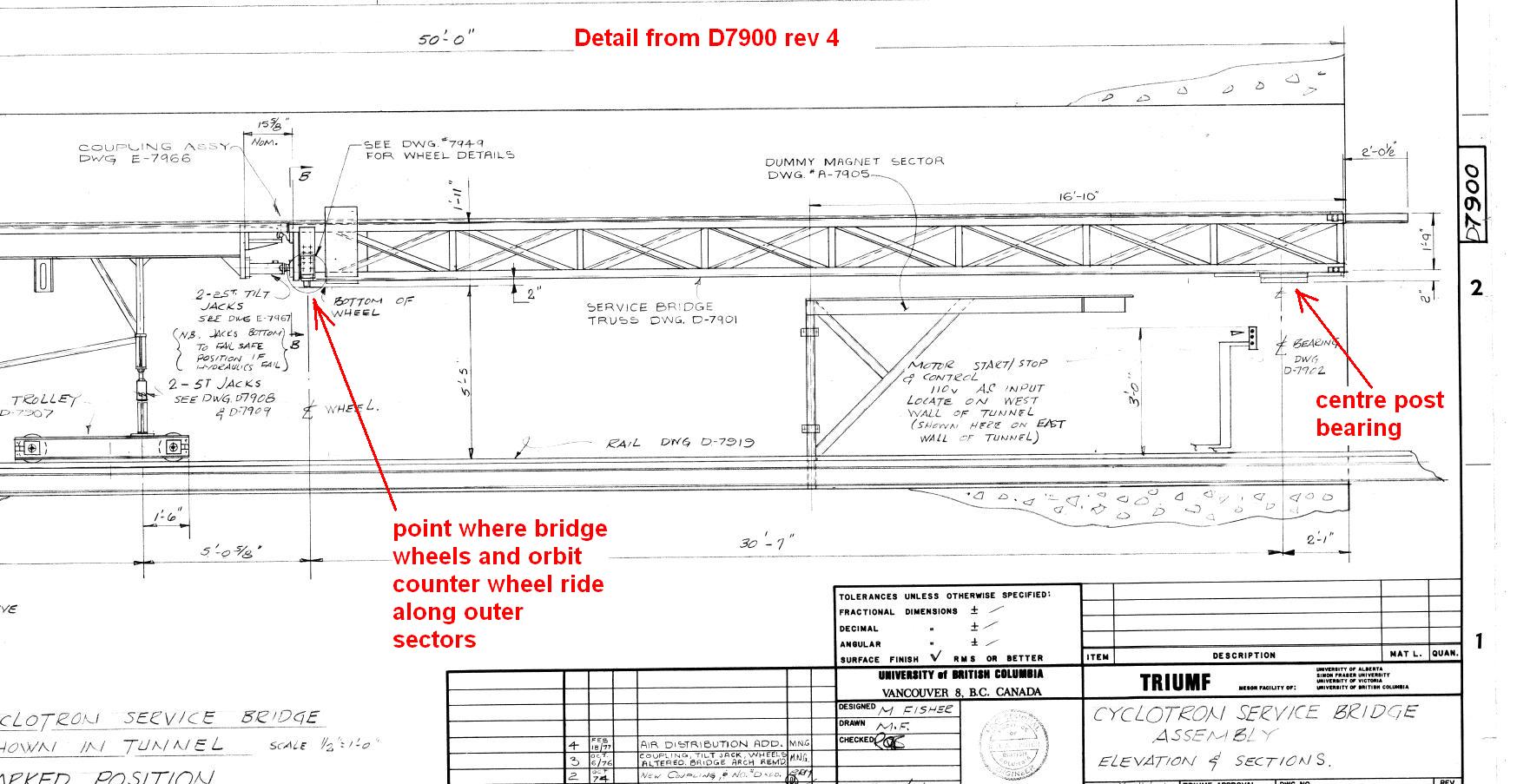
In any case, the orbit counter system has been observed to be operating normally and adequately by RH staff for several weeks of the 2012 shutdown. I recommend that an automated tank survey is attempted as normal procedure, with both RH and RPG staff present to observe and document the behaviour of the orbit counter.
Thanks,
Grant Minor, Remote Handling
|
Wednesday, March 26, 2025, 10:07, Riley Sykes, Elevation Jack, Maintenance, Screwjack 5 L/R
|
Both L and R of screwjack sets #5 have been inspected, serviced and lubricated. All in working order, no deficiencies present and ready for next service installation. |
Wednesday, July 17, 2024, 15:02, Adam Newsome, Infrastructure, Standard Operation, Safety Walkaround Complete - RH Shop, Back Shop, B1, and B2 levels
|
A safety walkaround for July 2024 was completed for the B1 and B2 levels by A. Newsome, and for the main shop and back shop by R. Sykes.
Results can be found in the master spreadsheet
Major deficiencies, main shop:
- Unpainted lead bricks need to be picked up. This was requested of mechanical services twice already in July 2024. Follow up next inspection if not removed.
- Nearly half bulbs burnt out - enough to warrant replacement. AN requested of electrical services on 2024-07-17. Follow up next inspection if not replaced.
Major deficiencies, back shop:
- Phone not working. AN created help ticket 2024-7-17. Follow up next inspection.
Minor deficiencies, B1 level:
- 4-5 light bulbs will need to be replaced soon, not urgent yet.
Major deficiencies, B2 level:
- On the outboard support frame, the lifting eye fastener was stripped which prevented the nut from tightening all the way, posing a rigging hazard. The damaged lifting eye was replaced with a working one 2024-07-15.
- Light fixture above bootbox - mounting damaged and hanging precariously. Reported to electrical services 2024-07-15 and informed common users of area.
Update 2024-07-17 - the issue has been resolved.
- Probes group has rad-waste in the middle of the floor. Reminded them to dispose of it soon.
|
Thursday, October 10, 2024, 12:30, Adam Newsome, Infrastructure, Standard Operation, Safety Walkaround Complete - RH Shop, Back Shop, B1, and B2 levels
|
A safety walkaround was completed for the RH Shop, Back Shop, B1, and B2 levels.
The resulting spreadsheet can be found on DocuShare as Document-242733.
Main deficiencies identified:
- Main Shop:
- Lifting equipment has overdue inspection
- Light bulbs burnt out
- Unpainted lead has not been removed
- B1:
- Crane has overdue inspection
- Lifting equipment has overdue inspection
- B2:
- Crane has overdue inspection
- Lifting equipment has overdue inspection
Action has been taken on all deficiencies.
|
Monday, January 06, 2025, 13:57, Adam Newsome, Infrastructure, Standard Operation, Safety Walkaround Complete - RH Building Shop and Back Shop
|
A safety walkaround was completed for the RH building shop and back shop.
The resulting spreadsheet can be found on DocuShare as Document-242733.
Main deficiencies identified:
- Main shop, ground level:
- Lighting still needs to be replaced (this was previously requested of electrical services and they are aware of it)
- Unpainted lead bricks still need to be picked up (this was previously requested of mechanical services and they are aware of it)
- Rad waste needs to be picked up (will do soon)
|
Friday, January 03, 2025, 10:20, Adam Newsome, Infrastructure, Standard Operation, Safety Walkaround Complete - RH Building B1 and B2 Level
|
A safety walkaround was completed for the RH building B1 and B2 levels.
The resulting spreadsheet can be found on DocuShare as Document-242733.
Main deficiencies identified:
- B2:
- Low on booties stock (more have been ordered)
- Rad waste from Probes group remains in the middle of the floor (requested RPG to ask them to remove it)
Action has been taken on all deficiencies. |
Friday, February 23, 2018, 15:44, Jason Kapalka, Elevation Jack, Repair, Replacement of Elevating System wiring
|
On January 8, 2018, while troubleshooting the Cyclotron Elevating System during the lid-up operation, the
insulation on the three motor drive wires were repaired (w/ electrical tape) and the two motor brake wires were
replaced (w/ crimped butt splices) between the horizontal conduit below the Cyclotron and the terminal block on
the Station #9 motor. The wiring was severely damaged over an 18" long interval that crosses the mid-plane of
the Cyclotron; outside of the 18" damage zone, the wiring insulation was ductile and showed no signs of cracking
or embrittlement.
On February 22, 2018, after the in-tank work was completed and the lid was lowered, the wiring for the synchro
and bump switch on Station #9 was pulled for inspection, which revealed that the insulation on the five synchro
wires had almost completely disintegrated, and the insulation on the six bump switch wires appeared to had
melted together to form a single wire over the typical 18" interval that roughly corresponds to the gap between
the Cyclotron resonators.
On February 23, 2018, the three motor drive wires on Station #9 were pulled and replaced, using crimped butt
splices to the existing wiring in the horizontal conduit below the Cyclotron, as the electrical tape repair job
during the lid-up operation was only a temporary fix. Also, the motor drive, motor brake, synchro, and bump switch
wires on Station #3 were inspected and replaced due to insulation damage.
On February 27, 2018, the synchro and bump switch wires on Station #5 were inspected and replaced due to insulation
damage. The motor brake and drive wires were inspected and re-connected as the insulation showed no signs of damage. |
Thursday, March 19, 2015, 13:14, maicodallavalle, Shielding, Standard Operation, Remote Handling B2 level Shielding door
|
The Remote Handling B2 level Shielding door has been closed. |
Tuesday, March 19, 2013, 19:17, Grant Minor, Elevation Jack, Standard Operation, Re-indexing of all jack station "zero" yoke elevations
|
The dimension between the yokes and the Cyclotron upper structure primary beams was set to .25" nominal at all jack stations today.
At each station:
- The jacks were jogged manually upwards until the yokes hard-stopped on a piece of .25" nominal shim stock (see attached reference photo, measured accurate within .005").
- The dial indicator was set and zeroed, and the station was backed off by .005" to 0.010" in order to remove the .25" reference stock (except at station 4 where the dial indicator mount was damaged).
- After the adjustment, the mechanical counter was decoupled from the output shaft of the jack (without affecting the synchro) and set to "00100".
This work was performed by Maico Dalla Valle and Daniel Wright in co-ordination with Dan Louie.
The defective mechanical counters at stations 5 and 9 were replaced, with a brand new counter at one station and a used repaired counter at the other station.
The yokes at all jacking stations should now be .250" +/- .015" from the upper structure.
|
Tuesday, March 14, 2017, 12:02, Jason Kapalka, Cyclotron, Standard Operation, Radiation survey   
|
The unshielded radiation survey was performed in the Cyclotron tank by the RH group using the service bridge,
tool trolley, and radiation survey attachment on 2017-01-30 (see attached plot).
The shielded radiation survey was performed in the Cyclotron tank by the RH group using the service bridge,
tool trolley, and radiation survey attachment on 2017-02-02 (see attached plot).
A obsolete version of the radiation survey procedure (from Don Jackson) that needs revising and the MATLAB code
for generating a radiation survey map (from Maxim Kinakin) is attached. |
|