ID |
Date |
Author |
Category |
Type |
Specific |
Subject |
186
|
Monday, January 25, 2016, 16:54 |
Isaac Earle | Maintenance | Target 1 | Cooling | T1 MRO Work |
The following work was performed at the T1 cooling package and target between January 18-21, 2016:
- Cuno water filters removed (3), and new filters installed
- Target water solenoid, H.E. secondary side solenoid, and Collimator A solenoids removed and replaced with new 24V DC versions
- All thermistors removed and replaced with Type K thermocouples
- All Proteus paddle wheels, o-rings, and paddle wheel pins replaced (5 each)
- Target side #6 Hansen QD fittings replaced because internal seal had failed and fittings were leaking when disconnected (2)
- Profile monitor copper air supply line leak was repaired
- All air QD fittings (6 total) for profile monitor actuation were replaced, the air restricting valves were tuned, and the flexible hose assemblies were checked for gross air leaks
- "T8" temp sensor was found to be located on the CuALCW common return line, not on the Col A supply line as labeled on XTPAGE. Position was swapped
Total dose for this work was 0.17mSv for Isaac Earle, and 0.10mSv for Keith Ng |
276
|
Thursday, February 17, 2022, 13:03 |
Matthew Gareau | Maintenance | Target 1 | Target | T1 MK2 wire scanner and protect monitor test removal and reattachment with pin straightening |
this Work was done on 09 Dec 2021.
Since Isaac Earle was leaving Triumf he was giving us (maico, chad, adam, and myself) a demonstration of how to remove targets, protect monitor, and wire scanner. During the removal it was noticed that one of the pins for the wire scanner was bent and it would not be possible to reattach without straightening the pins.
Luckily the fields from the ladder were low enough (374 uSv/h) and we were able to retrieve the wire scanner and manually bend the pins back. The wire scanner was reattached without incident, and now will need diagnostics to check on the target ladder to ensure all is operational. |
Attachment 1: IMG_20211207_140443.jpg
|
|
Attachment 2: IMG_20211207_140508.jpg
|
|
Attachment 3: IMG_20211207_140735.jpg
|
|
Attachment 4: IMG_20211207_122631.jpg
|
|
Attachment 5: IMG_20211207_142836.jpg
|
|
26
|
Tuesday, April 03, 2012, 15:55 |
Isaac Earle | Maintenance | Target 1 | Target | T1 Ladder Position Look-up Tables Updated |
Graham Waters has activated the appropriate target ladder position look-up tables for the T1-MK1 target which was installed in the beam line yesterday. |
330
|
Tuesday, June 06, 2023, 15:42 |
Albert Kong | Standard Operation | Target 1 | Cooling | T1 Heat Exchanger Low Flow Diagnostics |
On May 31, the low active water in BL1A was turned off briefly and upon re-starting, the flow to the T1 heat exchanger was very close to the reported warn limit (~6 gpm).
To see if this low flow could be remedied, we entered the BL1A tunnels briefly on Jun 06 but found no flow regulator valves for the T1 heat exchanger.
The low flow to the heat exchanger after the secondary water pump was re-started may be a normal characteristic of the system. Alternatively, this may have been caused by entrapped air in the heat exhanger after it was drained during 2023 shutdown to replace a leaky valve.
The latter is grounded in the fact that the flow in T2 recovered immediately after the flow was re-started. T2 was drained through a drain line in the tunnels whereas T1 was drained at the cooling station through a filter/copper line.
The difference in draining methods may have resulted in entrapped air and thus flow issues in T1 but not T2.
|
Attachment 1: Picture1.png
|
|
Attachment 2: Picture2.png
|
|
216
|
Monday, March 27, 2017, 16:15 |
Isaac Earle | Repair | Target 1 | Cooling | T1 Cooling System Target Water Return Hose Damaged |
The 18' shielding block which lies west of the T1 cooling package was removed on Friday Mar 24 so that vacuum equipment could be craned into the 1A tunnel. During replacement, the flexible SS hose for T1 target return water got caught under the block and was ripped apart. Workers in the area did not realize this had occurred. The cooling package tripped off when the hose ripped (likely due to low water flow or low supply pressure). In total approximately 6.5L was lost which flowed to the 1A tunnel below. The hose connections at the target and cooling package do not appear to have sustained damage. Plans are under way for a replacement hose to be fabricated and installed.
Update March 30, 2017: The damaged hose has been replaced with a new 20' long braided SS hose with 3/4" male NPT fittings both ends. Both air supply lines for T1 profile monitor actuation (1/4" copper) were also damaged during the Mar 24 block move and they have now been replaced. All hoses, cables, etc on the west side of the T1 monolith have been re-routed or secured to reduce the chance of this happening again in the future.
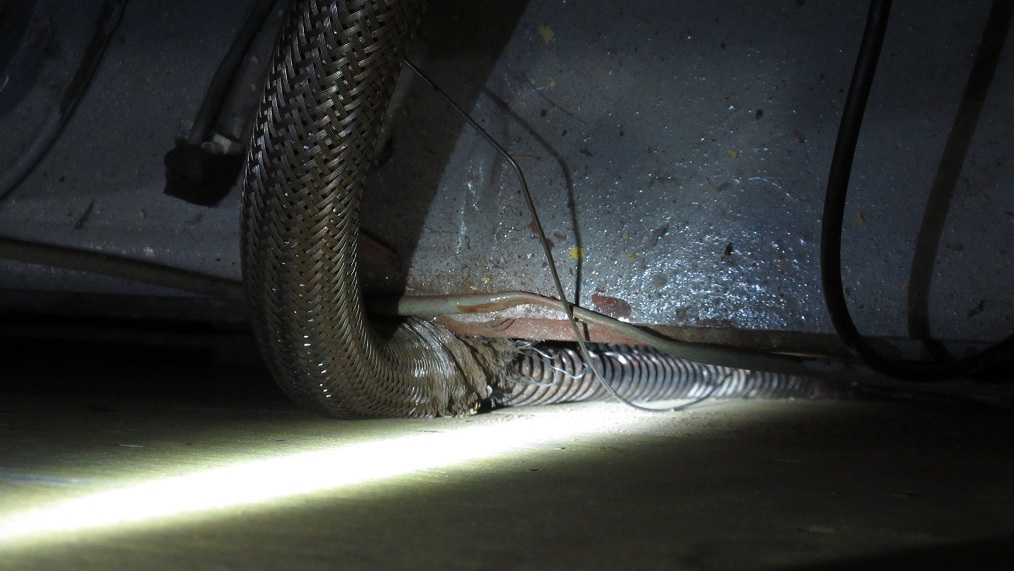
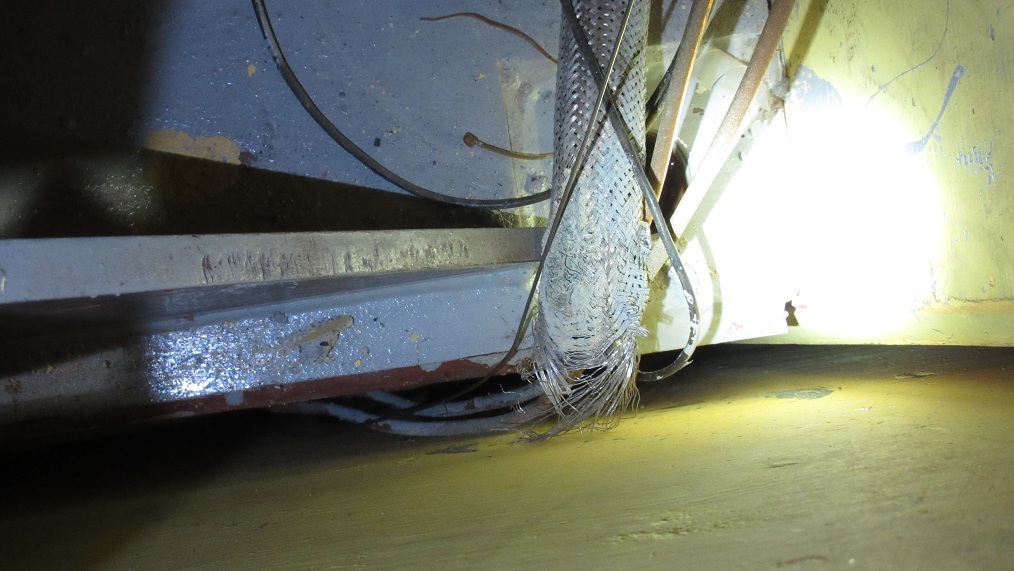
|
209
|
Friday, September 30, 2016, 16:59 |
Isaac Earle | Repair | Target 1 | Cooling | T1 Cooling System Inlet Pressure Transducer Replaced |
The T1 cooling system inlet pressure transducer (EPICS ID: B1A:T1CS:PGIN, Omega part # PX315-100GI) began failing in August (exhibited gradual decline in pressure with no corresponding change to flow rate or outlet pressure). A new transducer was installed on Sept 30 2016 which fixed the problem. Cyclotron Fault Report #9238 was returned and the temporary bypass on the warning level was removed. |
331
|
Tuesday, July 18, 2023, 09:14 |
Adam Newsome | Other | Target 1 | Cooling | T1 Cooling Package: target flow (FGTGT) sensor noise issues |
Between 1:00 pm and 6:00 pm on July 17, 2023, the T1 target cooling water flow rate sensor exhibited some noise which resulted in it dropping below the warning/trip limit. The control room requested that the threshold values be lowered - permission was granted. The thresholds were set to 2.3 gpm for both warn and trip levels. See attached screenshot from EPICS sensor data. The occasional spikes and dips continued throughout the night fairly consistently.
While the cooling water temperature (TCOUT) fluctuates, there does not seem to be an obvious correlation between the temperature and the flow rate, which suggests that the flow rate is still adequate.
It is worth noting that overall, the FGTGT signal has been slightly trending downward since around mid-July (see attached pic).
It is suggested to replace this sensor as soon as possible - perhaps the mini shutdown. |
Attachment 1: 1.PNG
|
|
Attachment 2: 2.PNG
|
|
315
|
Wednesday, February 01, 2023, 14:23 |
Albert Kong | Maintenance | Target 1 | Cooling | T1 Cooling Package: flow test after resin exchange / valve leak check / faulty(?) dial pressure gauge |
Maico/Eric/Albert:
The expansion tank in T1 was filled to ~36cm in the morning.
We contacted the control room to test flowrates in the T1 cooling loop after new installation of resin in the demineralizing line.
Epics interlocks tripped immediately as pump was turned on (flow too low or pressure to high) due to new resin.
Turning on the pump repeatedly extends the delay before system trips, until eventually the pump can run continuously.
Flowrate through demin line initially too high (~2.5 gpm), adjusted flow control valve to bring it to ~1.4 gpm (setpoint at the time ~0.4-1.5 gpm).
When the pump was turned on initially, saw physical pressure gauge (dial type) bottom out/make greater than 1 full rotation (>50 Psi).
No connection between the physical dial to EPICS so no cause for immediate concern.
All valves are more leaky than when the pumps are off - leaks definitely not due to depressurization.
Attached: photo of the likely 'faulty' dial pressure gauge.
|
Attachment 1: IMG_1038.JPEG
|
|
317
|
Thursday, February 02, 2023, 15:14 |
Albert Kong | Maintenance | Target 1 | Cooling | T1 Cooling Package: Leaked Valve Inspection |
A 0.75" SwageLok ball valve that was taken out from the T1 cooling package was inspected (SS-45S12).
All valves in the T1/T2 cooling packages likely leaked due to damage to plastic/rubber sealing components.
SEE PICTURES ATTACHED.
We can see that some bits of white plastic, possibly a bushing, has disintegrated and is leaking out from the valve shaft.
Additionally, there is a considerable amount of dirt/grit in and around the ball.
The surface of the valve opening exibits visible signs of wear (new valve opening is perfectly smooth).
Finally, a red-colored material is found on some small stainless steel parts which is either buildup from contaminants in the line or worn silicon/rubber lining.
Hypothesis: 90 um filter which had not been replaced caused the water in the line to build up particulates and wear plastic/rubber parts in the valve, causing them to leak.
From the previous test (ELOG 315), we know that the leak is not due to depressurization. |
Attachment 1: CompiledPictures.pdf
|
|
112
|
Thursday, April 03, 2014, 16:35 |
Isaac Earle | Standard Operation | Target 1 | Cooling | T1 Cooling Package Started |
The T1 cooling package was started around 2pm today. There was no change to the T1 volume vacuum during startup.
The package was inspected for water leaks: None found.
The demin loop flow (Q2) was adjusted to ~1.5gpm.
The target out water resistivity has reached 12 mega-ohm-centimeters after approximately 2.5 hours, indicating that the resin does not need to be changed. |
310
|
Monday, January 16, 2023, 15:01 |
Adam Newsome | Maintenance | Target 1 | Cooling | T1 Cooling Package MRO - 2023 Shutdown |
T1 Cooling Package MRO began Jan. 16, 2023.
The following maintenance tasks have been completed for T1 (this list will be updated as work progresses):
- Drained water
- Hansen fittings o-rings inspected: OK
- Replaced demineralizing flow metering valve (part number SS-8BK*)... this part was replaced because the equivalent part on T2 exhibited potential signs of wear during 2022 and was replaced in 2022 mini-shutdown (October). There are two things to note about this part: 1) when loosening it, it makes an audible *click* at some point during loosening rather than a smooth continuous feeling like the new replacement part, and 2) it appears to have originally been installed backwards in terms of the flow rate direction arrow. It is now installed correctly.
- Demineralizing resin can - exchanged with fresh resin (2023-01-18... dose rate of old resin which is currently located in the warm cell is approximately 40 uSv/h on contact)
- Replaced filters:
- Target water CUNO filter (it was relatively clean)
- M15 CUNO filter (it was relatively clean)
- Demineralizing 90 micron filter (it was very dirty with tiny pieces of debris)
- Replaced leaky valves (see e-log 318 and 320)
- Refilled expansion tank water (see e-log 321)
- Tuned demin flow rate to 1.1 gpm, turned on pump [2023-03-06], confirmed system functionality (all sensors OK, no water leaks observed). See screenshot attached of T1 state at approximately 4:00pm on 2023-03-06 after the system had been running for a significant time.
As of now, the cooling system is ready for beam. Prior to beam-on, actuation tests of key items such as the target ladder and beam blocker need to be performed. It is expected that this will be done within the next 1-2 weeks. |
Attachment 1: T1_2023-03-06.PNG
|
|
85
|
Friday, August 23, 2013, 10:39 |
Isaac Earle | Repair | Target 1 | Cooling | T1 Cooling Package Inlet Pressure (P1) Sensor |
The T1 cooling package inlet pressure (P1) has been dropping since approximately May 5, 2013 from the regular operating pressure of approximately 75psi to the present value of 47psi. An increase in the rate of decrease started around August 5th as well as increased noise in the signal. Plots attached below. No corresponding change in the outlet pressure, and no change in the water flow rate (also no change in inlet and oulet temperatures) leads to the conclusion that the transducer is failing or gas is trapped in the lines leading to the transducers in the BL1A tunnel.
Jamie Cessford and Ron Kuramoto are aware of the situation. The issue will be addressed during the September mini-shutdown.
.jpg?lb=RH-Meson+Hall&thumb=1)
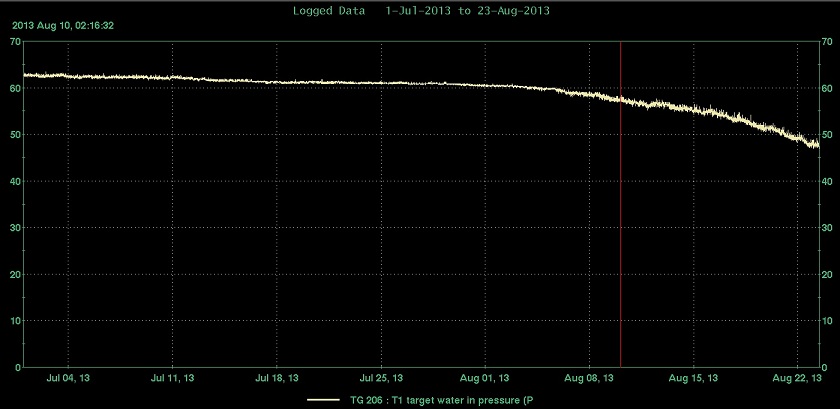
|
316
|
Thursday, February 02, 2023, 10:35 |
Albert Kong | Maintenance | Target 1 | Cooling | T1 Cooling Package Draining (Prep for Valve Replacement) |
Water reservoir in T1 started draining at ~7.30 am, will leave till tomorrow or overnight to fully drain.
(Preparation to replace all leaky valves).
Drained water samples collected for RPG. |
138
|
Tuesday, January 27, 2015, 17:38 |
Isaac Earle | Repair | Target 1 | Cooling | T1 Cooling Package 3/4" Valves Rebuilt - T1 MRO Complete |
- Both 3/4" ball valves on the T1 cooling package target water circuit were rebuilt, leak tested with house air pressure, and reinstalled
- The 3/4" ball valve on the T1 heat exchanger secondary side was replaced with a new unit
- The 3/4" needle valve on the T1 heat exchanger secondary side was rebuilt, leak tested with house air pressure, and reinstalled
- The T1 cooling package was refilled and restarted using a bypass across the inlet/outlet Hansen fittings
- The package was inspected while running and no leaks were visible (video survey taken with file stored on Isaac's PC)
- All T1 Cooling Package MRO activities are now complete |
20
|
Tuesday, March 20, 2012, 10:31 |
Isaac Earle | Repair | Target 1 | Cooling | T1 Cooling Package - Potential Water Leak |
The T1 expansion tank warning level sensor had tripped and the level was approximately 1cm from the base of the tank. No trip warning was observed when Tom Lyth checked the panels last week. The T1 cooling package and target monolith were inspected and no water was observed. Two puddles of water were found in the BL1A tunnel around the T1 package area: one directly below the 1AQ9 Cable Interlock Tray, and another approximately 1.5m to the west. However, water was observed in the same area when the tunnel was accessed in January. The T1 volume is currently vented, so there is no indication from the vacuum system as to whether or not water has leaked into the beamline.
The tank was refilled, and the level had not changed after 1 hour. I will continue to monitor the level. |
78
|
Friday, April 12, 2013, 17:33 |
Isaac Earle | Development | Target 1 | Cooling | T1 & T2 high-temp limit switch installation, wiring, and commissioning complete |
Installation, wiring, and commissioning of the high temperature limit switches for the T1 and T2 cooling packages was completed today as part of SAS project SASP0120. The relay output from the switches was wired in series with the Central Safety System signals for T1 and T2 (cable number 13250 and 12250 respectively) in break-out panel #2 on the Meson Hall south mezzanine. There were already 3 other circuits wired in series with each signal for various other interlock requirements.
After wiring, commissioning of the switches was performed according to the following procedure:
- With the limit switches in a non-tripped state, it was confirmed that the safety signals were reaching the CSS in the main control room as expected (had to jumper T2 circuit to achieve this as the T2 target is not currently installed)
- The limit switch was tripped by adjusting the set point on the switch, it was confirmed that the signal was lost
- The set point was changed to a non-trip level, and the switch trip cleared, confirmed that the signal in MCR returned
- The enable signal from each cooling package was removed by shutting off the cooling package (for T2 just removed jumper), confirmed that safety signal lost as expected
- Reversed this condition and confirmed that the signal returned
- Checked that the thermocouples are performing properly, and the switches actually trip on high temperature by directly applying heat to the thermocouple area on the cooling package using a heat gun; the switches tripped as expected when the set-points were exceeded
The results were discussed with John Drozdoff (Safety Systems group leader) who approved the method.
The final task remaining for SASP0120 is to route the PRV outlets to the 1A tunnel active drain using flexible hosing.
|
256
|
Wednesday, February 05, 2020, 14:53 |
Isaac Earle | Maintenance | Target 1 | Cooling | T1 & T2 cooling package MRO work completed |
Annual MRO work on the T1 and T2 cooling packages is now complete. The following tasks were performed:
- Water from both packages drained to the South TNF holding tank (samples taken)
- All Proteus paddle wheels, shafts, and o-rings replaced (5 each at T1 and T2)
- All Cuno filters changed
- Archived data for all sensor readbacks inspected. Only faulty sensor was B1A:T1CS:FGDEM
- Both packages refilled and restarted; Operating smoothly; Inspected for leaks, none found; Demin flow at ~1.0gpm
- B1A:T1CS:FGDEM readback is fixed with new paddle wheel
- South TNF holding tank water released after approval from RPG
- Old filters added to plastic pail with other T1/T2 filters located directly north of the BL1A blocks boot-box area
- Active water from filter canisters dumped into the RH lab active sink
|
160
|
Tuesday, May 12, 2015, 21:20 |
Grant Minor | Standard Operation | Target 1 | Target | T1 & T2 Targets moved from pos. 0 to pos. 4 |
Grant moved the T1 and T2 targets from position 0 to position 4 this evening at around 9pm.
The position 4 selector button on the T1 rack was not working. The manual control box had to be used with the adapter cable and military connectors for both T1 and T2 to achieve position 4 on both targets. |
45
|
Tuesday, June 26, 2012, 09:05 |
Isaac Earle | Maintenance | Target 1 | Cooling | T1 & T2 Target Water Flow Transducers Serviced |
The target water outlet flow transducers on the T1 and T2 cooling packages were serviced (new shaft, paddle wheel, & o-ring) to address a noisy signal. The service corrected the noisy signal. Additionally, it appears the worn parts were causing the transducers to read high, as both dropped approximately 1 gallon/minute after the service. Both transducers would occasionally trip the high flow warning (8.5gpm), and should now no longer do so.
A plot of the water outlet flows before and after the service is attached. Cyclotron fault report #6086 was returned. |
Attachment 1: T1_&_T2_water_flow.jpg
|
|
142
|
Friday, February 20, 2015, 13:55 |
Isaac Earle | Standard Operation | Target 2 | Target | T1 & T2 Target Moves |
- The T1-MK1 target was moved from the hot cell to storage pit hole #3 (ready as T1 spare)
- The T2-MK2 target was moved from the beam line to the hot cell for inspection and in preparation for T2/M9 work this shutdown
- The target measured up to 90mSv/hr at approximately 1m while being lifted
- Beam spots on the target will be measured and recorded to determine ideal offset (if any) for next running period
- A 10mSv/hr collimated field was measured coming from the T2 monolith hole
- An aluminum blank-off was installed over the hole followed by a stack of circular steel discs for shielding which reduced the max field in the area to 700uSv/hr |