|
ID |
Date |
Author |
Category |
Type |
Module |
Target/Number |
Subject |
|
835
|
Monday, January 26, 2015, 09:36 |
chad fisher | South Hot-Cell | Repair | TM2 | | TM2 Tray Alignment |
TM2 tray alignment was confirmed with the alignment tray this morning:
Front target 0.000 vertically, 0.000 horizontally.
Back target 0.003 low, 0.000 horizontally
Also, the master target jig was installed and measurements taken:
Front master target - 0.007 high, 0.000 left/right
Rear Master Target - 0.007 high, 0.000 left/right
Rear tray target - 0.003 low
|
Attachment 1: TM2_Tray_20150126_090448.jpg
|
|
|
836
|
Wednesday, January 28, 2015, 10:42 |
Anders Mjos | Conditioning Station | Maintenance | TM2 | | TCS shut down for site wide power outage |
|
|
837
|
Thursday, January 29, 2015, 11:31 |
chad fisher | South Hot-Cell | Repair | TM2 | | TM2 Tray Build |
On Tuesday morning I attempted to complete assembly of the source tray for TM2 however discovered that 3 1/4-20 x 0.25 titanium helicoils had not been installed into the mounting plate as they should have been. Checked and asked around for them but to no avail. I have ordered some, they should have been here yesterday.
Also, I have noticed that the threaded portion of the target pins ITA0328A appear to be too long and as such may be (are indeed) touching the supports. I am going to remove 1/32" or appropriate to remedy this problem (drawing shows 0.035 clearance). |
Attachment 1: TM2_Tray_20150126_112232.jpg
|
|
|
838
|
Monday, February 02, 2015, 09:59 |
chad fisher | South Hot-Cell | Repair | TM2 | | TM2 Tray Build |
Missing heli coils installed this morning.
Threads had to be chased with tap for 1/4-20 heli coil and missing countersinks hand applied to allow for installation. Care was taken to ensure no "swarf" was spread and operation was super clean. Chased holes blown out with canned air and a vacuum placed on the other side.
Final assembly can and will now continue. |
|
839
|
Monday, February 02, 2015, 14:06 |
chad fisher | South Hot-Cell | Repair | TM2 | | TM2 Tray build |
Master target jig installed to locate attachment bracket ITA3389 as well as conductor insulator block b (aluminum / for soldering version) and oven conductor blocks (ITD0353 and 03356).
There were NO ITA6145 fasteners or TGN0076 either. Standard 1/4-20 x 1" fasteners have been used in there place for now. Keith is following up with getting the missing fasteners into the shop.
Oven conductor blocks will have to be lapped before lines are attached as they both have dents on the high current mating surfaces.
|
Attachment 1: TM2_Tray_20150202_134752.jpg
|
|
Attachment 2: TM2_Tray_20150202_134759.jpg
|
|
|
858
|
Thursday, March 12, 2015, 09:48 |
Travis Cave | South Hot-Cell | Standard Operation | TM2 | No target | Module move |
TM#2 with no target and no source tray has been moved from the conditioning station to the north east silo. |
|
879
|
Tuesday, March 31, 2015, 11:36 |
chad fisher | South Hot-Cell | Development | TM2 | | TM2 Optics Tray Complete |
TM2 optics tray is complete.
Master alignment tray: 0 up/down, 0 left/right
Optics tray: Front 0 up/down, 0 left/right. Middle 0 up/down, 0 left/right. Back 0 up/down, 0 left right.
|
Attachment 1: 20150331_OPTICS_FRONT.jpg
|
|
Attachment 2: 20150331_OPTICS_MIDDLE.jpg
|
|
Attachment 3: 20150331_OPTICS_BACK.jpg
|
|
|
893
|
Tuesday, April 21, 2015, 13:01 |
Grant Minor | ITW | Development | TM2 | | TM2 MK4 Optics Tray - banana plug bore modification (on bench) |
The MK4 optics tray prepared for TM2 (as per ITA6082) had an undersized bore for the banana plug, making insertion of the plug extremely difficult / impossible.
Reference stores parts were collected to check the fit: male plug 3-4/01152 and female jack 1-6/1201. The size of the female jack was checked with a #21 drill at .159".
The bore on the optics tray was drilled out dry using the #21 drill to the same depth as the original blind hole, by Maico and Dan McDonald. Chips were carefully collected in a rag, and the hole was blown out with compressed air.
The fit was checked to be snug but possible, using the male plug and the Remote Handling ultem base (ref ITA6023).
Redlines and photos are attached.
|
Attachment 1: ita6092_redlines_gminor_21apr2015.pdf
|
|
Attachment 2: TM2_Optics_Tray_Bore_Mod_21Apr2015_1.JPG
|
|
Attachment 3: TM2_Optics_Tray_Bore_Mod_21Apr2015_2.JPG
|
|
Attachment 4: TM2_Optics_Tray_Bore_Mod_21Apr2015_3.JPG
|
|
|
899
|
Monday, April 27, 2015, 16:12 |
Keith C Ng | South Hot-Cell | Development | TM2 | | Ceramic Standoffs in TM2 source tray steerer assembly |
On drawing ITA6008 for the Encole 0.5" ceramic standoffs there is a note to match pairs of ceramics to within +/-0.001". This step was missed on the current build of TM2 source tray (ceramics were not measured).
Measured the lengths of the rest of the ceramic standoffs in inventory and they range from 0.5035" to 0.4950" in length. The ceramics have been sorted by length and grouped into bags.
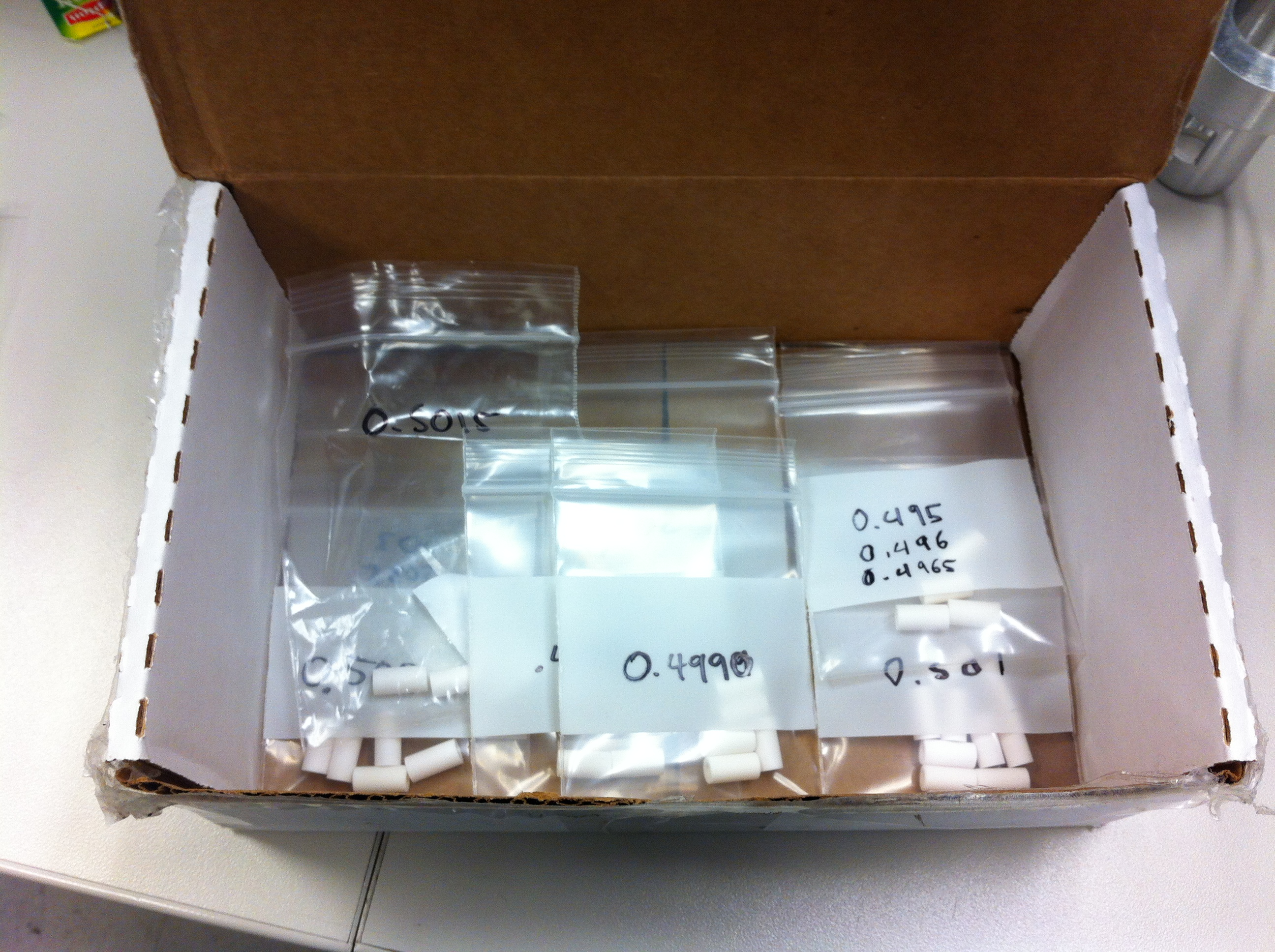 |
|
900
|
Monday, April 27, 2015, 17:09 |
Grant Minor | ITE | Development | TM2 | | TM2 - New Source Tray - Water Block Seal Groove Inspection Report |
The water blocks soldered to the TM2 cooling lines (see Ref. Assy. ITA6144) were inspected.
See attached inspection reports and drawings.
It was found that only 18% of the seal groove diameters and 55% of the depths were in spec.
The source tray must be tested on the test stand with c-seals to ensure that these blocks will seal properly on the module. |
Attachment 1: IMG_1859.JPG
|
|
Attachment 2: TM2_New_Source_Tray_Water_Block_Inspection_Results_24_April_2015.pdf
|
|
Attachment 3: TM2_water_block_inspect_24Apr2015.pdf
|
|
Attachment 4: TM2_New_Source_Tray_Water_Block_Inspection_Results_April_2015.xlsx
|
|
906
|
Thursday, April 30, 2015, 08:50 |
Travis Cave | South Hot-Cell | Standard Operation | TM2 | No target | Module move |
TM#2 with no source tray has been moved from the north east silo to the south hot cell. |
|
907
|
Friday, May 01, 2015, 08:27 |
chad fisher | South Hot-Cell | Repair | TM2 | | Containment Box Removal |
Containment box has been removed in preparation for wire replacement. |
|
908
|
Friday, May 01, 2015, 13:48 |
David Wang | South Hot-Cell | Standard Operation | TM2 | | Target Hall Scheduled Activities April 07 - June 26 2015 update |
Target Hall Scheduled Activities April 07 - June 26 2015 update. 2015-05-01. All TH scheduled jobs are finished on time this week. |
Attachment 1: Target_Hall_Scheduled_Activities__Apr_07_to_June_26_2015.mpp
|
Attachment 2: Target_Hall_Scheduled_Activities__Apr_07_to_June_26_2015.pdf
|
|
|
910
|
Tuesday, May 05, 2015, 10:57 |
chad fisher | South Hot-Cell | Repair | TM2 | | TM2 Wiring |
Old wiring was removed yesterday, new wiring run thru the vacuum chase. Old IMG gauge removed today, new cable trays installed and wires installed into cable trays. |
Attachment 1: TM2_New_Wiring_20150504_13.jpg
|
|
Attachment 2: TM2_Wiring_20150505_10.jpg
|
|
|
911
|
Wednesday, May 06, 2015, 14:30 |
Travis Cave | South Hot-Cell | Repair | TM2 | No target | Wiring of TM#2 |
Wires for TM#2 steering elements, and png gauge have been run down to the containment box level. Chad has placed them in the little cable trays. Slack has been pulled back. and termination of the wire will be done on the 7th of May. A modification was done to the signal line of the png gauge wire ultem block, as grounded screw was inserted to allow for strain relief so the end would hopefully quit breaking. See attached pictures for the details. |
Attachment 1: Photo_2015-05-06_8_26_10_AM.JPG
|
|
Attachment 2: Photo_2015-05-06_8_26_17_AM.JPG
|
|
|
912
|
Thursday, May 07, 2015, 11:02 |
Travis Cave | South Hot-Cell | Repair | TM2 | No target | Wiring of TM#2 |
Wires in TM#2 have been terminated at the top of the module. |
|
914
|
Monday, May 11, 2015, 11:20 |
David Wang | South Hot-Cell | Standard Operation | TM2 | | Target Hall Scheduled Activities April 07 - June 26 2015 |
The schedule has some changes due to new TM2 source tray coil cooling line leaking at test stand. Now,It is re-scheduled in such an estimation that TM2 source tray could be ready at teat stand by this Friday(May-15th). see attachment 1,2.
2015-05-12, Changed and updated the TH activity schedule according to Dons new beam schedule which is re-arranged after the coil line leaking issue. See attachments 3,4. No major conflicts has been found on the new schedule.
2015-05 25, Updated the TH activity schedule according to present TM2 job processing. See attachment 5,6. |
Attachment 1: Target_Hall_Scheduled_Activities__Apr_07_to_June_26_2015.mpp
|
Attachment 2: Target_Hall_Scheduled_Activities__Apr_07_to_June_26_2015.pdf
|
|
Attachment 3: Target_Hall_Scheduled_Activities__Apr_07_to_June_26_2015.mpp
|
Attachment 4: Target_Hall_Scheduled_Activities__Apr_07_to_June_26_2015.pdf
|
|
Attachment 5: Target_Hall_Scheduled_Activities__Apr_07_to_June_26_2015.pdf
|
|
Attachment 6: Target_Hall_Scheduled_Activities__Apr_07_to_June_26_2015.mpp
|
|
915
|
Wednesday, May 13, 2015, 13:55 |
chad fisher | South Hot-Cell | Repair | TM2 | | Shutter removal |
TM2 has been successfully de-shuttered.
All went pretty much according to plan except I had to remove one fastener out of the upper wiring harness (the one that has just been installed) to allow for enough clearance to rotated the shutter guide out of the way...I shutter to think what would have happened otherwise...anyways...
Close inspection of the shutter does show that the "thin" area isn't in very good shape; whether this is a result of removal or just the way it was is hard.Due to the ease of removal I would quess that it may have been a preexisting condition. That being said...I think we may want to consider replacing it.
|
Attachment 1: TM2_20150513_131339.jpg
|
|
Attachment 2: TM2_20150513_134232.jpg
|
|
|
917
|
Tuesday, May 26, 2015, 11:49 |
Grant Minor | Assembly/Bench Test | Repair | TM2 | | TM2 New Source Tray - Braze & Solder Report - 22 May 2015 |
Hello,
For reference, I have attached a list of all solder joints in the TM2 Source Tray, and the alloys used for the most recent build (as per ITA6144). I have also provided data sheets for the alloys, and PDF copies of all the drawings calling out the joints.
Certanium 34 C (222 deg C melt point) was used for all low-temperature solder applications, except for the steel inserts in the water blocks. Previous revisions of the Source Tray drawings called out a higher-temperature McMaster lead-based solder (304 deg C melt point). The change to Certanium 34 C on the prints was made in Bevan's era, during the transitional update of the source tray drawings between the TM1 and TM3 source tray projects, just before I took over updating the drawing packages. I believe Bevan made this change on general advice from Guy Stanford, who stated that Certanium 34 C is a much easier solder to work with and makes a more mechanically reliable joint. However, the change really should have had more review and validation testing before being implemented.
This said, we now have a source tray that uses Certanium 34 C, and rework of every joint would set us back too far in the schedule to meet the deadline, so we will have to run with it as it is.
Of particular concern are the joints on the target oven and coil heating blocks, which are now using a lower temperature solder (222 deg C melt vs 304 deg C melt). We have experienced a coil block failure on TM4 due to a failed solder joint, although the failure mode is not known for certain. We also had two recent failures on the test stand of a coil joint soldered with Certanium 34 C, but this was due to an error in the connection of cooling water to the joints (i.e. the joints had no coolant flow and the solder melted... this is expected!).
Anders and I have performed independent thermal analysis on the joints due to the radiative and electric heating from the target, and have concluded that even with a lower temperature solder, there is a lot of margin, so the risk seems to be low. This work will be published in a separate report to be circulated later.
Thank you and regards,
Grant |
Attachment 1: TM2_Source_Tray_-_Braze_and_Solder_Report_File_-_22May2015.pdf
|
|
Attachment 2: 1005_Bare_DS.pdf
|
|
Attachment 3: 1005_Bare_MSDS.pdf
|
|
Attachment 4: Certanium_34C_Data_Sheet.pdf
|
|
Attachment 5: Certanium_34C_MSDS.pdf
|
|
Attachment 6: mcmaster_carr_solder_7667A23.pdf
|
|
|
918
|
Tuesday, May 26, 2015, 14:34 |
chad fisher | South Hot-Cell | Repair | TM2 | | Shutter replacement |
The shutter in TM2 was successfully replaced today.
New lock washer and nut were installed onto shutter and nut torqued to 120 ft lbs.
Shutter guide alignment tool was used to insure tapped shutter guide holes were concentric with thru holes in shutter side mounting panel, button head screws replaced and torqued to 110 ft-lbs.
The shutter was manually cycled open and closed by David and everything is to operate well. |
Attachment 1: Shutter.jpg
|
|