Thursday, June 30, 2011, 16:47, John Wong, Development, Target 1, Target, Testing Elog
|
blah blah blah.... fjda;jfeowifjoajglfa;nafg |
Wednesday, May 14, 2014, 20:36, Grant Minor, Development, Target 2, Target, Target exercised to position 0, then back to 2.0 mm above position 4
|
The T2 target was exercised to position 0 around 6:15pm so that the T2 profile monitor could be used by operations. The T2 water package was re-enabled when the target was in position 0, however this resulted in some trips of the cooling package.
Operations called around 7:45 to request return of the target to about 2mm above position 4.
The target position was re-set so that the position reading fluctuated roughly between 2.7 and 1.6 mm above position 4 (hovering roughly around 2.0 mm), and so the potentiometer reading was hovering roughly between 0.801 and 0.798.
The cooling package was re-started, and called operations to confirm the system was OK. |
Tuesday, April 28, 2015, 15:55, Isaac Earle, Development, Target 1, Target, Target Version Jumper Wires Installed for T1-MK1 and T2-MK1
|
The T1-MK1 and T2-MK1 targets have been re-wired to allow version identification. Work was performed in the target storage pit. Approximate field around the targets in the pit was 100microSv/hr. Disposable coveralls were worn for the job and had 800cpm of contamination on completion. All nylon cable ties on the targets were replaced with PEEK cable ties. Total dose received was 0.06mSv by Isaac Earle. This modification has now been completed for all T1 and T2 target assemblies. |
Monday, April 11, 2016, 13:51, Isaac Earle, Development, Other, Other, Target Transfer Flask Hoist Hook Lower Limit Adjusted
|
The lower limit of the flask hoist hook has been adjusted. The travelling nut for the lower limit was rotated 3 notches closer to the upper limit travelling nut which resulted in an additional 1-3/8" travel of the hook at the lower limit. The door hinges and door cable pulleys were lubricated with WD-40 and actuation of the doors was tested several times. |
Friday, September 23, 2022, 10:51, Matthew Gareau, Standard Operation, Target 2, Target, Target T2-MK2 moved to storage pit
|
The T2-MK2 target was transported from the east hot cell to the storage pit at position 3.
As was noted in the past, position 3 is difficult to align. The flask alignment pins prevent the flask from positioning in the correct location, and it is required to have the flask just above the pins to ensure that the pins did not restrict the flask movement.
It is recommended to install a camera system to assist with the target placement and retrieval, which will help reduce the amount of dose one receives during this operation.
|
Wednesday, September 30, 2015, 17:07, Isaac Earle, Standard Operation, Target 2, Target, Target Moves for Profile Check - Possible Motor or Control Box Failure
|
The T1 and T2 targets were moved to position zero, then back to the target position today so that beam profile could be checked using the profile monitors. Movement for both targets was done with the portable control box.
The T1 target was moved from Position 4 to Position 0, then back to Position 4 (after checking the profile) with no issues.
While moving the T2 target from Position 4 to Position 0 the ladder stopped moving part way through travel. By toggling the control box "RUN / OFF" switch the motion could be restarted. This had to be done 2 or 3 times to reach Position 0. When returning to Position 4 after checking the profile the problem became more severe. It took over 20 minutes to move from Position 0 to 4 because the ladder only moved slightly or not at all each time the switch was toggled. This is either due to a failed motor on the target, or failure of the portable control box.
The next step will be to try moving the ladder of one of the target assemblies in the storage pit to determine which is at fault. In the mean time neither the T1 nor T2 target ladder should be moved. |
Monday, January 14, 2013, 16:55, Isaac Earle, Standard Operation, Target 2, Target, Target Move & Damaged Profile Monitor
|
The T2-MK1 target (spare T2 target) was transported from the hot cell to the storage pit today.
While the flask was being aligned to the storage pit locating pins, the base of the flask bumped the top of one of the alignment pins. This was caused by a slight misalignment between the flask locating hole and the alignment pin at the moment when the flask was lowered. This caused the target to swing within the flask and hit the inside wall of the flask.
While the target was being lowered into the storage pit hole, it was observed that the profile monitor cassette had become loose from the impact and was protruding from its frame. The target was raised back into the flask and transported back to the hot cell for inspection.
While lowering the target into the hot cell, the profile monitor cassette was protruding so much from its frame that it hit the target support ring on the hot cell turn table. This caused the profile monitor cassette to come completely out of its frame and fall onto the hot cell table. The cassette was damaged from the fall and appears to be unusable. Probes Group is in the process of assembling a new cassette, which should be ready within the next few days. They have requested that the damaged cassette be given to them so they can salvage parts (the cassette has not seen beam and should not be active).
The target was inspected and photographed and then transported to storage pit hole #4. It is possible that the profile monitor frame was also damaged.
This mistake can be avoided in the future by working much more carefully and slowly when locating the flask on alignment pins and by completely removing all flask swing before lowering the flask. |
Monday, July 23, 2012, 16:01, Isaac Earle, Development, Target 1, Target, Target Flask Seismic Restraint Clamps Installed  
|
Installation of the seismic restraint clamps has been completed for the MK1 and MK2 target flasks in the Remote Handling lab (photos attached). Two clamps on the MK1 flask required 3/8" shims due to warpage of the flask baseplate (see photo IMG_0429).
Dragan Mitrovic has been notified so that he can inspect the installation and close the work request. |
Wednesday, February 24, 2016, 13:03, Isaac Earle, Repair, Other, Other, Target Flask 2-Ton Hoist Chain Twist Corrected
|
A 1/2 turn twist in the target flask hoist chain has been corrected to address a deficiency observed by inspectors by Gordon Crane. This was accomplished by first holding the flask door yoke at the top position using rope slings, then lowering the hook block spider approximately 6", then lifting the stationary end of the hoist chain approximately 2" using the Meson Hall main crane to make the top of the chain slack.
A missing cotter pin for the counterweight on the RH HC Lab overhead crane was also installed. |
Thursday, March 24, 2016, 14:46, Isaac Earle, Other, Other, Other, TNF / 500MeV Resin Cans Removed from Storage Pit #1
|
Three used TNF / 500MeV system cooling system resin cans were removed from the Meson Hall target storage pit (two from Hole #1, one which was stored below block #1).
Two new active cans will be returned to Hole #1 after the TNF resin is changed in a few weeks time. |
Thursday, April 09, 2015, 13:56, Isaac Earle, Development, Target 2, Target, T2-MK2 target wired for version identification, cable ties replaced, ready for use
|
The "POT/CAM" MS connector on the T2-MK2 has been wired to allow automatic target version number identification by the new T1/T2 control system. Pin A was jumpered to Pin C. (MK1 targets will use Pin A to Pin B jumper).
The nylon cable ties on the target assembly were found to be very brittle and fragile, they have been replaced with PEEK cable ties.
The T2-MK2 target is now ready to be moved to the beamline. |
Tuesday, February 05, 2013, 09:50, Isaac Earle, Maintenance, Target 2, Target, T2-MK2 target moved from beam line to hot cell
|
The T2-MK2 target was transported from the beam line to the RH hot cell. The profile monitor was secured in the 'in' position before lifting the target, as it is better protected in this configuration. This procedure will be used for all future target moves to reduce the risk of damage to the monitor.
The field on the target while lifting was approximately 5mSv/hr at 2m. A field of 12mSv/hr was measured directly above the T2 target hole on the monolith. A shield plug was installed into the hole which reduced the field to 500µSv/hr.
A section of the "montior" cable was found to have damaged insulation (photo attached). Fortunately this cable terminates at the cooling package, so only a short section needs to be replaced.
|
Thursday, September 15, 2022, 14:34, Adam Newsome, Standard Operation, Target 2, Target, T2-MK2 target elevations measurement
|
The target elevations measurement and beam spot checks were completed on Sept. 15, 2022. This was done after a July 2022 target exchange for target positions 3 and 5.
Updated target elevation drawing can be found in DocuShare (Collection-33652) |
Tuesday, April 11, 2017, 17:31, Isaac Earle, Development, Target 2, Target, T2-MK2 target MRO and alignment of T2 devices
|
The following work was performed on the T2-MK2 target assembly and the T2 Protect assembly for maintenance purposes and to implement the alignment strategy detailed in E-Log #218:
March 30 (T2-MK2 target in hot cell):
- Profile monitor actuation checked: moved in and out smoothly, fully in at ~25psi
- Ran through all target positions, motion smooth, micro-switches all ok, potentiometer value unsteady when moving between position 0-1, steady when stopped, no issues form positions 2-5 (this was also observed last shutdown and there were no issues with ladder moves in the 2016 running period using EPICS)
- Water system pumped out with cold trap for 2 hours (previously was purged with clean water, then air overnight)
- Leak check performed: 10 minutes to reach 5.0E-3 Torr TP pressure, 25 minutes to reach 1.0E-3 Torr; 3psi helium supply applied in 0.5s bursts; No response at all target locations and all four aluminum delta seal locations. At base of bellows on left side (when facing ladder) quick response up to 0.6E-8atm.cc/s, quick recovery to baseline (<10s); At base of bellows on right side (when facing ladder) quick response up to 1.2E-8atm.cc/s, quick recovery to baseline (<10s). These small helium leaks were known (see E-Log #95) and have not caused issue in multiple years of running.
April 5:
- Position 1 and 2 potentiometer ratio changed to achieve new target alignment, look-up tables updated in PLC code (see E-Log #218, and attached new elevation measurements)
- Position 1 and 2 micro-switches adjusted to be centered at new positions
- Profile monitor inspected: no broken wires, but some not quite straight or parallel with others, also some wire insulation blackened. Scott Kellogg recommended installing new profile cassette
- Old profile cassette removed in hot cell and new one installed
- Profile monitor elevation adjusted (see attached new elevation measurements)
April 6:
- Electrical check on profile monitor performed at HC by Dave Cameron: deemed OK
- T2-MK2 moved from the hot cell to the beam line (~200mSv/hr at 0.5m)
- T2 protect monitor moved from beam line to hot cell (~16mSv/hr at 0.5m)
April 7:
- Elevation of protect monitor measured to confirm old measurement: within 0.1mm
- Old protect monitor cassette removed
- New cassette supplied pre-adjusted by Scott Kellogg
- New cassette installed in HC, elevation measured on entrance side: 1832.8mm (intended elevation was 1833.2mm, from E-Log #218)
- Protect monitor electronics checked by Shengli Liu and Dave Cameron at the hot cell: all OK
April 10:
- T2 profile monitor cable plugged in which caused unexpected jump in vacuum: 20mTorr - 180mTorr
- Large nut at top of feed-through connector tightened and vacuum returned to baseline
- T2 target position 1 and 2 potentiometer values tested from EPICS system to confirm PLC look-up table changes ok
April 11:
- T2 Protect assembly returned to beamline (12mSv/hr at 0.5m). T2 monolith position was monitored by Beamlines Group with their laser tracker during the move. A maximum of 0.2mm movement was measured which is attributable to noise.
- Air amplifier started, leak found from one of the M20BB cylinders; went away after reset of BB control system, BB exercised several times and leak could not be reproduced (no change to BL vacuum)
- T2 profile monitor tuned for slower actuation, smooth movement confirmed and no change to beamline vacuum (also done for T1 profile monitor)
- Electrical check on T2 protect monitor performed by Dave Cameron and Shengli Liu from racks on mezannine: all OK
- Electrical check on T2 profile monitor performed by Dave Cameron and Shengli Liu from racks on mezannine: initially very low signal, they discovered a previously unknown large resistor which was bypassed for the test: approximately 1/2 of signals show response to HV blip, deemed OK to restore shielding
- Target info sheet and updated elevations measurements delivered to Operations (elevations sheet attached)
Note: the T1 target (T1-MK2) was not removed from the beamline this shutdown, so new elevation measurements have not been submitted and T1 profile and protect monitor checks have not been performed |
Friday, April 06, 2018, 15:05, Isaac Earle, Standard Operation, Target 2, Target, T2-MK2 target MRO
|
The following is a summary of MRO work done on the T2-MK2 target during the 2018 shutdown:
Jan 8:
- Target moved from beamline to hot cell; 130mSv/hr at 0.5m
Jan 10:
- Position 4 (12mm Be) beam spots photographed. Spot is slightly high and left (from beam's eye view), also smaller and rounder (less eliptical) than usual - See E-Log #232
Jan 11:
- Flushed position 0,1,2,3,4 with water, then 4,2,1,0 with air
- Left with 10psi air running overnight in Position 0
Jan 12:
- Moved to position 4, 10psi air running through over the weekend to dry cooling lines
Jan 15:
- Pumped out water lines with leak detector
- Frist pump down blanked off tubing and new vac hose (no LN2): ~15 mins to get to 0.0E-10 TorrL/s
- Pumped out target w/ cold trap: ~7 mins to get to 0.0E-10 TorrL/s (left pumping for 2 hours)
April 2:
- Removed plugs at position 3 and 5
- Pressure tested, leak tested, and recorded alignment dimensions for first batch of new 5cm targets (#301, 307, and 309) - Records stored with targets in RH lab office
- Installed new 5cm beryllium target #309 at Position 3, and target #307 at Position 5
- Helium leak check on target water system: Baseline 0.0E-10 TorrL/s leak rate, 1.0E-3Torr, half second helium applications @ 4psi
Positions 1, 2, 3: no response
Positions 4, 5: up to 5.0E-10 after delay (appears to be drift)
Lower 'C' seals: no response
Upper-left 'C' seal: up to 1.2E-9
Upper-right 'C' seal: up to 2.4E-9
Left bellows: up to 6.0E-9
Right bellows: up to 3.0E-9
- Deemed water leak tight and ready for use (based on previous leak check results and operating experience)
- Tested all target position micro switches: all OK
- Tested profile monitor limits: both OK
- Tested profile monitor actuation: off down limit @ 5psi, on up limit at 35psi
- Tested potentiometer: slightly noisy signal from position 0 to 2 (no change from before)
- Measured Position 3 and 5 elevations
April 3:
- Measured Position 3 and 5 horizontal alignment wrt ladder
- Quick repeat of leak check: no change
April 6:
- Target returned to beamline
- Vacuum pulled on T2 area (1ACG4 down to 5mTorr in ~2.5hrs, was 4mTorr before venting yesterday)
- T2 cooling package started with target at Position 0 - no change to T2 vacuum
- Target information sheet and elevations data delivered to Ops
- XTPAGE 7L information updated
|
Tuesday, October 10, 2017, 12:09, Isaac Earle, Standard Operation, Target 2, Target, T2-MK2 position 4 target changed  
|
The following work was performed on the T2-MK2 target assembly during the 2017 fall shutdown:
Oct 4, 2017:
- Target moved from beamline to hot cell, measured 661mSv/hr at 0.5m (move went smoothly, having camera views at N/S and E/W angles very helpful)
- Flask tray wet wiped after transfer: 1st wipe 600cpm on 44-2 monitor, 2nd wipe 900cpm (3rd swipe not taken because tray looked clean)
- Flushed target with clean water, then compressed air (positions 0 through 5)
- Male Hansen fittings on the target assembly swapped with new units (in process of replacing all self sealing fittings in T1 and T2 water system)
- Checked all micro-switch positions and potentiometer readback: switches ok, pot value jumpy around position 1 and 2 (known from before), otherwise fine
- Left target overnight at position 4 with 20psi supply air running through to dry water system
Oct 5, 2017:
- Pumped down target with cold trap (~2 hours)
- Baseline leak check performed: 6 mins to reach 5.0E-3 Torr (3.2E-9 Torr*L/s), 21 mins to reach 1.0E-3 Torr (1.4E-10 Torr*L/s)
- Helium spray at 3psi for 0.5s bursts, tested with ladder in position 4
- No leak at any target positions or plugs
- Small leak on left side bellows, or bellows seal to ladder: up to 8.0E-9 Torr*L/s response, then quick recovery (known from previous leak checks, same magnitude)
- Small leak on right side bellows, or bellows seal to ladder: up to 2.0E-8 Torr*L/s response, then quick recovery (known from previous leak checks, same magnitude)
- Beam spot photos taken, position 1 (only target used this running period) has fairly well centered beam spot (see below)
- Position 4 target removed ("JAN29'97"), was very difficult to remove because one water tube stuck in ladder (this target was installed on ladder in 1997! First beam 2014)
- Used hammer in hot cell to remove which eventually broke the target water tubes from the wire EDM housing
- sealing surfaces cleaned with burgandy Scotchbrite on electric dremel tool
- Inspected sealing surfaces and ladder fitting threads using Nikon level: all appeared clean and undamaged
- Installed new 12mm beryllium target at position 4 ("Jul.06#4"), no issues with install
- Leak check repeated: reached 1.0E-3 Torr after 3 minutes (1.3E-8Torr*L/s)
- Down to 3.5E-9 Torr*L/s after 18 mins, began test
- No response at all target positions, checked left side bellows: same response as above
- Beam spot profile at Position 1 measured with Nikon level
- Vertical and horizontal positions of new Position 4 target measured
- New profile monitor cassette retainer pin installed (plate hole had to be opened up to 0.375" diameter), used vice grip pliers clamped onto clevis pin in order to install
Oct 6, 2017:
- Profile monitor actuation tested: start movement 5psi, fully IN at 35psi
- Profile monitor limit switches tested, ok
- Target transported back to beamline, no issues
- BL1A pumped down, Edi reported pump-down normal
- Electrical check performed on T2 profile monitor from mezzannine: Sheng-Li reported results normal
- Cooling system started: no change to BL1A vacuum
- Target info sheet and target elevations sheet delivered to Main Ops
- XTPAGE 7L information updated
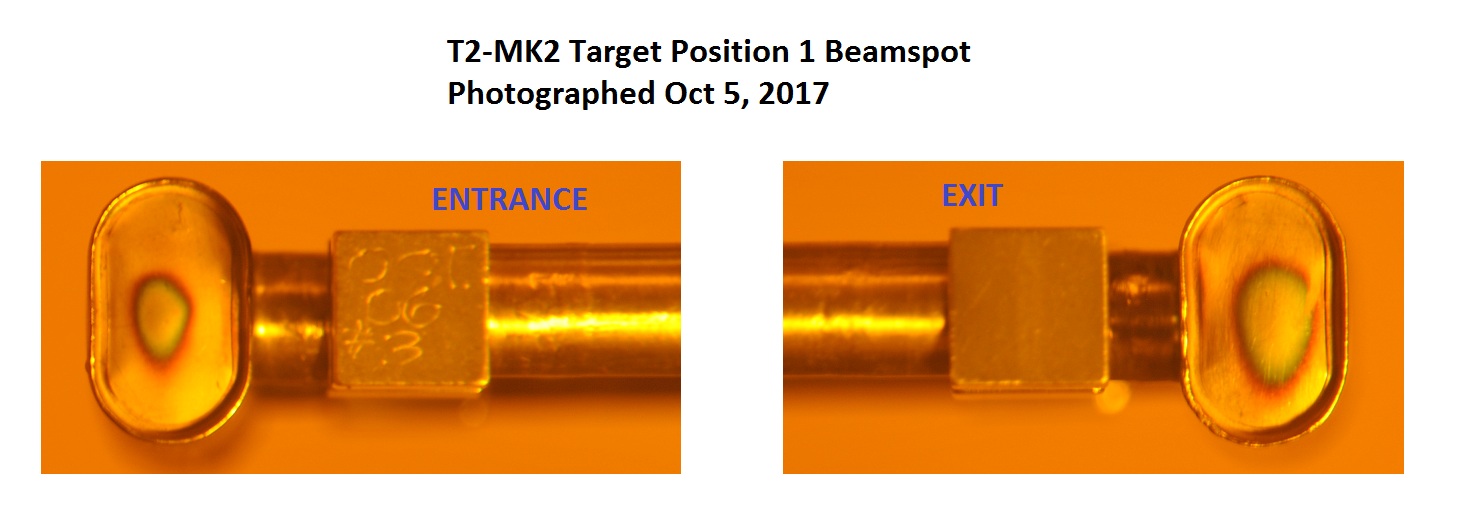
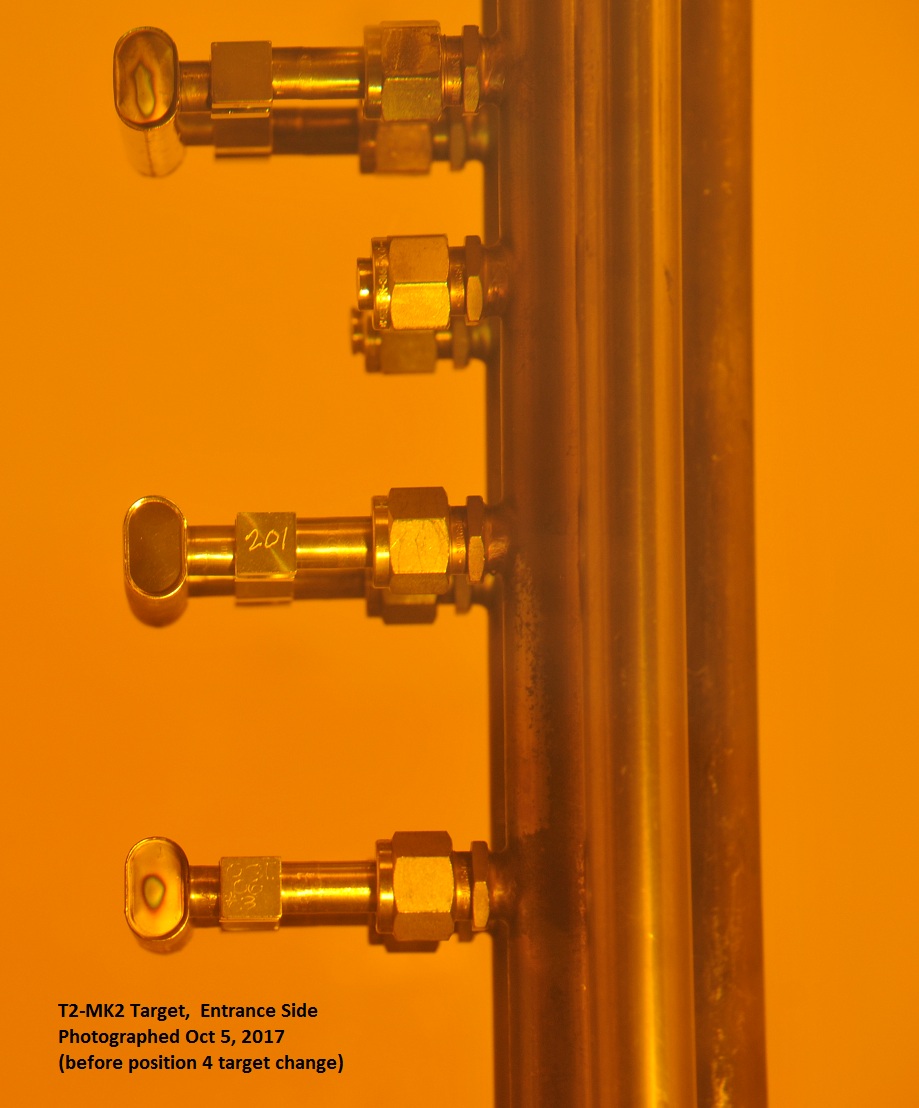
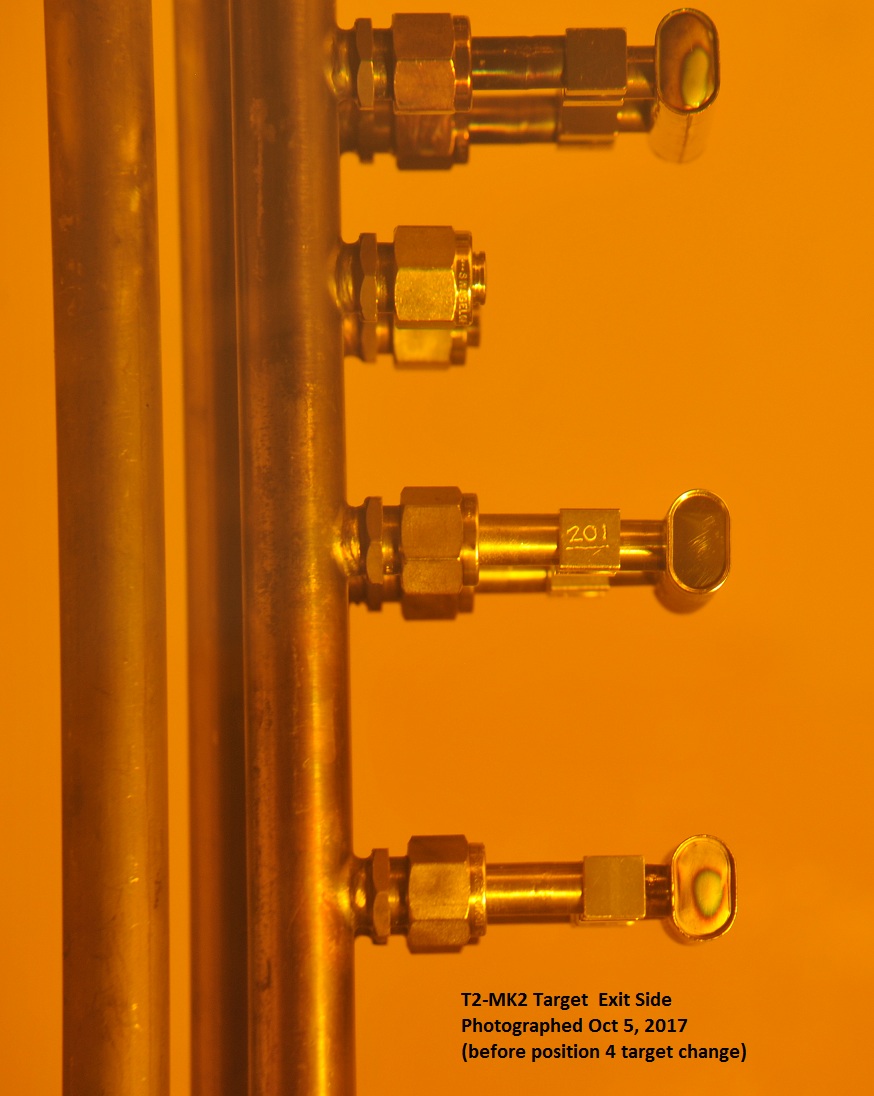
|
Wednesday, April 13, 2022, 12:31, Adam Newsome, Standard Operation, Target 2, Target, T2-MK2 moved: from target station to storage
|
The T2-MK2 target was moved from the target station to the storage area (position 3). Upon removal, it was measured with a pole monitor at 0.5 m to be 960 mSv/h. |
Wednesday, May 25, 2022, 10:16, Adam Newsome, Standard Operation, Target 2, Target, T2-MK2 moved: from storage location to hot cell
|
Target T2-MK2 was moved from the storage location (formerly position 3) to the hot cell in preparation for replacement of end of life targets. |
Wednesday, January 10, 2018, 17:45, Isaac Earle, Standard Operation, Target 2, Target, T2-MK2 beam spot photos, M20BB moved to storage pit 
|
The T2-MK2 target was moved from the beamline to the hot cell on January 8th. The field at 0.5m was 130mSv/hr. Photographs of the beam spot of the Position 4 target are attached below. This is a 12mm beryllium target (ID: "JUL.06#4). This is the only target on the T2 ladder that has seen beam since it was installed on October 10, 2017. A shielding plug was installed on the T2 flange. A new 5cm target will be installed on the T2-MK2 ladder after fabrication is complete. Regular testing and maintenance of the target assembly will also be performed before it is returned to the beamline.
The M20 beam blocker was also moved from the beamline to Hole #7 in the storage pit. The field at 0.5m was 22mSv/hr. A blank-off plate was installed on the M20BB flange (no o-ring). Seal replacement and general inspection/testing will be performed before it is returned to the beamline.
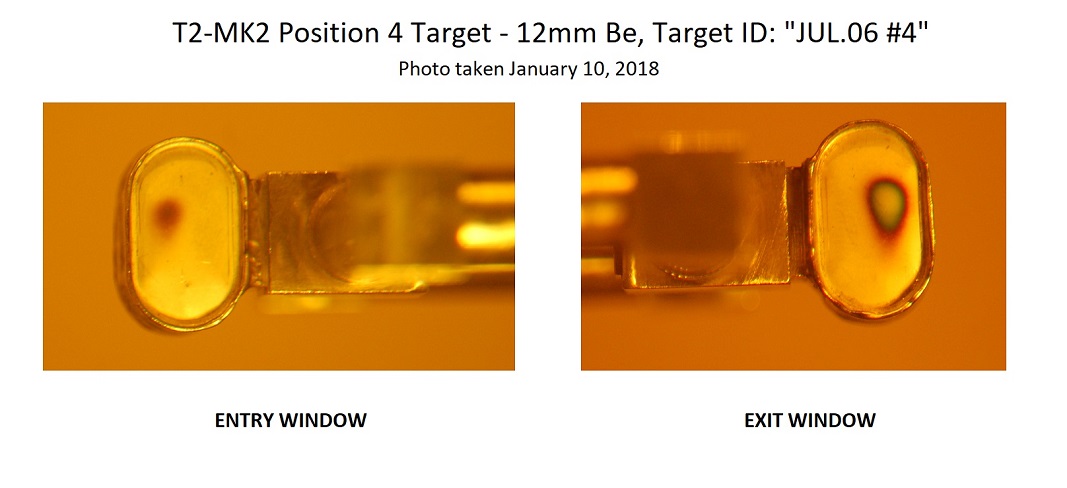
|
Friday, May 05, 2017, 15:09, Isaac Earle, Development, Target 2, Target, T2-MK2 beam spot check in hot cell   
|
On May 5th the T2-MK2 target was moved to the hot cell for the purpose of checking the beam spot on the Position 2 beryllium target to confirm the results of the T2 area realignment detailed in E-logs #218 and #220. In preparation beam was put on this target overnight for approximately 1.5hrs at 10uA and 4 hours at 50uA (previously had not seen beam). Also, there had been issues with the T2 profile monitor over the last couple days, so inspection and repeat of electrical check in the hot cell was planned. The field in the T2 monolith work area was up to 1.3mSv/hr, and a maximum field of 230mSv/hr was measured 0.5m from the target during removal.
Unfortunately no beam spot was visible on either the entrance or exit windows at Position 2 (a longer exposure will be required next time a beam spot is to be inspected). Detailed photos were taken, one of each side attached. It was noticed that the T2 profile monitor cassette had become dislodged within its housing (it was sitting approximately 1" from the fully installed position - photo attached). It is suspected that this happened when the target assembly was in the beamline - the first time the profile monitor was exercised back in April it moved quite quickly which may have caused the cassette to come loose (it is only held in with friction of the 9-pin connectors and the fit of the cassette body in the housing). It was re-inserted in the hot cell and an electrical check was performed by Shengli: all good. After the target was returned to the beam line the electrical check was repeated while the monitor was actuated in and out: once again all good, and the movement of the monitor was slow and smooth (video taken)
Prior to this job new cameras were installed in the hot cell opening aimed at the support ring hole (one aimed north, the other east). This proved to be a very useful upgrade and made the installation process significantly easier and smoother. Two cameras were also used during target installation at the monolith (only 1 was used in the past). Having a second camera at a different angle made alignment easier (reducing time and dose), and should be adopted for future target moves.
Vacuum pumpdown was normal, the cooling system was restarted without change to the vacuum, and operators were able to use the T2 profile monitor during beam ramp-up overnight.
Dose for this job: Isaac 0.17mSv, Keith 0.06, Ron 0.06
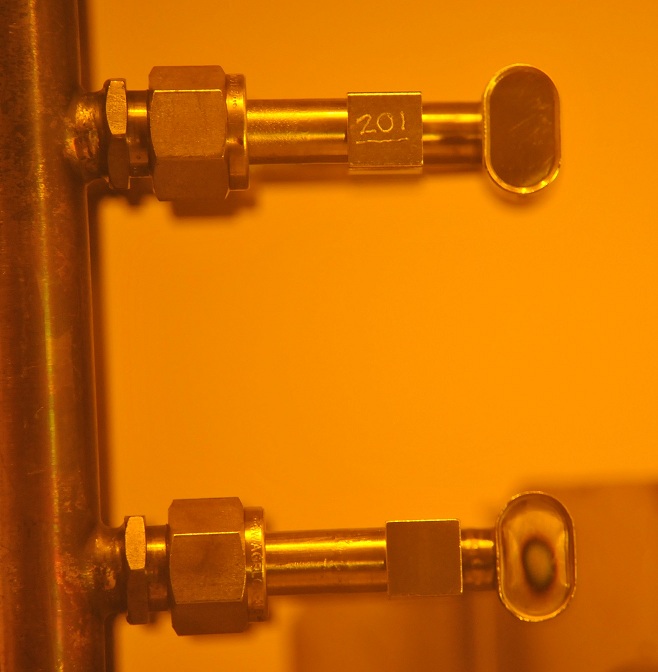
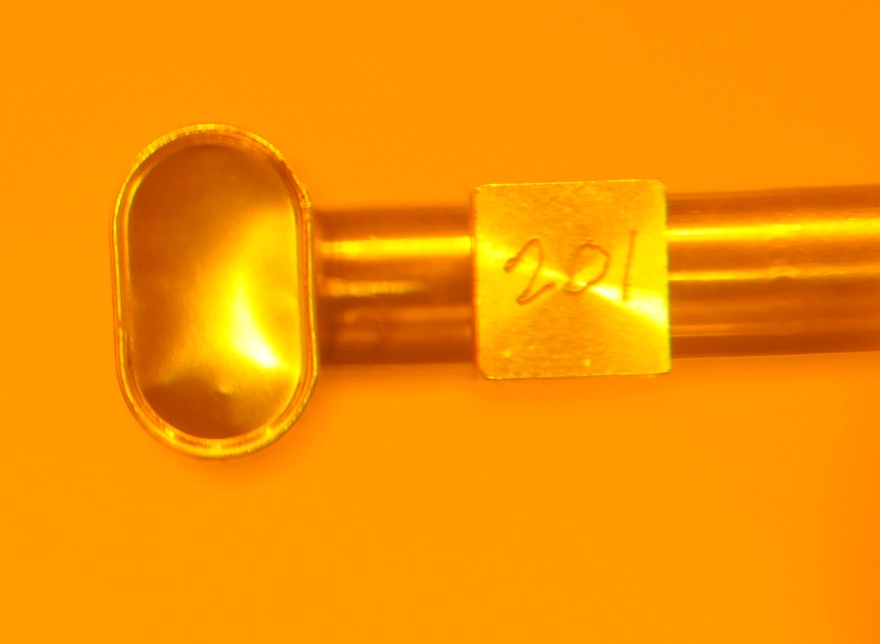
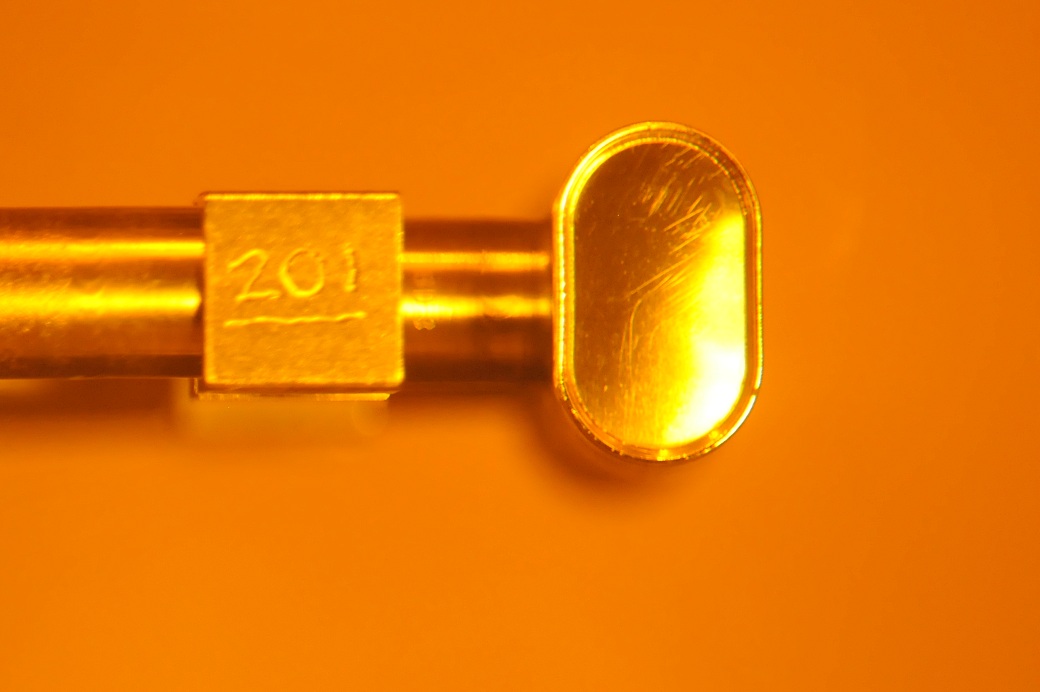
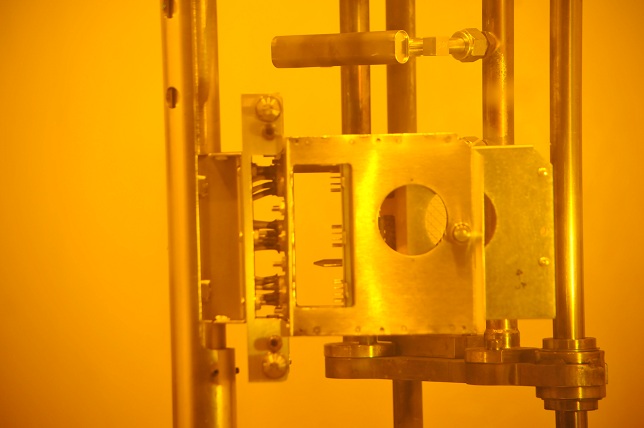
|
|