Friday, January 11, 2019, 13:59, Isaac Earle, Safe Module Parking, Development, , , SMP motor selection decision
|
SMP drivetrain design work is currently underway. Alejandro has selected a suitable 1200:1 reducer which will give a vessel rotation speed of 0.21rpm with a 1725rpm motor (deemed sufficiently close to the SHC rotation speed of 0.17rpm). The reducer however is only rated for 0.33hp, and Allon's analysis recommended we use a motor of at least 0.4hp
From his calculations the expected power required to turn the loaded vessel is 0.2hp (see Document-161943, p3). The higher figure of 0.4hp in his final recommendations comes from the power rating of a 40 tooth sprocket (the driver sprocket) with a No. 50 roller chain operating at 10rpm (the lowest speed shown on the table) - meaning this driver sprocket arrangement can handle up to 0.4hp. We discussed this on the phone on January 4th and agreed that a 1/3hp motor could be used which will match the reducer Alejandro selected, and will supply sufficient power given that calculations indicate only 0.2hp is required.
Once the vessel is installed in the shield box a test will be performed to determine the actual torque (and power) required to turn the vessel. If the value differs significantly from the calculated value the design will be revisited. |
Wednesday, May 15, 2019, 16:06, Isaac Earle, Safe Module Parking, Development, , , SMP module support flange installed and leak checked   
|
The SMP module support flange sub-assembly (IRH1755) was installed today according to drawing IRH1683. Dow Corning 111 sealing compound was used to keep the o-ring adhered to the lower groove during transportation and installation. The TCS shield plug (IRH1646) was then installed on the SMP module flange which has vacuum connections for leak checking. Vacuum was pulled on the SMP vessel using the Varian 979 leak detector. After approximately 3.5 hours of pumping the test port pressure was at 2.4E-2 Torr and leak rate was 7.9E-8atm*cc/s. Helium was configured with the regulator set at 10psi and flow rate of >10 bubbles per second in Windex and then applied slowly around the perimeter of the vacuum flange (IRH1686) and it's mating components on both the top and the bottom. There was no response on the leak detector indicating the seals on both sides of the module flange are leak tight.
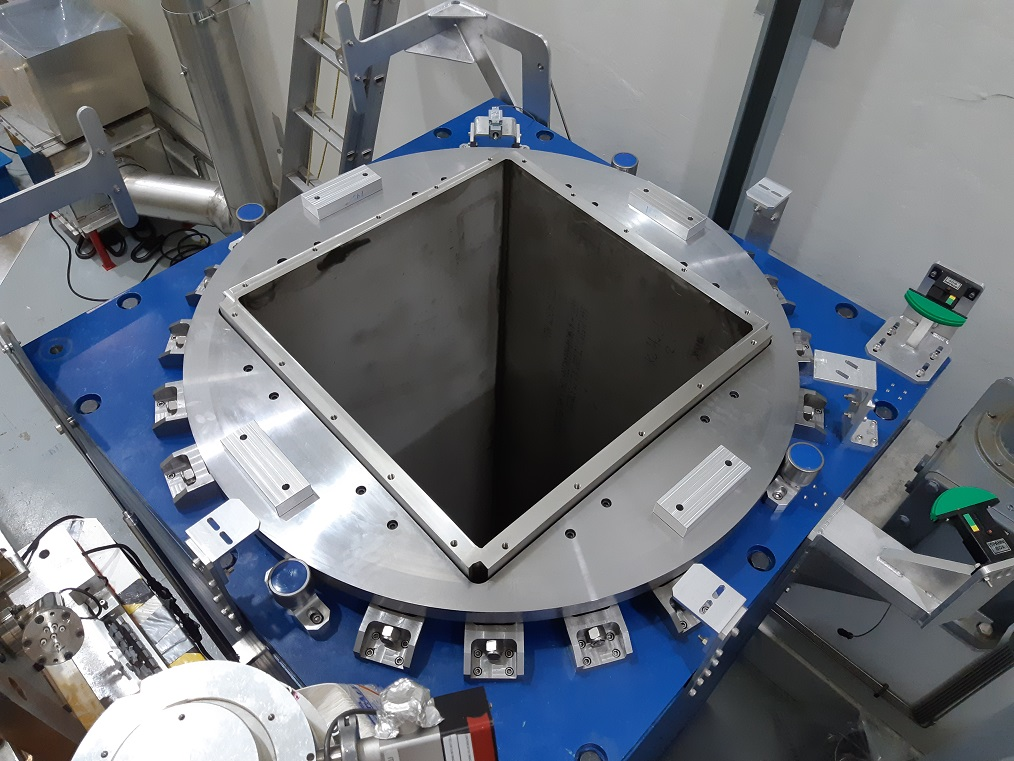
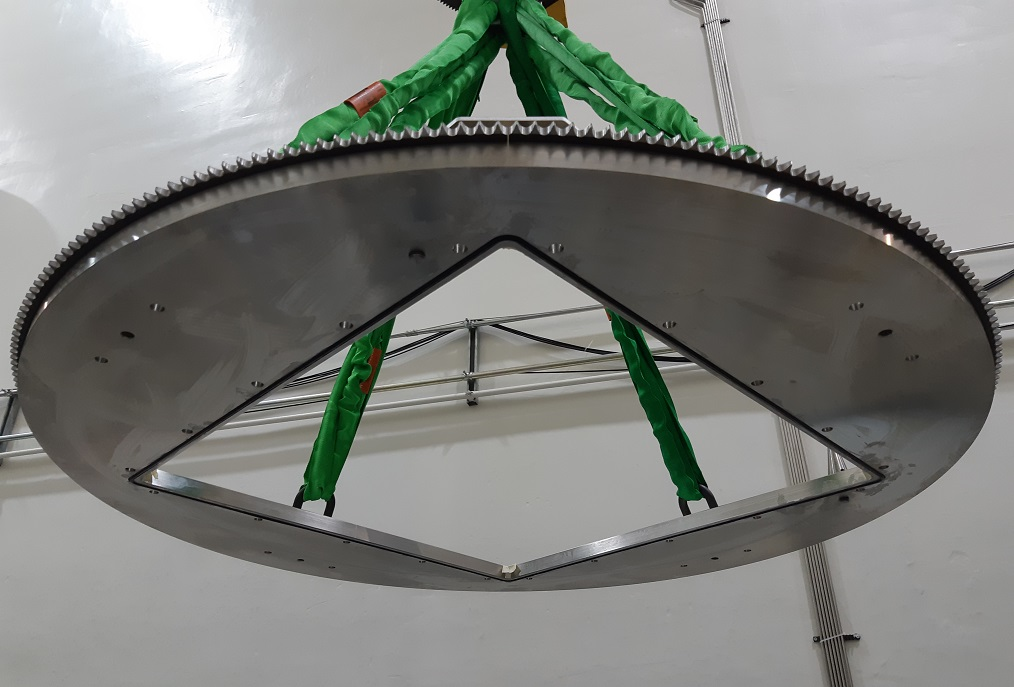
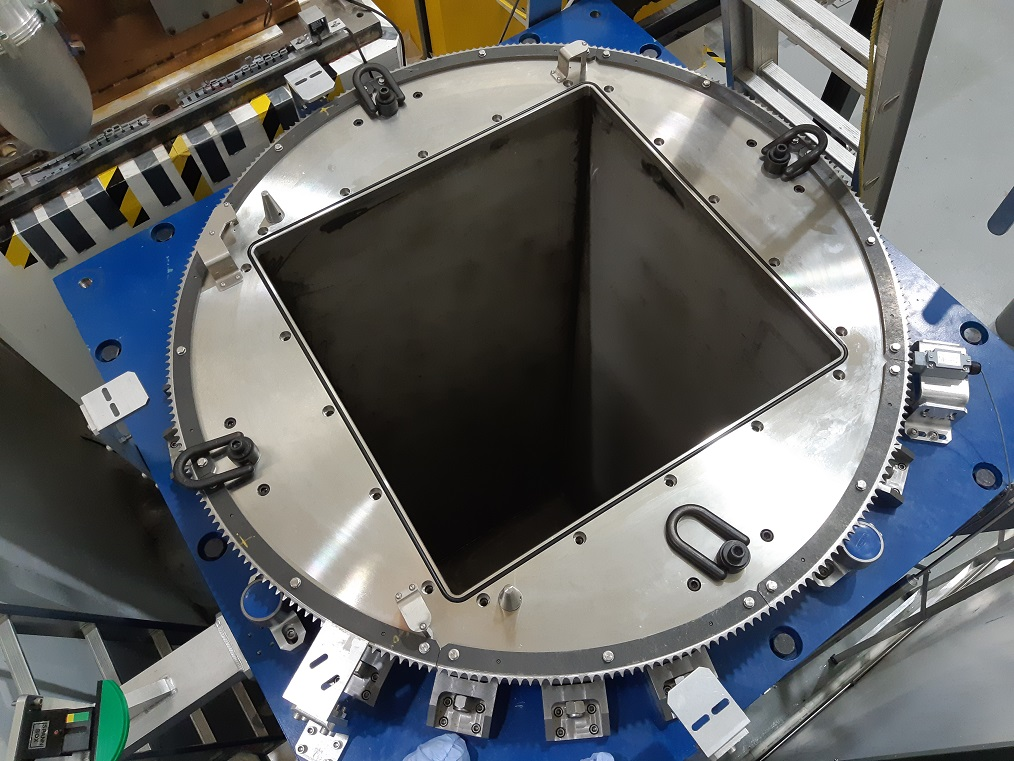
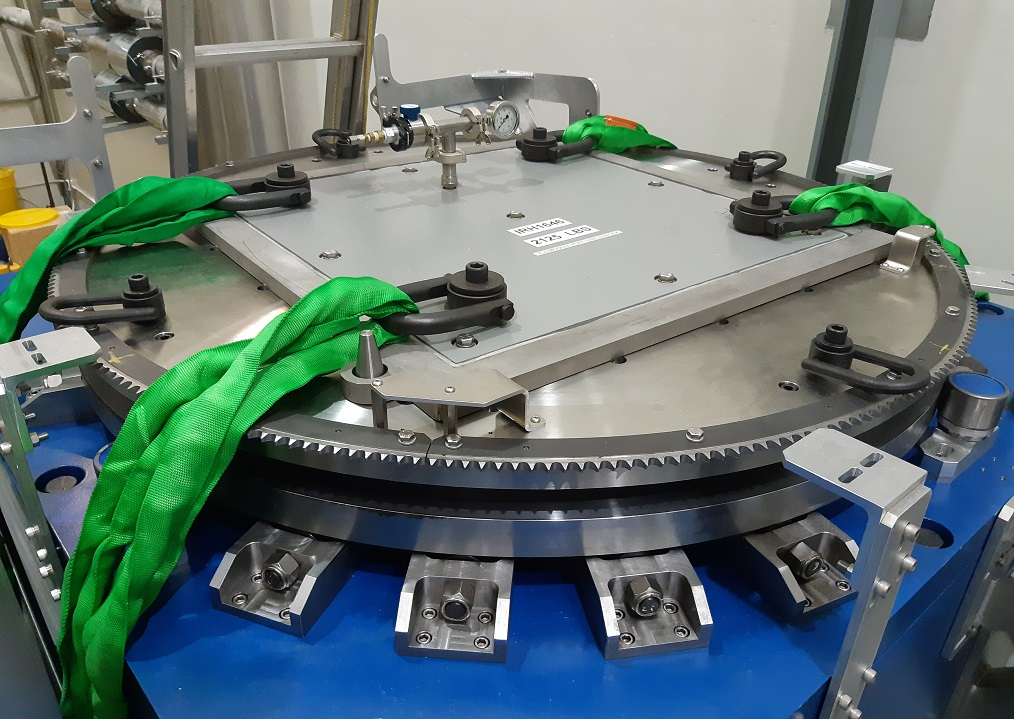
|
Thursday, January 09, 2025, 11:46, David Wang, Safe Module Parking, Standard Operation, TM4, No target, SMP is under vacuum for TM4 storage during shut down.
|
SMP:MP1 is started with SMP BV1 is opened. SMP is under vacuum for TM4 storage during shut down. |
Tuesday, October 15, 2019, 16:42, Isaac Earle, Safe Module Parking, Development, , , SMP flange alignment tested using shield plug   
|
As a preliminary test in preparation for SMP commissioning, one of the steel module shield plugs was installed into the SMP to check the positional and rotational alignment procedures. The following is a summary of the steps performed:
- Shield plug lifted with crane and rotated to an arbitrary (non-orthogonal) position
- Using the crane pendant the shield plug was roughly aligned over the SMP and lowered until the base was within 15cm of the top of the flange
- The SMP flange was rotated to roughly match the orientation of the shield plug
- Precise positioning of module achieved visually from within the Target Hall using crane for NESW position and SMP for rotation
- Module lowered into SMP vessel (not resting on base of vessel)
- Target Hall crane was then set to "Test Mode" and operated from the crane control room
- Crane position with the module centered in the SMP vessel was recorded as E-W: 18.5495m, N-S: 4.9065m
- The shield plug was lifted from the SMP, moved to an arbitrary location in the Target Hall, and set to a different arbitrary rotational position
- The SMP flange was returned to the "centered" position
- The shield plug was moved to the previously recorded location over the SMP and lowered to within 15cm of the top of the flange (using cameras)
- Steps 3-5 were repeated using only camera views to achieve alignment (SMP rotation was controlled using the pendant with instructions by phone from the crane room operator because the module for remote control currently requires a part to be changed)
Official commissioning of the SMP will now be planned as per the commissioning plan Document-170404
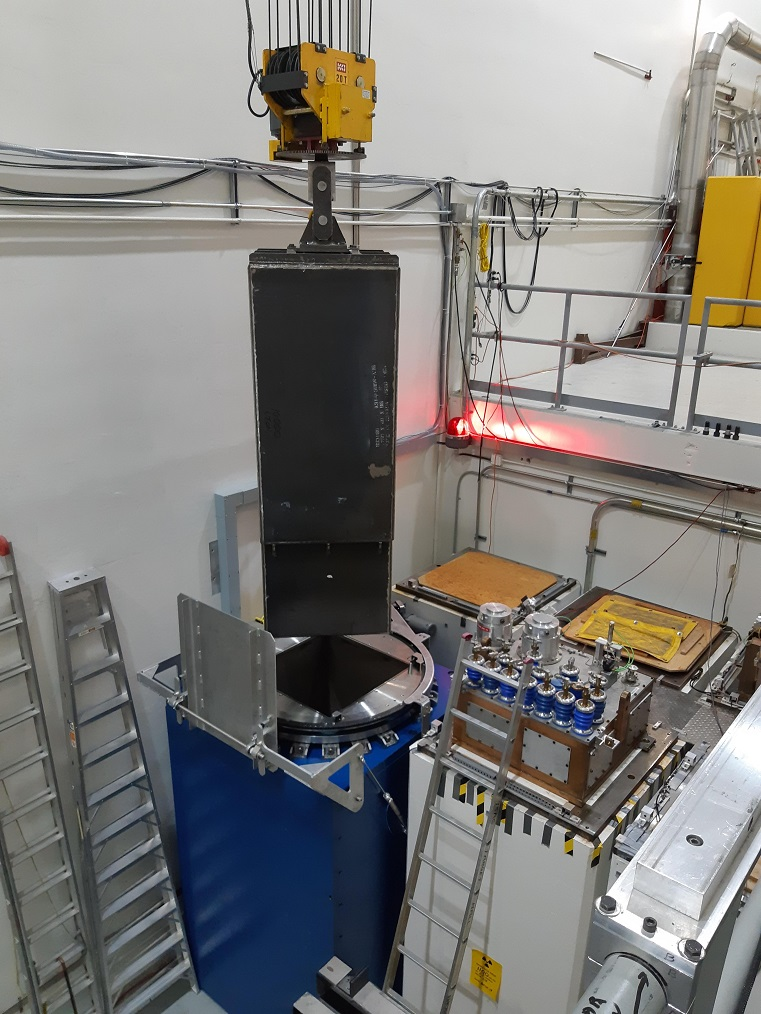
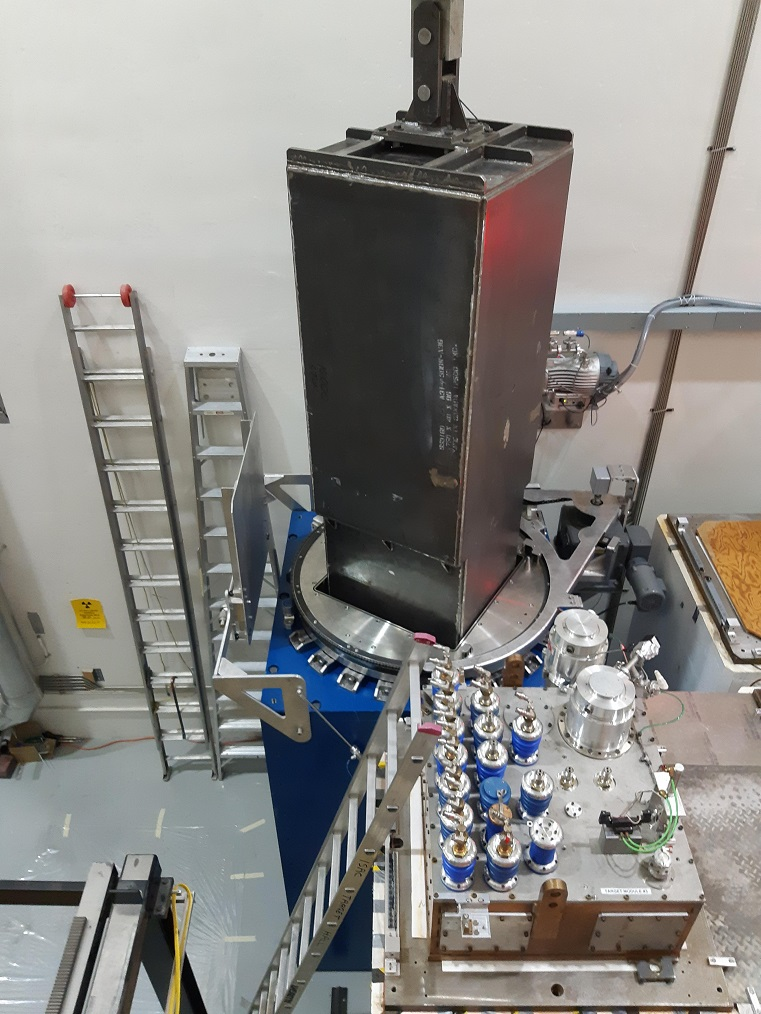
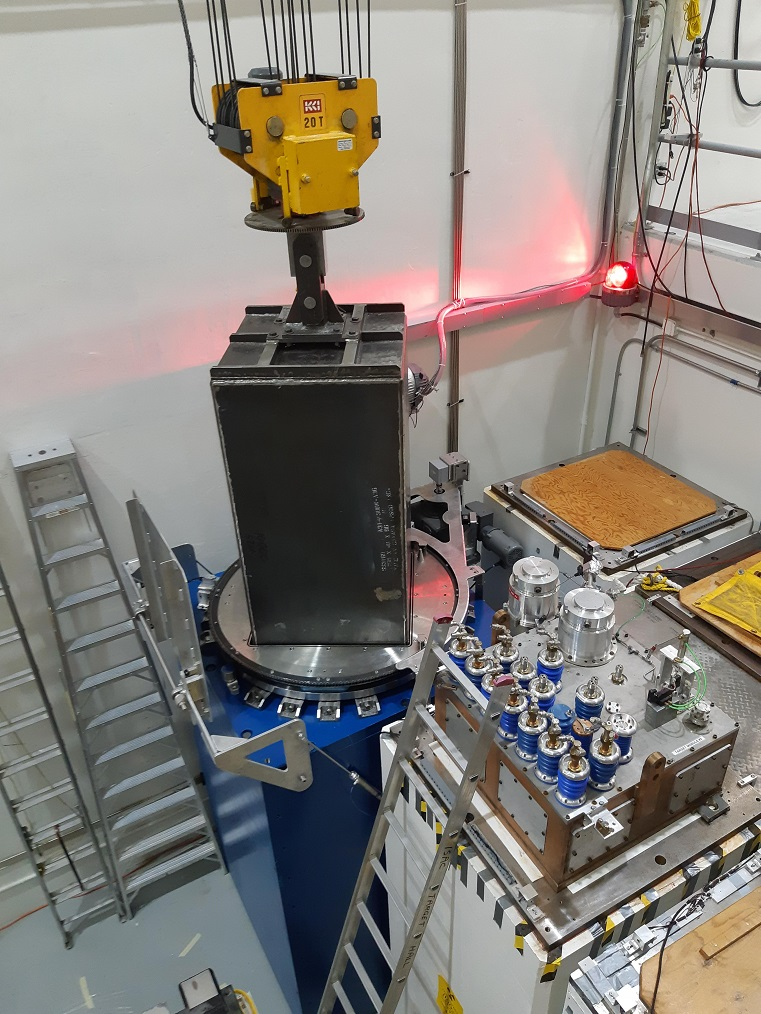
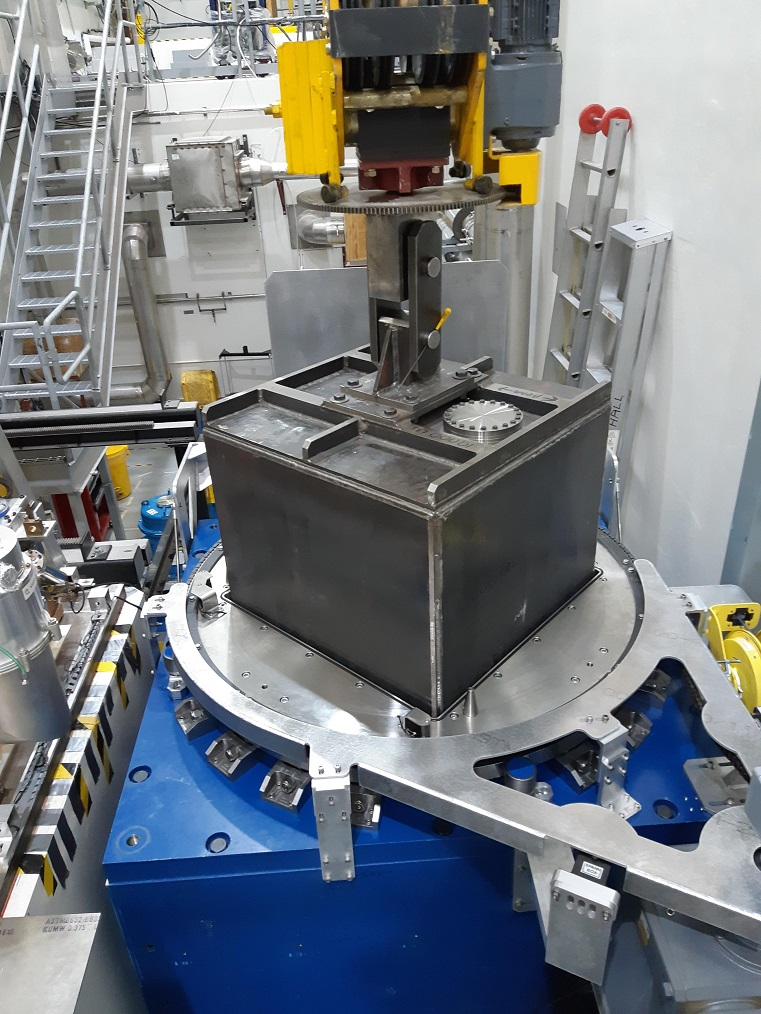
|
Friday, July 12, 2024, 08:51, Riley Sykes, Safe Module Parking, Maintenance, , , SMP chain guard
|
SS washers were added to all slotted holes on SMP chainguard cover plate |
Friday, August 23, 2019, 14:27, Isaac Earle, Safe Module Parking, Development, , , SMP camera video cabling installed and tested
|
Installation of the video lines for the SMP cameras was completed yesterday according to IRH1670 Rev B. All four cameras were confirmed to be displaying properly in the crane control room. The cameras are powered from an outlet wired to circuit 35/37 on Panel #443 (located in the NHCSA). This is independent from the power supply for other existing camera systems in the Target Hall. The SMP turntable was rotated through the full range of motion (reached CW and CCW limits) and the cable routing and reel take-up system performed as expected. |
Thursday, December 12, 2019, 14:39, Isaac Earle, Safe Module Parking, Development, , , SMP assembly shifted 1.0" north
|
The SMP assembly was shifted approximately 1.0" north today by pushing it, braced against the south wall, using a 100 Ton capacity air lifting bag supplied by Beamlines Group. The move was one of the action items identified at the Gate 4A/4B close-out review. During commissioning of the SMP, TM3 was installed into the vacuum vessel, which required the crane to be all the way at its south limit, so the move is to provide some margin for future use, particularly if TM1 is put in the SMP as the extent of its shielding is slightly larger than the other modules.
One of the air fittings for the lid actuation cylinder on the north side was damaged during the move. It was replaced and correct functionality of lid actuation was then confirmed. |
Tuesday, June 23, 2020, 10:56, David Wang, Safe Module Parking, Standard Operation, , , SMP annual service.
|
Dan and I did the SMP annual maintenance service today. Lid open/close , vessel rotation and limit switch check, lubricate chains, tighten fasteners, and visual inspection. Everything works fine. |
Tuesday, October 29, 2019, 10:00, Adam Newsome, Safe Module Parking, Development, , , SMP Updates to E-stop circuit and feedback signals
|
The SMP main control panel and remote control module were updated in order to implement the following items which were deemed desirable during commissioning:
- 24 VDC line added to E-stop circuit:
Previously the E-stop relay cut power to only 120 VAC. This means that the lid rotation motor would stop instantly, but since the lid open/close valve is powered by 24 VDC which comes from a power supply unit, there would be a short delay while the unit powers off in which the valve was still active. This could result in a situation in which, for example, someone is operating the pendant to close the lid and another person recognizes a hazard and presses the E-stop on the main panel, but the lid does not stop closing for approximately 3 seconds while the operator is still holding the "close" button down.
To rectify this issue, the 24 VDC line was routed through a NO contact of the same E-stop relay that controls the entire 120 VAC supply to the system. This was tested on Oct. 25, 2019 - working.
- Status feedback signals to remote control room:
Previously status signals for "Lid raised", "Lid Centred", "CW Limit", and "CCW Limit" were only displayed as light indicators on the main control panel. It was determined during remote operation that it would be helpful to have these signals sent back to the software interface so that an operator does not need to use a camera to look at the light indicators.
Electrical drawings and cable schedule have been updated to reflect these changes. The SMP will be tested again using the commissioning plan checklist to confirm no there were no inadvertent effects on the rest of the same from these changes.
|
Tuesday, August 27, 2019, 13:12, Adam Newsome, Safe Module Parking, Development, , , SMP Remote Control Wiring Inspection
|
The wiring for the SMP remote control module was inspected by Joel Semilla (TRIUMF electrician). The module was plugged in to verify there were no issues. No changes were suggested, and then wiring was approved. |
Thursday, October 10, 2019, 16:17, Adam Newsome, Safe Module Parking, Development, , , SMP Main Panel: Relay Addition for E-Stop Circut 
|
An update was made for the E-stop and power supply system in the SMP main panel. Upon testing remote control, it was determined that the Opto 22 AC module was not sufficiently rated to handle the current draw of the motor (5A fuse versus motor 5.7A current draw). The design was modified so that the E-stop chain, which supplies 120 VAC line voltage through the main panel E-stop then the remote module (or local pendant when plugged in), will now activate a relay rather than run directly to the motor and 24 VDC PSU. This means that this E-stop chain will not carry the current draw of the entire system. Rather, the relay that is toggled when the E-stop circuit is closed will supply the system with power - this relay is rated for 15 A so the main 10 A fuse will blow before the relay fails in the event of a current spike. The new relay was installed on Oct 9, 2019. The local pendant was tested at this time and worked as expected (motion control, E-stops). On Oct 10, 2019, remote control was tested again and is working as expected (motion control, E-stops). In the attached schematic screenshot, the modification is CR7. In the image of the panel, this relay is located in the top left.
Edit: TRIUMF electrician Joel Semilla has seen the design change and verified it is acceptable. |
Friday, May 17, 2019, 16:46, Adam Newsome, Safe Module Parking, Development, , , SMP Controls Installation Update   
|
The following controls-related items were installed for the SMP project:
- Cable tray
- Main control panel
- Motor starter box
- Wiring from limit switches and rotation motor to main control panel
- Air fittings at supply (quick disconnect)
- Main air supply hose from supply to control panel (quick disconnect)
- Air tubing from lid control valve at control panel to lid cylinders
Air fittings stem off existing air supply lines on the South wall, below a manual shutoff valve. A quick disconnect was installed. When SMP is not in use, manual shutoff valve should be left off.
Main control panel and motor starter box were mounted on the North wall. Wire duct runs from the main control panel to the grated floor. Cabling/air runs underneath the mezzanine platform, along existing and new cable tray, to the SMP.
Cable tray was installed on the South wall, from the corner to the SMP module. A cutout was made to accommodate for existing tubing. An additional ~1 ft. of tray will be added to the end, near the corner, at a future time.
Remainder of installation work to be done before commissioning:
- Mount and install new Opto-22 module
- Chain new Opto-22 module to existing one (power, comms) below mezzanine on North wall |
Friday, February 14, 2020, 14:13, David Wang, South Hot-Cell, Standard Operation, TM4, , SIS dummy target for IGLIS TM4 electrical check
|
Electrical check and HS, window leak check result at SHC. See attachment. |
Thursday, September 22, 2016, 13:04, David Wang, South Hot-Cell, Standard Operation, TM4, , SHC, TM4 leak check on HS line.
|
Chad and I leak checked the TM4 HS line after new target installation. base leak rate:0.0Xe-9 atm.cc/sec. No response on LD during the leak check. The line is leak free so far. It will be helium pressurized at TCS late. |
Tuesday, November 01, 2016, 14:58, David Wang, South Hot-Cell, Standard Operation, TM4, , SHC, TM4 leak check on HS line.
|
Chad and I did a leak check on TM4 HS line with new Ta target installed. Base leak rate 0.0xE-9 atm.cc/sec. base pressure 0.0XE-4. splayed 2 helium to each VCR joints and did 10 seconds helium flush. No response on LD during the test. The HS line is leak free so far. It will be helium pressurized at TCS later. |
Tuesday, May 10, 2016, 13:54, David Wang, South Hot-Cell, Standard Operation, TM2, , SHC, TM2 leak check on window line and HS line.
|
Chad and I leak checked the TM2 HS and window lines after new target installation. The window line was very easy pumped down on LD. But, The HS line only could pumped to 2-3 torr at first. Chad changed the VCR gaskets on HS line(target). It solved the problem. The LD could pumped both of Window and HS lines to the bottom scale. Chad sprayed lots helium around the VCR joints. No leak has been found. WE will do helium pressurizing test on them at TCS. |
Wednesday, August 24, 2016, 10:44, David Wang, South Hot-Cell, Standard Operation, TM2, , SHC, TM2 leak check on HS line.
|
Chad and I leak checked Tm2 Hs line with new target installed. Base LR 0.0Xe-9 atm.cc/sec. No leak has been found. This line will be helium pressured at TCS later. |
Monday, October 24, 2016, 14:54, David Wang, South Hot-Cell, Standard Operation, TM2, , SHC, TM2 leak check on HS line.
|
Chad and I did the leak check on TM2 heat shield line. LD base leak rate:0.0xE-9atm.cc/sec. Base pressure:0.0X E-9 torr. The line is leak free. |
Wednesday, November 23, 2016, 16:10, David Wang, South Hot-Cell, Standard Operation, TM2, , SHC, TM2 leak check on HS line.
|
Chad and I leak checked TM2 HS line with new UCx target installed. Helium spray 2 seconds on each joint and 10seconds flushing around target in SHC. LD base LR: 0.0XE-9atm.cc/sec, base pressure:0.0XE-4 torr. No response has been found on LD during check. The line is leak free. |
Tuesday, April 11, 2017, 14:06, David Wang, Conditioning Station, Standard Operation, TM4, , SHC, TM2 leak check on HS line.
|
Chad and I did leak check on TM1 HS line at SHC. 0.0XE-9 atm.cc/sec. No leak. |
|