|
ID |
Date |
Author |
Category |
Type |
Specific |
Subject |
|
188
|
Wednesday, February 24, 2016, 13:03 |
Isaac Earle | Repair | Other | Other | Target Flask 2-Ton Hoist Chain Twist Corrected |
A 1/2 turn twist in the target flask hoist chain has been corrected to address a deficiency observed by inspectors by Gordon Crane. This was accomplished by first holding the flask door yoke at the top position using rope slings, then lowering the hook block spider approximately 6", then lifting the stationary end of the hoist chain approximately 2" using the Meson Hall main crane to make the top of the chain slack.
A missing cotter pin for the counterweight on the RH HC Lab overhead crane was also installed. |
|
189
|
Monday, March 07, 2016, 18:22 |
Isaac Earle | Development | Target 1 | Controls | Preliminary Testing of T1 Control System Complete |
Preliminary testing of the new PLC control system and EPICS interface was completed today for the T1 target, T1 cooling package, and T1 collimator. All systems behaved as specified. This test did not include testing of any T1 thermocouples which will be included as part of the T2 test program to follow. This is not considered system commissioning, which will follow after all preliminary testing is complete and the commissioning plan document has been released.
A scanned copy of the T1 test plan with notes is attached. |
Attachment 1: T1_Testing_Checklist_-_Complete_-_March_7_2016.pdf
|
|
|
190
|
Wednesday, March 16, 2016, 16:50 |
Isaac Earle | Development | Target 2 | Controls | Preliminary Testing of T2 Control System Complete |
Preliminary testing of the new PLC control system and EPICS interface was completed today for the T2 target, T2 cooling package, T2 collimators, and T1 thermocouples. All systems behaved as specified.
Review of the commissioning plan is currently underway.
A scanned copy of the test plan is attached. |
Attachment 1: T2_Testing_Checklist_-_Complete_-_March_16_2016.pdf
|
|
|
191
|
Thursday, March 24, 2016, 14:46 |
Isaac Earle | Other | Other | Other | TNF / 500MeV Resin Cans Removed from Storage Pit #1 |
Three used TNF / 500MeV system cooling system resin cans were removed from the Meson Hall target storage pit (two from Hole #1, one which was stored below block #1).
Two new active cans will be returned to Hole #1 after the TNF resin is changed in a few weeks time. |
|
192
|
Thursday, March 24, 2016, 15:38 |
Isaac Earle | Development | Target 1 | Target | T1/T2 Beryllium Target Test Jig Fabrication Complete |
Fabrication of the T1/T2 beryllium target testing jig (TBP1721) was completed today by Dan MacDonald. With a target installed across the test ports, the inside volume pressurized with air to 103psi, and both ball valves closed, there was no noticeable drop in pressure over a 16 hour period. This result was deemed satisfactory for use of the jig for hydrostatic testing of new targets.
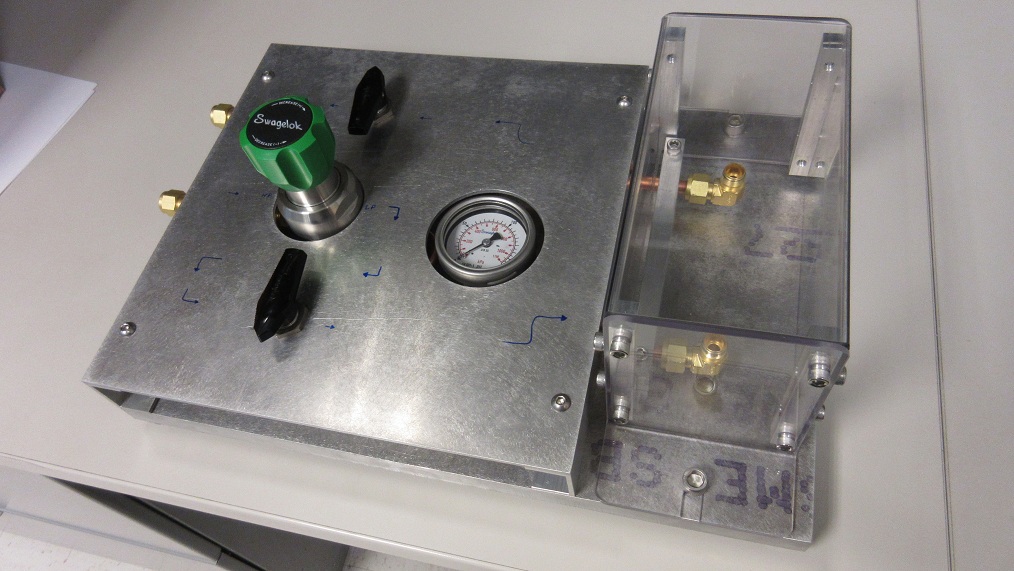
|
|
193
|
Thursday, March 31, 2016, 11:48 |
Isaac Earle | Standard Operation | Target 1 | Target | T1 & T2 Beryllium Target Manufacturing Complete |
Manufacturing of a new batch of T1 and T2 beryllium targets has been completed.
The job was completed under Machine Shop Work Order #41527. Eleven 12mm T1 targets (TBP1683) and seven 10cm T2 targets (TBP1691) were completed (exhausting all stock of the leftover EDM'd target housings). The target window profiles (TBP1695) were laser cut at an outside shop for greater precision and to save time. The target window assemblies were electron beam welded to the target housings (TBP1687 & TBP1692) by Bob Welbourn. The remainder of the tube welds were completed by George Sun. Assembly of the Swagelok fittings, target inspections, hydrostatic testing, and final helium leak checks as specified on the assembly drawings were performed by Isaac Earle. In addition to these tests, one spare target housing was pressure tested to 275psi (the max pressure of the regulator of target jig TBP1721). The target windows bulged at this pressure, but did not rupture.
The attached spreadsheet has details on target measurements and test results. The target serial numbers (listed in the spreadsheet) have been engraved on the 90 degree elbow of each target on both the entrance and exit side. Detailed photographs were taken of each target which are stored on Isaac Earle's hard drive (too large to attach).
If the 2015 target replacement plan is followed (See E-Log #168), these targets should last for at least 10 years.
|
Attachment 1: T1_T2_Be_Target_Documentation_(2016_Batch).xlsx
|
|
194
|
Thursday, April 07, 2016, 16:44 |
Isaac Earle | Development | Other | Controls | T1/T2 Controls "Assembly Tests" Completed |
The T1/T2 Control System "Assembly Tests" (Document 118467 Release #1, Section 5) have been completed. The expected result, as written in the document, occurred for every test. The T2 Shield Thermocouple #3 (B1A:T2:TC3SHLD:RDTEMP) showed slightly erratic behaviour when viewing archived data. It is uncertain at this point whether or not it will need to be bypassed in the B1A:T2:TGTRDY interlock.
The official commissioning tests (Section 6) are currently on-going. |
|
195
|
Monday, April 11, 2016, 13:51 |
Isaac Earle | Development | Other | Other | Target Transfer Flask Hoist Hook Lower Limit Adjusted |
The lower limit of the flask hoist hook has been adjusted. The travelling nut for the lower limit was rotated 3 notches closer to the upper limit travelling nut which resulted in an additional 1-3/8" travel of the hook at the lower limit. The door hinges and door cable pulleys were lubricated with WD-40 and actuation of the doors was tested several times. |
|
196
|
Monday, April 11, 2016, 13:54 |
Isaac Earle | Standard Operation | Target 2 | Target | T2-MK2 Target Transported from BL to HC |
The T2-MK2 target was transported from the beam line to the hot cell using the transfer flask. The target was measured to be 120mSv/hr at 0.5m. The steel shielding plug was installed in the T2 target hole to reduce upwards shine.
New beryllium target cassettes will be installed on the target ladder before it is returned to the beam line. |
|
197
|
Friday, April 15, 2016, 14:54 |
Isaac Earle | Standard Operation | Target 2 | Target | T2-MK2 Target Changes & Return to Beamline |
On April 11th the T2-MK2 target was flushed with water, then overnight with air at 5psi supply pressure. The target ladder was in Position 0 for this procedure.
On April 12th the target was pumped using a cold trap and the Varian leak detector for approximately 2 hours.
On April 13th pumping was restarted and the leak detector reached 0.0E-10 Torr*L/s with < 1.0E-3 Torr test port pressure. A general helium spray was performed with a small response to the mid 10^-9 range and quick recovery (this target was in use all of the 2015 running period w/o any vacuum issues). Plugs were removed from Positions 1 & 2. The swagelok threads on the ladder were cleaned with a wire brush then pressurized air. The sealing surfaces were cleaned using Scotchbrite then blown with air. Threads and sealing surfaces were inspected with the Nikon level: some minor thread imperfects on the threads and a few small pits on the sealing surfaces were observed. New 10cm beryllium targets were installed (Position 1: Target "OCT.06#3", Position 2: Target "#201"). A leak check was performed using 0.5s bursts of helium at supply pressure 3psi. Helium was applied at all target positions, delta seal locations, and along the length of both bellows. No responses observed that were greater than the initial leak check performed before the plugs were removed, therefore the target was deemed water leak tight and ready for use.
On April 14th position measurements for both new targets were taken as per Document-50194, which will be included in the target info sheet to be delivered to Operations.
On April 15th the target was returned to the beamline. All services were attached, the cooling package started, and vacuum pumped down normally.
Photographs of the Position 4 beam spots as well as the target ladder after new target installation are attached. |
Attachment 1: T2-MK2_Position_4_Entrance_Side_-_April_14_2016.JPG
|
|
Attachment 2: T2-MK2_Position_4_Exit_Side_-_April_14_2016.JPG
|
|
Attachment 3: IMG_7024.JPG
|
|
Attachment 4: IMG_7026.JPG
|
|
|
198
|
Wednesday, April 20, 2016, 10:01 |
Isaac Earle | Standard Operation | Target 1 | Target | T1/T2 Monitor Electrical Check Complete |
Mike Russell from Diagnostics Group has completed an electrical check on the T1 and T2 profile and protect monitors. He reports that both profile monitors look fine. The T1 protect monitor looks fine except for a weak or missing signal from the halo monitor. The T2 protect monitor looks fine.
Note: The protect monitor on the T1-MK2 target was working without issue during the previous running period and was not removed from the beam line during the 2016 shutdown. The cable for the T1 protect monitor was not disconnected during the 2016 shutdown. |
|
199
|
Friday, April 22, 2016, 14:45 |
Isaac Earle | Other | Other | Active Sump | RH MH Hot Cell Lab Active Sump Water Released |
The Remote Handling Hot Cell Lab Active Sump has been released to city sewer following the procedure in Document-64834. The water was close to the sump high limit switch (approximately 5800L). Before release the water was sampled, tested, and approved for release by RPG. The tritium analysis form has been filled out and returned to RPG,.
It took approximately 5 hours to empty the sump with all valves fully open and the water flowing through the 10" Cuno filter. |
|
200
|
Friday, May 13, 2016, 15:04 |
Isaac Earle | Standard Operation | Target 2 | Target | T2-MK2 Position 4 Adjusted to +1.5mm Offset |
The T2-MK2 target at Position 4 has been adjust to approximately +1.5mm offset. This causes the ladder to be moved downwards, raising the beam spot location on the target window. The potentiometer ratio at this offset is approximately 0.810 (> 0.8059 nominal ratio for position 4, and therefore closer to Position 5)
The purpose of the offset is to better center the beamspot on the target window. Target window photographs showed the beam spot being slightly below center (See E-Log #197), and target ladder elevations taken in Spring 2016 showed the Position 4 target approximately 1.0mm above the profile monitor center.
MCR has been instructed to continue running with this offset, and a message with details on how to do so was posted to their Plone site. |
|
201
|
Wednesday, June 15, 2016, 11:00 |
Isaac Earle | Standard Operation | Target 2 | Target | T2-MK2 Target Moved to Position #1 |
Position #4 on the T2-MK2 target has now reached the maximum beam time. The target was moved to Position #1 at the nominal elevation. This target should be used for the remainder of the 2016 running period. |
|
202
|
Tuesday, June 21, 2016, 09:25 |
Isaac Earle | Development | Other | Controls | T1/T2 EPICS System With-Beam Testing |
With-beam commissioning tests were completed today by Tony Tateyama and Isaac Earle. The test results are attached in PDF format. These tests are described in Section 7 of the Commissioning Plan (Document-118467 Release #2). These tests were not part of the official commissioning, but intended as an additional check of system functionality with beam on, and to confirm that the CCS current protection system performs as expected.
Official commissioning of the T1/T2 EPICS system was completed in April 2016, with the results released in Document-131503. |
Attachment 1: T1T2_EPICS_Section_7_Commissioning_Results.pdf
|
|
|
203
|
Tuesday, June 28, 2016, 08:32 |
Isaac Earle | Other | Other | Active Sump | RH MH Hot Cell Lab Active Sump Overflow |
A call was received from the MCR at approximately 21:30 on Monday June 27th to report that active drains in the east end of the Meson Hall were backing up and overflowing. I came in and found the leak coming from a broken spray nozzle in a sink in the rad waste area. The leak was stopped at which point there were puddles between 1-2m diameter around the active sump top flange, the drain directly south of the warm cell water windows, and the drain in the counting room south of the clean room. There was lots of water on the floor in the rad waste area as well. No water was found in the TR-13 area. A swipe was taken from the puddle around the active sump top flange, which was not above background level. Robin Swanson (ops) contacted Joe Mildenberger who gave permission for the sump to be pumped out after a water sample was taken. Robin took a water sample and left it for analysis by RPG, the sump pump was started and ran overnight. At approximately 8am the next morning the sump was almost empty and the pump was stopped. Floor swipes were taken where there had been puddles which were now dry - no contamination found. The areas in the hot cell lab which had been wet were mopped. |
|
204
|
Tuesday, June 28, 2016, 16:28 |
Isaac Earle | Other | Other | Active Sump | RH MH Hot Cell Lab Active Sump High Level Sensor Test |
The high level sensor for the Meson Hall Hot Cell Lab Active Sump was tested today and worked as expected. When the sensor is tilted (as occurs when the water level rises above it) an audible alarm sounds in the hot cell lab, and the Safety Panel in the MCR also alarms with "MHESA B1 RCR1 RM 6 WARN" displaying NOT OK. This alarm sounds every 3 minutes in the MCR until the PLC outside of the RCR lab is reset. When the sensor was tested on the RCR lab PLC there was a message indicating that the MH Hot Cell Lab Active Sump is full.
It is still unclear why the operators did not receive this alarm when the sump filled and overflowed last night (or possibly they did receive it, but it was ignored or silenced). The operators from that shift are currently off until this Saturday, so they will be contacted next week to try to learn more.
UPDATE (Sept 8, 2016): Further testing revealed that the electronics for the high level switch were wired incorrectly which resulted in the RCR PLC only seeing sump level high when the "silence" button on the electronics box for the switch was pushed. This was not discovered during previous tests because the "silence" button was pushed each time shortly after triggering the switch. The new electronics for the switch will address this issue. |
|
205
|
Wednesday, July 06, 2016, 13:31 |
Isaac Earle | Other | Other | Active Sump | Active Sump RCR Lab and MCR Alarms Not Working - Suspect Controls Issue |
Further tests were done on the active sump high level float switch today. The switch was triggered 1 time by filling the sump, and approximately 8 times by tilting the sensor manually. A local alarm sounded in the hot cell lab each time, but only one time in the RCR Lab and MCR (this occurred on the final trial). Fault report #9099 has been submitted to Controls Group. Although the existing float sensor did cause a local alarm when the sump was filled, it's operation did not seem ideal: it only triggered when completely horizontal, which wasn't until water was several inches above the base of the switch; in addition it appeared that it may be possible for the switch to become stuck under the horizontal portion of the sump (possibly even in an untriggered orientation). For these reasons a replacement level switch will also be investigated.
UPDATE (Sept 8, 2016): Further testing revealed that the electronics for the high level switch were wired incorrectly which resulted in the RCR PLC only seeing sump level high when the "silence" button on the electronics box for the switch was pushed. This was not discovered during previous tests because the "silence" button was pushed each time shortly after triggering the switch. The new electronics for the switch will address this issue. |
|
206
|
Tuesday, August 30, 2016, 14:09 |
Isaac Earle | Development | Other | Controls | T1/T2 PLC Code Update |
A new version of the T1/T2 PLC code has been uploaded to the PLC CPU. The main change in the new version is a fix to a bug related to the target MK# which may have caused the previous CPU crashes. The EPICS interface now needs to be updated so that no target information is displayed on the EPICS screens when there is no target installed, or jumpers for both MK1 and MK2 are detected. This must be tested during the next maintenance day. The appropriate tests are Section 6.4.1 Test #5 and #6 from Document #118467 |
|
207
|
Thursday, September 08, 2016, 17:26 |
Isaac Earle | Development | Other | Active Sump | New Active Sump High Level Switch and Electronics Installed |
To address the deficiencies identified in E-Logs #204 and #205 the old active sump high level switch was replaced with Omega LV164SS model (316SS stem and float, 4' length, standard mount) using adaptor flange TRH1316 to mount to the top flange of the sump. A new electrical box was also installed (circuit diagram attached in PDF format). The circuit was designed by Don Jackson and wired by Travis Cave. Connection to the RCR Lab PLC was done by Dave Morris.
The switch was tested using the following procedure:
1. The switch was triggered by submerging the base in water until the float lifted. This was confirmed to be equivalent to disconnecting the CPC-4 connector for the switch from the new electrical box
2. Switch connector disconnected: Local alarm sounds in HC Lab, red "Sump High" LED light illuminates, green "Sump Good" LED turns off, RCR PLC reports high level (cannot be reset), main control room "MHESA B1 RCR1 RM 6 WARN" displays NOT OK (this will sound every 3 minutes until the RCR PLC high level alarm is reset)
3. "Alarm Silence" button pressed on new electrical box: Local alarm stops, LEDs on electrical box do not change, RCR PLC still cannot be reset
4. Switch connector reconnected: "Sump High" LED turns off, "Sump Good" LED turns on, RCR PLC can be reset
5. Power to the electrical box removed by switching off the breaker: All LEDs turn off, no alarm, RCR PLC reports high level
Pump out of water from the MHESA Lab active sump to the HC Lab active sump was tested while observing the HC Lab sump. The water entering the HC lab sump did not splash on the new switch excessively, and did not cause any false alarms.
The new system will continue to be tested annually according to the calibration schedule.
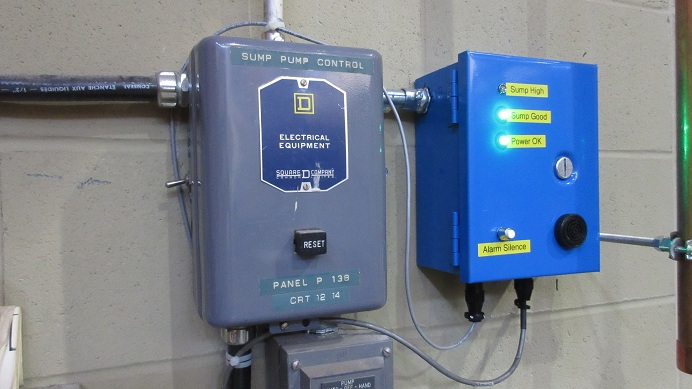
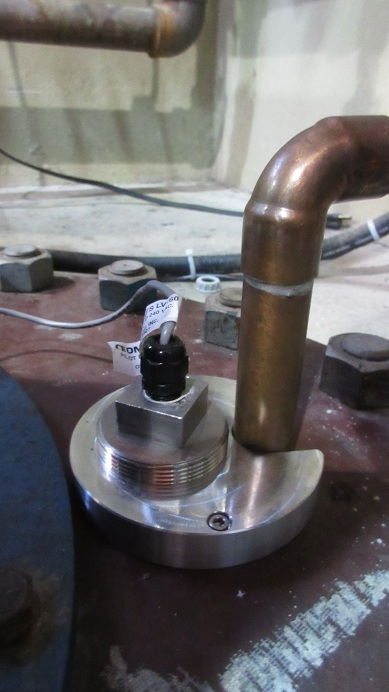
|
Attachment 3: RH_HC_Lab_Active_Sump_High_Level_Sensor_-_Electrical_Schematic.pdf
|
|