Monday, April 15, 2013, 11:00, chad fisher, South Hot-Cell, Standard Operation, TM3, , Items for TM3 dummy target installation
|
New gaskets and fasteners have been inserted into the south hot cell in preparation for installing the dummy target onto TM3 tomorrow. |
Friday, March 27, 2020, 08:45, Matthew Gareau, North Hot-Cell, Maintenance, , , Issues with the manipulators
|
This is a link to all of the issues with the NHC manipulators that I know of
https://documents.triumf.ca/docushare/dsweb/View/Collection-27663/Document-180176
|
Wednesday, May 24, 2023, 17:25, Carla Babcock, ITE, Repair, TM4, TiC#5, Issues with anode short
|
When I tried to raise the anode voltage in cathode bias mode on May 23 evening, I found the target or tube shorted to HV common. Investigations in the faraday cage today showed the same. I removed all the new electronics (resistors, gemovs, etc) from the power supply to no effect, so I disconnected the TGHT supply and pushed it away from the busbars. There was still a short. David Frank and I then went down to the pit and disconnected everything to measure the module. The module itself showed no short, and the bus bars in the chase for TGHT showed no short, though the ones for TBHT still showed the short.
David and Frank reconnected the module and I disconnected the TBHT supply in the faraday cage, then I found no shorts to TGHT/TBHT. When I reconnected everything there were still no shorts. There must have been a short in the TBHT line in the faraday cage, and another short in the TGHT line in either the faraday cage or on the module top. Both these shorts got resolved by taking everything apart. Still not sure how it happened.
Next I found I could not raise the anode voltage above 230V, it looked like it was current limiting but since the current limit was high, I figured it had something to do with the new electronics installed. I disconnected them all the in cage and that solved the problem, and then reconnecting the gemovs that go from the PSU terminals to HV common caused the problem again, so I left those disconnected. |
Monday, September 30, 2013, 16:04, Bevan Moss, Conditioning Station, Repair, TM3, NiO#2, Ion gauge filament replacement
|
The filament on IG1 for TM3 was replaced by myself and Edi. The old filament did not appear to be damaged but the controller claimed it was. The current gauge on TM3 is a single filament, ideally it would be upgraded to a double. |
Thursday, September 14, 2023, 11:16, Adam Newsome, Spent Target Vault, Development, , Ta #58, Investigation of Pail 211 (Ta #58)
|
Upon attempting to lower Pail 211 into their tile hole, CNL encountered issues with the pail getting stuck. They shipped the pail back to TRIUMF and requested we perform an investigation. The investigation report is attached.
The pail contents must be re-packaged into a new pail.
Note: the F-308 is currently sitting in the Meson Hall warm cell at approximately 250 uSv/h at 0.5 m.
Dose for primary worker (Chad Fisher) who inspected the cable, unbolted the flask lid, and handled the pail briefly: approx. 104 uSv
Dose for secondary worker (Danka Krsmanovic) who swiped the pail and flask to check for contamination: approx. 70 uSv
More photos available upon request from Adam Newsome. |
Thursday, February 20, 2020, 09:27, David Wang, Spent Target Vault, Standard Operation, , , Inventory of mini storage and vault. 
|
Repacked nSiC#1 in SHC and moved it to mini storage vault. Transferred UCx26 and UCx28# from vault to mini-storage. See attachment for vault and mini-storage inventory. |
Tuesday, November 08, 2016, 14:04, Isaac Earle, North Hot-Cell, Development, , , Interference check with TCS turbo pump and proposed NHC duct routing  
|
David Wang and I accessed the NHC today to check if the proposed duct routing (IRH1618) will interfere with servicing or replacement of the TCS turbo pump. A piece of plywood was placed in the future position of the NHC/TCS partition wall (IRH1609), and a ducting elbow was placed at the approximate position of the nearest elbow to the turbo pump.
David concluded that the ducting in the proposed location will not have any significant effect on replacement of the turbo pump, and he does not expect replacement will be difficult to perform after installation of the wall and NHC ducting. Standing at floor level towards the east side of the TCS space and reaching upwards seemed to be the best way to reach the turbo pump flange bolts. It was also noted that there was sufficient room in the TCS space for two workers to be in the area.
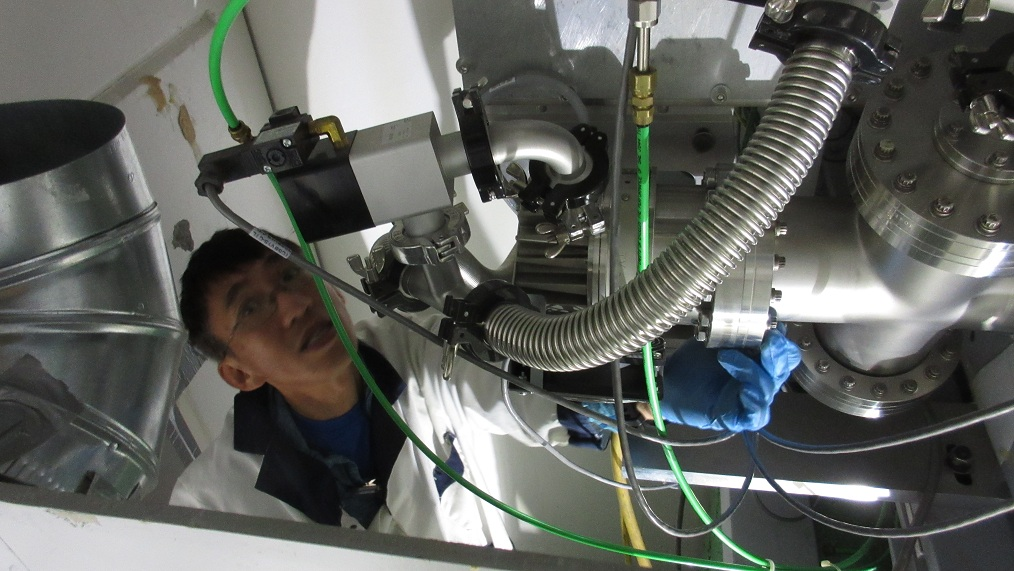


|
Thursday, September 21, 2017, 12:07, chad fisher, South Hot-Cell, Repair, TM2, , Insulator Replacement
|
Insulators ITD0053 and 54 have been replaced. All fasteners torqued to 56 in lbs.
|
Monday, September 23, 2024, 16:06, Aaron Tam, South Hot-Cell, Repair, TM3, , Insulator Addition to Water block  
|
September 23, 2024 - C. Fisher
- Containment box removed
- Insulator installed
- New window line VCR seals installed
- Dropped bolt from TiC#8 removed
- Containment box reinstalled
September 23, 2024 - A. Tam
- Containment box cover reinstalled
Photos attached |
Wednesday, December 19, 2018, 14:41, Anders Mjos, Conditioning Station, Standard Operation, , No target, Installed Shield Block on TCS
|
Frank and Anders installed lid on TCS and started vacuum system yesterday. To run over the Holidays. Retrieved dose badge from operational storage area. Measured field to be ~ 10 mSv/h at ~9am. Beam went off about 8:30am. |
Wednesday, November 06, 2013, 10:41, David Wang, South Hot-Cell, Repair, TM2, , Installed 2 turbopumps on TM2
|
Bevan and I installed 2 turbo pumps on TM2. The o- ring flanges on TM2 had been cleaned before the installation. |
Thursday, October 05, 2017, 11:04, Anders Mjos, ITW, Maintenance, , , Installation of new valve for module move ventilation
|
David installed the new ball valve and connections for the SAS project module move ventilation. SASP0482. Drawing reference ISK5029B. |
Thursday, April 06, 2017, 15:16, Anders Mjos, Conditioning Station, Maintenance, , , Installation of new break out box to accommodate both ITM:MP2 and TCS:MP1
|
Installation by Marshall. Dave M from controls adjusted circuitry to get TCS:MP1 to start.
Work is being done in preparation for the Module Move Ventilation SAS project |
Wednesday, September 12, 2018, 15:30, Isaac Earle, North Hot-Cell, Development, , , Installation of NHC operator-level lighting completed  
|
Installation of of operator-level lighting in the NHC was completed today according to drawing IRH1801. 2" x 2" Panduit was mounted to the wall on aluminum brackets to support the power cables. These lights can be replaced remotely by unplugging the power cords using the manipulators, lifting the cable out of the Panduit with a hooked pole tool through the manipulator slave end removal roof hatch, lifting the light fixture off the support bracket with the pole tool, then installing a new fixture in the opposite order. This RH procedure will be tested at a later date as part of NHC commissioning.

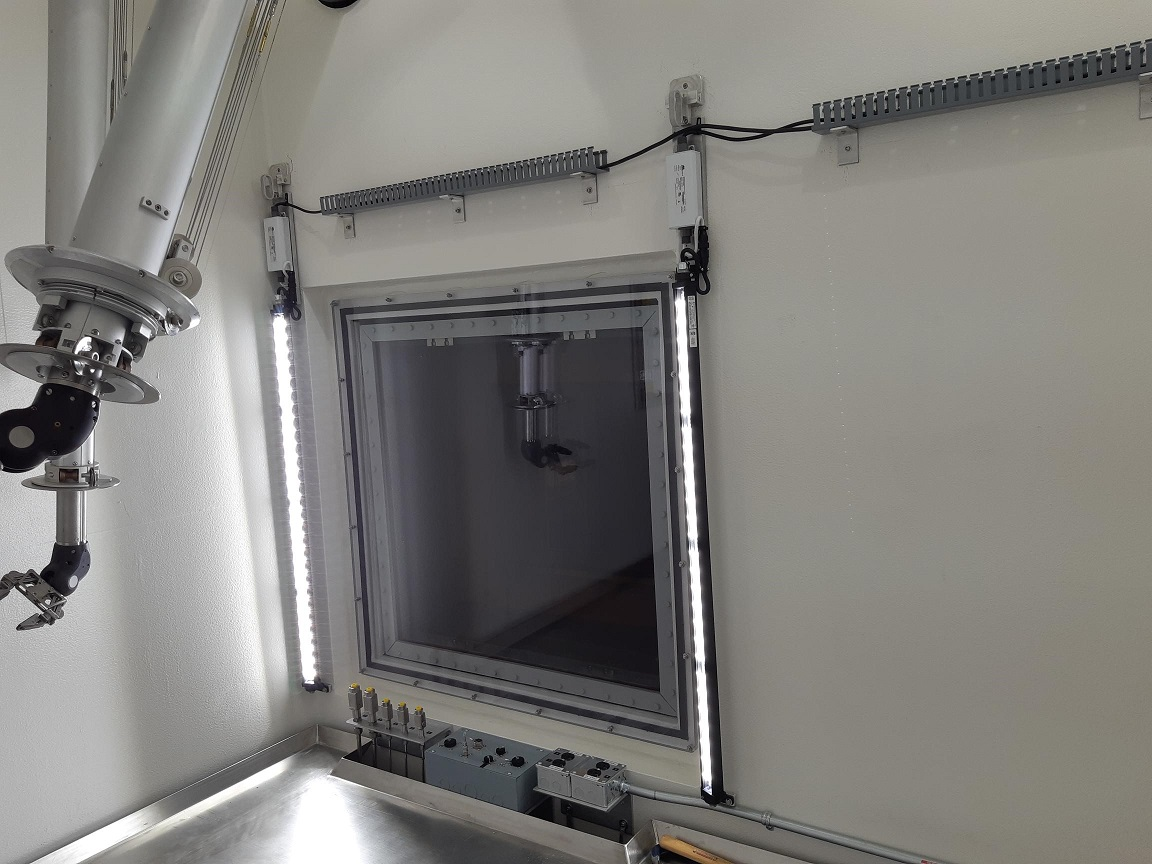
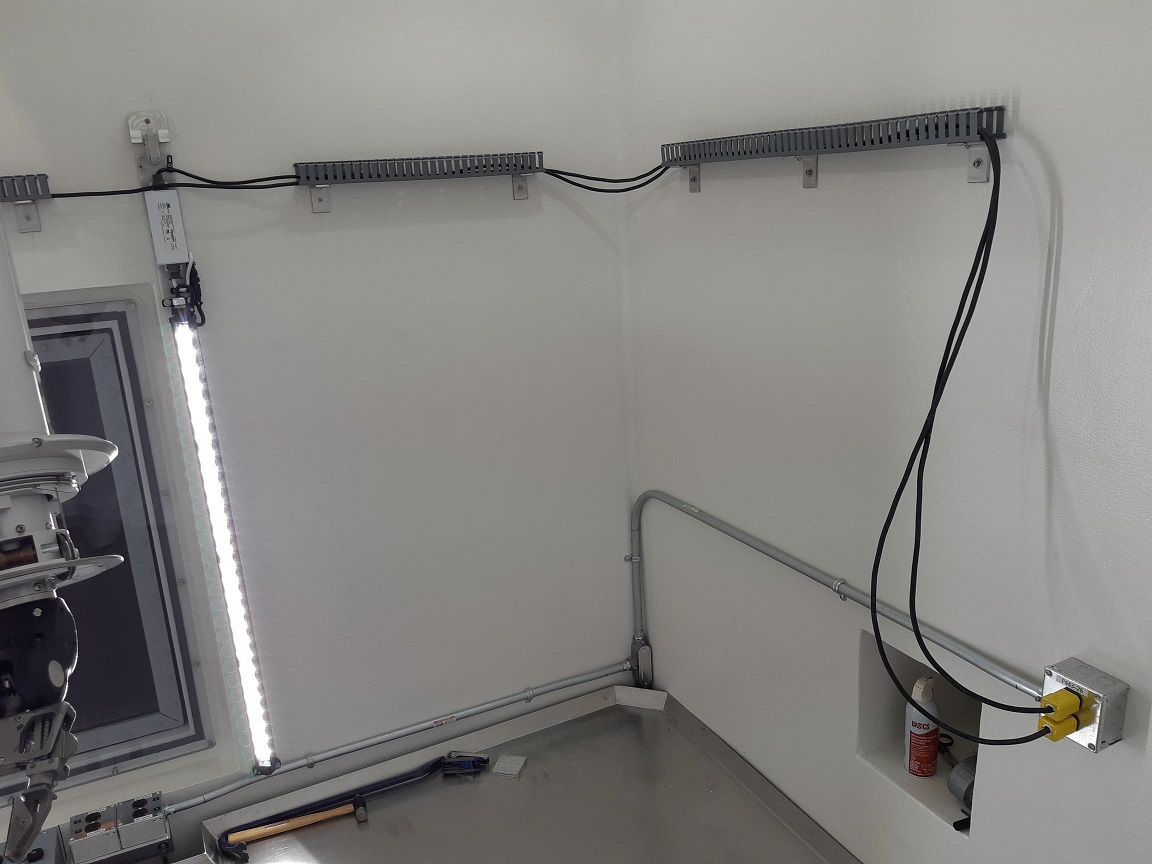
|
Wednesday, November 15, 2017, 08:55, David Wang, Conditioning Station, Standard Operation, , , Install shield plug onto TCS and pumping down TCS.
|
Shielding plug is installed onto TCS. TCS is being pumped down to keep it under vacuum for the rest of the year. |
Wednesday, October 14, 2015, 14:49, David Wang, South Hot-Cell, Standard Operation, TM2, , Install new high current cables to TM2  
|
I installed a set of new high current cables for TM2 Febiad run. The top of TM2 is configured to Febiad mode. See attachments |
Thursday, January 25, 2024, 07:31, David Wang, Crane, Standard Operation, , , Inspection oftareg hall crane below hook attachment pins and plates ITA6550-01
|
Tom Kauss inspected target hall crane below hook attachment pins and plates ITA6550-01 yesterday. He certified the use of these pins and plates for year 2024. The inspection of these pins and plates was in Target hall crane annual check list. It was issued as a calibration index by Isaac Earle in 2022-Feb-08. After inspection, The inspection tag was issued and attached to pin. Tom has an inspection record on this job. |
Thursday, January 25, 2024, 07:27, David Wang, Crane, Standard Operation, , , Inspection of target module lifting frames ITA0494-1997-01 and ITA0494-1997-02
|
Tom Gauss inspected two target module lifting frames ITA0494-1997-01 and ITA0494-1997-02 yesterday. He certified the use of these two frames for 2024. Inspection tags have been issued and attached to frames. He has inspection record on them. |
Friday, January 27, 2023, 07:18, David Wang, Crane, Standard Operation, , , Inspection of target module lifing frame ITA0494-1997-01 and ITA0494-1997-02
|
Tom Gauss inspected two target module lifting frames ITA0494-1997-01 and ITA0494-1997-02 yesterday. He certified the use of these two frames for 2023. Inspection tags have been issued and attached to frames. He has inspection record on them. |
Wednesday, November 16, 2011, 07:46, chad fisher, South Hot-Cell, Standard Operation, TM1, TaC#1, Inspection of TaC#1
|
Inspection of TaC#1 showed that the oven was indeed broken on the A+ (left oven leg) side of the central block.
See the following for pictures.
https://documents.triumf.ca/docushare/dsweb/View/Collection-7438 |
|