Thursday, August 07, 2014, 13:58, David Wang, South Hot-Cell, Standard Operation, TM4, UCx #10, Leak check on TM4 HS water line with new UCX target.
|
Isaac and I leak checked TM4 HS line with new UCX target. The leak detector base LR 0.0xE-9 atm.cc/sec, base pressure0.0xE-4torr. Isaac sprayed helium on both VCR connections(5 seconds each) and flushed helium around the target for 6 seconds. No response on leak detector. |
Thursday, August 07, 2014, 10:45, Travis Cave, South Hot-Cell, Standard Operation, TM4, no target, module move
|
TM#4 has been moved from the south west silo to the south hot cell. |
Wednesday, August 06, 2014, 11:12, Travis Cave, South Hot-Cell, Standard Operation, , SiC#30, Spent target move
|
SiC#30 in pail #117 has been move to the spent target vault and placed in spot 2C. See attached PDF for details. |
Wednesday, August 06, 2014, 11:11, Travis Cave, South Hot-Cell, Standard Operation, TM3, no target, module move
|
TM#3 with no target has been moved to the northwest silo for storage. |
Tuesday, August 05, 2014, 11:53, David Wang, ITE, Repair, , , Reconnected ITE entrance module
|
ITE entrance module is reconnected in ITE. |
Tuesday, August 05, 2014, 10:40, Travis Cave, ITE, Standard Operation, , , module move
|
ITE Entrance module has been moved back to the east station. |
Thursday, July 31, 2014, 08:08, chad fisher, South Hot-Cell, Standard Operation, TM3, SiC#30, SiC#30 Removed and inpect   
|
SiC#30 has been removed from TM3. A quick exam of TM3 source tray did not yield any obvious signs of damage.
9 pin connector on the target showed the usual sparking/arcing marks.
Heat shield has been removed from the target. Inside of heat shield has some unusual marks on it and quite a lot of black deposits.
|
Wednesday, July 30, 2014, 11:51, Travis Cave, Conditioning Station, Maintenance, , , entrance module move
|
ITE Entrance module has been moved from the east station to the conditioning station. |
Monday, July 28, 2014, 17:26, Ron Kuramoto, ITW, Repair, , , ITW:IV5 Air leak repair  
|
Air leak was found at the Solenoid control valve located in the Pre-Separator & DB0 room. The gasket between the solenoid body and its manifold block was broken, see attached photos. The gasket and solenoid body were replaced. Air was turned back on to IV5 (B/L gate valve) with no apparent air leaks. The gate valve was actuated open & closed from the control room seeing both limits successfully.
Repair was done by Dimo Y. who received 0.01 mSv, and assisted by Anthony I. & Ron K. who both received zero dose.
Rad fields measured by RPG were; 1300 uSv/hr above B/L and 350 uSv/hr @ the Solenoid valves at knee height.
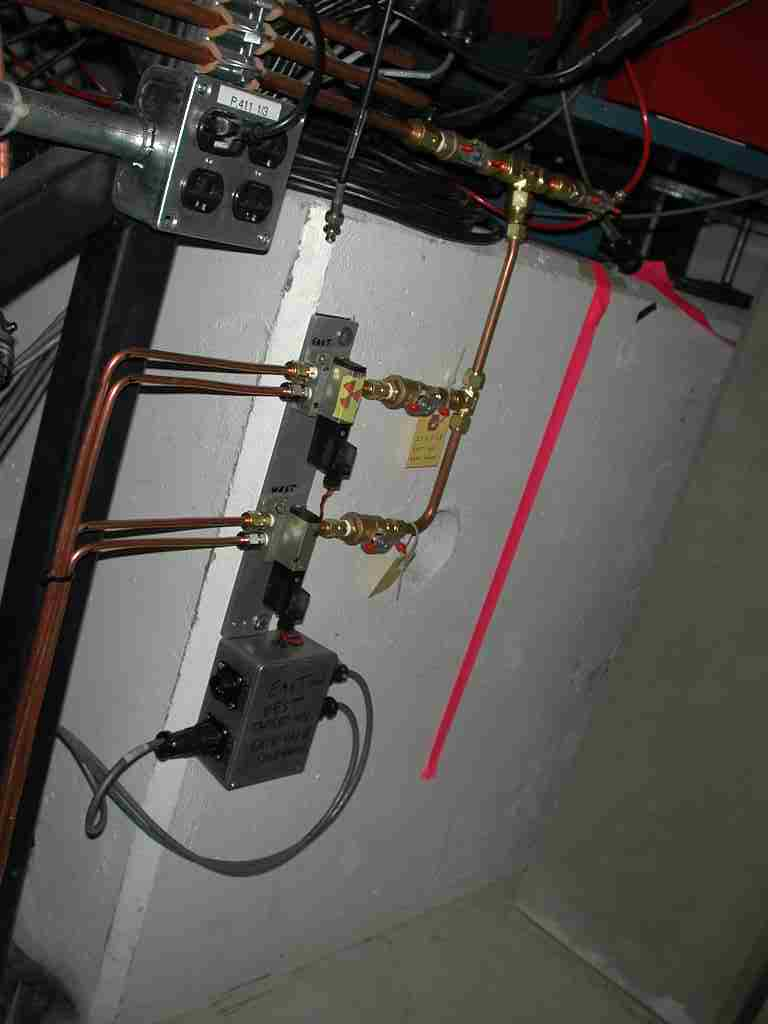
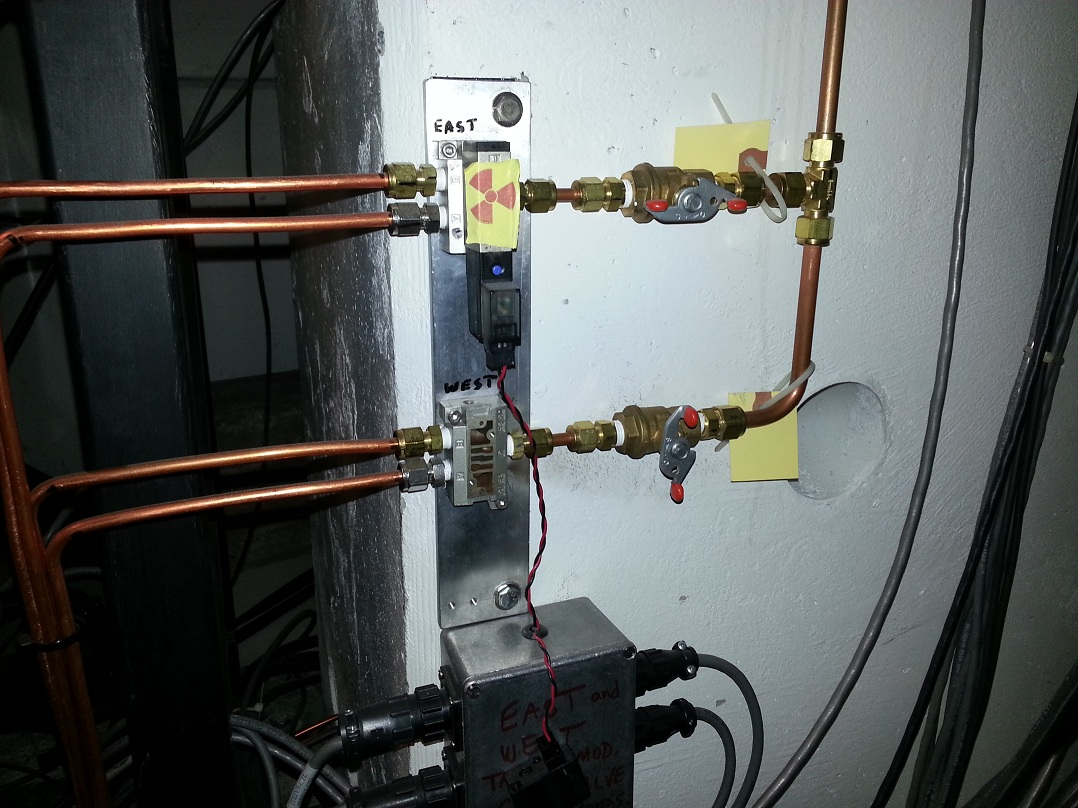
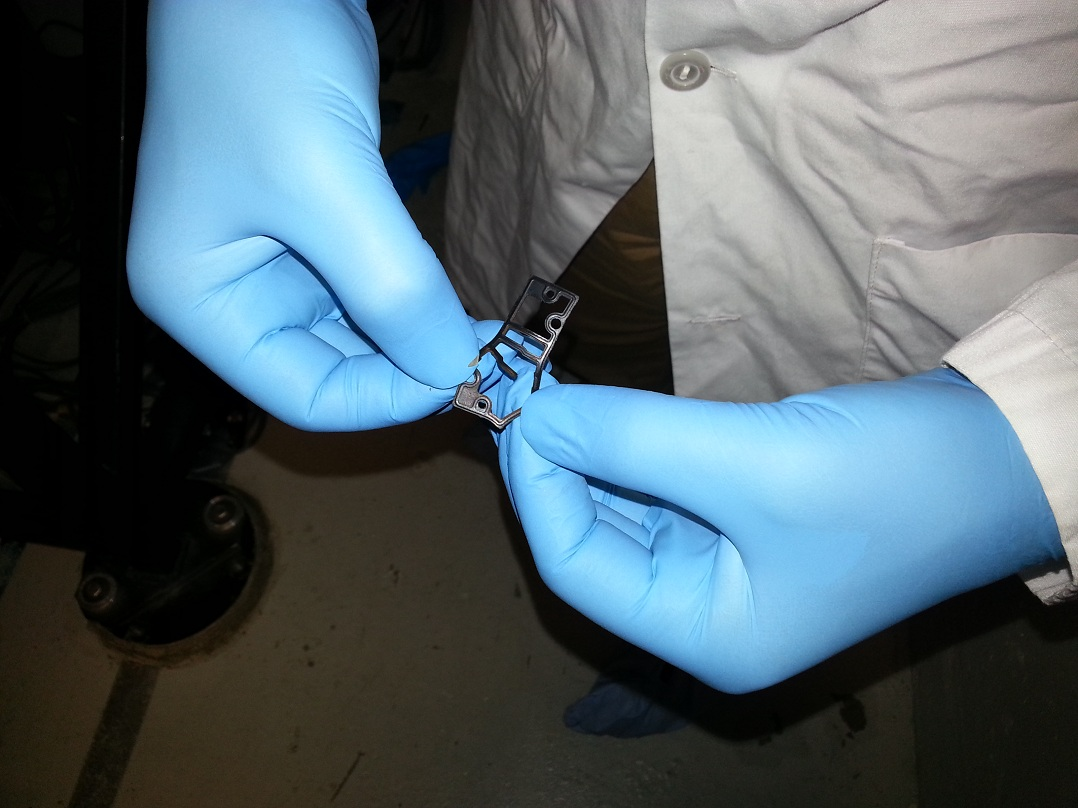
|
Monday, July 28, 2014, 14:45, David Wang, Conditioning Station, Development, TM2, , turned off TM2 and CS turbo pumps.
|
I turned off TM2 and CS turbo-pumps. TM2 will be moved from CS to silo tomorrow morning. |
Monday, July 28, 2014, 14:37, David Wang, Conditioning Station, Development, TM2, , helium pressure test on TM2 tube heater +(D)and -(C)water lines. 7x
|
- TM2 installed in Conditioning Station
- Varian Leak detector connected directly to Target Module 2 Service cap.
- Vacuum draw in Target Station with both module turbo pumps
- Leak detector baseline normal (10^-4 Torr, 10^-9 Std cc/s He)
- Since no Source tray is installed, and tube heater supply conductor is blanked off in target enclosure, it was necessary to test both supply and return points.
- For each line tested, 80 psi He was connected, and waited ~2 min to for a response on the leak detector.
- Lines tested:
- conductor D (tube heater), Supply -> no He response
- conductor D (tube heater), Return -> no He response
- conductor C (tube heater), Supply -> no He response
- conductor C (tube heater), Return -> no He response
- Based on this leak testing, both supply and return lines of conductors C & D are leak tight under 95 psi He (80 psig He supply to vacuum)
|
Monday, July 28, 2014, 09:29, Travis Cave, Conditioning Station, Standard Operation, TM2, no target, module move
|
TM#2 has been moved from the south hot cell to the conditioning station. |
Thursday, July 24, 2014, 18:21, Grant Minor, South Hot-Cell, Repair, TM2, No target / no source tray, Leak check on TM2 ionizer tube cooling lines C and D - module side  
|
Target Ionizer tube cooling lines "C" and "D" in Target Module 2 were both leak checked at the Hot Cell. The lines were both blanked-off.
Bill Paley was present with David Wang in the Target Hall, operating the leak detector. Grant Minor and Anders Mjos were present with Chad Fisher at the Hot Cell.
The "D" circuit was already blanked off with a copper blank containing silver brazed stainless steel inserts and indium plated inconel c-seals.
The "C" circuit was already blanked off with an aluminum blank and rubber o-rings.
The cooling lines are indicated in the attached screencapture from ITA6021 Rev .14, and are also labelled in the attached photo.
The "D" circuit was checked first, starting at around 12pm.
1. The helium flow was tested by blowing dust on the work table.
2. The base leak rate on the Varian leak detector was confirmed in the "D" circuit to be stable at 10^-9 atm cc / sec and the pressure was 10^-4 Torr.
3. Each soldered joint on the "D" circuit was sprayed with a 2-second blast of helium - no response at the Varian.
4. The joint between the module-half of the water block and the copper blank-off was sprayed with a 2-second burst - no response.
5. A general area flood of helium sprayed for 10 seconds was applied all around both the "D" and "C" blocks - no response.
It was concluded that the "D" circuit had passed this leak check. The "C" circuit was checked next. The detector was changed to the "C" circuit and the circuit was pumped down. At around 2pm the leak check resumed.
6. The base leak rate on the Varian leak detector was confirmed in the "C" circuit to be stable at 10^-9 atm cc / sec and the pressure was 10^-4 Torr.
7. The solder joint area on the "C" circuit was sprayed with an 8-second burst of helium - no response.
8. The joint between the two halves of the water blocks was sprayed with a 6-second helium burst - no response.
It was concluded that the "C" circuit had passed this leak check.
The electrical continuity of the "C" and "D" circuits were confirmed in the Target Hall at the service cap, and in the module at the Hot Cell, to double check that the correct lines has been pumped and leak checked - this was OK.
The ionizer tube heater lines appear to be leak tight at the Hot Cell.
|
Thursday, July 24, 2014, 09:10, Travis Cave, South Hot-Cell, Standard Operation, TM2, no target, module move
|
TM#2 has been moved to the hot cell from the north east silo. |
Wednesday, July 23, 2014, 13:36, David Wang, ITW, Standard Operation, TM1, , TM1 in ITW.
|
TM1 has been connected in ITW . The new roughing pump replaced on last Friday works good. I started all turbo pumps in ITW. The ITW TP1 controller was broken during the starting time. Dimo and I changed a new controller for ITW TP1 in electrical room. The pumping down is good so far. ITW water supplies to TM1 only. |
Tuesday, July 22, 2014, 07:32, David Wang, Conditioning Station, Standard Operation, TM1, , Stop TM1 and CS turbo pumps and ruff pump.
|
Stop TM1 and CS turbo pumps and ruff pump. TM1 is disconnect at CS. It will be vented tomorrow morning and moved to ITW. |
Monday, July 21, 2014, 13:11, David Wang, Conditioning Station, Standard Operation, TM1, , helium pressure test on TM1 HS water line at CS.
|
The TM1 HS line is pressure tested this morning with 70 psi helium at CS. No response has been found on leak detector. |
Thursday, July 17, 2014, 11:49, David Wang, Conditioning Station, Standard Operation, TM1, , TM1 and CS turbo pumps have been started
|
I connected TM1 at CS. All turbo pumps have been started. The pumping down is good so far. |
Thursday, July 17, 2014, 10:13, David Wang, Conditioning Station, Standard Operation, TM1, , Leak check on TM1 HS water line with new target installed
|
Chad and I leak checked TM1 HS waterline with new target installed at SHC. The LD base LR:0.0xE-9atm.cc/sec, base pressure: 0.0xE-4 torr. Chad sprayed helium on both VCR fittings and flushed helium around the target. No response has been found on leak detector. The target HS line is leak tight so far. I will do helium pressure test on this line at CS on next Monday. |
Thursday, July 17, 2014, 09:29, Travis Cave, South Hot-Cell, Standard Operation, TM1, Ta#43, module move
|
TM#1 with Ta#43 has been moved from the south hot cell to conditioning station. |
|