Thursday, June 22, 2017, 11:10, chad fisher, South Hot-Cell, Maintenance, , , In cell airline
|
The in cell airline has preemptively been replaced. The hose was, as far as I know the original. |
Monday, June 19, 2017, 07:29, David Wang, Conditioning Station, Standard Operation, TM2, , Update TH MS project schedule. 
|
Update TH MS project schedule. See attachment 1,2. |
Thursday, June 15, 2017, 11:29, Isaac Earle, North Hot-Cell, Development, , , NHC inlet ducting installed   
|
The North Hot Cell inlet ducting assembly was installed today in the target hall at the north end of the NHC roof block. A small section of the perforated aluminum sheet on the TCS cage had to be trimmed for the assembly to fit (see IMG_0214). At each end of the assembly it was fastened to the roof structure using a 1/4"-20 tapped hole in the steel roof, and a 1/4"-20 anchor in the north wall of the target hall. The base flange of the assembly was sealed to the roof structure and TH wall using Sikaflex 1A polyurethane sealant on all sides.
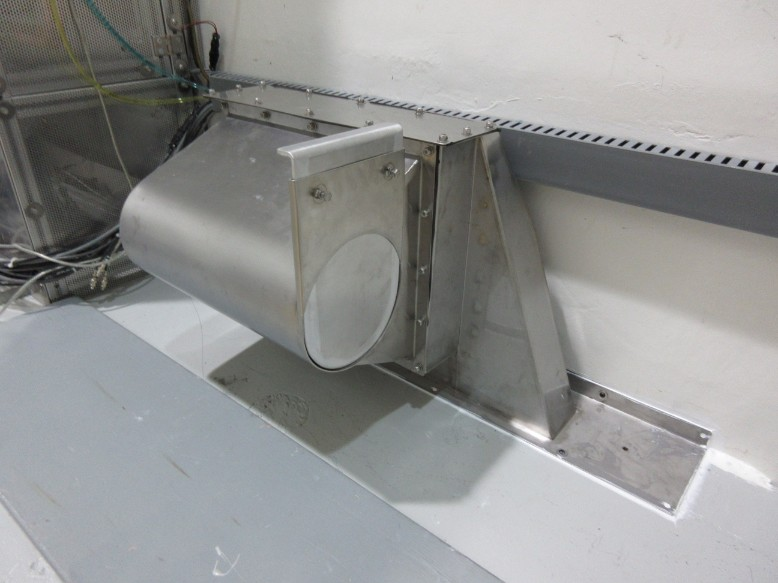
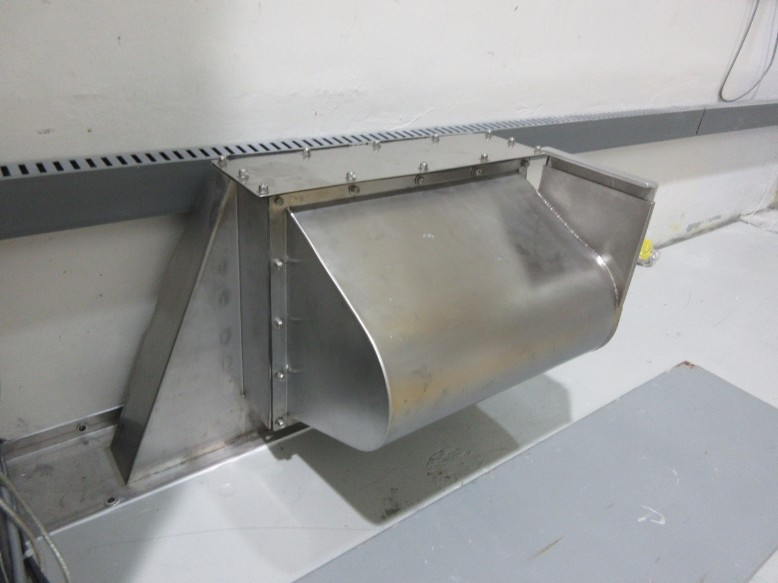
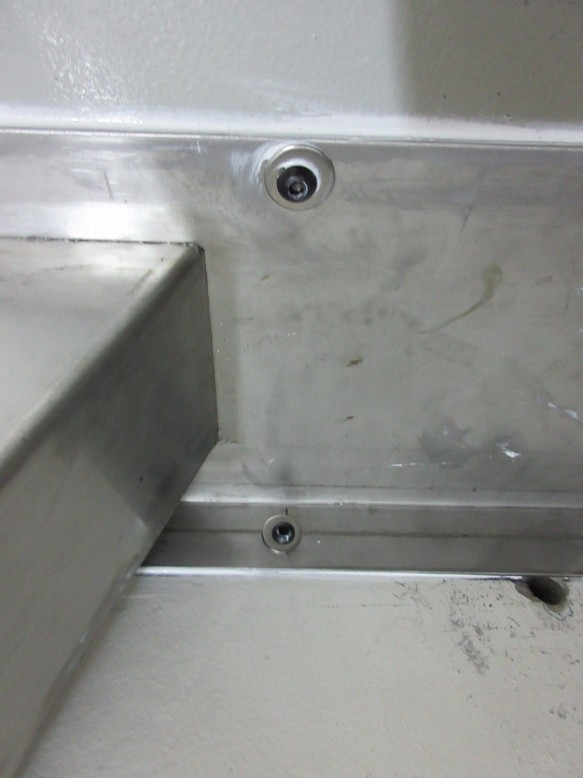
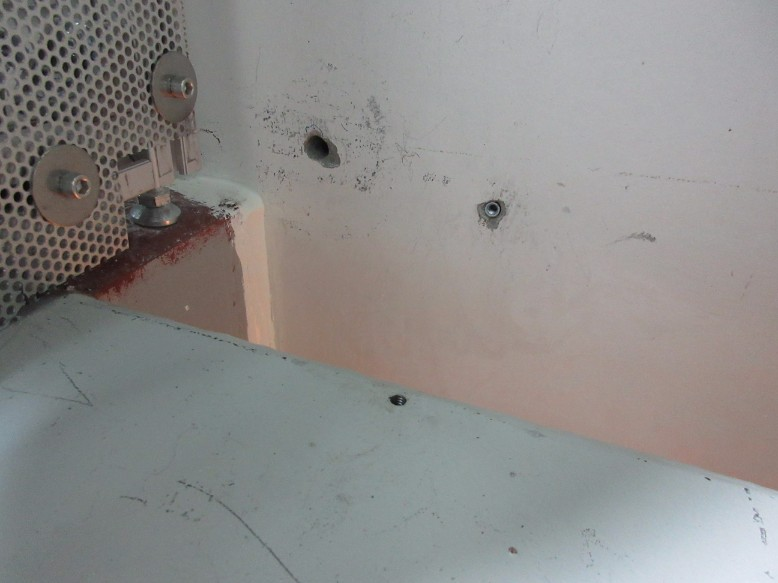
|
Tuesday, June 13, 2017, 13:41, David Wang, ITW, Standard Operation, TM2, , TM2 has been connected in ITW.
|
Yasmine and I connected TM2 in ITW today. the control page is set to febiad mode. Both gas line in ITW are opened for febiad run. All connections are double checked. Module connection checklist is finished. All turbo pumps are started now. Everything is good so far. The TM2 is ready for conditioning when the ITW vacuum is good enough. |
Tuesday, June 13, 2017, 11:10, Grant Minor, Crane, Maintenance, , , ISAC THall Crane 100% / 125% Load Test Documentation - 2011    
|
The ISAC Target Hall Crane was load tested and re-certified in January 2011 prior to doing a near-capacity lift for the North Hot Cell roof structure (IRH1112E).
Photos and documentation from Norelco is attached.
- Grant |
Tuesday, June 13, 2017, 09:57, Travis Cave, ITW, Standard Operation, TM2, SiC#36, module moved
|
TM#2 with SiC#36 has been moved from the conditioning station to the west target station. |
Monday, June 12, 2017, 13:51, Travis Cave, Spent Target Vault, Standard Operation, , , Spent Target move
|
The spent Ta#51 target has been moved from the south hot cell to the spent target vault. It was placed in pail#149 and put in spot 8B of the vault. |
Friday, June 09, 2017, 11:21, chad fisher, North Hot-Cell, Maintenance, , , Model 'N' Slave Removal Through Roof
|
Isaac and Chad disengaged the slave end of the manipulator and performed a slave removal through the slave removal roof hatch. This is part of investigation into a 'Z' motion tape that is "rubbing" on its drum on the master side of the manipulator during manual 'Z' retraction of 'Z' extension.
This also was the first test of the concept of removing the manipulator slave through the manipulator hatch that was built into the roof.
The lifting bail on the slave end of the manipulator was not centered to the hatch as per design but this did not compromise the procedure at all and the procedure otherwise followed the design intent.
Pictures can be located on Docushare http://documants.triumf.ca/docushare/dsweb/View/Collection-20157
|
Thursday, June 08, 2017, 08:35, David Wang, Conditioning Station, Development, TM2, , TM2 gas line reconfiguration on the module top.
|
Reconfigured TM2 gas line on the module top. It matches with the febiad gas line we are using on service tray now. Facing the module, both of them should be that right side line of two SST lines on feed-through. The gas line on TM2 was leak checked with a blind cap installed on service tray side and LD connected on module top this Tuesday. It is leak free with helium spray on the top of module and service tray. |
Thursday, June 08, 2017, 07:37, David Wang, Conditioning Station, Standard Operation, TM2, , Helium pressure test on TM2 water llines at TCS.
|
The helium pressure test on HS line is done at TCS this morning. I got the same result as last time when we helium pressure it it with first target in April. The leak rate on this line is 1.8 XE-7atm.cc/sec. So, we know this leak is mostly on the line, but not on the VCR joints connecting the target. See attachment for last time(April) checking e-log. The leak could be from water block which is same as other lines. I do not think this leak rate will affect the operation.
The attachment can not be opened for some reasons. Please check TM2 leak check 2017-03-13 e- log for last time test result and comment. |
Wednesday, June 07, 2017, 13:34, David Wang, Conditioning Station, Standard Operation, TM2, , TM2 and TCS vacuum system has been connected.
|
I started all turbo pumps. |
Wednesday, June 07, 2017, 13:33, David Wang, Conditioning Station, Standard Operation, TM2, , TM2 SiC#36 leakc check and electrical check.
|
The results are good. See attachment. |
Tuesday, June 06, 2017, 13:42, chad fisher, South Hot-Cell, Standard Operation, TM2, SiC#36, Ta#51 removed SiC#36 installed
|
This afternoon Ta#51 was removed from TM2 and SiC#36 installed.
All new fasteners used. High current fasteners torqued to 130 in lbs.
|
Wednesday, May 24, 2017, 08:11, David Wang, ITW, Standard Operation, TM2, , TH schedule 132 update weekly 
|
See attachments. |
Tuesday, May 23, 2017, 14:10, David Wang, ITE, Standard Operation, , , ITE water interlock check is done.
|
We do this check once a year now. Rene found a target oven reset issue during the check . He will consult with Friedhelm. The interlock check is good. |
Tuesday, May 23, 2017, 13:30, David Wang, ITE, Standard Operation, TM4, , TM4 has been connected in ITE
|
Yasmine and I connected TM4 in ITE . All turbo pumps are started. |
Tuesday, May 23, 2017, 10:41, Travis Cave, ITE, Standard Operation, TM4, UC#20, Module move
|
TM#4 with UC#20 has been moved from the conditioning station to the east target station. |
Friday, May 19, 2017, 13:49, David Wang, Conditioning Station, Repair, TM4, , TM4 TP1 at TCS
|
TM4 TP1 is replaced. TCS and TM4 was argon vented before the job.The job took about 30minutes. I started the all turbo pumps after job. All pumps work fine. The TCS vacuum is good. |
Friday, May 19, 2017, 12:25, David Wang, Conditioning Station, Standard Operation, TM4, , TCS and TM4 water flow measurement.
|
|
TCS(LPM) |
Freq(HZ) |
TCS+TM4(LPM) |
Freq(HZ) |
Ta |
5.5 |
106 |
3.7 |
68 |
Tu |
5.6 |
107 |
4.3 |
79 |
Coil(RU only) |
5.8 |
112 |
4.6 |
92 |
HS |
7.0 |
13 |
6.6 |
12 |
MSP |
6.4 |
21 |
5.8 |
21 |
EE |
5.6 |
112 |
3.8 |
77 |
Window |
4.5 |
81 |
4.3 |
78 |
|
Thursday, May 18, 2017, 11:36, Travis Cave, Conditioning Station, Standard Operation, TM4, UC#20, Electrical Check
|
Electrical check of TM#4 with UC#20 at the conditioning station under vacuum. See attached for details. |
|