|
ID |
Date |
Author |
Category |
Type |
Specific |
Subject |
|
94
|
Tuesday, November 26, 2013, 10:33 |
Isaac Earle | Repair | Target 2 | Target | T2-MK2 Water Flush |
The T2-MK2 target in the hot cell was flushed with water and then purged with air so that stagnant water is not left sitting in the target. Replacement of the failed 10cm Be cassette will take place in January 2014. |
|
196
|
Monday, April 11, 2016, 13:54 |
Isaac Earle | Standard Operation | Target 2 | Target | T2-MK2 Target Transported from BL to HC |
The T2-MK2 target was transported from the beam line to the hot cell using the transfer flask. The target was measured to be 120mSv/hr at 0.5m. The steel shielding plug was installed in the T2 target hole to reduce upwards shine.
New beryllium target cassettes will be installed on the target ladder before it is returned to the beam line. |
|
201
|
Wednesday, June 15, 2016, 11:00 |
Isaac Earle | Standard Operation | Target 2 | Target | T2-MK2 Target Moved to Position #1 |
Position #4 on the T2-MK2 target has now reached the maximum beam time. The target was moved to Position #1 at the nominal elevation. This target should be used for the remainder of the 2016 running period. |
|
212
|
Monday, January 09, 2017, 15:07 |
Isaac Earle | Standard Operation | Target 2 | Target | T2-MK2 Target Moved from BL to HC |
The T2-MK2 target assembly was moved from the beam line to the hot cell today. A maximum field of 203mSv/hr was measured at approximately 0.5m
A steel shielding plug has been installed in the T2 hole to reduce shine and allow the T2 volume to be pumped down. |
|
74
|
Monday, March 18, 2013, 15:17 |
Isaac Earle | Maintenance | Target 2 | Target | T2-MK2 Target Maintenance and Re-Wiring |
- T2-MK2 target moved from beamline to hot cell (Feb 4th)
- Steel target support shield installed as well as ~3 layers of lead blankets. Even with this extra shielding fields in the working area were as high as 800µSv/hr.
- Target flushed with water, then with air overnight to dry
- Target pumped out using cold trap (required 4 iterations to removed all water)
- Target lift "T" removed, painted, labelled
- Unused proximity sensor removed and stored in tool port boot box cabinet
- Replaced o-rings for feed through ports #1, 2, and 3, as well as plug port
- Removed unused electrical feedthrough at port #3 and replaced with plug
- Replaced all nylon Swagelok ferrules on water supply lines
- Leak checked upper water supply lines, found Hansen fitting teflon tape needed replacing, then was leak tight
- Target wiring inspected by Dave Cameron, determined all wiring requires replacement including motor wires
- Removed target ladder drive motor, found motor coupling had degraded and was crumbling
- Ordered new aluminum flexible coupling (McMaster PN: 6208K511)
- Installed new coupling and replacement motor (See attached photo)
- Disassembled profile monitor upper cable housing, and inspected the o-ring under part SKRH1001B. The condition of the o-ring was good. Bent pins found on Deutsche connector
- Deutsche connector was found to be installed with 2 o-rings in a single o-ring groove, neither was the correct size
- Reassembled profile monitor assembly using new Deutsche connector installed with nut side up for easier future removal. New SKRH1001B part was used with polished o-ring surfaces. New o-rings used with Apiezon M grease
- Re-wiring completed by Dave Cameron (March 12th) (See attached photos)
- Checked motor functionality, position microswitches, monitor microswitches: All OK
- Actuated profile monitor: smooth travel, no bellows twist, fully engaged @ 20psi
- Installed lift "T", threads on support pillar B10106 required chasing
- Photographed target ladder and above vacuum flange
- Confirmed suspicion that part B10105 is undersized and was installed with an undocumented spacer between it and part D10390
- Added this spacer to Solidworks model of target (3/4" OD, 0.505" ID, 5/8" height)
- Leak checked water supply bellows and target cassettes: OK (scanned PDF of results attached)
- Target ladder left in position 0
- Profile monitor raised and secured in position for transport
- Target moved to storage pit location #5 (no standoffs on pit hole flange) (~1.8mSv/hr at 3-4m from target) (March 15th)
- The old T2 heat exchanger tube array was moved to the storage pit while the blocks were off (placed between hole locations 12 & 13)
|
Attachment 1: IMG_1189.JPG
|
|
Attachment 2: IMG_1194.JPG
|
|
Attachment 3: IMG_1197.JPG
|
|
Attachment 4: IMG_1207.JPG
|
|
Attachment 5: T2-MK2_Tgt_leak_check.PDF
|
|
|
175
|
Thursday, October 01, 2015, 11:43 |
Isaac Earle | Repair | Target 2 | Target | T2-MK2 Target Ladder Drive Motor Failure |
The stepper motor that drives the target ladder on T2-MK2 has failed. This is the cause of the difficulty moving the target ladder yesterday afternoon (see previous e-log). This was confirmed this morning by attempting to move the T1-MK1 target ladder in the storage pit using the portable control box - the ladder moved with no issues.
The motor is scheduled for replacement during the 2016 winter shutdown unless it is needed more urgently. Operations have been informed that T2 ladder movement will not be possible until this motor is replaced. |
|
156
|
Friday, April 24, 2015, 11:53 |
Isaac Earle | Standard Operation | Target 2 | Target | T2-MK2 Target Info Sheet & Elevations |
T2-MK2 target information sheet, beam spot measurements, and elevations were updated and delivered to Operations. PDF copy attached.
No work was done to T1-MK2 (placed in storage pit for 2015 shutdown duration to lower fields), so the sheets will not be updated. |
Attachment 1: T2-MK2_-_2015_Elevations.pdf
|
|
|
197
|
Friday, April 15, 2016, 14:54 |
Isaac Earle | Standard Operation | Target 2 | Target | T2-MK2 Target Changes & Return to Beamline |
On April 11th the T2-MK2 target was flushed with water, then overnight with air at 5psi supply pressure. The target ladder was in Position 0 for this procedure.
On April 12th the target was pumped using a cold trap and the Varian leak detector for approximately 2 hours.
On April 13th pumping was restarted and the leak detector reached 0.0E-10 Torr*L/s with < 1.0E-3 Torr test port pressure. A general helium spray was performed with a small response to the mid 10^-9 range and quick recovery (this target was in use all of the 2015 running period w/o any vacuum issues). Plugs were removed from Positions 1 & 2. The swagelok threads on the ladder were cleaned with a wire brush then pressurized air. The sealing surfaces were cleaned using Scotchbrite then blown with air. Threads and sealing surfaces were inspected with the Nikon level: some minor thread imperfects on the threads and a few small pits on the sealing surfaces were observed. New 10cm beryllium targets were installed (Position 1: Target "OCT.06#3", Position 2: Target "#201"). A leak check was performed using 0.5s bursts of helium at supply pressure 3psi. Helium was applied at all target positions, delta seal locations, and along the length of both bellows. No responses observed that were greater than the initial leak check performed before the plugs were removed, therefore the target was deemed water leak tight and ready for use.
On April 14th position measurements for both new targets were taken as per Document-50194, which will be included in the target info sheet to be delivered to Operations.
On April 15th the target was returned to the beamline. All services were attached, the cooling package started, and vacuum pumped down normally.
Photographs of the Position 4 beam spots as well as the target ladder after new target installation are attached. |
Attachment 1: T2-MK2_Position_4_Entrance_Side_-_April_14_2016.JPG
|
|
Attachment 2: T2-MK2_Position_4_Exit_Side_-_April_14_2016.JPG
|
|
Attachment 3: IMG_7024.JPG
|
|
Attachment 4: IMG_7026.JPG
|
|
|
148
|
Monday, April 20, 2015, 11:42 |
Isaac Earle | Standard Operation | Target 2 | Target | T2-MK2 Target & T2 Protect Moved |
The T2-MK2 target was moved from the hot cell to the beam line. The T2 Protect Monitor was moved from the beam line to the hot cell. The T2-MK2 assembly measured 136mSv/hr at 0.5m, and the protect monitor was 8mSv/hr. Total dose incurred by Isaac Earle: 0.18mSv. No dose to other workers |
|
95
|
Monday, January 06, 2014, 15:55 |
Isaac Earle | Repair | Target 2 | Target | T2-MK2 Repair |
The leaking 10cm Be target was removed from position 3 on the T2-MK2 target ladder and the water ports were blanked-off with 3/8" Swagelok plugs. A 10cm Be target remains in position 4. The target was pumped down using the cold trap and a helium leak check was performed. All target locations on the ladder were found to be leak tight. The delta seal locations and fittings above the vacuum flange were also leak tight, however small leaks were discovered at the weld at the lower end of each bellows, details below.
Using the old leak detector in the Meson Hall HC Lab, at baseline level 18 on 10X scale with the target oriented as when installed in the beamline, using 1/2 second application of helium at ~3psi:
East side bellows: response up to 90 on 10X scale, returned to baseline in ~5s
West side bellows: response up to 30 on 50X scale, returned to baseline in ~5s
Based on previous helium leaks of this size it is expected that the bellows are still water leak tight. Replacement of the bellows will not be considered unless a water leak is found.
After an electrical check is performed on the profile monitor by Probes Group, this target will be returned to the beam line and pumped down to check for water leaks. If water leak tight, the T2-MK2 target will be used for operation in 2014.
Photos are attached of the failed 10cm Be target, as well as the T2-MK2 target assembly with leak locations indicated. |
Attachment 1: DSC_6622.JPG
|
|
Attachment 2: DSC_6623.JPG
|
|
Attachment 3: DSC_6626.JPG
|
|
Attachment 4: IMG_1809.JPG
|
|
|
200
|
Friday, May 13, 2016, 15:04 |
Isaac Earle | Standard Operation | Target 2 | Target | T2-MK2 Position 4 Adjusted to +1.5mm Offset |
The T2-MK2 target at Position 4 has been adjust to approximately +1.5mm offset. This causes the ladder to be moved downwards, raising the beam spot location on the target window. The potentiometer ratio at this offset is approximately 0.810 (> 0.8059 nominal ratio for position 4, and therefore closer to Position 5)
The purpose of the offset is to better center the beamspot on the target window. Target window photographs showed the beam spot being slightly below center (See E-Log #197), and target ladder elevations taken in Spring 2016 showed the Position 4 target approximately 1.0mm above the profile monitor center.
MCR has been instructed to continue running with this offset, and a message with details on how to do so was posted to their Plone site. |
|
213
|
Thursday, January 12, 2017, 09:21 |
Isaac Earle | Standard Operation | Target 2 | Target | T2-MK2 Position 1 Beam Spot |
The beam spot on the 10cm beryllium target in Position 1 on T2-MK2 (Target ID: "OCT.06#3") was measured and photographed yesterday. A fairly well centered spot was measured to be approximately 4.6mm wide x 5.2mm tall on the entrance window and 5.7mm wide x 7.6mm tall on the exit window using the Nikon micrometer level. This target first saw beam on June 16, 2016.
A PDF scan of the beam spot measurements and photographs of the beam spots are attached.
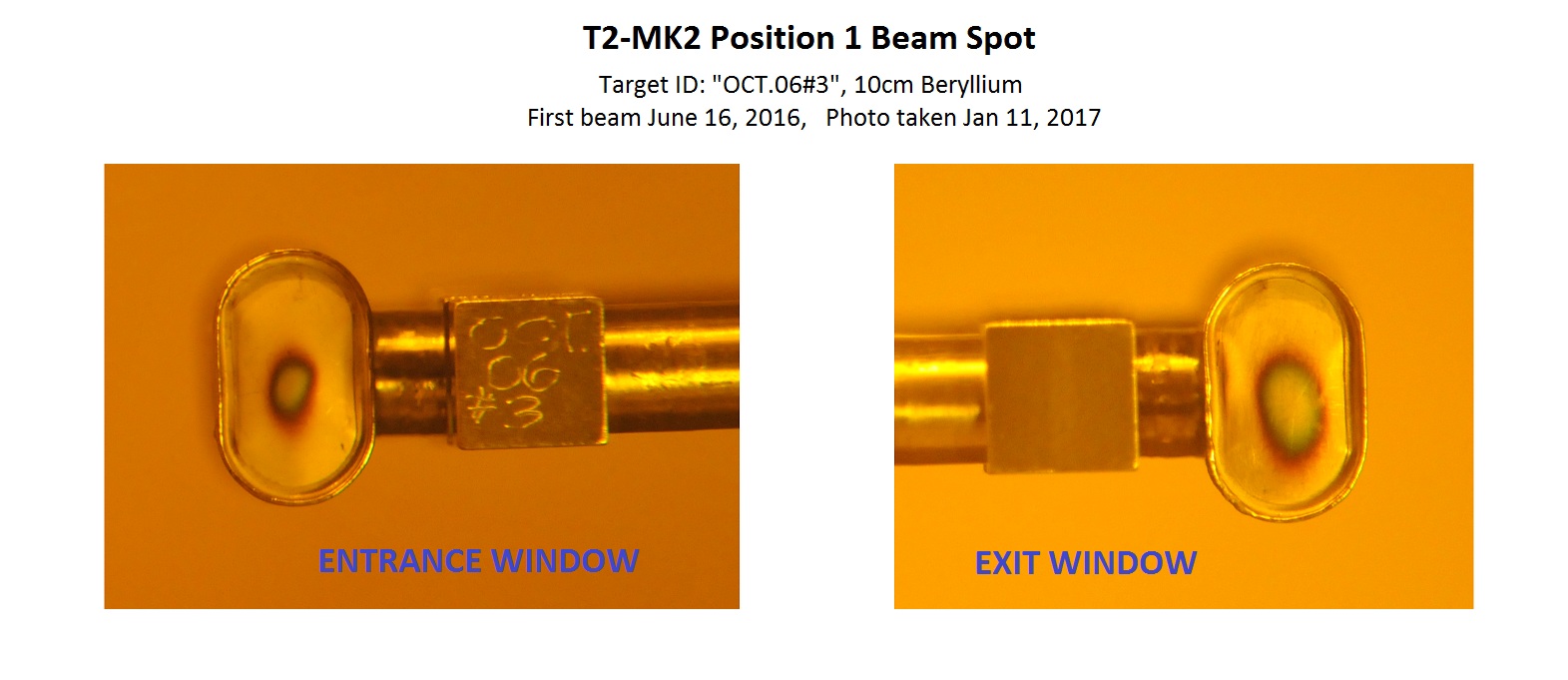
|
Attachment 2: T2-MK2_Position_1_Beam_Spot_Measurements_-_Jan_11_2017.pdf
|
|
|
145
|
Thursday, March 12, 2015, 10:51 |
Isaac Earle | Standard Operation | Target 2 | Target | T2-MK2 Pos'n 4 Elevation Measurements |
Elevation measurements of the T2-MK2 target were taken in the hot cell to confirm previous records in preparation for the T2 Protect Monitor adjustment that will take place later this shutdown. Potentiometer readings were also checked for ladder position 2mm above and below nominal in case we decide to run the target in an offset position again.
Entrance Side:
Ladder moved until potentiometer at 16.19kΩ (nominal position 4)
- Measurement on tape: 1838.7mm
At elevation 1836.7mm: 16.04kΩ
At elevation 1840.7mm: 16.27kΩ
Exit Side:
Ladder moved until potentiometer at 16.19kΩ
- Measurement on tape: 1837.9mm
At elevation 1835.9mm: 16.04kΩ
At elevation 1839.9mm: 16.29kΩ
The elevation measurements at nominal position agree with those taken in May 2014.
The T2-MK2 target is now ready to be returned to the beam line after completion of the M9-T2 work.
Keith C. Ng and Isaac Earle both received .02mSv dose during this procedure.
|
|
96
|
Thursday, January 09, 2014, 15:21 |
Isaac Earle | Repair | Target 2 | Target | T2-MK2 Electrical Check |
An electrical check was performed on the T2-MK2 profile monitor by Bill Rawnsley. All signals produced the expected response, and Bill approved the monitor for use. Bill has saved screenshots of the signal profile.
The target ladder position micro-switches and profile monitor in/out limit switches were also tested: all OK.
The T2-MK2 target is now ready to be transported to the beam line. |
|
180
|
Friday, October 09, 2015, 15:18 |
Isaac Earle | Repair | Target 2 | Target | T2-MK2 Check at Hot Cell and Motor Drive Cable Replacement |
While the T2 monolith was uncovered for T2 Protect repair (see previous e-log), it was decided that the T2 target should be moved to the hot cell to address issues discovered last week with target ladder movement (see e-log #175)
Oct 7:
- T2-MK2 target was moved from the beamline to the hot cell after the T2 protect was reinstalled (the target measured 896mSv/hr at 0.5m)
- The target was inspected in the hot cell: profile monitor looked normal, two beam spots (one higher, one lower) were observed on the entrance window (see photos), the spot on the exit window was low but not quite touching the weld
- T2 profile monitor was checked by probes group at the hot cell --> ok
- Ladder movement was checked by cycling through all target positions twice using the portable control box. This revealed that the drive motor is actually functioning properly and the fault lies elsewhere
- Tested T2 motor drive cable from 1A racks to beamline with Dave Cameron. Found Pin B has 190kOhm short to building ground. Attempts to fix the cable at both ends were unsuccessful and spare wires in the bundle could not be used because there is a break in the cable at an unknown location and use of wire colours in both sections is inconsistent
- Checked entrance side elevation: 1839.0mm with potentiometer at 16.19kOhms. This is consistent with previous measurement of 1838.7mm. This confirms that pot, motor, and drivetrain for ladder movement are all ok.
Oct 8:
- Decided to run new cable for target motor drive (already had on hand for T1/T2 controls upgrade in 2016 shutdown). The cable is labeled T2TGTMTR-DRV. It was first tested at the hot cell and then installed by Doug and Ron
- The T2-MK2 target was returned to the beamline. A camera and monitor setup was used to watch the target entering the hole remotely which greatly reduced dose (inserting the target requires multiple iterations to get alignment correct, so dose is typically higher than when removing devices from the monolith)
- T2 profile and protect monitors checked by Probes Group from the mezannine --> both ok
- Pumping on T2 volume began late morning, leak was found at T2 protect flange (see previous e-log), after correcting this the vacuum pumped down normally. A helium leak check was performed on all flanges on the T2 monolith --> no leaks found
Oct 9:
- All services attached to target
- T2-MK2 target moved to position 0 using the new cable and the portable control box
- T2 cooling package started (no change to vacuum)
- T2 cooling package expansion tank level checked - the tank was only ~1/3 full, suspected leak through disconnected female hansen connection. Tank was refilled to normal level using ISIS water
- Plant Group began replacement of blocks over T2 late morning |
Attachment 1: entrance_1.JPG
|
|
Attachment 2: entrance_2.JPG
|
|
Attachment 3: entrance_3.JPG
|
|
Attachment 4: exit_1.JPG
|
|
Attachment 5: exit_2.JPG
|
|
Attachment 6: exit_3.JPG
|
|
Attachment 7: profile_mon.JPG
|
|
|
290
|
Thursday, May 05, 2022, 14:38 |
Adam Newsome | Maintenance | Target 2 | Controls | T2-MK1: profile monitor actuation check and repair to connector |
An attempt was made to actuation the T2 profile monitor, however it showed up in EPICS as being not present. Furthermore, the "Remote" indicator light on the physical controller was not lit up despite the switch being in remote mode. The limit switch indicator light was working.
Upon troubleshooting with Erwin Klassen, it was determined that a jumper was missing on the profile monitor control connector (on the target end, rear of bulkhead). The jumper shorts pins A and G on the mil-spec connector on the controller end, which is for 120 VAC supply, to indicate that the device is connected. T1-MK1 was checked - this jumper was present on T1-MK1, across pins E and F of the mil-spec connector, but was not present on T2-MK1. Otherwise the connectors were identical. It is suspected that it was accidentally omitted during maintenance in the past. Regardless, a new jumper was soldered in-place on T2-MK1 across pins E and F to replicate T1-MK1. The system functioned normally after this.
Attached photo shows the completed solder job - the current state of the connector on the rear side of the target bulkhead panel. |
Attachment 1: T2-MK1_prof_mon_connector_-_rear_-_after_fix.jpg
|
|
|
287
|
Wednesday, April 13, 2022, 12:33 |
Adam Newsome | Standard Operation | Target 2 | Target | T2-MK1 moved: from storage area to target station |
The T2-MK1 target was moved from the storage area (formerly position 4) to the target station. Services were reconnected in order to prepare for normal operation. |
|
55
|
Friday, September 07, 2012, 16:35 |
Isaac Earle | Repair | Target 2 | Target | T2-MK1 Target Repair Completed |
- Profile monitor wiring harness checked by Bill Rawnsley using resistor pack --> OK
- New profile monitor (0.005" gold coated molybdenum wires) installed & blip tested --> OK
- Potentiometer checked --> OK
- Target position and profile monitor in/out micro-switches checked --> All OK
- Target leak checked: very small response at top and base of left side bellows (when facing target ladder), otherwise leak tight
(Meter on 10X scale, Baseline: 6. Meter reached 9 at top of bellows, 11 at bottom of bellows with 1s He application. Both recovered after ~30s)
- Straightened twisted bellows on both sides which was causing "clicking" noises during target ladder travel
(Note: water supply tube nylon swagelok ferrules should be replaced at next opportunity, currently no spare parts)
- Target leak checked again - No change due to bellows adjustment
- Static water pressure test performed, as target is likely water leak tight: Target filled with water, pressurized with air to 80psi, then valved off and left overnight. No visible water leak from bellows. Pressure dropped 11psi over 15 hours. Test was repeated, but the line valved off before the target to establish a baseline. The baseline test dropped 15psi over 16 hours. The increased leak is likely due to the additional valve added to the system, or different amounts of air in the system compared to total system volume. Baseline test shows that the pressure drop seen in first test appears to be due to a small leak in the test equipment, or expansion over time of the supply water hose. Concluded that target is water leak tight. Additionally, target assemblies have been installed in the beam line in the past with significantly higher helium leak rates, and no observed water leak, with no problems.
- All water pumped from target using liquid nitrogen trap
- Target ladder moved to position zero
- Target moved from hot cell to storage pit location #4. Ready for use in beam line. |
|
66
|
Tuesday, January 08, 2013, 10:52 |
Isaac Earle | Maintenance | Target 2 | Target | T2-MK1 Target Maintenance |
- T2-MK1 target transported from storage pit to hot cell
- Proximity sensor removed
- Target lift "T" removed, painted, relabeled
- Replaced flange o-rings: Plug (#202), Feed through port 1 (#222), Feed through port 2 (#222), Feed through port 3 (#213), Water supply tubes 1 and 2 (#208)
- Replaced all nylon Swagelok ferrules
- Leak checked water tubes: OK
- All wiring above vacuum flange replaced, secured, inspected (D. Cameron)
- Damaged lower MS connectors replaced (D. Cameron)
- Discovered motor wire insulation degrading (D. Cameron)
- Motor replaced and rewired
- Motor, position micro switches, and profile monitor micro switches tested: ALL OK
- Tested profile monitor actuation: Smooth (IN: start motion @ 5psi, fully actuated @ 20psi)
- Target lift "T" installed
- Feed through port cap #2 replaced with TBP0936 (old cap was makeshift part using weird gunk sealant)
- Upper and lower parts of target photographed
- Target ladder moved to position 0
- Target ready for use. Will be transferred to storage pit hole #4
* Approximately 50cpm found on 44-2 monitor from wet wipe used to clean blue flanges surrounding hot cell entrance on HC roof
|
|
183
|
Thursday, November 05, 2015, 17:07 |
Isaac Earle | Repair | Target 2 | Target | T2-MK1 Profile Monitor Repair and Pos'n 3 Target Removal |
The following work was performed on the T2-MK1 target. The profile monitor and monitor cage on this target were damaged in January 2013, See E-Log #68
Oct 23:
- T2-MK1 target moved from storage pit hole #4 to the hot cell (field measurement was not possible because the pole monitor had issues
- Position 2 and 3 targets photographed (see attached)
- Position 3 target (10cm Be) removed. This target had accumulated 11.5 months of beam time. Maximum for T2 targets is 12 months according to new schedule.
Oct 26:
- Position 3 plugged
- Profile monitor cage inspected and photographed. The cage (TBP0106D) and aluminum frame (TBP0101C) were both noticeably damaged (see photos)
- Attempted to insert dummy cassette, went in smoothly
- Moved target ladder through all positions, moves smoothly, micro-switches ok, potentiometer ok
- Motor drive coupling inspected - no issues
- Actuated monitor in and out: traveled fairly smoothly, 40psi required to insert, 20psi to pull back out
- Dummy cassette removed, real replacement cassette inserted (went smoothly)
- Horizontal wires inspected w/ Nikon level, found to be crooked
Oct 27:
- Cassette frame nuts (TBP0108C-2) loosened and monitor frame adjusted until horizontal wires horizontal, nuts re-tightened and torqued
- Vertical and horizontal measurements of profile monitor position measured - All within 1-2mm of previous measurements in 2010
- Although some physical damage to frame is visible it still positions monitor in correct location and seems to be fully functional, therefore will use if electrical is ok
Oct 28:
- Electrical check performed on profile monitor by Mike Russell
- All 26 wires visible. Screenshot of scope taken (see attached)
- Moved to position 5 to stretch bellows, and air left running through target overnight to dry
Oct 29:
- Cold trap filled with LN2, pumping with new leak detector started
- Test port at E-1 Torr range after 30s, E-2 after 1.5mins, E-3 range after 3mins, 0.0E-10 torrL/s leak rate after ~10mins, TP at <1.0E-3Torr after ~15mins
- Leak check performed with 3psi helium applied w/ ~0.5s bursts at all target locations, bellows, top of vac flange, and Hansen fittings
- Small leak found at left bellows lower weld (expect is negligible for water use), no response from all target locations (see attached scan of leak check notes), deemed water leak tight
Nov 3:
- Plumb bob measurements taken
- Vertical and horizontal measurements of Pos'n 2 target taken
- Target ladder moved to position 0, profile monitor secured in IN position to prevent damage during move
Nov 5:
- Target returned to storage pit hole #4
- Field of 53mSv/hr measured at ~0.3m (attempted 0.5m measurement, but was a little close)
The T2-MK1 target is now fully functional and ready for use. The 10cm Be target in position 2 has not seen beam.
Note that the target window welds show some uneveness (see photos), but not expected to affect performance b/c leak tight. The elevations sheet will be updated and filed in the T2 Binder in the Meson Hall HC Lab Office.
|
Attachment 1: damage_to_cage_frame.JPG
|
|
Attachment 2: damage_to_prof_mon_cage.JPG
|
|
Attachment 3: posn_2_entrance_1.JPG
|
|
Attachment 4: posn_2_exit_1.JPG
|
|
Attachment 5: posn_3_entrance_1.JPG
|
|
Attachment 6: posn_3_exit_1.JPG
|
|
Attachment 7: T2_MK1_target_with_a_new_profile_monitor_(oct_28_2015_by_mike_russell).JPG
|
|
Attachment 8: T2MK1_leak_check_notes_-_nov_2015.jpg
|
|