ID |
Date |
Author |
Category |
Type |
Module |
Target/Number |
Subject |
1950
|
Monday, July 15, 2019, 13:29 |
David Wang | Conditioning Station | Development | TM4 | | Vacuum surge when TM4 B line iwas supplied with water. |
Yesterday, TM4 B line was supplied with water at TCS for testing. TCS: IG1 and IG2 had big response on it. See attachment. The water was disconnected right away, and line was purged. Vacuum recovered after overnight pump. |
Attachment 1: vacuum_surge_on_B_line_with_water.png
|
|
1953
|
Friday, July 26, 2019, 11:28 |
David Wang | South Hot-Cell | Standard Operation | TM4 | | TM4 move from SHC to TCS. |
Tm4 has been moved from SHc to TCS without containment box. It is a new source tray on TM4. A layer of plastic sheet was put on TH floor on module pass route during the move. |
1954
|
Friday, July 26, 2019, 11:41 |
David Wang | South Hot-Cell | Standard Operation | TM4 | | TM4 with spare target electrical check and leak check. |
Electrical check on TM4 with spare test target. PQ is still shorted to RU. But, The short between 60KV bias and PQRU which we found last time is gone. Target to PQRU at 250V mega measurement: 22.08 M. All conductivity between ABCD are about 5.0 m ohm which are good. All other ohm meter and Mega measurements are OL. Helium spray leak check on HS target VCR fittings is passed. Two blank offs are installed on source tray window cool lines. They passed leak checked at SHC as well. |
1955
|
Friday, July 26, 2019, 15:43 |
Isaac Earle | Safe Module Parking | Development | | | SMP vacuum control system completed |
The SMP vacuum control system has been wired and setup to be controlled from EPICS. Backing valve control (SMP:BV1) was tested by connecting to the turbo pump solenoid on TM3 located in the silo directly north of the SMP. The SMP pump (SMP:MP1) was turned on and off through the EPICS interface and responded as expected. Both convectron gauges (SMP:CG1 and SMP:CG2) responded as expected when the pump was turned on. The readings from the two gauges were consistent throughout the mili-Torr range.
The work was done by Ray Mendoza under WP I2019-07-24-4 (work request #5239).
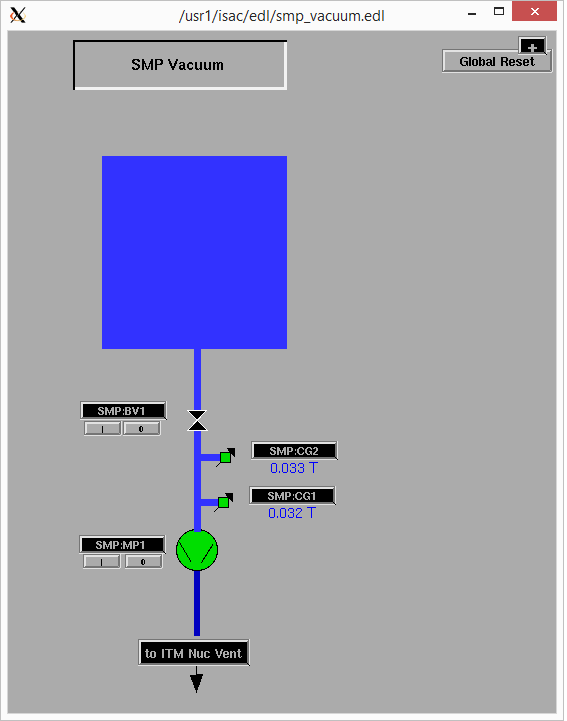
|
1961
|
Wednesday, August 14, 2019, 08:55 |
David Wang | ITE | Standard Operation | TM2 | | TM2 has been disconnected in ITE. |
TM2 has been disconnected in ITE. The bias jumper between U and T was burned out during the last beam time. |
1966
|
Friday, August 16, 2019, 08:51 |
David Wang | Conditioning Station | Repair | TM4 | | TM4 waterlines helium pressure test at TCS. |
LD base leak rate, 0.0Xe-9atm.cc/sec. Helium pressure, 70psi. 5 minutes each circuit. No response on all water line except containment box window which has a VCR leak issue now. Window line leak rate, 2.3Xe-4 atm.cc/sec. |
1967
|
Friday, August 16, 2019, 08:52 |
David Wang | Conditioning Station | Standard Operation | TM4 | | TM4 is moved from TCS to SW silo. |
TM4 is moved from TCS to SW silo this morning. The move is good. |
1970
|
Friday, August 23, 2019, 14:27 |
Isaac Earle | Safe Module Parking | Development | | | SMP camera video cabling installed and tested |
Installation of the video lines for the SMP cameras was completed yesterday according to IRH1670 Rev B. All four cameras were confirmed to be displaying properly in the crane control room. The cameras are powered from an outlet wired to circuit 35/37 on Panel #443 (located in the NHCSA). This is independent from the power supply for other existing camera systems in the Target Hall. The SMP turntable was rotated through the full range of motion (reached CW and CCW limits) and the cable routing and reel take-up system performed as expected. |
1971
|
Tuesday, August 27, 2019, 13:12 |
Adam Newsome | Safe Module Parking | Development | | | SMP Remote Control Wiring Inspection |
The wiring for the SMP remote control module was inspected by Joel Semilla (TRIUMF electrician). The module was plugged in to verify there were no issues. No changes were suggested, and then wiring was approved. |
1972
|
Thursday, August 29, 2019, 12:54 |
Adam Newsome | South Hot-Cell | Standard Operation | TM3 | | TM3 Move |
TM3 has been moved from the Middle-East silo to the South Hot Cell. |
1973
|
Tuesday, September 03, 2019, 10:48 |
Adam Newsome | South Hot-Cell | Standard Operation | TM3 | | TM3 Move |
TM3 has been moved from the South Hot-Cell to the Middle-East silo. |
1974
|
Tuesday, September 03, 2019, 10:49 |
Adam Newsome | South Hot-Cell | Standard Operation | TM4 | | TM4 Move |
TM4 has been moved from the Conditioning Station to the South Hot-Cell. |
1975
|
Wednesday, September 04, 2019, 13:53 |
chad fisher | South Hot-Cell | Repair | TM4 | | TM3 CB to TM4 |
The TM3 containment box has been installed onto TM4. No issues, leak checked ok.
|
1983
|
Tuesday, September 10, 2019, 14:04 |
David Wang | ITW | Standard Operation | | | ITW water interlock check. |
ITW water interlock check is finished. Everything is good. |
1984
|
Thursday, September 12, 2019, 09:26 |
David Wang | ITW | Repair | TM4 | | ITW bad vacuum issue and trouble shoot. |
ITW secondary vacuum was bad in last two days after TM4 was connected in ITW. Today when check the exit 2 module, I found a small needle valve on exit 2 module top was slightly opened for some reason in past months. The valve is closed . ITW vacuum is returned to normal status. |
1987
|
Wednesday, September 18, 2019, 14:28 |
Travis Cave | Spent Target Vault | Standard Operation | | | Repacking of the targets. |
Three of the five targets in the mini storage have been repackaged into the stronger pail. |
1988
|
Thursday, September 19, 2019, 10:11 |
Travis Cave | Spent Target Vault | Standard Operation | | | Repacking of the targets. |
Another target in the mini storage has been repackaged into the new pails. With one remaining to do which will be done on Monday. |
1989
|
Monday, September 23, 2019, 13:21 |
Travis Cave | Spent Target Vault | Standard Operation | | | Repacking of the targets. |
All targets in the mini vault have been repackaged and are now ready to be loaded into F-308s. All the target pails have new numbers see attached sheet for details. |
Attachment 1: Target_Index_2019-09-23_Mini_Vault.pdf
|
|
1990
|
Monday, September 30, 2019, 11:27 |
Isaac Earle | Safe Module Parking | Development | | | SMP vacuum vessel modifications completed |
The SMP vacuum vessel welds were reinforced to match the specifications on IRH1710 Rev D. In addition a tube stub was added on the side of the vessel for installation of a PRV. The relief valve installed was Accu-Glass 113150, with 2psi setpoint (not the MDC 420036 model specified on IRH1710 Rev D). The drawing will be updated to reflect this.
Welding was performed in the TRIUMF machine shop. A larger capacity forklift was rented to move the vessel back and forth between the shop and the Meson Hall loading bay where the main crane was used to flip the vessel between welds.
After welding the vessel was leak checked using a blank-off plate (helium leak tight). The vessel was then returned to the Target Hall, the top flange IRH1755 was re-installed, and the TCS shield plug was installed on the flange. The vessel was pumped down over the weekend using the SMP vacuum pump, and reached 8mTorr by Monday morning. A helium leak check was performed in the Target Hall: baseline leak rate 0.0E-9 atm-cc/sec, 0.0E-4Torr port pressure, no response to generous helium spray on PRV and around both seal locations for the top flange.
Remaining re-assembly of the SMP will now proceed. |
2000
|
Friday, October 04, 2019, 16:43 |
David Wang | Conditioning Station | Standard Operation | TM2 | | TM2 has been connected at TCS. |
TM2 has been connected at TCS this morning. helium pressure test on Tm2 HS line is done. No leak. |