Tuesday, June 23, 2015, 10:24, Isaac Earle, Standard Operation, Other, Other, BL1A Holding Tank Water Released
|
The water in the BL1A holding tank was released to the city sewer. This water was sampled, tested, and approved for release by RPG two weeks ago. The total volume was 510L, a combination of water from the T2 and TNF systems. The total time required to pump out the water with all valves fully open was 1hr2m. Paperwork for the water release was completed and returned to RPG. |
Wednesday, July 15, 2015, 10:33, Isaac Earle, Standard Operation, Target 1, Cooling, T1 & T2 Cooling System Check
|
- All T1 and T2 values on XTPAGE were stripped back to April 1, 2015: All systems appear to be functioning normally, nothing unusual observed
- Expansion tank levels checked visually: T1 level at 1/2" above top sensor nut, T2 level at 1/4" below top sensor nut --> filled to 1/2" above
- Lower air amplifier in use; cool to touch; approximately 25s between each cycle (when air is exhausted from device) |
Monday, September 28, 2015, 10:29, Isaac Earle, Standard Operation, Other, Active Sump, RH Hot Cell Lab Active Sump High Level Sensor Tested
|
The RH hot cell lab active sump high level sensor was tested as part of the yearly scheduled inspection. High water level was simulated by tilting the sensor sideways with a long pole sample scoop. The Main Control Room and Hua Yang from Nuclear Medicine were notified before the test. The alarm sounded as expected, and a message was received in the main control room. This is a latching signal, so a Control Room operator will go to the MHESA RCR lab to reset the alarm. The water level was approximately 12" below the high level sensor, so the sump may need to be sampled and emptied soon. |
Wednesday, September 30, 2015, 17:07, Isaac Earle, Standard Operation, Target 2, Target, Target Moves for Profile Check - Possible Motor or Control Box Failure
|
The T1 and T2 targets were moved to position zero, then back to the target position today so that beam profile could be checked using the profile monitors. Movement for both targets was done with the portable control box.
The T1 target was moved from Position 4 to Position 0, then back to Position 4 (after checking the profile) with no issues.
While moving the T2 target from Position 4 to Position 0 the ladder stopped moving part way through travel. By toggling the control box "RUN / OFF" switch the motion could be restarted. This had to be done 2 or 3 times to reach Position 0. When returning to Position 4 after checking the profile the problem became more severe. It took over 20 minutes to move from Position 0 to 4 because the ladder only moved slightly or not at all each time the switch was toggled. This is either due to a failed motor on the target, or failure of the portable control box.
The next step will be to try moving the ladder of one of the target assemblies in the storage pit to determine which is at fault. In the mean time neither the T1 nor T2 target ladder should be moved. |
Friday, October 02, 2015, 17:25, Ron Kuramoto, Standard Operation, Target 1, Target, Raise Target to lower Rad levels for 1AM7 repair
|
Today the T1MK2 target was moved from Position 4 to Position 0 to lower the Rad fields for the 1AM7 repair in the 1A Tunnel. The Rad levels were still to high only dropping by 1000uSv/Hr to 5000uSv/Hr, so the 1AM7 repair is planned for next Tuesday's maintenance day on Oct 6th. 1A will be off till then giving a longer cool down.
The target was then moved moved back to Position 4 with the Pot ratio reading 0.699. The target was moved using the portable Control box. The "power on light" on the Control box needs to be replaced.
Note: The MS connector on the 1AT2 cable needs to be tighten before using. It became loose when swapping the portable Control box cable to the 1AT1 cable.
The cooling package turned on ok after the vacuum was established.
Don Jackson assisted me with this operation and was appriciated....
|
Monday, October 05, 2015, 15:25, Isaac Earle, Standard Operation, Other, Other, Old T2 Protect Monitor Cassette Update
|
The T2 protect monitor cassette removed in April 2015 (see E-log #154) was surveyed today. It was approximately 3mSv/hr at 0.5m and 15mSv/hr on contact. It is unlikely that this monitor will ever be cool enough for hands-on elevation adjustment that it requires, therefore it has been bagged, labeled, and transferred to the east hot cell for storage. |
Tuesday, October 13, 2015, 10:52, Isaac Earle, Standard Operation, Target 1, Target, T1 & T2 Target Ladder Moves
|
The T1 and T2 targets were both moved from Position 0 to Position 4 at approximately 2:30am on Saturday October 10th using the portable control box. Operations had tried to move the T1 target to position 4 using the old control system but for unknown reasons it would move to any position except position 4 and the portable control box had to be used. The portable control box should continue to be used for T1 and T2 target moves until the new control system is installed in the 2016 shutdown. |
Monday, January 18, 2016, 17:19, Isaac Earle, Standard Operation, Target 1, Cooling, T1 & T2 Packages Drained; BL1A Holding Tank Released
|
The T1 and T2 cooling packages were drained to the BL1A holding tank on Jan 8 2016. The volumes were 100L and 80L respectively. Before starting there was 350L of water in the holding tank from the 500MeV system which Steve Sapriken drained in September 2015. The T1 and T2 systems were sampled and delivered to RPG. After receiving permission from RPG to release all 3 portions of water it was pumped into the city sewer on Jan 18, 2016. |
Wednesday, February 03, 2016, 17:35, Isaac Earle, Standard Operation, Target 2, Cooling, T2 MRO Work
|
The following work was performed at the T2 cooling package and target between Jan 25 - Feb 3, 2016:
- Cuno water filters removed (2), and new filters installed
- Target water solenoid, H.E. secondary side solenoid, Collimator A solenoid, and Collimator B solenoids removed and replaced with new 24V DC versions
- All thermistors removed and replaced with Type K thermocouples
- All Proteus paddle wheels, o-rings, and paddle wheel pins replaced (5 sensors total)
- Target side #6 Hansen QD fittings replaced
- All air QD fittings (6 total) for profile monitor actuation were replaced, some of the flexible hosing was replaced (cracking), and the flexible hose assemblies were checked for gross air leaks
- Top surface of the cooling package resin can support platform was painted (was rusty)
- Resin can swapped (previous resin swap was during Shutdown 2014)
- Target water check valve was removed and tested (working as expected), then reinstalled |
Thursday, March 31, 2016, 11:48, Isaac Earle, Standard Operation, Target 1, Target, T1 & T2 Beryllium Target Manufacturing Complete
|
Manufacturing of a new batch of T1 and T2 beryllium targets has been completed.
The job was completed under Machine Shop Work Order #41527. Eleven 12mm T1 targets (TBP1683) and seven 10cm T2 targets (TBP1691) were completed (exhausting all stock of the leftover EDM'd target housings). The target window profiles (TBP1695) were laser cut at an outside shop for greater precision and to save time. The target window assemblies were electron beam welded to the target housings (TBP1687 & TBP1692) by Bob Welbourn. The remainder of the tube welds were completed by George Sun. Assembly of the Swagelok fittings, target inspections, hydrostatic testing, and final helium leak checks as specified on the assembly drawings were performed by Isaac Earle. In addition to these tests, one spare target housing was pressure tested to 275psi (the max pressure of the regulator of target jig TBP1721). The target windows bulged at this pressure, but did not rupture.
The attached spreadsheet has details on target measurements and test results. The target serial numbers (listed in the spreadsheet) have been engraved on the 90 degree elbow of each target on both the entrance and exit side. Detailed photographs were taken of each target which are stored on Isaac Earle's hard drive (too large to attach).
If the 2015 target replacement plan is followed (See E-Log #168), these targets should last for at least 10 years.
|
Monday, April 11, 2016, 13:54, Isaac Earle, Standard Operation, Target 2, Target, T2-MK2 Target Transported from BL to HC
|
The T2-MK2 target was transported from the beam line to the hot cell using the transfer flask. The target was measured to be 120mSv/hr at 0.5m. The steel shielding plug was installed in the T2 target hole to reduce upwards shine.
New beryllium target cassettes will be installed on the target ladder before it is returned to the beam line. |
Friday, April 15, 2016, 14:54, Isaac Earle, Standard Operation, Target 2, Target, T2-MK2 Target Changes & Return to Beamline   
|
On April 11th the T2-MK2 target was flushed with water, then overnight with air at 5psi supply pressure. The target ladder was in Position 0 for this procedure.
On April 12th the target was pumped using a cold trap and the Varian leak detector for approximately 2 hours.
On April 13th pumping was restarted and the leak detector reached 0.0E-10 Torr*L/s with < 1.0E-3 Torr test port pressure. A general helium spray was performed with a small response to the mid 10^-9 range and quick recovery (this target was in use all of the 2015 running period w/o any vacuum issues). Plugs were removed from Positions 1 & 2. The swagelok threads on the ladder were cleaned with a wire brush then pressurized air. The sealing surfaces were cleaned using Scotchbrite then blown with air. Threads and sealing surfaces were inspected with the Nikon level: some minor thread imperfects on the threads and a few small pits on the sealing surfaces were observed. New 10cm beryllium targets were installed (Position 1: Target "OCT.06#3", Position 2: Target "#201"). A leak check was performed using 0.5s bursts of helium at supply pressure 3psi. Helium was applied at all target positions, delta seal locations, and along the length of both bellows. No responses observed that were greater than the initial leak check performed before the plugs were removed, therefore the target was deemed water leak tight and ready for use.
On April 14th position measurements for both new targets were taken as per Document-50194, which will be included in the target info sheet to be delivered to Operations.
On April 15th the target was returned to the beamline. All services were attached, the cooling package started, and vacuum pumped down normally.
Photographs of the Position 4 beam spots as well as the target ladder after new target installation are attached. |
Wednesday, April 20, 2016, 10:01, Isaac Earle, Standard Operation, Target 1, Target, T1/T2 Monitor Electrical Check Complete
|
Mike Russell from Diagnostics Group has completed an electrical check on the T1 and T2 profile and protect monitors. He reports that both profile monitors look fine. The T1 protect monitor looks fine except for a weak or missing signal from the halo monitor. The T2 protect monitor looks fine.
Note: The protect monitor on the T1-MK2 target was working without issue during the previous running period and was not removed from the beam line during the 2016 shutdown. The cable for the T1 protect monitor was not disconnected during the 2016 shutdown. |
Friday, May 13, 2016, 15:04, Isaac Earle, Standard Operation, Target 2, Target, T2-MK2 Position 4 Adjusted to +1.5mm Offset
|
The T2-MK2 target at Position 4 has been adjust to approximately +1.5mm offset. This causes the ladder to be moved downwards, raising the beam spot location on the target window. The potentiometer ratio at this offset is approximately 0.810 (> 0.8059 nominal ratio for position 4, and therefore closer to Position 5)
The purpose of the offset is to better center the beamspot on the target window. Target window photographs showed the beam spot being slightly below center (See E-Log #197), and target ladder elevations taken in Spring 2016 showed the Position 4 target approximately 1.0mm above the profile monitor center.
MCR has been instructed to continue running with this offset, and a message with details on how to do so was posted to their Plone site. |
Wednesday, June 15, 2016, 11:00, Isaac Earle, Standard Operation, Target 2, Target, T2-MK2 Target Moved to Position #1
|
Position #4 on the T2-MK2 target has now reached the maximum beam time. The target was moved to Position #1 at the nominal elevation. This target should be used for the remainder of the 2016 running period. |
Monday, January 09, 2017, 15:07, Isaac Earle, Standard Operation, Target 2, Target, T2-MK2 Target Moved from BL to HC
|
The T2-MK2 target assembly was moved from the beam line to the hot cell today. A maximum field of 203mSv/hr was measured at approximately 0.5m
A steel shielding plug has been installed in the T2 hole to reduce shine and allow the T2 volume to be pumped down. |
Thursday, January 12, 2017, 09:21, Isaac Earle, Standard Operation, Target 2, Target, T2-MK2 Position 1 Beam Spot 
|
The beam spot on the 10cm beryllium target in Position 1 on T2-MK2 (Target ID: "OCT.06#3") was measured and photographed yesterday. A fairly well centered spot was measured to be approximately 4.6mm wide x 5.2mm tall on the entrance window and 5.7mm wide x 7.6mm tall on the exit window using the Nikon micrometer level. This target first saw beam on June 16, 2016.
A PDF scan of the beam spot measurements and photographs of the beam spots are attached.
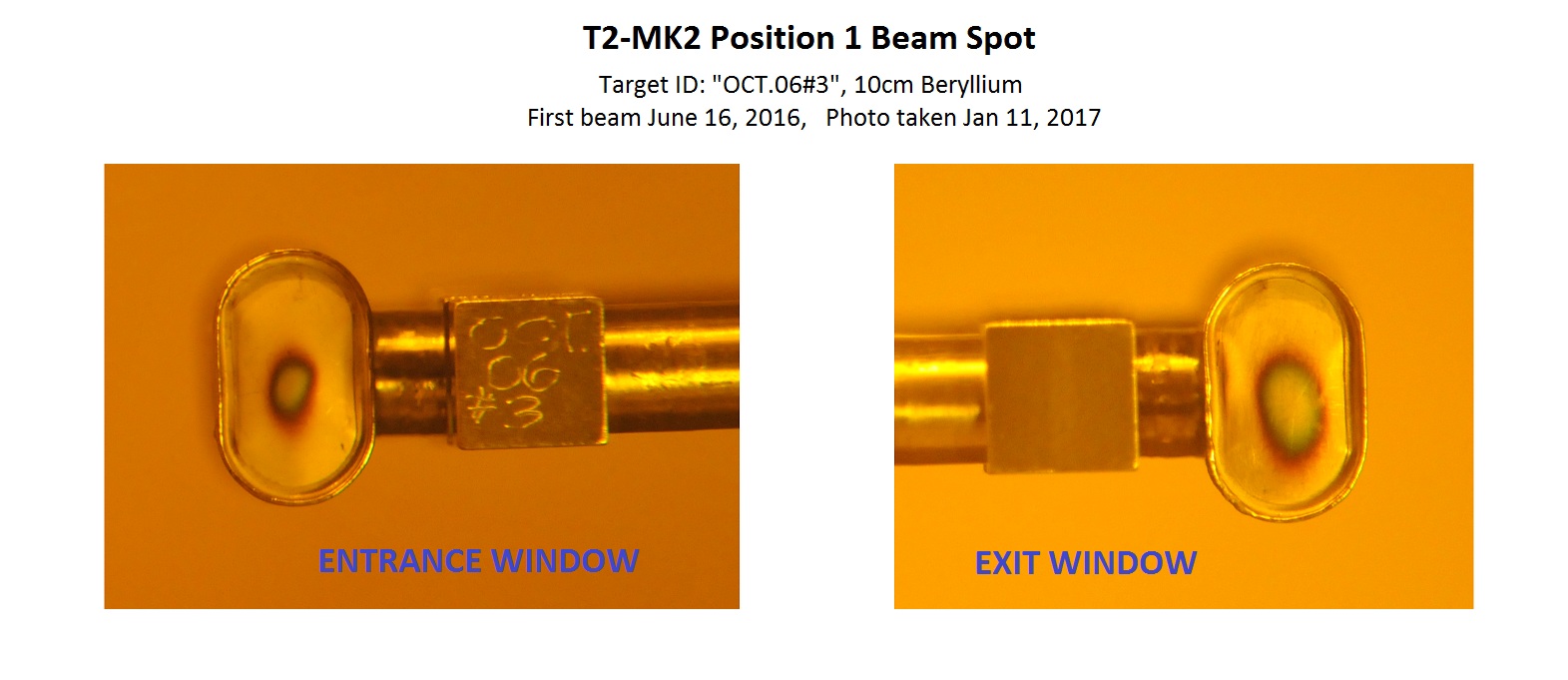
|
Thursday, January 19, 2017, 08:55, Isaac Earle, Standard Operation, Target 1, Cooling, T1 MRO work complete
|
The following work was completed on the T1 cooling package:
- water drained to BL1A holding tank
- all resevoir o-rings changed
- all cuno filters changed:
M15 permanent magnet filter < 5uSv/hr at 0.5m, dark grey colour
Target inlet filter 210uSv/hr at 0.5m, light brown colour
Resin filter, <5uSv/hr, looks clean and new
- package re-filled and started
- demin circuit flow tuned to 1.0gpm
- #6 female Hansen fittings at target end of flexible hose swapped for previously used SS models (zinc coated steel models (PO# TR207041) were accidentally ordered and installed last shutdown and had black corrosion on the inside)
The T2 cooling package was also drained to the 1A holding tank.
After approval from RPG the holding tank water was released.
Note: the appearance of the used cuno filters is consistent with previous years. |
Wednesday, March 15, 2017, 16:13, Isaac Earle, Standard Operation, Other, Active Sump, Meson Hall Hot Cell Lab Active Sump Water Released
|
On March 13th in the morning the Meson Hall Hot Cell Lab active sump reached the high level sensor. The system responded as expected: high level panel warning light illuminated, siren sounded, and MCR notified via "B1 RCR1 RM6 WARN". A 1L sample was delivered to RPG for analysis. After approval, the sump was pumped out over the following two days. The procedure in Document #64834 was followed for sampling and pump-out. |
Tuesday, October 10, 2017, 12:09, Isaac Earle, Standard Operation, Target 2, Target, T2-MK2 position 4 target changed  
|
The following work was performed on the T2-MK2 target assembly during the 2017 fall shutdown:
Oct 4, 2017:
- Target moved from beamline to hot cell, measured 661mSv/hr at 0.5m (move went smoothly, having camera views at N/S and E/W angles very helpful)
- Flask tray wet wiped after transfer: 1st wipe 600cpm on 44-2 monitor, 2nd wipe 900cpm (3rd swipe not taken because tray looked clean)
- Flushed target with clean water, then compressed air (positions 0 through 5)
- Male Hansen fittings on the target assembly swapped with new units (in process of replacing all self sealing fittings in T1 and T2 water system)
- Checked all micro-switch positions and potentiometer readback: switches ok, pot value jumpy around position 1 and 2 (known from before), otherwise fine
- Left target overnight at position 4 with 20psi supply air running through to dry water system
Oct 5, 2017:
- Pumped down target with cold trap (~2 hours)
- Baseline leak check performed: 6 mins to reach 5.0E-3 Torr (3.2E-9 Torr*L/s), 21 mins to reach 1.0E-3 Torr (1.4E-10 Torr*L/s)
- Helium spray at 3psi for 0.5s bursts, tested with ladder in position 4
- No leak at any target positions or plugs
- Small leak on left side bellows, or bellows seal to ladder: up to 8.0E-9 Torr*L/s response, then quick recovery (known from previous leak checks, same magnitude)
- Small leak on right side bellows, or bellows seal to ladder: up to 2.0E-8 Torr*L/s response, then quick recovery (known from previous leak checks, same magnitude)
- Beam spot photos taken, position 1 (only target used this running period) has fairly well centered beam spot (see below)
- Position 4 target removed ("JAN29'97"), was very difficult to remove because one water tube stuck in ladder (this target was installed on ladder in 1997! First beam 2014)
- Used hammer in hot cell to remove which eventually broke the target water tubes from the wire EDM housing
- sealing surfaces cleaned with burgandy Scotchbrite on electric dremel tool
- Inspected sealing surfaces and ladder fitting threads using Nikon level: all appeared clean and undamaged
- Installed new 12mm beryllium target at position 4 ("Jul.06#4"), no issues with install
- Leak check repeated: reached 1.0E-3 Torr after 3 minutes (1.3E-8Torr*L/s)
- Down to 3.5E-9 Torr*L/s after 18 mins, began test
- No response at all target positions, checked left side bellows: same response as above
- Beam spot profile at Position 1 measured with Nikon level
- Vertical and horizontal positions of new Position 4 target measured
- New profile monitor cassette retainer pin installed (plate hole had to be opened up to 0.375" diameter), used vice grip pliers clamped onto clevis pin in order to install
Oct 6, 2017:
- Profile monitor actuation tested: start movement 5psi, fully IN at 35psi
- Profile monitor limit switches tested, ok
- Target transported back to beamline, no issues
- BL1A pumped down, Edi reported pump-down normal
- Electrical check performed on T2 profile monitor from mezzannine: Sheng-Li reported results normal
- Cooling system started: no change to BL1A vacuum
- Target info sheet and target elevations sheet delivered to Main Ops
- XTPAGE 7L information updated
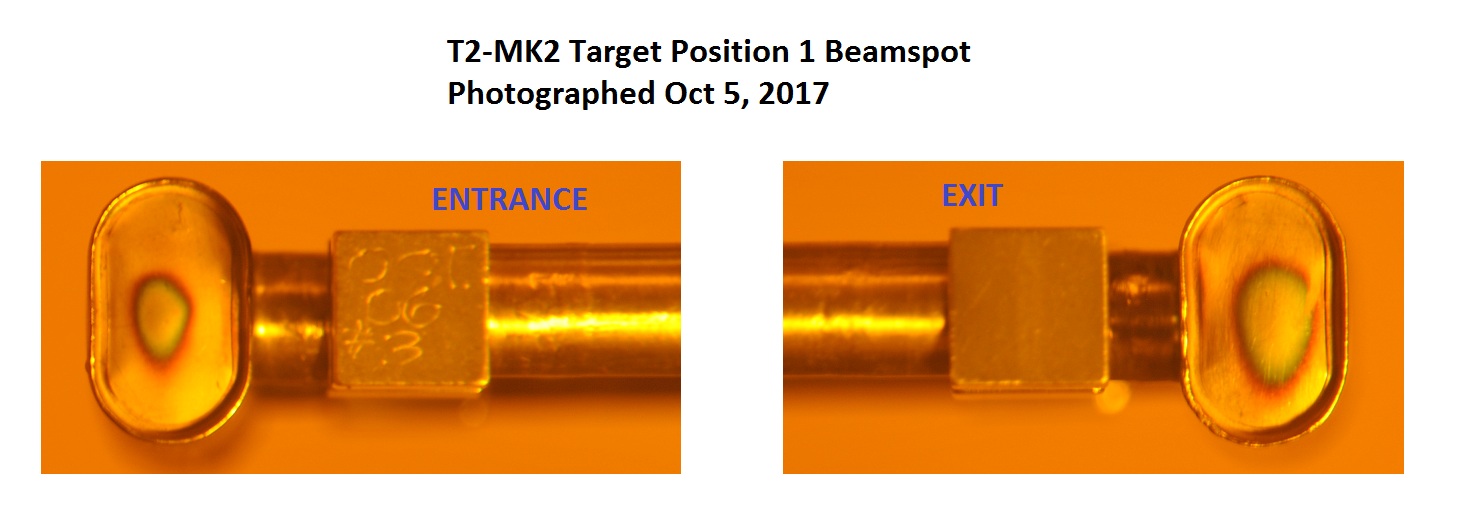
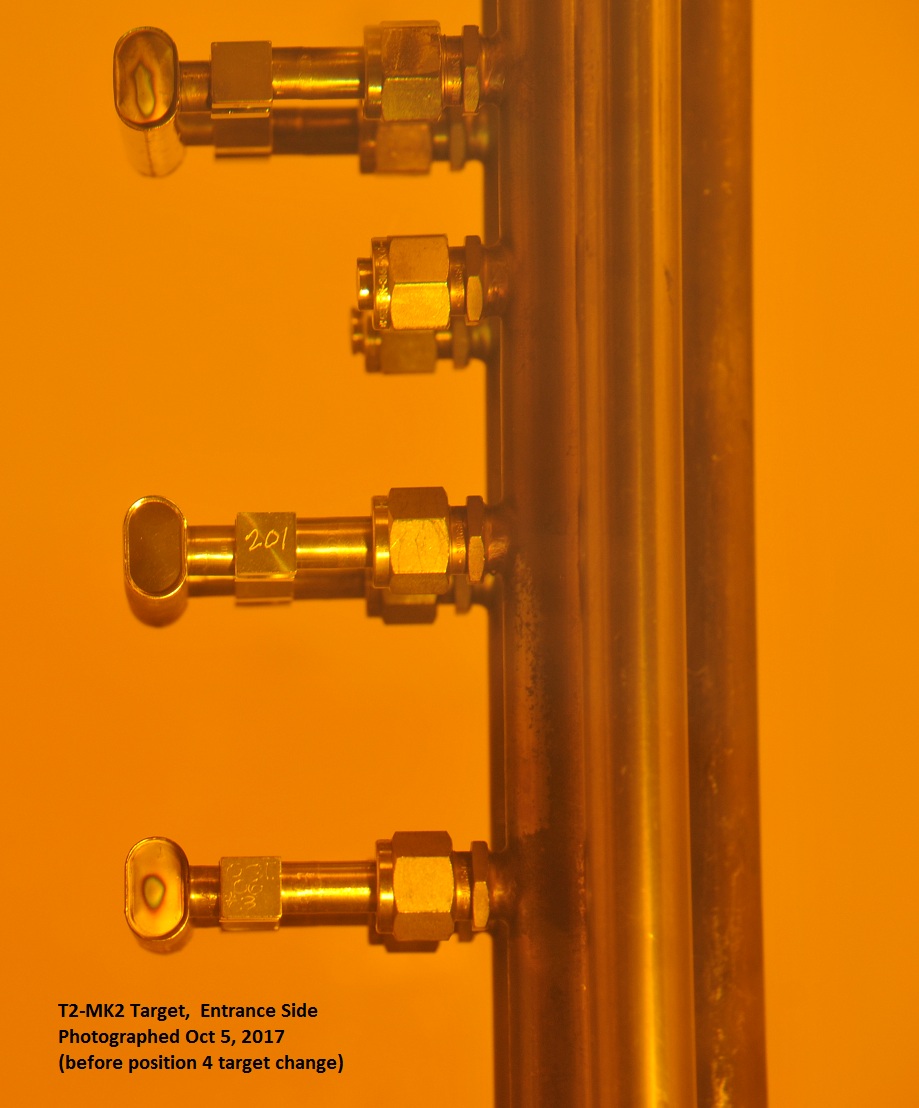
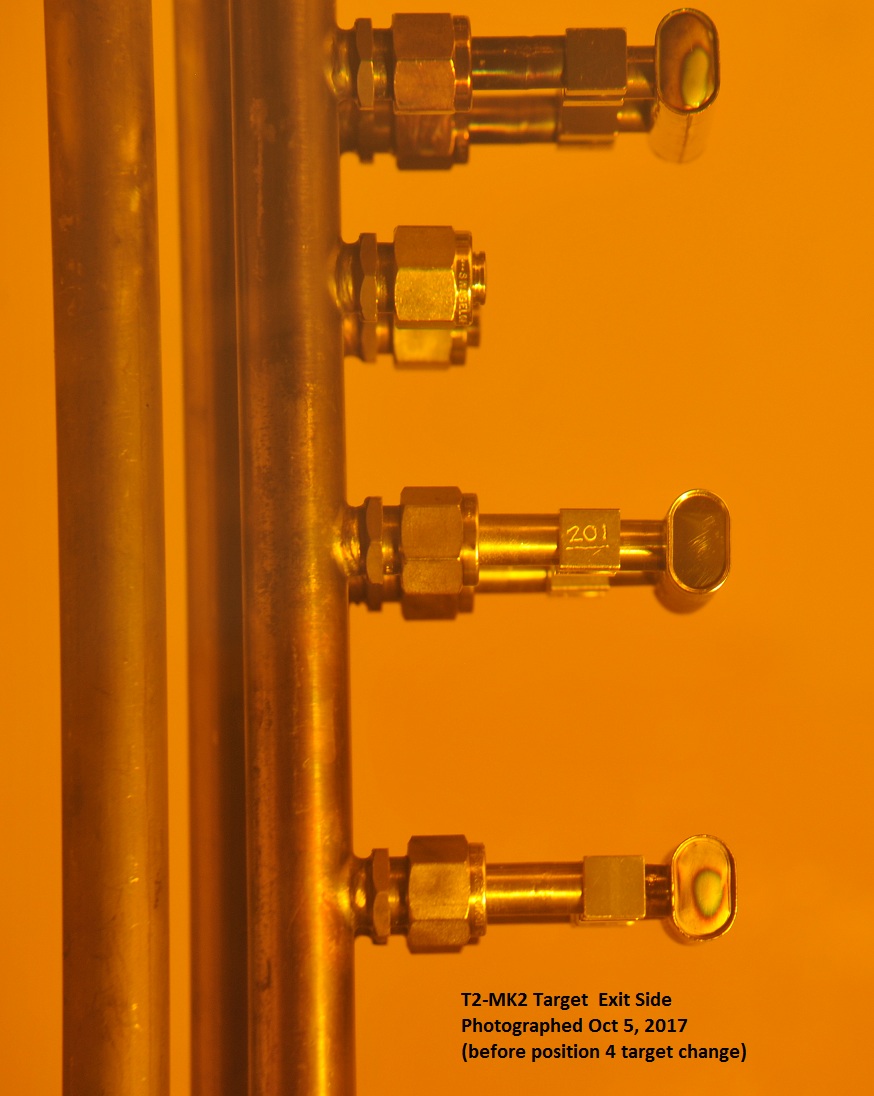
|
|