Thursday, May 01, 2025, 09:33, Travis Cave, ITE, Standard Operation, TM4, UC#48, Module move
|
TM#4 with UC#48 went from the conditioning station to the east target station. |
Wednesday, June 18, 2025, 09:28, Travis Cave, Conditioning Station, Standard Operation, TM4, C#5, Module move
|
TM#4 with C#5 moved from the NHC to the conditioning station. |
Thursday, June 19, 2025, 11:22, Travis Cave, Spent Target Vault, Standard Operation, , UC#48, Spent Target Move
|
The spent UC#48 target was removed from the North Hot Cell, place in pail#303 and put into vault spot 2C, it was 35.4mSV/hr when removed from the NHC. See attached PDF for vault details. |
Monday, July 28, 2014, 17:26, Ron Kuramoto, ITW, Repair, , , ITW:IV5 Air leak repair  
|
Air leak was found at the Solenoid control valve located in the Pre-Separator & DB0 room. The gasket between the solenoid body and its manifold block was broken, see attached photos. The gasket and solenoid body were replaced. Air was turned back on to IV5 (B/L gate valve) with no apparent air leaks. The gate valve was actuated open & closed from the control room seeing both limits successfully.
Repair was done by Dimo Y. who received 0.01 mSv, and assisted by Anthony I. & Ron K. who both received zero dose.
Rad fields measured by RPG were; 1300 uSv/hr above B/L and 350 uSv/hr @ the Solenoid valves at knee height.
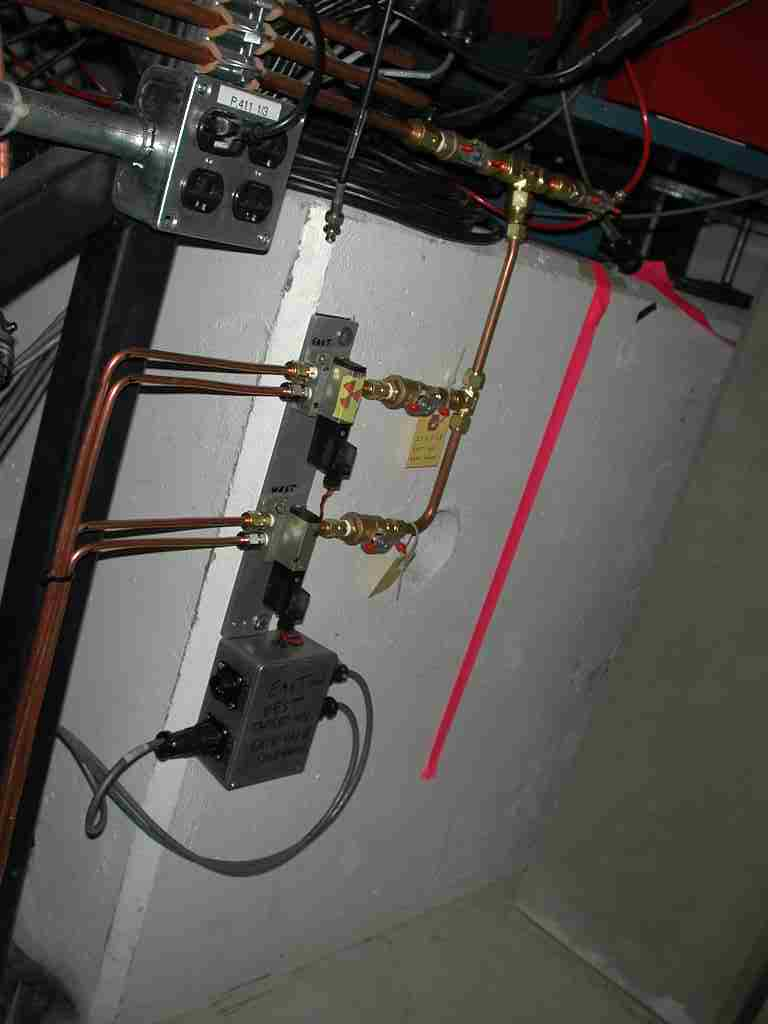
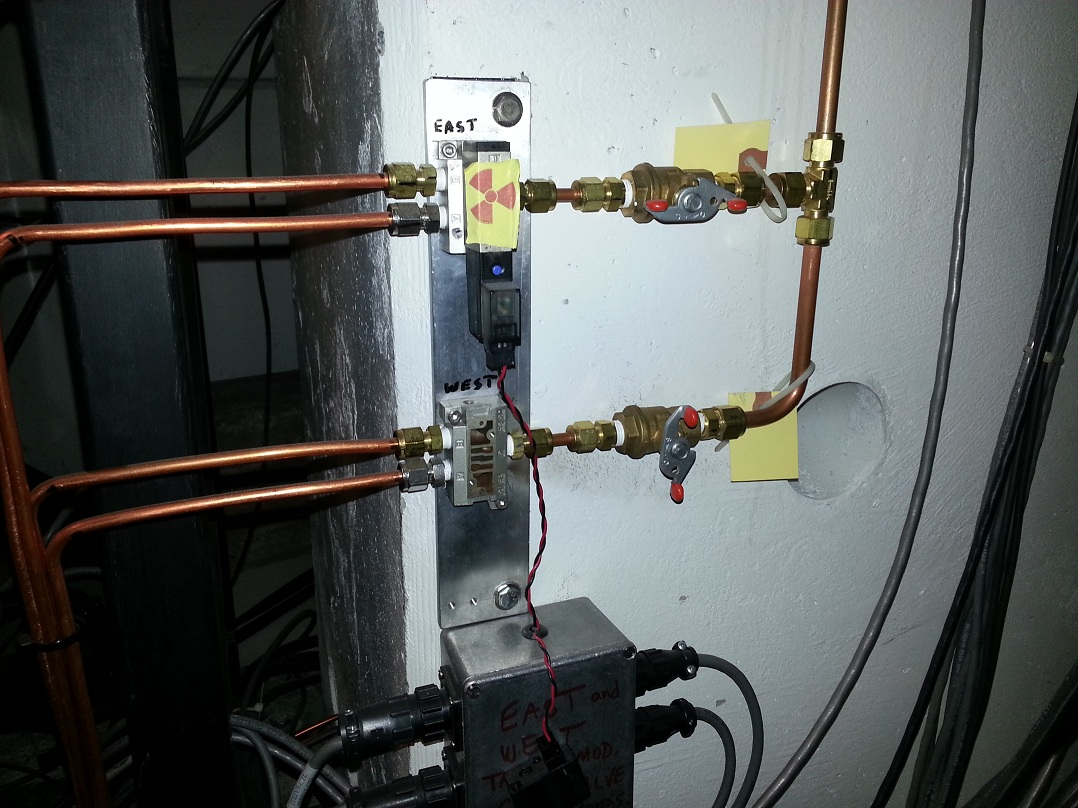
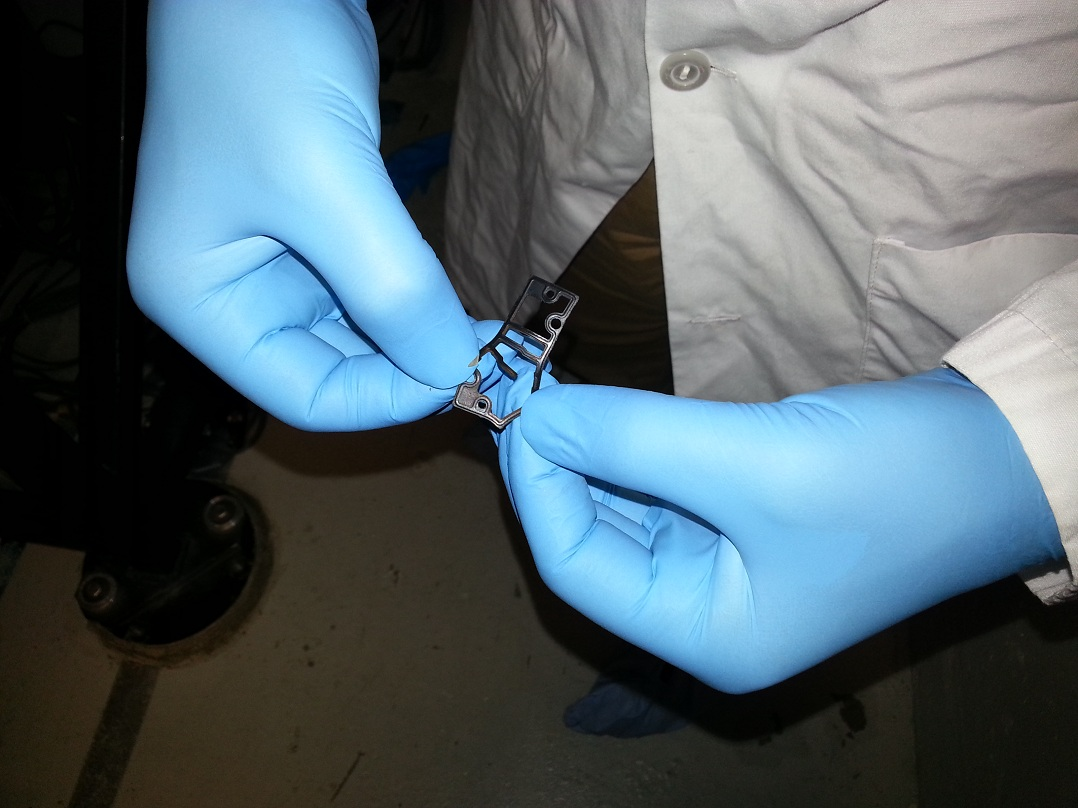
|
Thursday, May 09, 2024, 13:52, Riley Sykes, Waste Package/Ship, Standard Operation, , , F308 Service/Inspection
|
F308 Inspection and service complete on #06, #08, #13, #15, #16, #19, #20, #21, #22.
All in good condition with new gasket material installed on #20.
Prepped for move to ISAC B3 for storage. |
Wednesday, July 10, 2024, 10:44, Riley Sykes, South Hot-Cell, Maintenance, , , Spring idler install 
|
New spring idlers were installed onto rotational chain drive for SHC roof. Operation ran smoothly in both directions to full limit. Chain was noted to have adequate slack when not on driven side. Periodic checks to confirm operation will continue in the following months to guarantee proper operation. |
Friday, July 12, 2024, 08:51, Riley Sykes, Safe Module Parking, Maintenance, , , SMP chain guard
|
SS washers were added to all slotted holes on SMP chainguard cover plate |
Thursday, June 30, 2011, 16:04, Pierre Bricault, Conditioning Station, Repair, TM1, , TM1 status
|
Friday June 24 2011
The target module has been moved to the Conditioning Station (CS)
Pumping overnight
Saturday June 25 2011
Pressure Service Cap (SC) 3E-6 T
Pressure Containment Box (CB) 6.6E-6 T
High voltage test to 40 kV, unfortunately, the pressure is not great so we stop at 40 kV
Pressure at the end of the day: 1650H was, P SC 2.6E-6T
P CB 6.6E-6 T
Sunday June 26 2011
Pressure P SC 1.6E-6T
P CB 6.6E-6 T
It seems we have a leak. The pressure does not drop in the CB over one day.
Today June 27 2011
Pressure P SC 1.2E-6T
P CB 6.6E-6 T
We leak check the target module and found two leaks, one on the ground electrode and one on the mounting plate cooling circuit.
This is a new one. We had test this line three times before and it was ok.
Action for tomorrow.
After CS vent,
Move TM1 to SHC
Survey
Connect LD to Mounting plate cooling circuit
Open Side panel and leak check.
Meeting at 0830H |
Tuesday, August 02, 2011, 09:41, Pierre Bricault, Conditioning Station, Repair, TM1, ITW-TM1-Ta#37-LP-SIS, Test high voltage on TM1
|
TM1 has received the Ta#37-LP and has been pumping since thursday. This morning the pressure gauges read, IMG1: 1.6x10^-6 T and IG1: 7.4x10^-7 T.
The high voltage power supply has been connected to all high voltage feedthroughs and the voltage raise to 42 kV.
High voltage conditioning started around 20 kV and after few minutes we were able to go up to 40 kV.
The pressure increases on both locations, IG1 went up to 8.1x10^-7T and IMG1 went up to 1.8x10^-6T.
The module is good to go. |
Monday, April 04, 2022, 10:44, Nadia Jorgenson, South Hot-Cell, Repair, , , Turntable Chain Repair 
|
Last week we repaired the South Hot Cell turntable chain/sprocket. Chain was loose and there was a few section where the chain was not lining up properly with the sprockets.
3 issues were discovered:
- One of the pins was bent. It’s been replaced but is a temporary fix. Need to replace them with stronger pins.
- The smaller sprockets near the motor were too far from the main turntable sprocket which was causing the links to not immediately line up with the teeth on the turntable sprocket. With too much slack in the chain, it’s likely that this is were the misalignment was starting. This was fixed by adjusting the motor position and the position of the yellow plate bolted to the floor.
- The yellow plate that is bolted into the floor has oversized holes relative to the bolts/washers used. This allows us to adjust the position, but the washers are to thin and are being bent/pulled into the holes. Should be replaced with thicker washers that can withstand the tension and this will help prevent the plate from sliding out of position. |
Wednesday, May 11, 2022, 16:15, Nadia Jorgenson, Spent Target Vault, Standard Operation, , , Emergency Close Mechanism Test
|
The emergency close mechanism for the Storage Vault door was tested by Travis Cave, Nadia Jorgenson, and Dan McDonald. The door was opened to its fully open limit, then closed with the emergency system.
The test was successful. |
Wednesday, May 11, 2022, 16:29, Nadia Jorgenson, Spent Target Vault, Standard Operation, , , Routine mechanical inspection: storage vault
|
An inspection was performed on drive systems for the main storage vault by Dan McDonald, Travis Cave and Nadia Jorgenson. The functionality was not tested. Some areas for improvement noted, but otherwise nothing concerning was discovered.
Notes:
-
The wire insulation to the motor is showing wear and tear. Should be replaced in the future. For now was patched with electrical tape, see picture. May be beneficial to add an e-chain for the portion of the wiring that moves when door is opening and closing
-
Emergency close mechanism cable should be changed to have a 5/32” Nico Sleeve
-
Moving parts still need to be lubricated
-
Chain inspected (OK)
-
Gearbox inspected - OK
-
All drive system set screws checked and tightened
-
Sprocket alignment checked - OK
-
Limit switches checked - OK
-
Emergency close mechanism cable checked - OK
|
Wednesday, May 25, 2022, 10:23, Nadia Jorgenson, Spent Target Vault, Repair, , , F-308 Loading, Mini-Storage Vault Failure
|
5 pails were moved from the mini-storage vault into F-308's
At one point during the loading the mini-storage vault door would not close. Cause was a blown fuse, which was replaced and operations were able to continue as usual. Possible reason the fuse blow was a tilted pail that may have become jammed between the tray and the roof of the mini-storage vault.
[Edit 2022-12-01, Adam Newsome]: the pails which were removed were: 220, 227, 233, 235, 238 |
Thursday, June 30, 2022, 14:28, Nadia Jorgenson, Safe Module Parking, Standard Operation, , , Annual Inspection of Safe Module Parking - Electrical
|
An annual electrical inspection was performed on the SMP today by Travis Cave and Nadia Jorgenson as per Work Permit I2022-06-30-2. The following items were checked:
Electrical Inspection of Safe Module Parking:
- Check condition of wiring for physical/radiation/UV damage
- Check for cable tray debris or damage
- Some objects stored in the cable tray but nothing concerning, no damage noted
- Check inside control panel: components and wiring, labeling
- Labeling intact, components in good condition
- Wiring in good condition
- Verify camera views
- Check connectors for damage
- Check pendant for damage and verify labeling intact
- Lid open/close test
- Lid was opened and close multiple times - smooth operation, no concern
- Lid close logic was checked - OK
- Vessel rotation and limit switch check
- Centre, CW and CCW limits were checked, functioning
Still to be done – Mechanical Inspection:
- Lubricate chains
- Inspect tensioners
- Tighten fasteners
- Inspect components during rotation - chain drive, rotary limit switch, and cable reel etc.
|
Monday, July 04, 2022, 11:44, Nadia Jorgenson, Safe Module Parking, Standard Operation, , , Annual Inspection of Safe Module Parking - Mechanical  
|
An annual mechanical inspection was performed on the SMP today by Dan McDonald and Nadia Jorgenson. The following items were checked:
- Lubricate chains
- Inspect tensioners
- Tighten fasteners
- A few slightly loose, most are in need of washers, see attached pictures
- Could use some shims in a few places, see attached picture
- Inspect components during rotation - chain drive, rotary limit switch, and cable reel etc.
|
Monday, July 04, 2022, 11:54, Nadia Jorgenson, Spent Target Vault, Maintenance, , , Added Lubrication,fittings need to be changed
|
Dan lubricated components on the target storage vault (This was an outstand task from annual inspection). No issues on the main storage vault but we were not able to lubricate the mini storage vault because the position of the grease nipple on the fittings makes them inaccessible, see attached pictures. All four should be replaced with 90 deg fittings. |
Friday, March 27, 2020, 08:45, Matthew Gareau, North Hot-Cell, Maintenance, , , Issues with the manipulators
|
This is a link to all of the issues with the NHC manipulators that I know of
https://documents.triumf.ca/docushare/dsweb/View/Collection-27663/Document-180176
|
Tuesday, October 27, 2020, 11:46, Matthew Gareau, North Hot-Cell, Repair, , , Ratcheting repair issues with both left and right master
|
The were issues with both left and right master ratcheting;
- the left handle was getting stuck in a close position when there was a higher ratcheting tension added
- the right ratcheting was not tightening preventing proper use of the manipulator
Chad and myself were able to identify a missing set screw for the tong cable.
Once this was added the issue with the left master ratcheting seems to be solved.
Lubricant was added to the left master ratchet and this seems to solve this problem as well.
There was also an observation of missing set screws on the spare manipulator for attaching the wrist to the ratcheting handle, which will need to be ordered and attached.
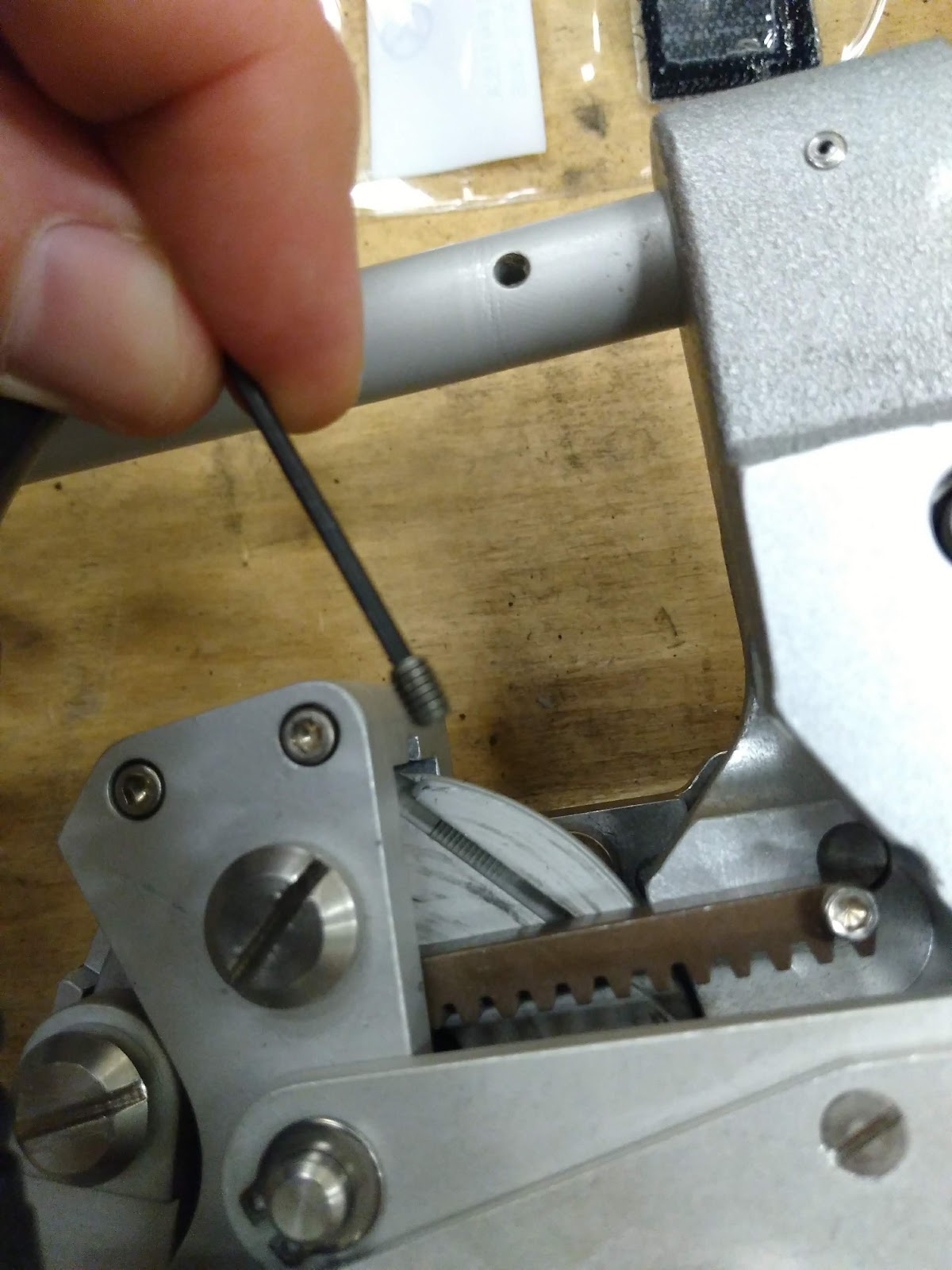
|
Thursday, December 24, 2020, 09:00, Matthew Gareau, North Hot-Cell, Development, , , NHC USB connection
|
24/Noc/2020
USB was discovered to be in the reverse direction and will need to be change around to become operational
01/Dec/2020
USB was pulled from conduit
While attempting to re-pull the USB in the correction direction, the ethernet cable was damaged and need to be replaced,
(thanks to the Hubert's team for the wire help)
It was decided that it was too problematic to re-pull the wires with all other wires in the way. Therefore all the wires were removed from the operator control panel, and pulled so that the USB, USB power cord, and ethernet could be re-pulled all together.
However, even once all the wires were re-pulled and reconnected it was discovered that the USB had become damaged, and was removed again.
23/Dec/2020
- A new conduit was added through to the NHC, for only the USB
- USB was fed through, reconnected, and tested
- Putty will need to be added around the conduit to ensure a good seal into NHC |
Friday, March 05, 2021, 09:12, Matthew Gareau, North Hot-Cell, Development, TM3, , Containment box door removal and swivel arm test
|
First thing I entered into the NHC to install to the target kart mounting clip, and remove excess tools and materials from the hotcell
After the TM3 without a target was lowered into the NHC.
Once inside, with the use of the manipulators, I was able to remove the containment box door, place it on the swivel arm, move the arm out of the way, after the door was return to the containment box and reattached.
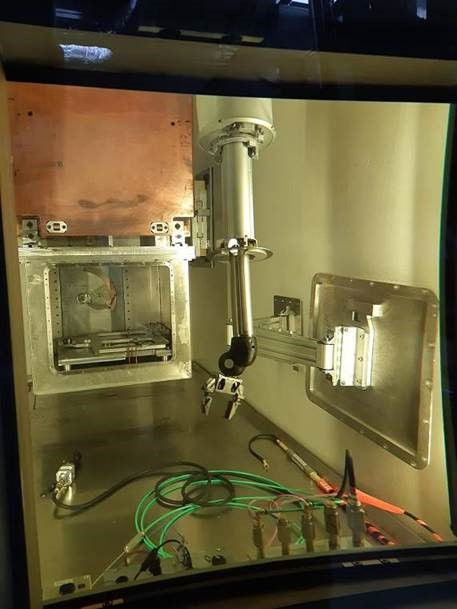
|
|