ID |
Date |
Author |
Category |
Type |
Module |
Target/Number |
Subject |
1839
|
Monday, December 10, 2018, 15:31 |
Isaac Earle | North Hot-Cell | Development | | | NHC remote connection testing with manipulators |
The following tests have been successfully completed using the NHC manipulators:
- Ventilation pre-filter (mounted on the NHC/TCS partition wall) removed and re-installed using the manipulators
- Electrical plugs (two total) for operator-level LED lighting located on east wall of cell interior plugged in, and un-plugged using the manipulators
- Electrical plug inserted into and removed from each of the 120V outlets (four total) located in front of the viewing window using the manipulators
- All diagnostic service connections removed and reinstalled using the manipulators (six total, see IRH1765)
- All Staubli air and gas connections removed and reinstalled using the manipulators (five total, see IRH1749)
These tests were performed at various different times over the last several months by Isaac Earle and/or Chad Fisher. |
1841
|
Tuesday, December 18, 2018, 11:13 |
Isaac Earle | North Hot-Cell | Development | | | NHC manipulator slave-end swap, RH test, and various other work |
The following North Hot Cell work was completed over the last week under work permit I2018-12-12-1:
Thurs Dec 13th:
- Prepared master side according to removal manual (noticed screwing in the right side locking screw was not as smooth to go in as normal; left side was smooth like normal)
- Removed manipulator roof block and set down in yellow frame (required some stacked wood to prevent light from bottoming out)
- Removed steel side plates in NHC manipulator hatch
- Removed the slave end (SN: 9764) – noticed “Right Elevation/Twist Coupler” off of vertical by around 30 degrees
- Wrist elevation of removed slave end was not locked, lifted it slightly and this brought the coupler to the vertical position and it locked with a click
- Suspected the thru-tube also would be misaligned, confirmed by inspecting visually in hot cell (Unsure why this misalignment occurred considering we followed the removal procedure properly. One theory is that when we accidentally left the timing screw in the master side handle cable drum last time it may have caused things to get a little out of alignment)
Friday Dec 14th:
- Un-did the right side locking screw on the master
- Then could turn coupler on the thru-tube to the vertical position from within the hot cell
- Re-locked the right side locking screw (this time it went in smoothly)
- With all couplers on thru-tube vertical we then installed the replacement slave (SN: 9352) as per instructions
- For future slave end changes should use some sort of long chain or sling instead of having the auxiliary crane hook block within the hatch (some sort of T-hook type lift feature replacing the bail may work better as well)
- Evaluated the manipulator: seemed to be working normally, Chad tested plugged in LED lamp plug and also opened and closed the work table hatch
- Noticed Z motion tape on slave end loose when fully extended in Z (nice and tight when retracted) – this seems to be normal
- Confirmed manipulators can reach all surfaces of the table
- Then tested remote handling of LED light fixtures from the Target Hall using pole tools through the manipulator roof hatch
- Started with both LED light plugs un-plugged
- Used 9’ standard beam lines RH pole tool (this worked fine, but 10-12’ would be better)
- Curved hook end attachment
- First lifted cables out of all cable tray sections (the wall mounted Panduit)
- Then removed the East light fixture assembly (IRH1800) - lifted from designated lift loop (IRH1796) – This went smoothly
- Hoisted up into the Target Hall, then lowered back down to re-install
- To reinstall had to hook the assembly at a lower point due to flex of the pole from the weight of the assembly (hooked just below the ballast for installation). Using this method reinstalling the fixture went smoothly. I will update the design to move the designated lift point (or add an additional one) at this location.
- Once the light fixture was on the bracket, replaced the cables in the cable tray using the pole tool. The final section on the east wall before the outlets was a little tricky, but by viewing and reaching from the north-west corner of the hatch it was do-able
- Confirmed visually that remote removal and installation of the west fixture can be done using the same procedure as the east
- Replaced lamp block (stored lifting hardware for hatch side plates above block, below hatch cover)
Monday Dec 17th:
- Left side slave-end boot was installed as per manual instructions. It was done with two people inside the cell this time which went much smoother than just one last time (the boot was not installed on the slave prior to moving it into the hot cell because we wanted to inspect the tape and cables after installation and the boot would prevent that)
- The condition of both boots was checked. Both appear to be in new condition with no signs of degradation. The material seems pliable and strong.
- Chad Fisher, ISAC Hot Cell Operator, checked the light level from the cold side of the hot cell and confirmed that it is acceptable. However, without the operator level LED lighting it was too dim.
Tuesday Dec 18th:
- Lift bails for both manipulator slave ends set to farthest north position which results in face that mates with thru-tube to be close to vertical when hanging from lift bail
- Work table, stairs, entrance floor area, pre-filter assembly, tool port, window cover, and hot side service connection panel vacuumed and wet wiped to remove dirt and dust.
- NHC inlet damper (located in Target Hall) adjusted to set NHC depression to around 1.05”wc (the NHC damper is currently not responding to the NVCS and needs to be investigated and repaired by Controls Group and/or Mechanical Services)
|
1842
|
Wednesday, December 19, 2018, 14:41 |
Anders Mjos | Conditioning Station | Standard Operation | | No target | Installed Shield Block on TCS |
Frank and Anders installed lid on TCS and started vacuum system yesterday. To run over the Holidays. Retrieved dose badge from operational storage area. Measured field to be ~ 10 mSv/h at ~9am. Beam went off about 8:30am. |
1843
|
Wednesday, January 02, 2019, 10:26 |
Anders Mjos | Conditioning Station | Standard Operation | | | Restarrted TP1S |
Found pumps off after the holidays. Restarted roughing pump and TP1S |
1844
|
Thursday, January 03, 2019, 13:30 |
David Wang | ITW | Repair | | | ITH:MP1 |
ITH:MP1 inlet pressure showed 10torr after power outage during holiday. All ITE/W turbo-pumps were tripped because of it. Removed one shielding block above the vacuum station. Visually checked oil level and condition in pump. oil level is high. oil color is dark. no oil leak . Installed a local convectron gauge on pump inlet. After pumping down, It shows pump is good. Tightened all KF 25 and 50 clamps on pump inlet side. Reconnected pump to system. Everything works fine so far. All ITW / E turbo pumps are started now. |
1845
|
Thursday, January 03, 2019, 13:41 |
David Wang | Crane | Repair | | | Target hall crane PLC issue. |
Target hall crane did not work properly after power outage during Christmas time. The only movement could be operated is crane rotation. Power is supplied crane. The control board on N-S, E-W and up-down movement showed F51 error code which is tripped limit.. All these clues pointed to a PLC control problem. Don dale was asked for help. He used the crane control PLC program on an old computer in RH control room reset the PLC system. Everything works fine after his reset. |
1847
|
Friday, January 04, 2019, 14:38 |
Isaac Earle | North Hot-Cell | Development | | | NHC cameras tested |
The NHC module support flange cameras (4 total) as well as the NHCSA camera were tested today and confirmed to be working properly. All cameras were angled and focused properly, and displaying clearly on the monitors in the ISAC RH Control Room. Photos of the control room monitors are attached below.
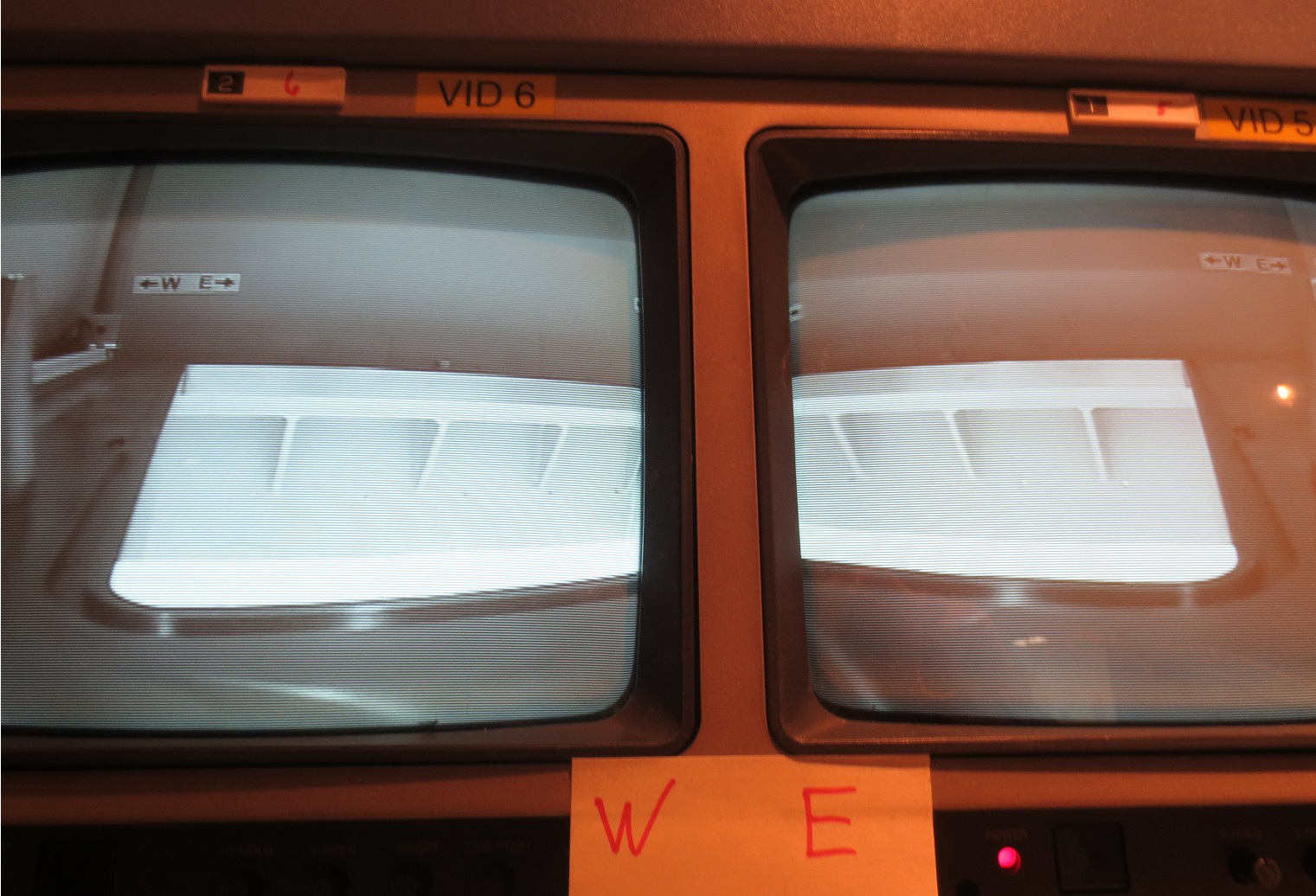
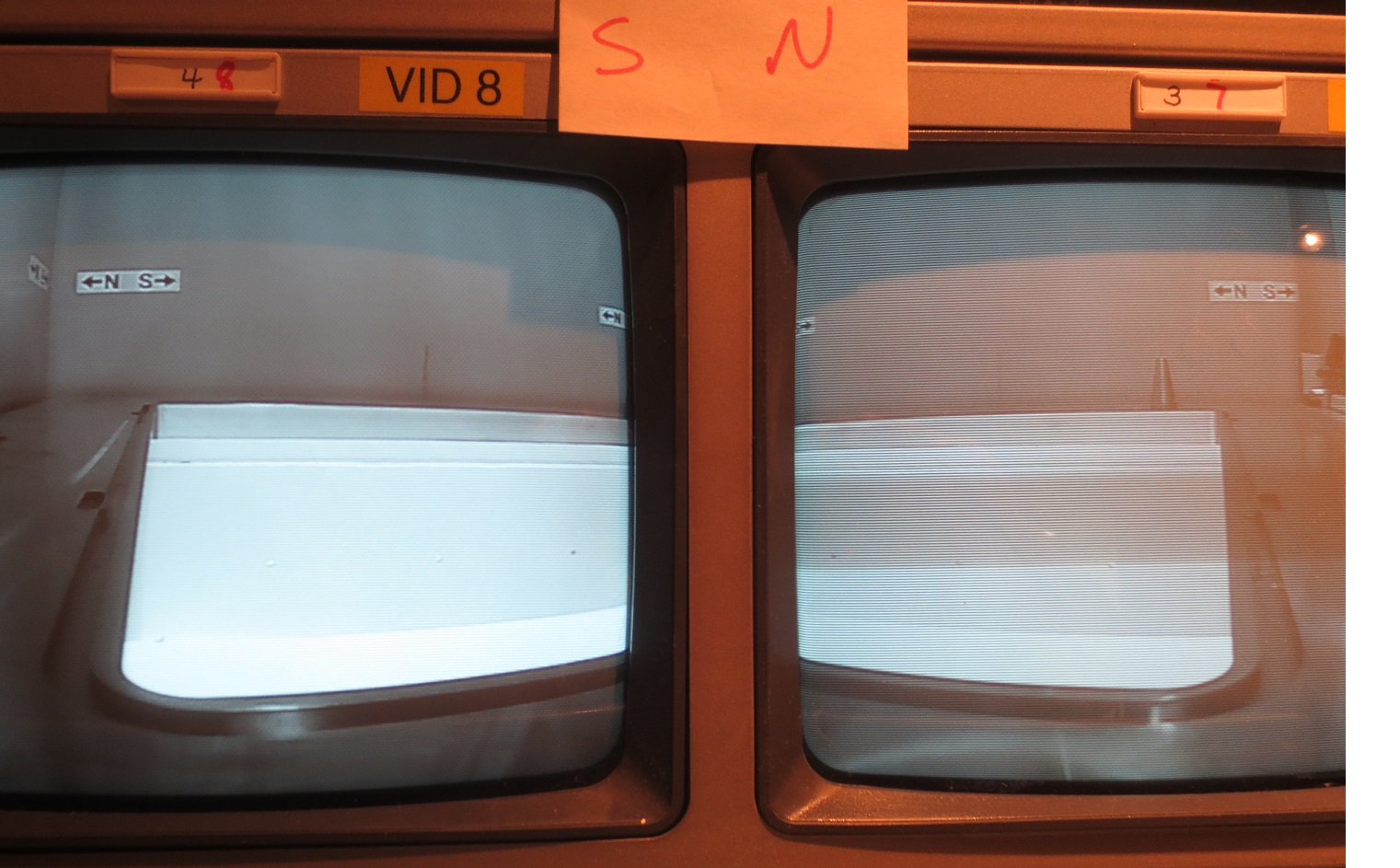
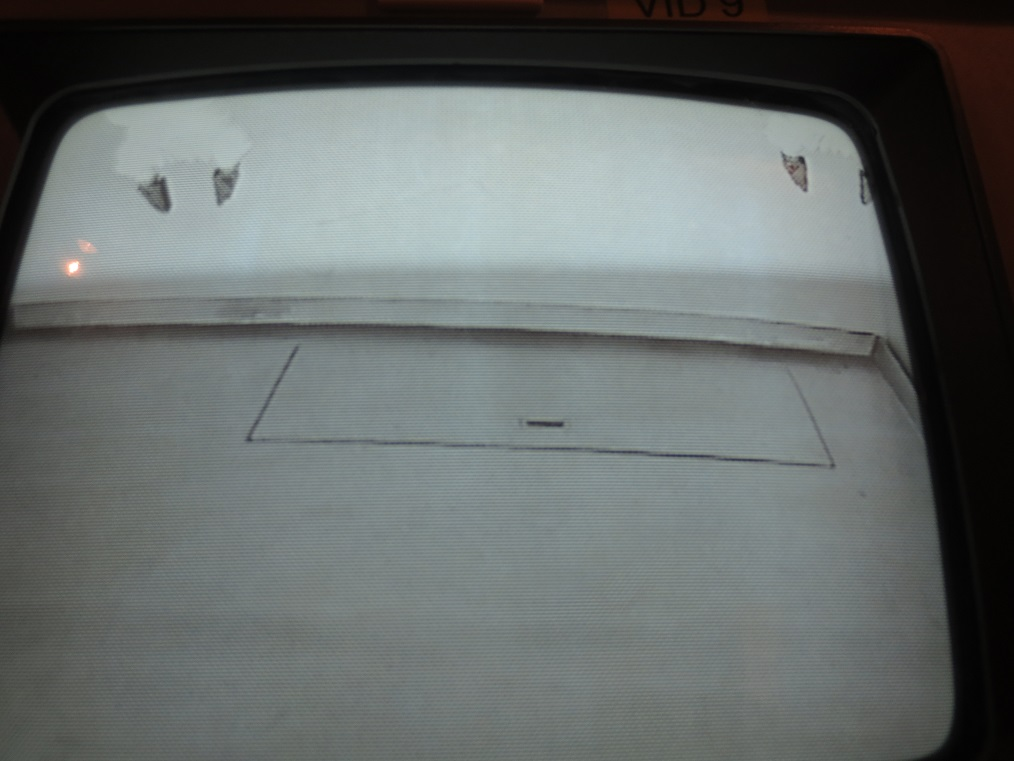 |
1849
|
Wednesday, January 09, 2019, 06:26 |
David Wang | Conditioning Station | Standard Operation | | | TCS vacuum pumps have been stopped. |
The tCS will be vented soon for TM2 move later this week. |
1852
|
Wednesday, January 09, 2019, 13:29 |
David Wang | ITW | Repair | | | ITH:MP1 |
ITH: MP1 has been replaced due to its poor performance. Its motor and power cable are taken out and reused on new pump. Vacuum group assembled them together, and installed the new pump. The new pump works fine. |
1855
|
Friday, January 11, 2019, 11:26 |
Travis Cave | Spent Target Vault | Standard Operation | | UC#25 | Spent Target Move |
The spent target in the south hot cell has been moved to the spent target vault. It was placed in pail 204 and placed in spot 6B. The pail is made of thicker steel and thus will not need to be repackaged later. The ISAC spent target vault is full there is no more room for any more targets. |
Attachment 1: Target_Index_2019-01-11.pdf
|
|
1857
|
Friday, January 11, 2019, 13:59 |
Isaac Earle | Safe Module Parking | Development | | | SMP motor selection decision |
SMP drivetrain design work is currently underway. Alejandro has selected a suitable 1200:1 reducer which will give a vessel rotation speed of 0.21rpm with a 1725rpm motor (deemed sufficiently close to the SHC rotation speed of 0.17rpm). The reducer however is only rated for 0.33hp, and Allon's analysis recommended we use a motor of at least 0.4hp
From his calculations the expected power required to turn the loaded vessel is 0.2hp (see Document-161943, p3). The higher figure of 0.4hp in his final recommendations comes from the power rating of a 40 tooth sprocket (the driver sprocket) with a No. 50 roller chain operating at 10rpm (the lowest speed shown on the table) - meaning this driver sprocket arrangement can handle up to 0.4hp. We discussed this on the phone on January 4th and agreed that a 1/3hp motor could be used which will match the reducer Alejandro selected, and will supply sufficient power given that calculations indicate only 0.2hp is required.
Once the vessel is installed in the shield box a test will be performed to determine the actual torque (and power) required to turn the vessel. If the value differs significantly from the calculated value the design will be revisited. |
1859
|
Friday, January 18, 2019, 10:26 |
Isaac Earle | North Hot-Cell | Development | | | NHC sealing improvements and repeat of RH test for LED lights |
The following NHC development work was completed under WP I2019-01-09-4:
- Location of RH feature on operator level LED lighting updated to match IRH1800 Rev B design
- Remote Handling test of the LED fixtures was repeated using a 9' pole with hook attachment through the manipulator slave hatch from the Target Hall: both LED fixtures were removed and reinstalled successfully with relative ease
- Tool port seal replaced to address an audible air leak: the 1/4" foam seal was removed and replaced with adhesive backed 5/8" wide hollow foam rubber seal (McMaster Carr PN: 93085K81). Prior to the change DPG4 was at 0.63"wc, after the change wit was 0.73"wc with all system variables constant.
- NHC manipulator access block seal was replaced, likewise to address an audible air leak: the 1/4" foam seal was removed and replaced with adhesive backed 1/2" thick BunA-N rubber strip (McMaster Carr PN: 9023K85). DPG4 was at 0.94"wc prior to the change, and 1.07"wc after with all system variables constant
|
1860
|
Monday, January 21, 2019, 16:27 |
Isaac Earle | North Hot-Cell | Development | | | NHC in-cell camera wired to right side monitor |
The NHC right side monitor has been wired to display the signal from the in-cell camera. This was tested using a snake camera on both of the CPC-4 connectors.
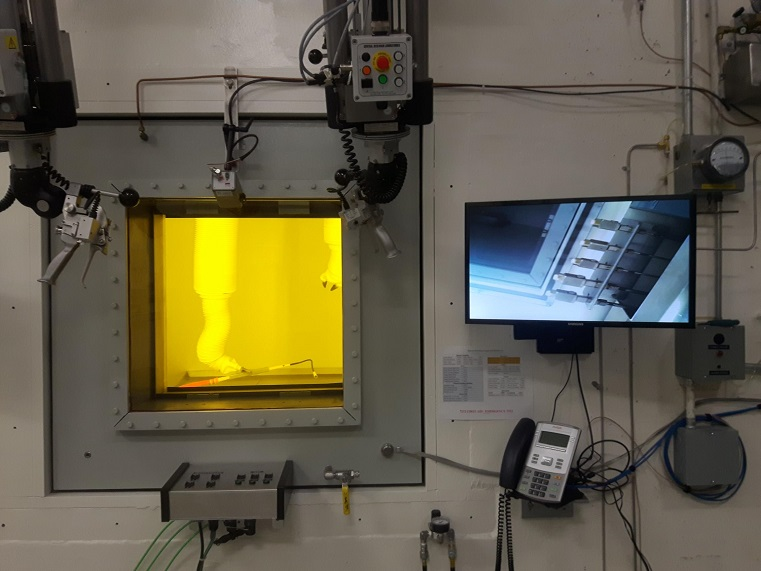
|
1862
|
Thursday, January 24, 2019, 10:34 |
David Wang | ITW | Maintenance | | | Changed 24VDC plugs of TP solenoid valves in ITW |
3 damaged 24VDC plugs of TP solenoid valves are replaced. Inspected other plugs. All of them are in good condition now. |
1864
|
Thursday, January 31, 2019, 14:16 |
Isaac Earle | North Hot-Cell | Development | | | NHC grounding approval |
Franco Mammarella was consulted regarding electrical grounding of the NHC design (RS103 of Document-131915). After discussing the design, and having grounding inspected by Randy Boehm, Franco approved the design and advised that the grounding system should be inspected periodically. This task has been added to the Remote Handling inspection index on an annual schedule. A PDF copy of the e-mail correspondence with Franco is attached. |
Attachment 1: NHC_grounding.pdf
|
|
1865
|
Monday, February 11, 2019, 10:26 |
Isaac Earle | Safe Module Parking | Development | | | SMP shield box and vacuum vessel moved to Target Hall |
On February 8th the SMP shield box (IRH1675) and the vacuum vessel (IRH1806) were both raised from a horizontal to vertical orientation in the ISAC-1 Experimental Hall. Hamilton "Mini-Mite" S-MM2-43FS caster wheels were then installed on the base of the shield box and it was lowered down the hatch to the B2 level. The vacuum vessel was then lowered into the shield box, supported by the rollers, as designed. The shield box and vessel combination were then moved south along the steel plated floor until positioned under the hatch leading to the Target Hall. Movement along the floor was achieved by pushing the back of the vessel with an electric fork truck and pulling from the front with a cable winch attached to a plate mounted in the floor in the SHC service area, centered east/west between the Ante Room doors. The fork truck alone was sufficient to move the assembly on the smooth section of the plates, but the winch was needed on the section paitned with textured grit. The vacuum vessel was then lifted into the Target Hall and placed in a temporary storage location in the silo area. The shield box was then lifted, casters removed, and then lifted up into the Target Hall. It was a very tight fit with the tubing which has been installed on the SHC and NHC ducting for the new flow meters, but the move was completed without causing damage. The shield box was placed on the B2 level in the Target Hall where some final tapped holes will be added on the exterior before moving to the final installation location.
|
Attachment 1: 20190208_091133.jpg
|
|
Attachment 2: 20190208_095126.jpg
|
|
Attachment 3: 20190208_105902.jpg
|
|
Attachment 4: 20190208_112619.jpg
|
|
Attachment 5: 20190208_113012.jpg
|
|
Attachment 6: 20190208_114833.jpg
|
|
1873
|
Thursday, February 21, 2019, 15:10 |
Isaac Earle | Safe Module Parking | Development | | | Seismic requirements for SMP |
Dragan Mitrovic, TRIUMF structural engineer, was consulted earlier this week regarding seismic requirements for the SMP assembly. Installation location, overall dimensions, total weight, and the center of mass for assembly IRH1670 were provided to him by e-mail. On Feb 20th he communicated verbally that he had analyzed the assembly for seismic loads, and concluded that this equipment does not require anchoring or any other form of seismic restraint.
Update (May 30, 2019): Confirmed with Dragan that the approach he used for analysis was that specified in the BC Building Code (both 2012 edition and updated 2018 edition). |
1880
|
Friday, March 01, 2019, 10:23 |
Travis Cave | Spent Target Vault | Standard Operation | | | Source tray moved |
The old TM#2 source tray and TM#4 optics tray have been removed from the vault and placed into the spent target storage on tray 9 which is meant for source trays. |
1882
|
Tuesday, March 05, 2019, 09:38 |
chad fisher | South Hot-Cell | Repair | | | Transfer Fixture Repair |
Transfer fixture has been remotely disassembled to the point where the ball nut lock plate assembly can be inserted into the tool port and the plate replaced by hand in the tool port without having to enter the hot cell. Straight head screws will be replaced with SHCS to facilitate easier re-assembly and future disassembly. |
Attachment 1: 20190305_092228.jpg
|
|
Attachment 2: 20190305_092231.jpg
|
|
Attachment 3: 20190305_092326.jpg
|
|
Attachment 4: 20190305_092558.jpg
|
|
1883
|
Tuesday, March 05, 2019, 14:29 |
chad fisher | South Hot-Cell | Repair | | | Tray Transfer Fixture Repair Complete |
Repair of the tray transfer fixture is complete (minus testing).
A distorted ball nut lock plate was replaced and thread loc added. to the ball nut/plate assembly. Testing will take place tomorrow once the thread lock has a chance to cure. |
Attachment 1: 20190305_130312.jpg
|
|
Attachment 2: 20190305_132303.jpg
|
|
Attachment 3: 20190305_133800.jpg
|
|
Attachment 4: 20190305_141346.jpg
|
|