|
ID |
Date |
Author |
Category |
Type |
Specific |
Subject |
|
250
|
Tuesday, April 16, 2019, 15:35 |
Keith C Ng | Repair | Other | M9 | M9 project post shutdown summary |
Completed work at m9 beam line:
- Removed existing service stand and associated cable and water services. Legacy b1 water services still need to be removed for future magnet installation. Old service stand is currently in warm cell waiting for disposal.
- M9 Q345 and vacuum roughing line were cleaned by CMMS group.
- M9 B1 is disconnected but remains in beam line ready for removal and refurbishment for 2020 shut down. Relevant ports have been sealed off.
- New Q1 Q2 baseplate was test fit and did not fit with guide post bolted in place, interferes with T2 port blank off plate.
- 3d lidar scans of magnet space were done.
- Leica tracker data was taken of the holes in the poured in place concrete pad.
Photos from shutdown are on remote handling group folder, under "\\trwindata\groups\remote handling\Photos\2019\2019 m9 project" |
|
262
|
Monday, April 06, 2020, 15:02 |
Isaac Earle | Standard Operation | Target 2 | M9 | M9 beam blocker returned to beamline |
The M9 beam blocker was returned to the beamline today using the RH shielded transport flask. The top flange o-ring was replaced before installation.
After installation the "Lift T" assembly was removed, and electrical cable and air supply connected. Correct functionality of the limit switches was confirmed with the control room. Actuation of the beam blocker could not be tested at this time because control takes place through the M9 area ASU.
|
|
261
|
Monday, March 23, 2020, 16:13 |
Isaac Earle | Maintenance | Other | Other | M9 beam blocker MRO completed |
M9 beam blocker MRO work was completed in the hot cell today. This included replacement of the main shaft seals and replacement of the air cylinders. Actuation was tested after replacement and the blocker moved smoothly through the full length of travel with approximately 45psi air pressure. It is ready for transport back to the beamline. |
|
289
|
Wednesday, May 04, 2022, 11:27 |
Adam Newsome | Standard Operation | Target 2 | M9 | M9 and M20 Beam Blocker Actuation Test |
The beam blockers for M9 and M20 were actuated, and vacuum was monitored to ensure no disruptions. Both actuation tests were successful. Motion was observed and no abnormalities noted. Cabling and air connections checked: OK.
Note: there was a safety interlock issue with M9 which prevented actuation - a relay or fuse was temporarily removed from the safety system ~10 years ago but it was not replaced. It was replaced for the purpose of this test, and then removed again. |
|
265
|
Friday, June 12, 2020, 13:54 |
Isaac Earle | Development | Other | M9 | M9 Q1Q2 water header installed |
The Q1Q2 water header (TB23481) was mounted this morning as per installation drawing TB23400.
Heat shrink tubing was applied to the B1 power cables (two positive, two negative) over the length of cable in the highest field which was showing some signs of radiation damage on the insulation. The tubing used was McMaster-Carr PN 75665K932 (Clear PTFE, 4:1 shrink ratio, 1.0" ID before shrinking), as recommended by Syd Kreitzman. Each piece of tubing is 4' long, and two were used per cable. The first one was shrunk along its full length, then the second piece was only shrunk where it overlaps the first and the remainder was left loose. This was done to minimize time required in the high dose area.
Hand-stacked concrete bricks were removed from the location where the new piping will run to the water header. This is scheduled to take place between July 6-8 |
Attachment 1: 2.jpg
|
|
Attachment 2: 1.jpg
|
|
|
260
|
Wednesday, March 11, 2020, 10:29 |
Isaac Earle | Development | Other | M9 | M9 Q1Q2 service stand foot plate installed |
The M9 Q1Q2 "foot" plate (TB23363) has been installed over the floor plate. A nominal gap between the plates of 1/2" was set before lowering the plate, it was then leveled using the three adjustment bolts resulting in a larger gap. After leveling, the plate was lifted to remove the spirit levels and lock the position of the leveling bolts. The plate was then re-lowered and the tiedown bolt assemblies (TB23383) were installed using 50ft*lbf of torque (about the maximum practical amount with standard 20' pole tools) |
|
258
|
Friday, February 28, 2020, 09:06 |
Isaac Earle | Development | Other | M9 | M9 Q1Q2 service stand floor plate installed |
The M9 service stand floor plate (TB23351) was installed in the M9 pit yesterday. Prior to installation all 5 threaded inserts were tested using a 1/2"-13 stud tool on an RH pole. The west most hole (shown in red below) had damaged threads and the stud could only be threaded in 2 turns. All other locations (shown in green) had usable threads with 6-8 full turns possible with the stud tool. The plate was installed using RH floor plate bolts (TB23382) at all four locations with viable threads. The bolts were torqued to 30 ft*lbs which on a bench test was shown to fully compress the belleville washer. The standard torque spec for 1/2"-13 stainless bolts (43 ft*lbs) was not used to allow easier disassembly in the future.
 |
|
267
|
Tuesday, July 07, 2020, 15:13 |
Isaac Earle | Development | Other | M9 | M9 Q1Q2 service stand Lemo connector wiring |
The diagram below shows the wiring for the two connectors on the service stand (the wires running from the stand to the power supplies. (see TB23400 for details)
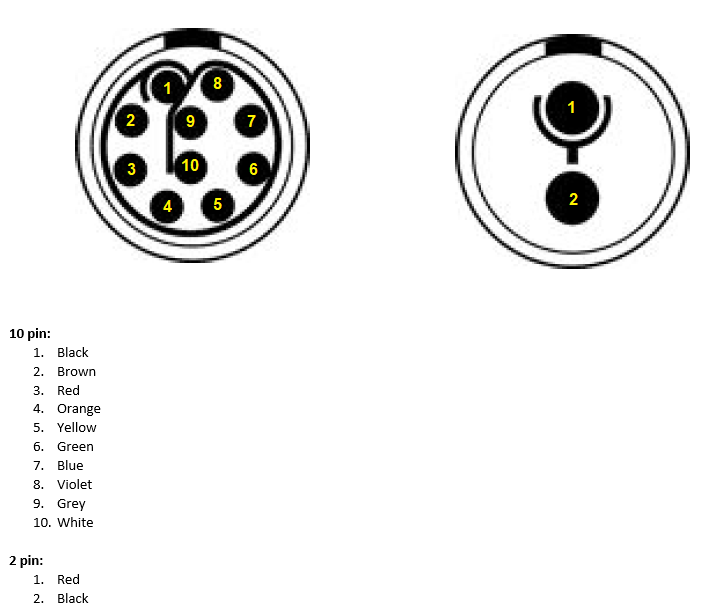
|
|
266
|
Tuesday, July 07, 2020, 13:22 |
Isaac Earle | Development | Other | M9 | M9 Q1Q2 |
The M9 Q1Q2 magnet assembly lift beam has been installed according to drawing TB23401. The side-to-side as well as beam-axis direction adjustment features were tuned so that the assembly is level when lifted.
Aug 5, 2020 update: All fasteners on the lift beam assembly have been torqued according to the specification on drawing TB23401
|
Attachment 1: 8.jpg
|
|
Attachment 2: 1.jpg
|
|
Attachment 3: 4.jpg
|
|
Attachment 4: 6.jpg
|
|
|
13
|
Monday, January 23, 2012, 15:27 |
Isaac Earle | Repair | Target 2 | Target | M20BB returned to beam line. M9BB moved to hot cell. |
M20 beam blocker was transferred from the hot cell to the beam line.
M9 beam blocker was transferred from the beam line to the hot cell.
Field at 50cm from M9 beam blocker during removal: 5000μSv/hr
Field above M9BB hole on monolith after removal: 3500μSv/hr
Unlike M20BB, M9BB has an unmodified lower shielding plate, and no plastic bushing.
|
|
237
|
Friday, April 13, 2018, 14:21 |
Isaac Earle | Maintenance | Other | Other | M20 beam blocker MRO and T1/T2 final checks |
The M20 beam blocker main shaft seals were replaced as per the T1/T2 target device maintenance schedule. Both air cylinders were found to be leaking past the seals, and the blocker would not actuate in the hot cell even with 100psi (max site air) so they were also replaced. With the new cylinders the blocker actuated smoothly at about 45psi. It is recommended that the air cylinders be replaced every second service (once per 10 years). The blocker was returned to the beam line and smooth actuation and limit switch functionality were confirmed.
The following final checks were performed on T1/T2 devices:
- Lower air amplifier started and tuned to 120psi output
- Air amplifier cycle time measured: 70 seconds for two cylinder turn-overs (1 complete cycle)
- T1 and T2 profile monitor actuation checked: T1 reached in and out limits but speed unknown because target covered; T2 traveled smoothly in and out and reached limits as expected
- T1 and T2 target ladders were moved to the various targets that could be used this running period (#1 for T1; #1, 3, and 4 for T2) - No issues
The T1 and T2 targets are ready for the running period. Shielding can now be replaced over T2.
|
|
323
|
Friday, March 03, 2023, 16:00 |
Albert Kong | Maintenance | Target 2 | Other | M20 Return to T2 Monolith + Vaccum Leak / T1-T2 Valve Re-inspection |
We moved M20 back to the T2 monolith and re did the connections for air + limit switches + T2 profile monitor air.
Note: T2 profile monitor electronics sparked when we moved M20 out initially. (Update: Shengli Liu from probes group performed a test on the T2 profile monitor electronics on Mar24 and found that they are working properly)
M20 started leaking when we tried to bring it to vaccum - from the monolith o ring seal and not the main shaft seal - will look to correct on monday.
Verified through measurement that the replacement o ring was the correct size (#268 0.139" diameter compared to the 0.131-0.137" that was remved - likely shrunk over use).
Update (Mar 06, 2023): M20 was lifted ~5 in above the monolith flange and we identified that the leak was caused due to damage to the o ring (image attached).
The o ring likely damaged when M20 was brought into contact wit the monolith flange, lifted up again, and brought down for a final time before vaccum check.
The above procedure was done because the flask tends to stall close to the lowermost position and prevents unlatching unless lifted systems are lowered fully.
This will be noted in updated procedures.
T1/T2 valves were not leaky still (only a few droplets) - pending T2 cooling system pump on for final leak verification. |
Attachment 1: IMG_1755.JPEG
|
|
Attachment 2: IMG_1657.JPEG
|
|
Attachment 3: IMG_1763.jpeg
|
|
Attachment 4: Screenshot_2023-03-30_124716.png
|
|
|
324
|
Monday, March 06, 2023, 16:58 |
Albert Kong | Repair | Target 2 | Cooling | M20 O-Ring Replacement and Valve Replacement Leak Check |
We replaced tha O-ring on M20 at T2 and brought the target station down to vacuum, which allowed the target water pump to be turned on.
After turning the pump on, we inspected the replaced valves for any leaks and found none - the flow on the demineralizing line was adjusted to 1.2GPM (also done at T1) by turning the needle valve.
Will observe till tomorrow to ensure that the T2 system is stable before proceeding with last system check. |
Attachment 1: T1_Mar06_2023.png
|
|
Attachment 2: T2_Mar06_2023.png
|
|
|
319
|
Tuesday, February 21, 2023, 16:56 |
Albert Kong | Maintenance | Target 2 | Other | M20 BB moved to meson hall hot cell roof |
The M20 beam blocker was moved from the T2 monolith to the meson hall hot cell with the remote handling flask (completed ~4pm).
This operation was performed in preparation for M20 maintenance (main shaft o-ring replacement + air cylinder re-lubrication).
RPG surveyors measured 20,000 CPM from swiping the surface of the beam blocker shaft, and measured 25 mSv/hr on contact with the beam blocker.
Fields on the hot cell roof were at 100 uSv/hr at 0.5 meters from the top of the M20 BB. This should reduce drastically with the introduction of lead blanket shielding (see attached pictures).
|
Attachment 1: IMG_1255.JPEG
|
|
|
12
|
Friday, January 20, 2012, 10:23 |
Isaac Earle | Repair | Target 2 | Target | M20 BB Shaft Bearing Replaced |
The replacement shaft bearing was machined by Maico Dalla Valle and installed in the beam blocker. Smooth operation of the beam blocker air cylinders was confirmed, and the beam blocker is scheduled to be re-installed in the T2 monolith on Monday morning (Jan 23). |
Attachment 1: P1010788.JPG
|
|
Attachment 2: P1010808.JPG
|
|
|
162
|
Thursday, June 11, 2015, 16:59 |
Isaac Earle | Development | Other | Controls | Lab Test of New T1/T2 Level Sensors |
The new T1/T2 level sensors (Omega LVCN414) were tested in the RH HC lab today using the Omega software on a laptop and positioning the level sensor flange above a bucket of water with similar height as the expansion tank.
The level sensors behaved as expected with varying water level.
The level sensor was configured with the following parameters:
- Loop Fail-Safe: Empty
- Output at Empty: 4mA at Bottom
- Start-up condition: Empty
- Sensor Height: 50.1cm (Based on TBP1682)
- Fill Height: 45.0cm (Based on TBP1682)
This results in 4mA output at 0cm tank height, and 20mA output at 45.0cm tank height.
This test will be repeated next week with the sensor wired directly to the PLC. |
|
3
|
Friday, November 04, 2011, 13:36 |
Isaac Earle | Maintenance | Target 2 | Target | Kaon Target (Training) |
Moved Kaon Target from storage pit to remote handling hot cell using flask as training exercise. Safety surveyor scanned storage pit area (wide flanges: clean, pit floor: 50cpm). Returned flask to hot cell lab floor and covered storage pit. |
|
288
|
Thursday, April 14, 2022, 14:38 |
Adam Newsome | Other | Target 2 | Diagnostics | Issue with Protect Monitor SHV Cable |
Diagnostics group (Shengli Liu) noted a lack of connectivity between control panel and T2 Protect Monitor via the high voltage cable. Upon inspection it was noted:
- The cable was very brittle due to radiation exposure and it was cracking in multiple places
- In the SHV connector, the pins were slightly bent (bending them back into position seemed to rectify the connectivity issue).
- The cable was bent at the strain relief junction
RH Group has advised that Diagnostics replace the entire cable as soon as possible. For now it appears to be working. |
Attachment 1: PXL_20220414_210238000.jpg
|
|
Attachment 2: PXL_20220414_210053641.jpg
|
|
Attachment 3: PXL_20220414_210037717.jpg
|
|
|
178
|
Tuesday, October 06, 2015, 14:04 |
Isaac Earle | Other | Other | Controls | Instructions for loading display screen for T1/T2 |
The following instructions were provided by Graham Waters:
From diag5pc bootup
Password: cfzx29mkdr
Bring up a terminal (click on "terminal icon" left side of screen)
> su
> xpfk34yzjc
> chmod o+rw /dev/ttyS0
> chmod o+rw /dev/ttys1
Bring up terminal emulator GTKTerm
From booton left of screen
Click on Applications->Accessories->GTKTerm |
|
349
|
Friday, June 28, 2024, 15:44 |
Albert Kong | Other | Other | Transfer Flask | Inspection of Primary Target Transfer Flask |
The primary transfer flask was inspected on the 26th of June, 2024:
- Electrical cabling and connections externally mounted on the flask + on the hook/latch were inspected for wear, damage, proper connections,etc.
- It was learned that the controls+power cable that drives the latch also runs the height indicator pulley+lead weight system, this should be reworked in the future and replaced with proper load bearing rope/cable.
- The cable connecting to the main control box was duct-taped heavily, it may be a good idea to replace it with proper reinforcement in the future.
- The power cable connection to the grey junction box is not terminated properly and should be re-terminated (some other cables may need to be re-terminated properly).
- Various markings on the exterior of the flask were checked:
- Marks on the flask flange were still visible
- Marks on the flask body for reference flask orientation were still visible
- The weight of the flask (30,000 lbs) had faded and was written over with a sharpie (it may still be a good idea to paint a larger version of the weight so that it is visible by the crane operator)
- Limit switches throughout the flask was inspected
- The chain hoist limit switches were tested and both functioned properly, some wear was observed on the spring toggle for the upper limit switch but it does not need to be replaced yet.
- The limit switches on the hook/latch were tested and functioned properly, with the exception of the 'unlatch' limit switch which we could not test because the unlatch indicator light on the control was broken (this should be re-tested in the future).
- Rolling/rotating components (pulleys for the door and level indicator, guide wheels inside the flask, door pin/hinge, main lifting eye, hook latch) were inspected
- A retaining ring was missing from one of the level indicator pulleys which was promptly replaced
- All other pins/shafts/rollers were in visually in good condition and rolled properly (despite some being rusty) and had proper retaining components (cotter pins, retaining rings, etc.).
- Note that for future inspections, it may be a good idea to manually move the various rollers to check by hand if the pins/shafts need to be lubricated
- Also, the lead weight driving the level indicator should be painted over, and a sacrificial contact pad should be used to prevent the load from wearing the outside of the flask
- Electrical assemblies inside the control and grey junction boxes were inspected and found to be in good condition
- *Except for a broken LED for the unlatch limit switch in the main control box (the broken LED issue was sourced to a broken relay that was promptly replaced, the unlatch status light shows up now)
- All hook/latch actuating switches on the control box seemed to be working (note that the finger-related switches were not tested)
- Note that there is an 'override' button on the control box whose purpose is unclear, we should investigate this to determine its purpose in the future
- Note that to access the internals of the control box, only the two central screws along the white line need to be removed
- The chain hoist and cable pulley system for flask door were inspected
- The chain lubrication seemed dry, it would be a good idea to re-lubricate the chain properly and perform some form of maintenance on the hoist in the future
- The chain length is retracted and dropped from a bucket and currently causes the chain to rub against a corner on top of the flask, in the future it may be a good idea to make some changes to avoid this
- The flask door cables used duct tape to prevent the crimped cable loops from fraying and was still in good condition
- In the future, we may want to look into the cables' channel to check for fraying or damage along their length.
- Inspect main flask structure
- Welds on and around the main lifting eye were in good condition without chipping paint
- There was visible deformation on the lifting eye from contact with the hook, but this should be no cause for concern, and besides this, no signs of wear/damage was found on the lifting structure
- The external welds on the main flask body were in good condition
- The welds on the hook/latch that we could see were in good condition and still fully painted
- There was some rusting on the platform
- The welds on the ladder and platform were of lesser quality than the lifting structure but no cracks or broken welds were found
- In the future, we should determine a weight limit for the platform based on some analysis
- The aluminum tray was inspected and found to be in good condition, however we should replace the old rubber pieces with new ones at some point
- The drive mechanism for the doors/hook/latch was tested and we were able to travel the full distance without abnormal sounds from the chain hoist.
- Seismic clamps were inspected and the bolts + threaded inserts were re-tapped and greased for smoother disassembly/installation.
In addition to the items above, the four 'fingers'/actuators that are holstered by the base of the flask was inspected visually, we will confirm their function before determining whether they need regular inspection/maintenance.
Also, at some point we should inspect the target alignment frames, their camera systems, as well as hot cell flask controls systems.
|
Attachment 1: Flask_Inspection_Images_(26_June_2024).pdf
|
|