Tuesday, April 03, 2012, 12:11, David Wang, Conditioning Station, Development, , , leak check on conditioning station vacuum system
|
I did a leak check on conditioning station vacuum system today.The vacuum system had been roughed over night . This morning before the leak check,the convectron gauge reading on emittance box is 20m torr which is reasonable. I hooked the leak detector to system (without turbo pump on) . The leak detector showed base LR 6.3xE-8 atm.cc/sec. At this base LR, I found 2 leaks up to low E -6range on that cross tube flange to small turbo pump, and the cross tube flange to vessel. I found some of the bolts on the flanges could be tightened more ½ to ¾ turn without difficulty. I checked all the fasteners on the box, cross tube, and turbo pump, tightened some of them. By doing it, the base leak rate dropped to 3.0x E-8 atm,cc/sec, base pressure still 0.0XE-4 torr. I sprayed helium again, the response I found before now disappeared. I waited for about 1hour, and let the leak detector base leak rate dropped to 1.3 xE-8 atm.cc/sec, and base pressure still at 0.0xE-4 torr. At the same time, i only use leak detector as back up pump for whole sysytem and shut off the valve to the scroll pump.By doing this , the leak detector is much stable on the base leak rate. With the help of Bevan, i sprayed the helium to all the vacuum equipments again.This time,no any tiny response has been found on leak detector.The leak rate stayed at 1.2x E-8atm.cc/sec, and no change on pressure also. I checked helium bubble several times during the spray. The conditioning station vacuum system is leak tight. |
Monday, April 02, 2012, 08:17, David Wang, Conditioning Station, Development, , , conditioning station IMC pump down.
|
I pumped down conditioning station IMC today. The inside bellow pressure is -20 psi on the gauge.Visually checked the bellow before and after pump.The bellow is in retracted condition now. |
Tuesday, March 13, 2012, 09:42, chad fisher, South Hot-Cell, Standard Operation, TM1, UCx#3, UCx#3 Autopsy
|
An autopsy was performed on UCx#3 yesterday afternoon. This autopsy followed the plan written by Anders. Indeed, both sides of the target oven had seperated from the central block.Pictures were taken by Anders and Pierre.
After the disection the target was placed back in a can under argon. Any small piece were placed in a zip lock bag and also put in the can under argon. |
Tuesday, March 13, 2012, 12:24, Anders Mjos, South Hot-Cell, Standard Operation, TM1, UCx#3, UCx#3 Autopsy
|
chad fisher wrote: |
An autopsy was performed on UCx#3 yesterday afternoon. This autopsy followed the plan written by Anders. Indeed, both sides of the target oven had seperated from the central block.Pictures were taken by Anders and Pierre.
After the disection the target was placed back in a can under argon. Any small piece were placed in a zip lock bag and also put in the can under argon.
|
Pictures are available on DocuShare:
https://documents.triumf.ca/docushare/dsweb/View/Collection-8189
ISAC e-log entries:
https://web.accel.triumf.ca/isac_elog/Elog_shift_view.pl?shiftid=10803
See attachment for autopsy plan.
|
Tuesday, March 13, 2012, 09:43, chad fisher, South Hot-Cell, Standard Operation, TM1, UCx#3, UCx#3 to spent vault
|
UCx#3 was packaged into a spent can, double bagged and the bag and cans filled with argon as much as possible. Lid was attached and can moved to the storage vault. The target was placed in in Pail 93, and placed into slot 1C of the vault, it was 11.7mSv/hr when removed from the south hot cell. See attached file for latest vault details |
Monday, March 12, 2012, 11:54, Travis Cave, South Hot-Cell, Standard Operation, TM1, no target, module moved
|
TM#1 has been moved from the south hot cell to the north east silo, move went well. |
Monday, March 12, 2012, 10:03, chad fisher, South Hot-Cell, Standard Operation, TM1, UC#3, UC#3 Removal 
|
UC#3 was removed from TM1 this morning. Upon removing the oven heater bolts BOTH legs fell demonstrating that both sides of the oven tube have broken off from the central block.
Target was put into a can under argon for disposal after the module is removed from the cell.
The source tray looked to be in very good, clean condition.
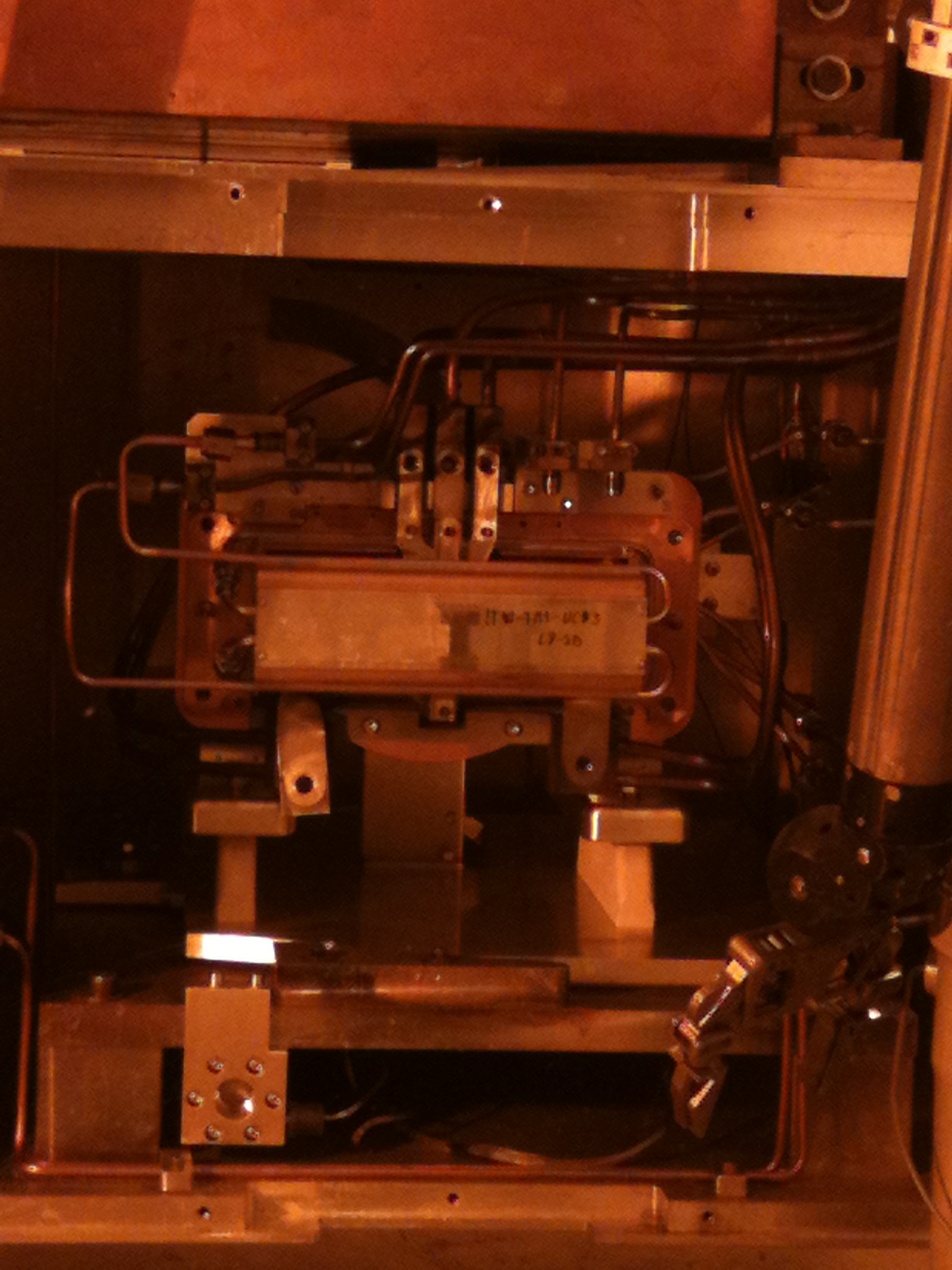
|
Monday, March 12, 2012, 09:19, Travis Cave, South Hot-Cell, Standard Operation, TM1, UCx#3, module move
|
TM#1 with UC#3 was moved from the west maa to the south hot cell, move went well |
Wednesday, February 01, 2012, 09:54, David Wang, ITW, Maintenance, TM1, , ITW and TM1 winter shut down vacuum leak check
|
ITW and TM1 winter shut down vacuum leak check had been finished yesterday.All ITW primary vacuum vessel, secondary vacuum vessel, and TM1water lines had been leak checked.No any leak has been found .The ITW and TM1 are both leak tight.Some detail information below:
TM1 and ITW primary vacuum vessel and water lines: The leak detector was hooked on BV2 after TP2. Calibrate leak detector.leak detector BL 0.0xe-9atm.cc/sec,BP0.0xe-4 torr.
Sprayed helium to all primary vacuum vessel seals, flanges, turbo pumps,gauges, blank offs, bellows, and insulation blocks on TM1 and ITW. No any response had been found on leak detector.Also applied 60 psi helium to all water lines in TM1 for 5minutes each,no any response on leak detector.The leak rate stayed at 0.0xe-9 to 0.3 xe-9 atm.cc/sec all the time. All waterlines in TM1 are leak tight.
ITW secondary vacuum vessel:the leak detector was hooked on BV4s after TP4.Leak detector BL 0.0xe-9 atm.cc/sec ,BP 0.00xe-4 torr. Sprayed helium to all secondary vacuum seals which include all bellows, tank to tank flange seals,tank flange to modules seals,beam diagnostics, gauges,turbo pumps, and EXIT 2 top service cap seals.No any response had been found on leak detector during the check. The secondary vacuum vessel is leak tight on ITW.
All high vacuum gauges were read at 2-3xe -7 torr range during the test time and no change during the test. |
Monday, January 16, 2012, 09:30, David Wang, ITE, Maintenance, , , Changed all old inducion coils for flow sensors in ITE
|
I had changed all old induction coils for flow sensors in ITE .I checked all ITE water signals on control boards in electrical room.They are all very stable and constant.All ITE inductions coils work fine now. |
Thursday, January 12, 2012, 14:32, David Wang, ITE, Repair, TM4, , TP2 on TM4 has been replaced
|
TP2 on TM4 has been replaced with a new turbo pump , I didnt reset the controller in electrical room.So this new pump start to run at 8083 hours on ITE TP2 controller. The new TP2 pump properly started. It works fine now. |
Thursday, January 12, 2012, 08:43, Travis Cave, Spent Target Vault, Standard Operation, , , Spent targets to F-308s
|
All targets in the mini storage have been moved to F-308s and those flasks have been moved over to rad waste. The transfer of target occurred on January 10th and the flasks were moved to rad waste on January 11th. Contamination was found on the bottoms of some of the pails and was removed, some of the contamination was difficult but not impossible to remove from the pail bottoms. |
Tuesday, January 10, 2012, 11:51, Grant Minor, Conditioning Station, Repair, , , IMC at Cond. Station is VENTED - DO NOT PUT MODULE IN
|
Hi Remote Handling,
The guage on the IMC circuit in the Target Hall is reading atmosphere, and the bellows is currently relaxed (i.e. expanded), whereas it should be reading about -20inHg and the bellows should be contracted (i.e. compressed).
I've attached a photo of what the guage and fittings should look like when pumped down to -30inHg.
Either the IMC circuit has been vented, disturbed, or it has some kind of leak. When I was in the Target Hall this morning, I saw the gauge bent around the railing at an awkward angle with a pretty severe bend in the copper line, it appeared to have been disturbed by the temporary glove box sitting at that level used by Rob Walker for nuclear ventilation work.
I will co-ordinate pump-down and leak check of the circuit, but the Conditioning Station cannot be used until this is repaired.
Cheers,
Grant
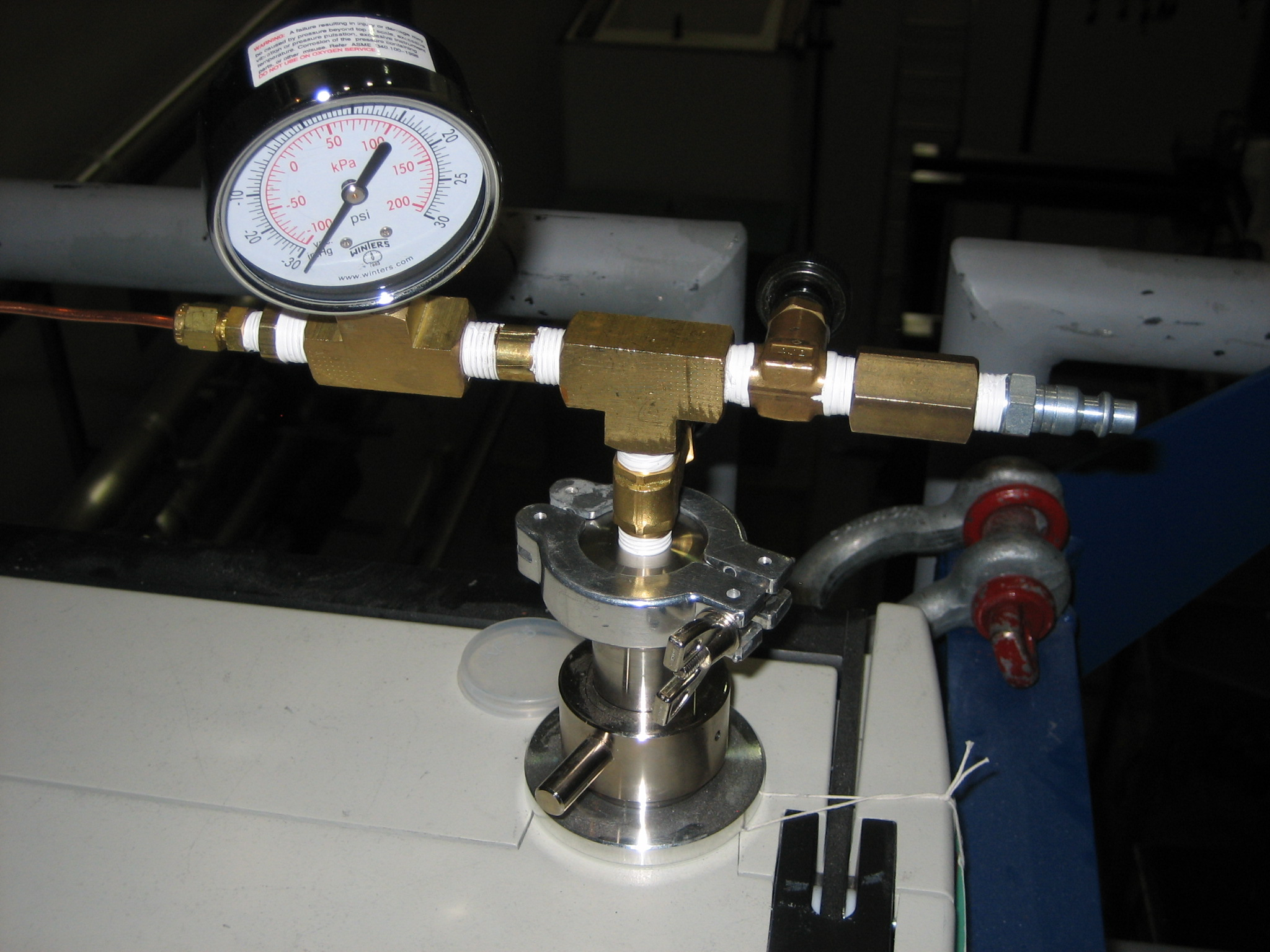 |
Monday, January 09, 2012, 14:44, David Wang, ITE, Maintenance, TM4, , ITE and TM4 2012 winter shut down leak check is completed.
|
I did a vacuum leak check on all ITE primary vacuum vessel and secondary vessel.I also did a helium pressure test(80psi ) on all TM4 water lines. There is no leak has been found.ITE and TM4 are both leak tight now.
ITE primary vacuum vessel and TM4 waterlines:
Hooked leak detector after TP1 between BV1. leak detector base pressure :0.0xe-4 torr. base leak rate:1.8x e-8 atm.cc/sec.sprayed helium around all TM4 and exit 1 ,2 module primary vessel including all flanges, gauges, bellows,turbos,blank offs,etcThere is no any response on leak detector. All water lines had been pressurized with 80 psi helium for 5 minutes. The leak rate always stayed at 1.8xe-8 atm.cc/sec which is the base leak rate on ITE this time, and no vacuum pressure change also.The TM4 water lines and ITE primary vacuum vessel are leak tight.
ITE secondary vacuum vessel:
Hooked leak detector after TP1S between BV1S. Leak detector base pressure :0.0xe-4 torr.Base leak rate:0.0xe-9 atm.cc/sec. Sprayed helium around all TM4,EXIt 1,2 module secondary vessel including alll flanges,gauges, air cylinders , valves, and blank-offs.There is no any response on leak detector . tThe late rate kept at 0.0XE-9 ATM.CC/SEC, and no pressure change either.The ITE secondary vacuum vessel is leak tight. |
Thursday, January 05, 2012, 11:40, Travis Cave, Spent Target Vault, Standard Operation, , , Target swapping 
|
Looks like the UC target s #1 and #2 were found invalidprize winners for their all inclusive trip to Chalk River and have thus been placed back in to storage for the next draw. In their place a pair of lucky Ta targets won, seems to be Ta lucky draw this year, Ta#28 and #29 have been placed in the mini storage for several fabulous day and wondrous nights, before being whisked away on their all inclusive one way trip to Chalk River. See attachments for the status of both vaults. |
Wednesday, January 04, 2012, 13:49, Travis Cave, Spent Target Vault, Standard Operation, , , Moving the spent targets to mini storage.
|
Well the first of this year's lucky winners to win a fabulous one way trip to Chalk River are as follows. UC#1, UC#2, Ta#25, Ta#26, and Ta#37. First these lucky winners will get to stay several days and night in the lovely all inclusive mini vault before being loaded in to their very own private F-308 flasks to be whisked away off to fabulous Chalk River. |
Thursday, December 15, 2011, 13:08, Travis Cave, Spent Target Vault, Standard Operation, , , Spent Target Assay
|
Spent target assay completed. A total of 16 target were looked at, 13 were low enough to be assayed and those 13 are at shippable levels, the other 3 of the 16 looked at were too hot to ship and assay. See attached pdf for complete details. |
Thursday, November 24, 2011, 10:40, Travis Cave, ITW, Standard Operation, TM1, UCx#3, Module move
|
TM#1 with UCx#3 moved from the conditioning station to the west target station. |
Thursday, November 24, 2011, 10:39, Travis Cave, ITW, Standard Operation, TM1, UCx#3, Module move
|
TM#1 with UCx#3 moved from conditioning station to west target station. Move went well. |
Tuesday, November 22, 2011, 15:07, Bevan Moss, Conditioning Station, Standard Operation, TM1, UCx #3, HV testing
|
High Voltage (HV) testing was completed on TM1 today. Vacuum was very good 1.9 x 10^-7 T in the service cap, 3.2 x 10^-7 in the containment box, and 2.0 x 10^-6 in the secondary. The voltage was successfully brought up to 27kV with a current draw of 0.12mA and o sparking. At the next step, 30 kV, the current draw was above 0.3mA and sparking was beyond 20 sparks per minute. The module should not be taken above 27kV. There is the possibility this voltage can be increased with conditioning but it is very unlikely. See attached for a graph of the testing. These results are comparable to the results without the source tray (see previous elog) |
Monday, November 21, 2011, 13:49, David Wang, Conditioning Station, Standard Operation, TM1, , TM1 full leak check in conditioning station
|
TM1 full leak check in conditioning station has been fulfilled this morning.Both air to vacuum leak check and waterlines helium 80psi pressure test are fine.The result:
Air to vacuum helium spray:base leak rate on leak detector 1.6x E-9 atm .cc/sec.base pressure0.0xE-4 torr. sprayed helium around all flanges, turbo pumps,panels,bellow,insulation stands, gauges. No Response on leak detector. Air to vacuum seals on TM1 is leak tight.
Helium pressure test on all water lines.with 80 psi helium 3minutes test:
PNG1 :2.4XE-7torr .PNG4 :2.6x E-6torr . IG1 :5.1xE-7torr.
A :target oven(+) BL:2.0xE-9 atm.cc/sec .First minute no response,then climbed to1.9xE-8 atm.cc/sec. Stabled at 1.9xE-8 atm.cc/sec to 3 minutes.
B:target oven(-) BL:5.5x E-9 atm.cc/sec.First 80 seconds no response, then climbed to 1.8xE-8atm.cc/sec. Stabled at 1.8xE-8atm.cc/sec to 3 minutes.
C:tube heater(-) BL:8.0xE-9 atm.cc/sec .First minute no response ,then climbed to 2.7xE-8 atm.cc/sec. Stabled at 2.7x E-8 atm.cc /sec to 3 minutes.
D: tube heater(+) BL: 1.0xE-8 atm.cc/sec. First minute no response , then climbed to 1.8xE-8 atm.cc/sec. Stabled at 1.8x E-8 atm.cc/sec to 3minutes.
G:EE BL:1.0xE-8 atm.cc/sec .First 1.5 minutes no response , then climbed to 1.7x E-8 atm.cc/sec. Stabled at 1.7x E-8atm.cc/sec to 3minutes.
F:heat shield BL:1.2x E-8 atm.cc/sec. First 1.5 minutes no response , then climbed to 1.9 xE-8 atm.cc/sec. Stabled at 1.9 xE-8 atm.cc/sec to 4 minutes. Total test time 4 minutes.
I: mounting plate BL:1.2 x E-8 atm.cc/sec. NO RESPONSE on leak detector in 3minutes.
M: window BL:1.2x E-8 atm.cc/sec First 1.5 minutes no response,then climbed to 2.0xE-8 atm.cc/sec . Stabled at 2.0xE-8 atm.cc/sec to 3minutes.
The base pressure on leak detector stayed at 0.0x E-9 torr through all the test, and no pressure response on high vacuum gauges. |
|