ID |
Date |
Author |
Category |
Type |
Module |
Target/Number |
Subject |
1503
|
Tuesday, April 25, 2017, 19:35 |
Grant Minor | Crane | Repair | | | ISAC Target Hall Crane - West Hoist Brake Rattle |
Below is a report on the ISAC Target Hall crane brake issue observed yesterday and addressed today:
- On April 13th, both the East and West hoist brake assemblies were replaced by Gordon Crane & Hoist, after David observed a burning smell
- The East assembly was replaced with a completely new brake assembly from Kone crane
- The West assembly was replaced with a refurbished assembly, which used the East assembly housing fitted with a rebuild kit by Gordon Crane
- Yesterday while preparing TM3 for a lift, David noticed a vibration / rattle sound coming from the West hoist brake
- This issue was only observed when starting the hoist from a complete stop, at the slowest possible upwards hoist speed
- Once the hoist speed increased, the sound went away, even after returning to a slower speed
- Tom from Gordon Crane & Hoist came in this morning at 7am and replaced the new West assembly with the original West assembly, which had at that point also been fitted with a rebuild kit at Gordon Crane’s shop
- Tom also inspected the East brake assembly again
- Tom commented that he had issues setting the right gap between the friction plates and the brake rotor – too close and the brake would not release properly, too far and the brake rattle issue would be observed
- He also commented that during this most recent repair of the West brake, he applied never seize to the shaft and spline to ensure that this friction point was not an issue
- After Tom finished his repair and inspection of the brakes, David attempted a test lift of an SEG block (10 ton) at the slowest lift speed
- The rattle noise coming from the West brake was still observed
- Travis also tested the slowest speed in Remote Test mode from the control room, with David and Grant present in the Target Hall, the rattle was also still observed
- Tom advised that the rattle would not affect the safety of the hoist, and no damage would be done to the brake assemblies by running the hoist normally with the rattle noise
- Tom ensured that he would consult with Aiden and they would likely order a brand new West brake assembly from Kone
- Tom called Aiden Gordon to confirm that it was ok to proceed
- Aiden called me around 1:30pm and left a message that the slow speed rattle sound was benign and that we could proceed with normal operations, but he would definitely address the problem moving forward, and we should standby for his report
Photos and video have been uploaded to Docushare. The hoist noise before the repair and after the repair during the test lifts can be heard in the videos.
https://documents.triumf.ca/docushare/dsweb/View/Collection-19812
Thanks and regards,
Grant
--
Grant Minor, M.A.Sc., P.Eng.
TRIUMF Remote Handling Group Leader
Nuclear Engineer
4004 Wesbrook Mall, Vancouver
BC, Canada, V6T2A3
gminor@triumf.ca
(604) 222-7359
http://www.triumf.ca/profiles/4557
|
1511
|
Thursday, April 27, 2017, 16:58 |
Isaac Earle | North Hot-Cell | Development | | | Right side NHC manipulator installed |
Installation of the NHC right side manipulator was completed yesterday. The three piece manipulator was assembled in the module assembly area on the manipulator cart which was then craned through the hatch to the NHC service area (the slave end had to be removed for it to fit through the hatch). The installation went relatively smoothly except for the second (cold side) piece of lead shielding around the thru tube which would not fit because the OD of the two halves were not concentric when assembled (arrived this way from CRL). The shielding was removed and 0.070" was cut down on the lathe, after which installation could be completed. The slave end lift bail and the pulley cover panel had to be removed for the manipulator to fit through the thru-tube. Both these items were reinstalled after the manipulator was in the wall, and it was confirmed that the slave end lift bail aligns with the slave-end removal hatch in the NHC roof. There was some difficulty getting the slave end to the horizontal position using the Y motion drive, also while preparing the manipulator for installation we noticed one of the Z motion tapes on the master side was sliding to the edge of one of the pulleys and rubbing - both these issues will be investigated at a later date.
We confirmed that it is possible to remove the master end using the manipulator cart. We will practice doing this at some point before the cell is commissioned. We will also do a run-through of slave end removal through the NHC roof.
Electronic copies of the Model-N installation and removal manual as well as the manipulator cart user manual are attached for future reference.
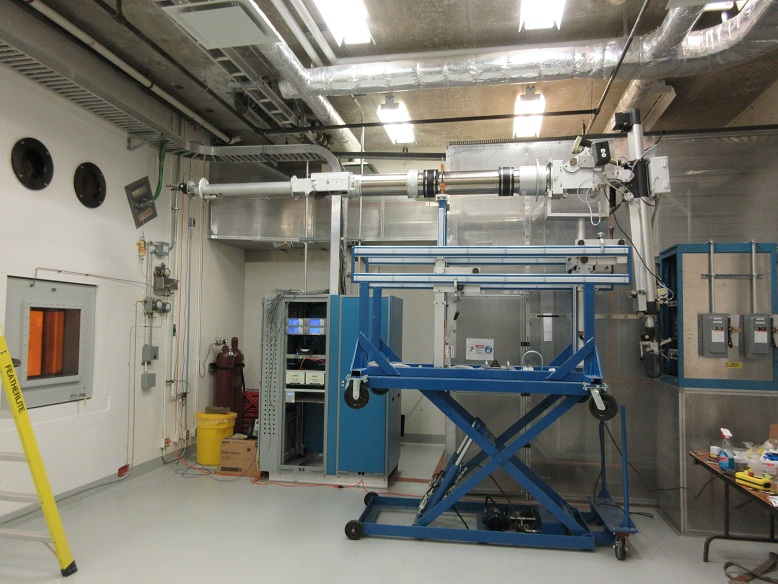
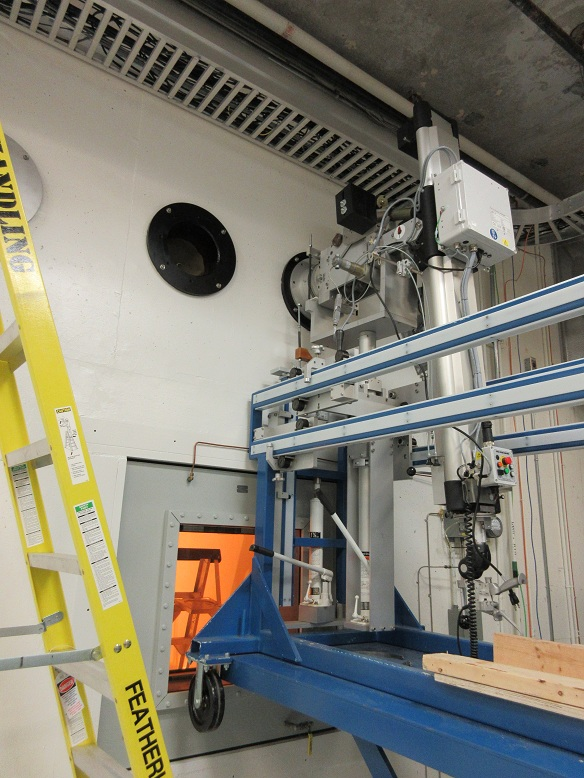
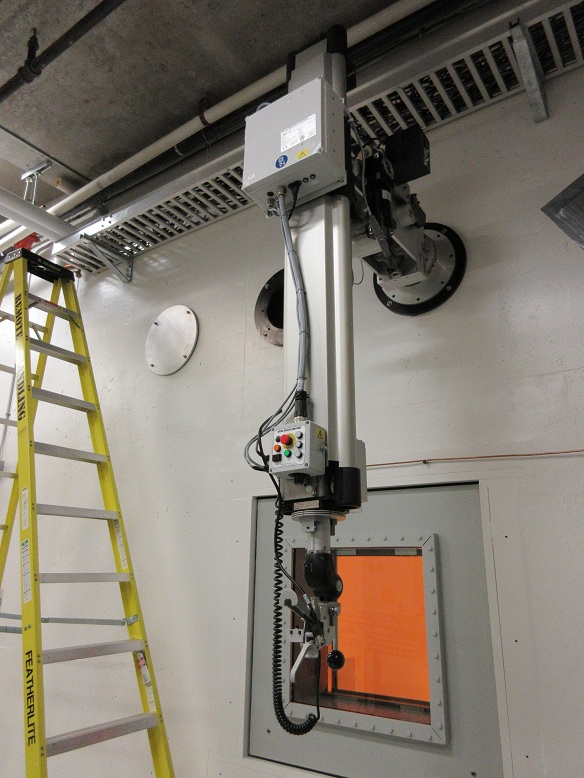
|
Attachment 4: CRLD-1046-B_rev_1_Installation_Removal_Manual_(July_2013).pdf
|
|
Attachment 5: Manipulator_Cart_User_Manual__(CRLD-1003).pdf
|
|
1513
|
Friday, April 28, 2017, 12:04 |
Anders Mjos | Conditioning Station | Maintenance | | | MP1 problem |
TCS:MP1 was tripping of intermittently yesterday. It was found by Dave Morris that the current sensor was not set correctly causing the pump on status to flicker at times. Dave adjusted the settings yesterday. The system should be operational and is currently running normally. |
1516
|
Monday, May 01, 2017, 12:32 |
David Wang | Crane | Repair | | | TH crane burning smell |
TH crane burning smell showed again this morning. It appeared after 1-1.5 hours of continuously using during the F308 flasks moving in TH.After a certain time of using I think the brake gap is reduced because of thermal expansion. The main hoist and brakes work fine still. We knew these brakes gap are tight especially on west side. So, It is not surprised that this burning smell appeared again. It does not affect the safe of crane use in my view. But, The life of this brake assembly could be affected. I would like everyone know this issue. We may need to consult Gordon crane as well. Maybe, The gap should be increased up a little bit. On this Friday, I will use crane to transfer 30K lbs shielding blocks. It will be a good test on crane main hoist again. |
1518
|
Tuesday, May 02, 2017, 09:48 |
Isaac Earle | North Hot-Cell | Development | | | NHC polycarbonate window cover panel installed |
The window cover panel has been installed on the hot side of the NHC shielding window according to drawing IRH1638. It was necessary to drill and tap a hole in the steel frame first to achieve proper grounding for stud welding. The strength of all studs were checked by installing a nut on the stud tightened against a block up against the steel frame, which was then torqued to a minimum of 10 ft*lbs. For the final installation the nuts were each torqued to approximately 3 ft*lbs. Visibility from the cold side of the cell was checked before and after installation by Chad Fisher and Isaac Earle: no distortion was caused by the new cover panel and with the in-cell work lights aimed in a similar direction to how the permanent lights will be installed (shining down from the roof, and also aimed south from the periphery of the window) there was no significant decrease in visibility of the work space. A couple of small scratches are visible on the panel surface - these were already there when the panel arrived at TRIUMF. The panel has been installed in an orientation that will minimize the visibility of these scratches during normal work. When the work lights were aimed at the window many imperfections in the panel were visible, however this is not expected to occur during normal operation. After the cell lighting has been installed the visibility will be re-evaluated and a new panel can be procured if necessary.
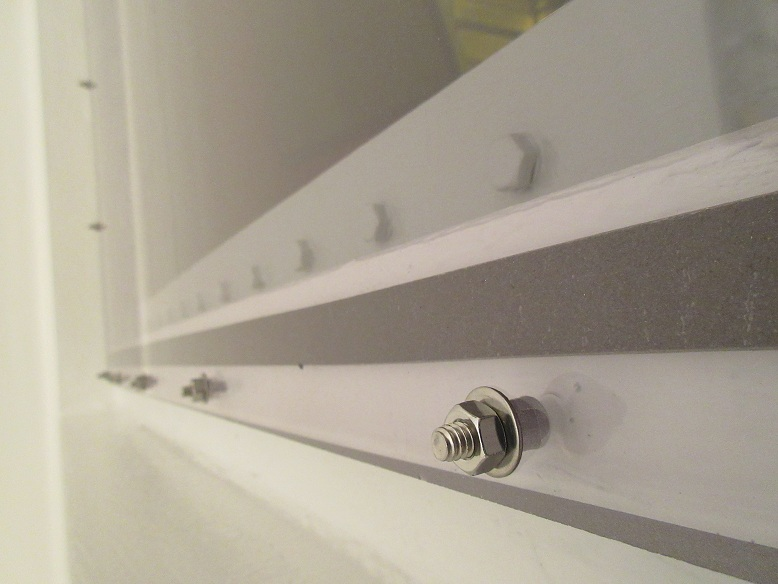
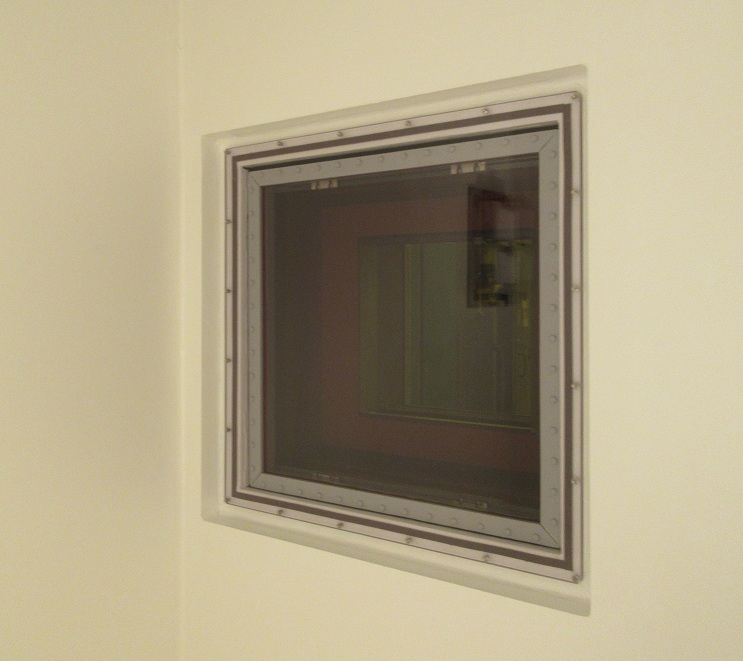
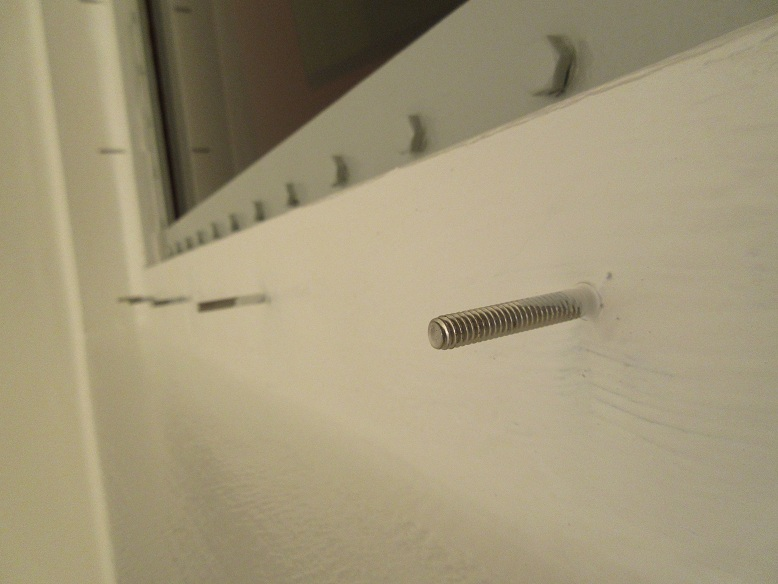
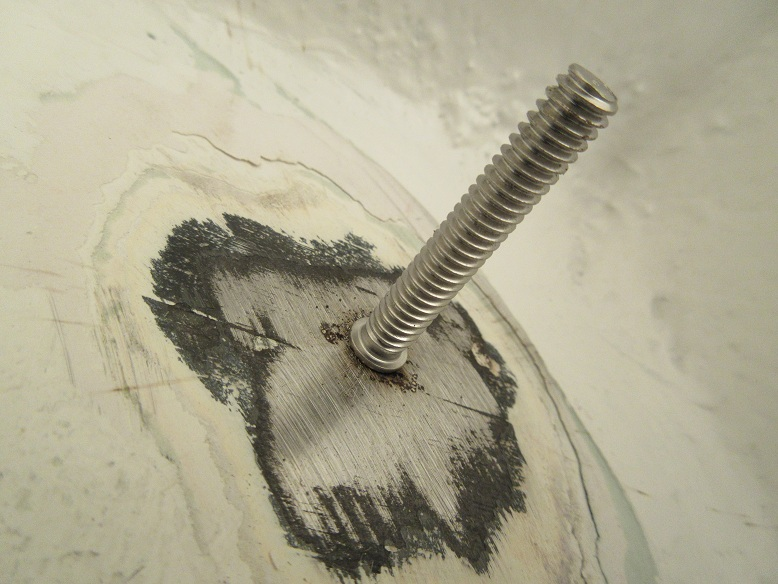
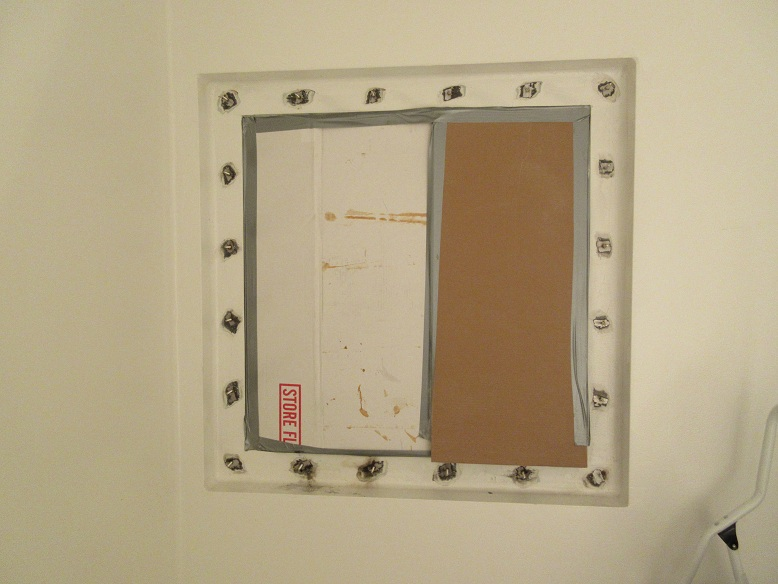
|
1519
|
Tuesday, May 02, 2017, 13:49 |
Travis Cave | Spent Target Vault | Standard Operation | | | Spent Targets moved |
Five spent targets have been moved from the target storage vault to the mini vault in preparation for Thursdays loading of the F-308s. See attached for the list of targets in the mini vault, and the new status of the storage vault. |
Attachment 1: Mini_Vault_Storage_May_2_2017.pdf
|
|
Attachment 2: Vault_Storage_May_2_2017.pdf
|
|
1527
|
Monday, May 08, 2017, 09:49 |
David Wang | Conditioning Station | Standard Operation | | | TH schedule 132 update weekly |
Update TH schedule weekly to show the job process. |
Attachment 1: Target_Hall_shedule_132_Apr_to_Sep.mpp
|
Attachment 2: Target_Hall_shedule_132_Apr_to_Sep.pdf
|
|
1528
|
Monday, May 08, 2017, 14:46 |
Travis Cave | Spent Target Vault | Maintenance | | | Mini Vault Door |
Mini Vault Door as some difficulty over coming a small hump on its track. To open the door one needs to give the door a slight tug while it is opening to over come this hump. |
1531
|
Wednesday, May 10, 2017, 13:42 |
Anders Mjos | Conditioning Station | Repair | | | Leaky gauge at TCS:TS2 (e-fault: 9609) |
Neil Wong will fix this leak tomorrow Friday. See attached schematics for location. |
Attachment 1: IRH1056_-_Leaky_Gauge.pdf
|
|
1532
|
Wednesday, May 10, 2017, 14:00 |
Anders Mjos | South Hot-Cell | Development | | ITE-Ta-LP-FEBIAD | Test target examination |
Chad and Anders inspected the test target in the hot cell today. The lid had been previously removed.
- The EE looked to have performed well.
- A piece of Ta foil was found inside the heat shield. It is not clear if this has been there during operation or if it entered the heat shield while in the hot cell. The foil has markings which indicate that it has seen heat.
- Travis measured 40 MOhm at 500V between heat shield and anode after the target was removed.
Photos are available on DocuShare |
1533
|
Thursday, May 11, 2017, 16:10 |
Isaac Earle | North Hot-Cell | Development | | | NHC roof block to TH north wall gap sealed |
The gap between the north face of the NHC roof block and the target hall north wall in the area where the NHC inlet ducting will be installed has been sealed with Sikaflex 1a flexible polyurethane sealant applied over foam backer-rod. |
1534
|
Friday, May 12, 2017, 07:42 |
David Wang | Crane | Repair | | | TH crane burning smell, smoke, and big noise on east side main hoist brake assembly. |
This morning, when I prepare for today's crane check, The crane made a very strong noise without any load during the full speed up motion. I stopped the crane right away, and noticed that east side of main hoist motor area was smoking . The crane was moved to east end. And, I climbed up to the top, and found the smoke is coming form brake side, and should be produced by braking. The smell is same as before.Unless other thing is wrong, I think Gordon crane technician has to adjust the gap to a proper distance on both side of the main hoist. I feel very uncomfortable by operating the crane this way. They have to figure out what is wrong on these new brake assembly installation.
2017-05-12. This morning , Crane technicians increased both side of main hoist brake gaps today. They found on east side brake assembly, The gap is automatically closed after some jogging motions. Peter think this is caused by torque produced by automatic adjustment springs on brake. This torque rotate the gap adjustment device and closed the gap. We operate the crane for a while with 20000lbs load on it after gap adjustment. The rattling sound is still there at slow up motion. But, The main hoist braking sound is softer and gentle comparing to past month.This sound is more close to the sound before we replaced the brake assembly. So, This adjustment could be right in my view. They checked gaps after 0.5 hours operation. Everything is still fixed there . No change. They suggest we keep operating the main hoist, and they will be back on next Monday check again. I operated the main hoist up and down in different speed motion for 1 hour after they left. Everything works fine. Braking are gentle. No strange sound and smoke during up or down. I will do more operation on Monday morning before they come. Lets see the result after their checking.
2017-05-15 This morning, 20minutes of crane main hoist up and down test with lots jogging and braking. The braking sound is softer and gentle. Everything works fine.
2017-05-15. Gordon crane technician Peter came in during lunch time. Both side main hoist brake gaps have been checked. They are still at the same position as last Friday. The gap is not changed after operation. Peter will be back on next Monday and check everything again. |
1542
|
Thursday, May 18, 2017, 10:41 |
Travis Cave | Spent Target Vault | Standard Operation | | UC#19 | Spent Target move |
The spent UC#19 target has been moved from the south hot cell into the spent target storage. It was placed in pail #145 and put in tray one spot C. See attached PDF for all vault details. |
Attachment 1: Vault_Storage_May_18_2017.pdf
|
|
1548
|
Tuesday, May 23, 2017, 14:10 |
David Wang | ITE | Standard Operation | | | ITE water interlock check is done. |
We do this check once a year now. Rene found a target oven reset issue during the check . He will consult with Friedhelm. The interlock check is good. |
1555
|
Friday, June 09, 2017, 11:21 |
chad fisher | North Hot-Cell | Maintenance | | | Model 'N' Slave Removal Through Roof |
Isaac and Chad disengaged the slave end of the manipulator and performed a slave removal through the slave removal roof hatch. This is part of investigation into a 'Z' motion tape that is "rubbing" on its drum on the master side of the manipulator during manual 'Z' retraction of 'Z' extension.
This also was the first test of the concept of removing the manipulator slave through the manipulator hatch that was built into the roof.
The lifting bail on the slave end of the manipulator was not centered to the hatch as per design but this did not compromise the procedure at all and the procedure otherwise followed the design intent.
Pictures can be located on Docushare http://documants.triumf.ca/docushare/dsweb/View/Collection-20157
|
1556
|
Monday, June 12, 2017, 13:51 |
Travis Cave | Spent Target Vault | Standard Operation | | | Spent Target move |
The spent Ta#51 target has been moved from the south hot cell to the spent target vault. It was placed in pail#149 and put in spot 8B of the vault. |
Attachment 1: Vault_Storage_June_12_2017.pdf
|
|
1558
|
Tuesday, June 13, 2017, 11:10 |
Grant Minor | Crane | Maintenance | | | ISAC THall Crane 100% / 125% Load Test Documentation - 2011 |
The ISAC Target Hall Crane was load tested and re-certified in January 2011 prior to doing a near-capacity lift for the North Hot Cell roof structure (IRH1112E).
Photos and documentation from Norelco is attached.
- Grant |
Attachment 1: ISAC_TH_Crane_Load_Test_Norelco_Sept_30_2011.pdf
|
|
Attachment 2: IMG_8722.JPG
|
|
Attachment 3: IMG_8752.JPG
|
|
Attachment 4: IMG_8735.JPG
|
|
Attachment 5: IMG_8745.JPG
|
|
1560
|
Thursday, June 15, 2017, 11:29 |
Isaac Earle | North Hot-Cell | Development | | | NHC inlet ducting installed |
The North Hot Cell inlet ducting assembly was installed today in the target hall at the north end of the NHC roof block. A small section of the perforated aluminum sheet on the TCS cage had to be trimmed for the assembly to fit (see IMG_0214). At each end of the assembly it was fastened to the roof structure using a 1/4"-20 tapped hole in the steel roof, and a 1/4"-20 anchor in the north wall of the target hall. The base flange of the assembly was sealed to the roof structure and TH wall using Sikaflex 1A polyurethane sealant on all sides.
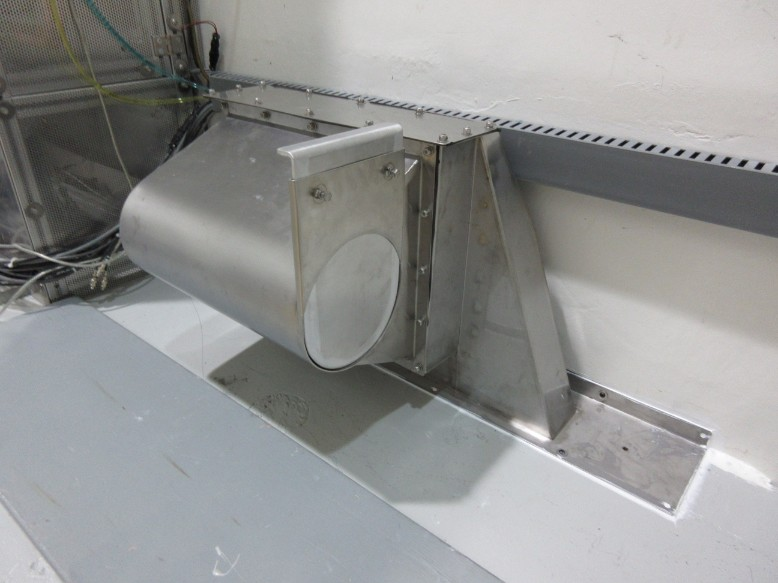
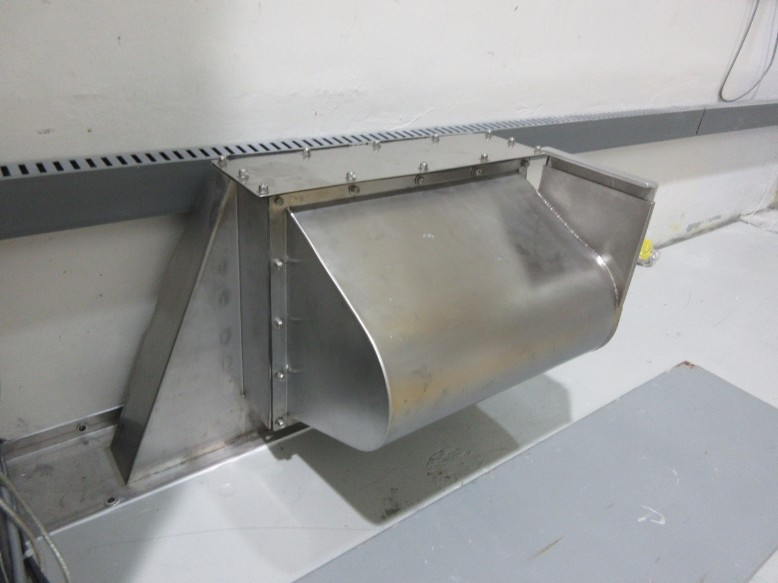
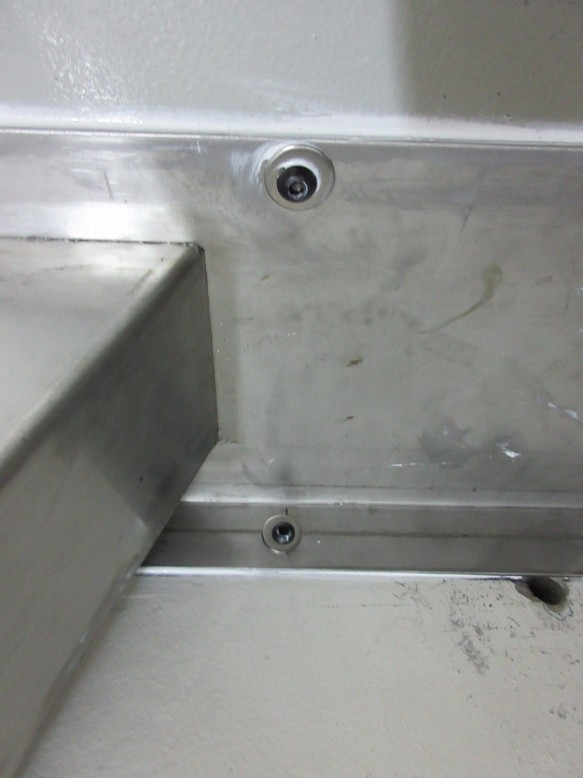
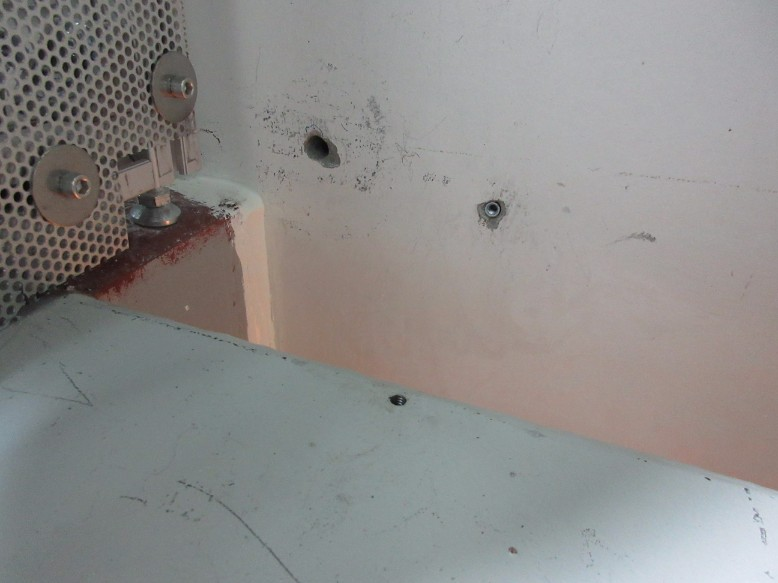
|
1562
|
Thursday, June 22, 2017, 11:10 |
chad fisher | South Hot-Cell | Maintenance | | | In cell airline |
The in cell airline has preemptively been replaced. The hose was, as far as I know the original. |
1563
|
Friday, June 23, 2017, 12:08 |
David Wang | Crane | Repair | | | TH crane inspection and probem fixing by Gordon crane |
Gordon crane technician Peter came in today and checked TH crane. Maico and I were there with him. What he found is that brake gap on both side of main hoist decreased after months of using. The solution is to lock the automatic self adjustment system so the gap will be fixed there. Each year during annual inspection, they will adjust the gap manually. After he locked both side of device, I tested the crane up and down couple of times. The brakes work fine. |