Tuesday, January 02, 2024, 15:58 :
Started HV ramp up on TM3 service tray about 3pm today. Had to bypass TCS:BIAS interlocks to make it work - there are some flow restrictions on the water lines that are causing the flow interlock to periodically trigger. The water flow it not very important for this test as long as the water is moving. Turned out that it was also conveninent to have all the interlocks bypassed because sparks tripped off the IG1 gauge and this did not cause the HV bias supply to turn off. Should use same setup next time.
Some sparking around 35-44kV, tripped off turbos/IG1/IG1S 3 times and so decided to ramp down.
Tried again while standing outside TH door to hear if sparking is outside the vacuum. Went to 48kV very slowy with multiple trips of the turbos, mostly TP2. Lots of sparks but easy to ramp back up to previous high point, so likely just a painful conditioning process. Current draw 167uA at 48kV. No sparks audible outside door, and vacuum response looks too large to be electrical noise.
Continued on Wednesday January 03 - went up to 53kV in the same way as before, lots of TP2 trips making its current a bit unstable... data was dumped as TM3_servicetray_conditioning_jan32023. Tried limiting the current on the power supply to very near the drain current to see if that reduces the number of trips. Didn't notice a significant effect.
Thursday, January 04, 2024, 09:57 :
Restarting conditioning, starting at 180uA at 53kV. Got up to around 60kV with many trips of the turbos, and one restart of the IG1 controller needed. Added a grounding hook to the vacuum controller rack to see if that helps reduce the trips. (doesnt appear to have).
Friday, January 05, 2024, 09:51 :
Continuing conditioning. Starting by sitting at 50kV for 10mins. No sparks observed during this time.
Even though we got to 60kV last time, onset of conditioning started at 58.6kV with a trip at 58.9kV... got up to 70kV.
Got to 72kV on Monday January 08 2024.
On Monday Jan. 15, tried to improve the grounding on the vacuum services rack to reduce sparking through the turbo controllers. Added two welding cables from the vacuum rack ground busbar to the copper grounding strip on the ground. If the spark is travelling from the faraday cage to the rack through conduit or grounding cables, maybe this will help. If it is coming through the turbo cable then it likely won't. Tried to add grounding straps on the turbo controller chassis (there is a brass screw which I think is for this purpose) but couldn't get either of the screws out with any resonable force. They undo a bit then get stuck...
Wednesday, January 17, 2024, 20:39:
David vented TM3 with N, then opened the service cap to install new insulators. We pumped back down and Alexander and I ramped back up today - instabilities started around 55kV and we were back to slow conditioning in the high 50s. Got up to a set point of 65kV. Ray did some work on the TCS bias supply and now neither the set point or readback is correct. The PSU was reading 51.5kV at set point 50kV and 60kV at set point 58kV. Will continue later...
Wednesday, January 31, 2024, 16:23
Ramped up again, some slight instabiities around 56kV but could still go up pretty quick until about 65kV. Since Ray's testing of the TCS:BIAS supply both the readback and the set point are off from the powersupply display. Ran out of time and ramped down at set point 70.5.
Set point |
Readback |
PSU reading |
63 |
64 |
65.5 |
66.5 |
67.5? |
68 |
69.5 |
70.6 |
71.5 |
70.5 |
71.7 |
73 |
|
|
|
|
|
|
Tuesday, February 06, 2024, 14:47
Testing again after venting the module with air. First tiny spark at 48, then some vacuum reactions starting at 49 but still no issues. Bit more reactive around 53.
Set point |
Read back |
PSU reading |
53 |
53883 |
55 |
57 |
57924 |
59 |
60 |
61 |
62 |
64 |
65 |
66.5 |
|
|
|
stopped at 69.4
Wednesday, February 07, 2024, 15:28 :
Ramped easily to 60kV set point and let it sit there. Didn't spark at all then after 100mins, sparked TP2 off. Otherwise first sparking happened at set point 67.
Found at limit at around 72.5 on the PSU front output, set point 70.6. think it comes from EPICS. Will have to test the power supply.... stopped there.
Thursday, February 08, 2024, 15:03 :
Long term testing. ramped back up, first spark at set point 65.
Let it sit for 2hrs 20mins. Something like 6 sparks during this time. Current also dropped significantly from 0.32A to 0.27A.
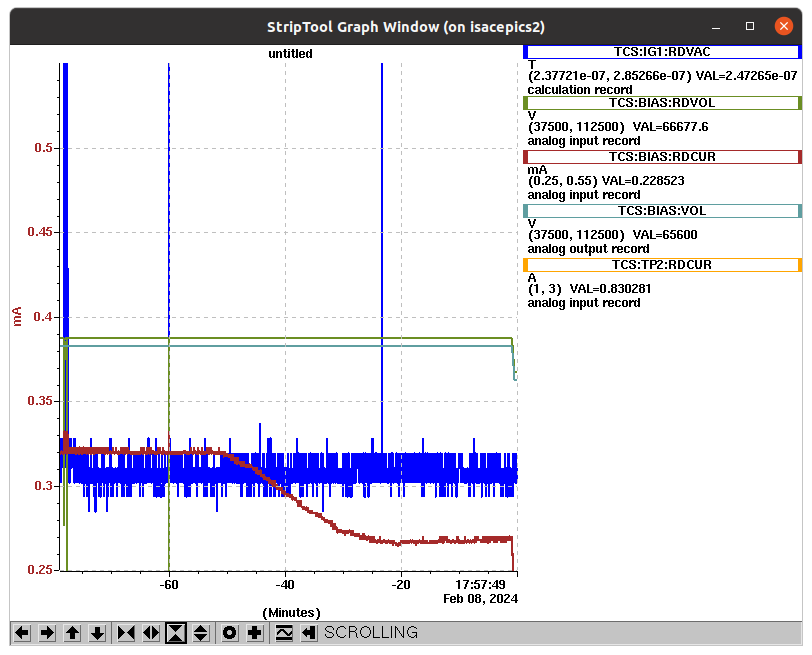
EDIT 2024-11-25, Alexander Shkuratoff:
All the StripTool data related to the above tests are on the server as the following below. Those without "Alexander" in the name were dumped by Carla.
And the StripTool settings:
|