Thursday, August 17, 2017, 14:38, Isaac Earle, North Hot-Cell, Development, , , 4/6 NHC roof blocks installed 7x
|
Roof blocks IRH1641, IRH1642, IRH1643, and IRH1644 have been fully assembled, labeled, and installed as per drawing IRH1652. Fabrication of TCS shield block (IRH1646) and NHC module port block (IRH1645) is still in progress.






|
Friday, October 06, 2017, 11:12, Isaac Earle, North Hot-Cell, Development, , , NHC module port shield block and TCS vessel shield block installed    
|
The NHC module port shield block (IRH1645) and the TCS vessel shield block (IRH1646) were installed yesterday in the target hall according to assembly drawing IRH1652. No issues were encountered during installation. Vacuum was pulled on the TCS and a leak check was performed on the shield: no leaks found.
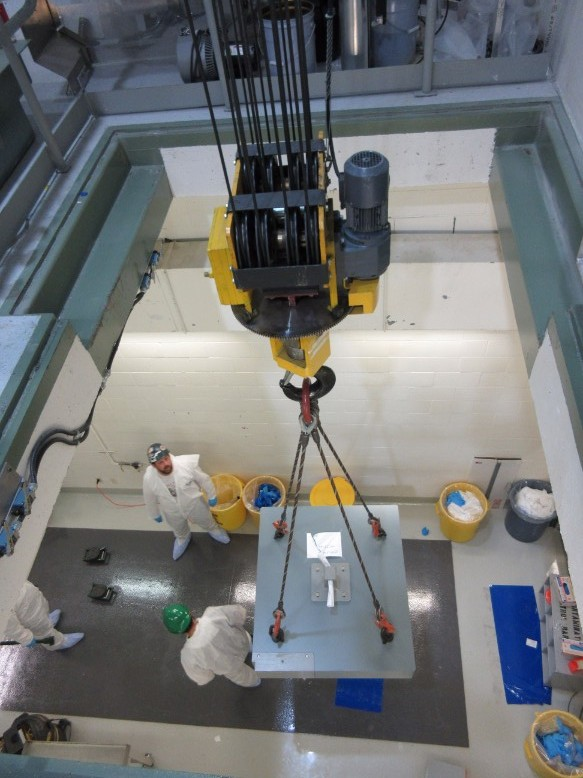
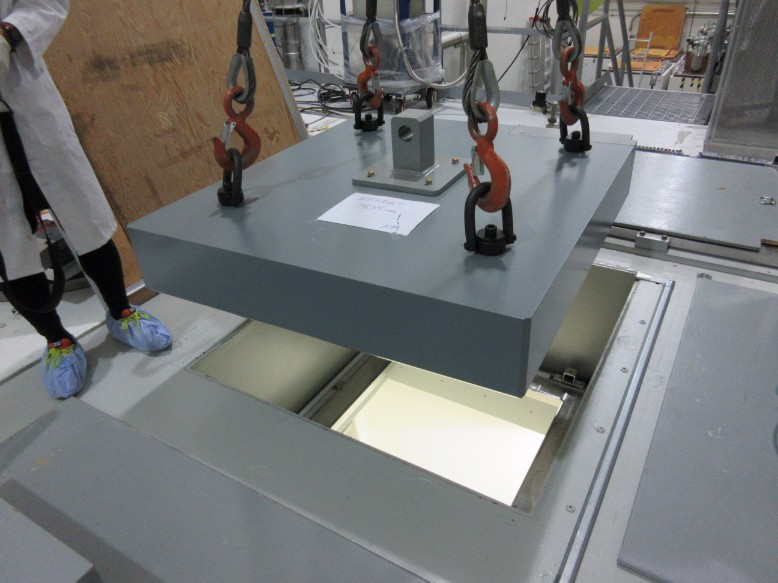
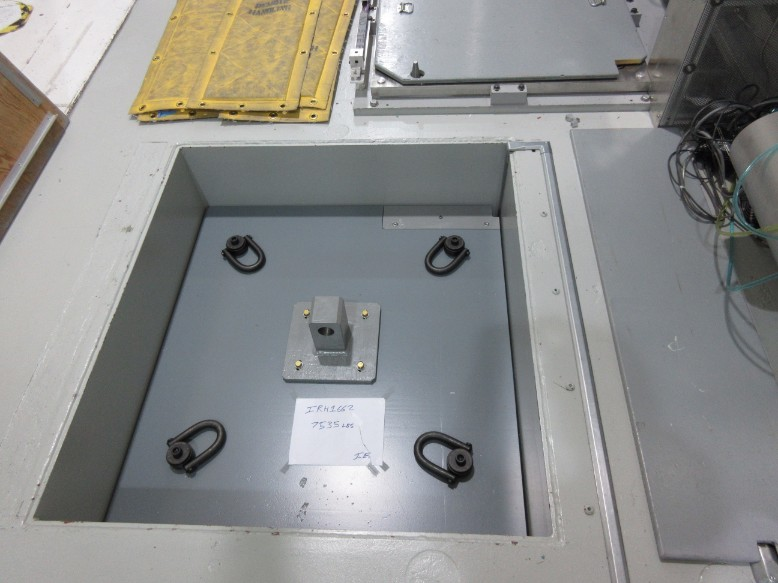

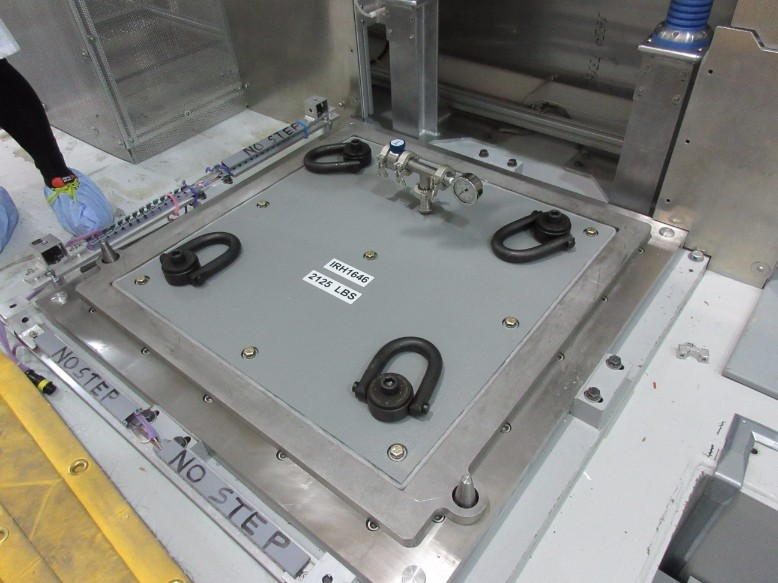
|
Friday, October 06, 2017, 11:21, Isaac Earle, North Hot-Cell, Development, , , ISAC-1 active sump drain pipe modified  
|
The 4" PVC drain line in the ISAC-1 active sump was modified so that the drain pipe terminates below the low level water line of the automatic pump-out system. This will prevent backflow of sump gasses into the SHC, NHC, or TCS space if the air pressure in any of those rooms are lower than the sump air pressure. The details of the modification were specified by Mechanical Services Group, and the work was done by Paul Jensen. This system is defined in drawing IAM19183.
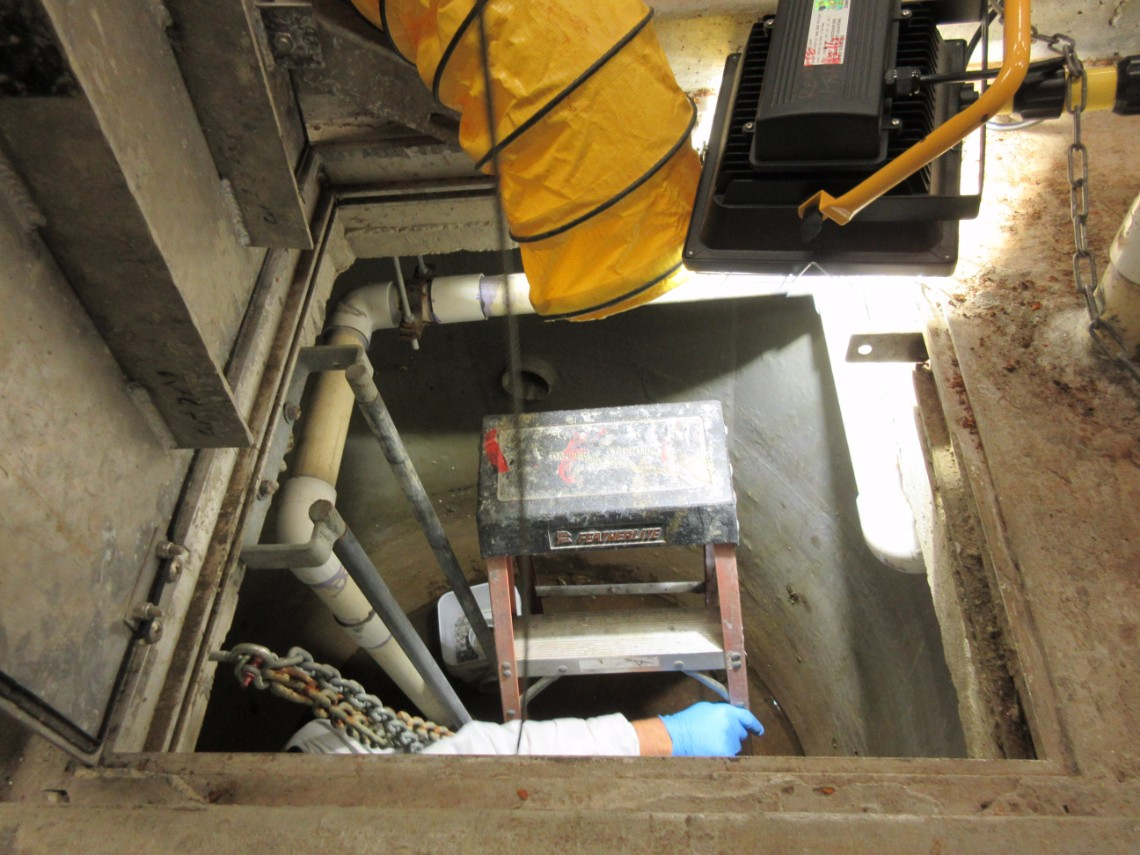
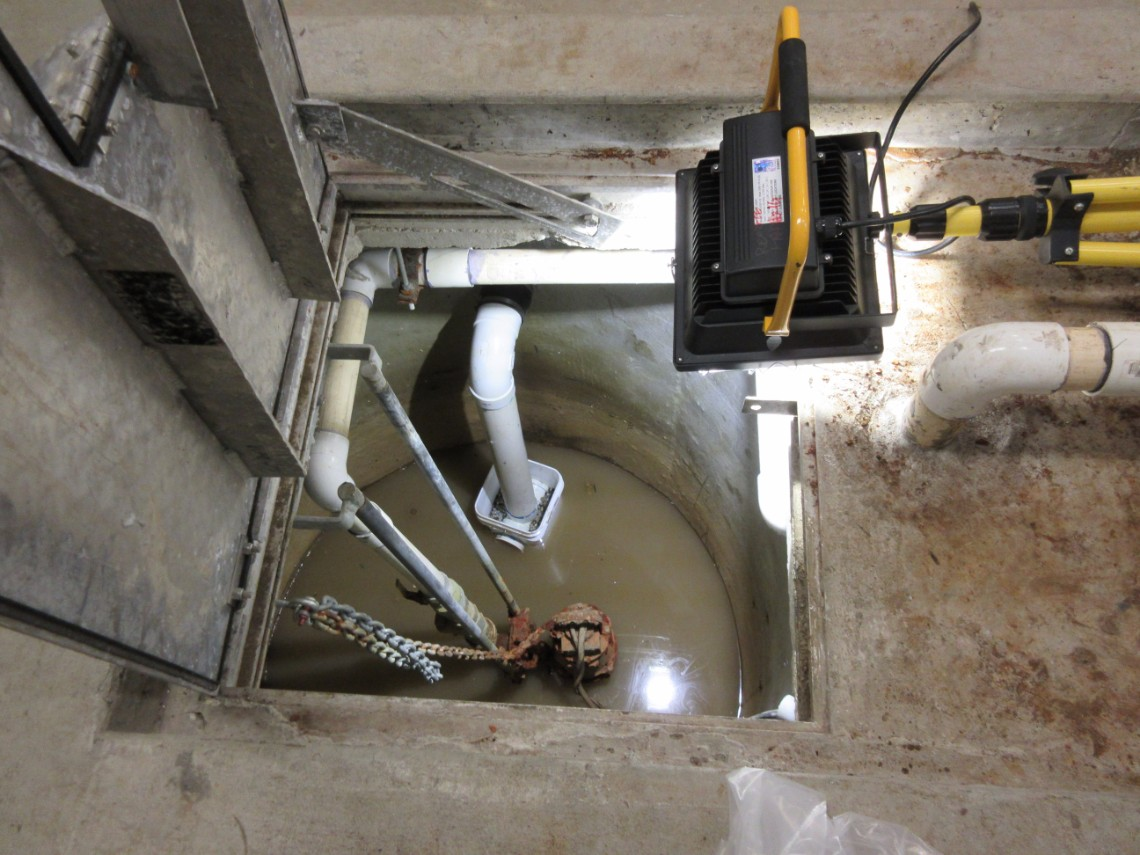
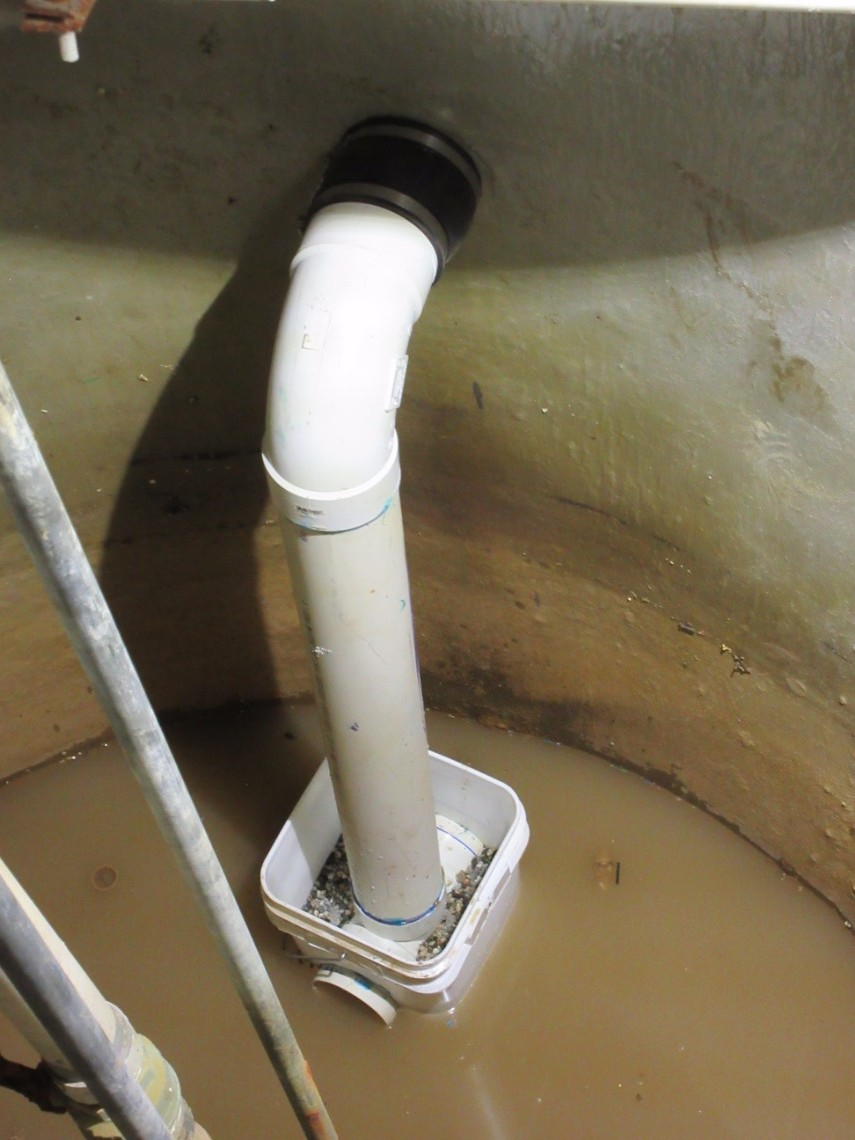
|
Friday, December 01, 2017, 16:42, Isaac Earle, North Hot-Cell, Repair, , , NHC manipulator service visit 
|
Pete Dudley, manipulator service technician from CRL, was on site from Nov 27-30 to service the NHC Model N manipulators (See E-log entry #1578 for background).
He began by evaluating the motion selection and electric drive of the manipulator installed on the blue service cart. This manipulator had chip A0166R01, same as the right side manipulator which had the failure described in E-Log 1578. Pete noted that the arm was very slow to switch between the different drive directions, and had a significant lag between when the switch for motion was released, and when the motor actually stopped driving. This was the case with all directions. Because of this, he suspected that the right arm Z tape broke because when the manipulator reached the switch at the end of travel, the motor did not stop quickly enough causing over tension and snapping the tape. A newer chip, A0166R04, was removed from the spare master arm (received Spring 2017), and installed into the master arm on the blue cart. The test was repeated, and this time the motion selection and drive worked as expected. The situation which previously caused failure was evaluated: slave end fully extended in Z, master end fully collapsed in Z. In this configuration the arm was moved back and forth in the Y direction. No tape failure occurred, and the Z motion tape tension seemed normal. Y motion drive was attempted, and was not possible, as expected. This test was repeated in the opposite configuration (slave end fully collapsed, master end fully extended) with the same results. Full drive speed was used for all tests.
The right side slave arm (with broken Z tape) was then removed and transported to the HCSA. Using the bench mounted locking plate, the broken Z tape was replaced, and a full inspection and cable/tape tensioning was performed. Pete accidentally broke the Z tape on the right side master arm while investigating the failure, which was also replaced.
The other two slave arms were also both inspected, tensioned, and tested in the same way. Then all three were each in turn installed to the master arm #9348 on the blue manipulator transport cart where all mechanical motions and drives were tested (except X, because mounted on cart), the failure situation described above was also tested for all three slave arms.
The left side manipulator was then installed into the wall. It was necessary to remove the lead sheilding on the thru-tube and machine it down approximtaely 0.070" in order for the arm to fit into the wall tube. After installation, the manipulator motions and drives were tested again including the X motion, and the failure scenario situation was also re-tested. Chad used the left side manipulator to remove and re-install the pre-filter mounted on the west side partition wall. He also confirmed that he could reach the east wall electrical outlets and the outlets, gas fittings in front of the window.
The right side slave arm was adjusted so that the Y position was moved 1/2 turn of the shaft drive towards the window (this is the maximum adjustment possible before it hits a hard stop). This was done so that the operator can more easily reach the outlets and air/gas connections inside the cell in front of the window. Because both the master and slave ends protrude further out from the wall compared to the E-HD manipulators for the SHC, this modification makes the NHC manipulators feel a bit more like the SHC manipualtors for the operator. After the adjustment, the right side slave arm was installed. The left side slave arm was removed, adjusted the same as the right side, then reinstalled. The spare slave arm was also adjusted in the same way.
The right side manipulator was evaluated through all mechanical motions. We attempted to remove the A0166R04 chip from the left side, and install in the right in order to try the motion drives, however the pins had been damaged from the previous removal/install, and eventually one pin broke so this was abandoned. CRL will ship us at least three new A0166R04 chips which should arrive in 2-3 weeks.
Upon completion of the work the location of the different arms is as follows: Right side master #9351, Left side master #9348, Spare master #9763, Right side slave #9349, Left side slave #9764, Spare slave #9352
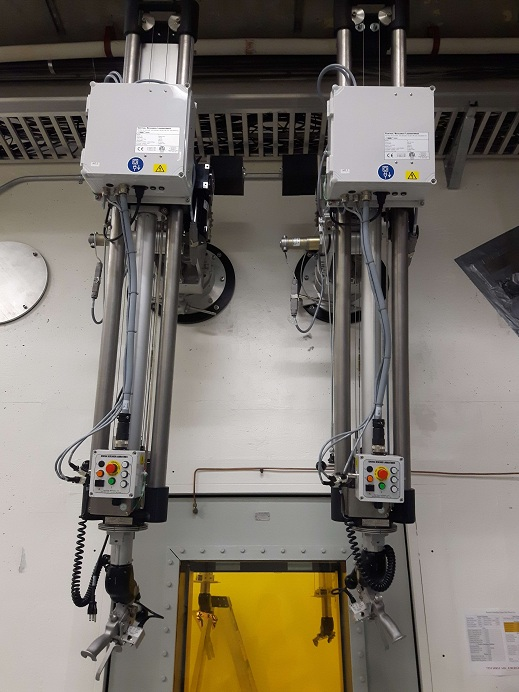

|
Thursday, June 21, 2018, 17:15, Isaac Earle, North Hot-Cell, Development, , , Motorla CP200 radio with throat mic tested in NHC
|
A Motorla CP200 portable two-way radio was tested today for use inside the ISAC hot cells. A High Technology Communications Throat microphone PRO model from Planet Headset was used with the radio. Chad entered the NHC wearing the throat mic and radio under a air supplied hood to mimic real world conditions. Communication was clear with the other person in the NHC service area, in the SHC service area, at various locations on the B1 level, and even with an operator in the TRIUMF Main Control Room.
This testing satisfies RS 104 of the NHC requirements specification (Document-131915, Release 1) |
Thursday, July 19, 2018, 14:22, Isaac Earle, North Hot-Cell, Development, , , NHC diagnostic signals - connector and wiring details
|
Installation of the diagnostic connections between the NHC hot and cold sides has been completed. The cable bundle was prepared by Travis Cave in the electronics workshop with connectors attached at one end only. Metal fish tape was first ran through the conduit from the cold side to hot side, the non-terminated end of the cable bundle was attached to the fish tape inside the cell, cable pulling lubricant was applied, then the cable bundle was pulled through the conduit to the cold side, and the cold side terminations were then made. For future replacement of the cables and connectors the same method should be used, and a minimum of 6m of cable length. Connector details can be found on drawings IRH1765 (hot side) and IRH1767 (cold side). Conduit is 1" trade size PVC type (PO#3041531). Wiring details for each connector are attached below:
9 pin CPC connector:
Pin 1: Brown
Pin 2: Red
Pin 3: Orange
Pin 4: Yellow
Pin 5: Green
Pin 6: Blue
Pin 7: Violet
Pin 8: Black
Pin 9: No connection
All wires 14 gauge.
Connector PN: Amp 211768-1
Cap PN: 208652-1
4 pin CPC connectors:
Pin 1: Coax RG-179
Pin 2: Red (18 gauge)
Pin 3: Black (18 gauge)
Pin 4: No connection
Connector PN: Amp 206430-1
Cap PN: 208800-1
SHV:
Connector: IRH1769 (customized "Kings 1709-1" connector)
USB:
5m long powered USB 3.0 cable
Connector: IRH1770 (customized "TE Connectivity PC4B0100-15NY-1-C" connector)
Cap PN: USBFTV 2 N
Ethernet:
Wires installed in the following order when viewing the back side of connector with PN lettering right-side-up:
Blue |
Blue/White |
Orange/White |
Orange |
Green/White |
Green |
Brown/White |
Brown |
Connector PN: Tyco 1546877
Cap PN: 208652-1
|
Wednesday, August 01, 2018, 09:47, Isaac Earle, North Hot-Cell, Development, , , NHC diagnostic signals and control panel tested
|
On July 30th the NHC diagnostic signals were tested:
- 9 pin CPC: a shorting plug was installed on the hot side - continuity check results were as expected
- 4 pin CPCs: snake camera installed in both hot side connectors with portable monitor on cold side - both connectors worked as expected
- USB: laptop connected on hot side, USB mouse connected on cold side - worked as expected
- Ethernet: laptop connected on hot side, cold side connected to building ethernet port - connection to network worked as expected
- SHV: a shunt was installed on the hot side - a short circuit was measured from the cold side as expected
with no shunt installed the line was Megger tested: 1.63 G-ohms recorded @ 1000V
The control panel switches for the in-cell receptacles were also tested. Each switch (a - d) worked as expected.
On July 31st the gas supply solenoid valves were tested. 60psi air was hooked to each solenoid inlet. With the valve closed there was no air flow. When each push-button or switch was activated air flow was observed through the correct solenoid. |
Wednesday, September 12, 2018, 15:22, Isaac Earle, North Hot-Cell, Development, , , NHC air and gas supply lines - test and leak check
|
Testing was completed today on the NHC air and gas supply lines. For each line a Staubli plug was installed on the fitting inside the hot cell, the line was charged with compressed air (50psi for gas lines #1, #2, and #3; 100psi for the air lines #4 and #5). All connections inside and outside the cell were checked for leaks using Snoop including connections for the solenoid valves. No leaks were found. Correct operation of the solenoids was confirmed as well as correct plumbing (no lines crossed). |
Wednesday, September 12, 2018, 15:30, Isaac Earle, North Hot-Cell, Development, , , Installation of NHC operator-level lighting completed  
|
Installation of of operator-level lighting in the NHC was completed today according to drawing IRH1801. 2" x 2" Panduit was mounted to the wall on aluminum brackets to support the power cables. These lights can be replaced remotely by unplugging the power cords using the manipulators, lifting the cable out of the Panduit with a hooked pole tool through the manipulator slave end removal roof hatch, lifting the light fixture off the support bracket with the pole tool, then installing a new fixture in the opposite order. This RH procedure will be tested at a later date as part of NHC commissioning.

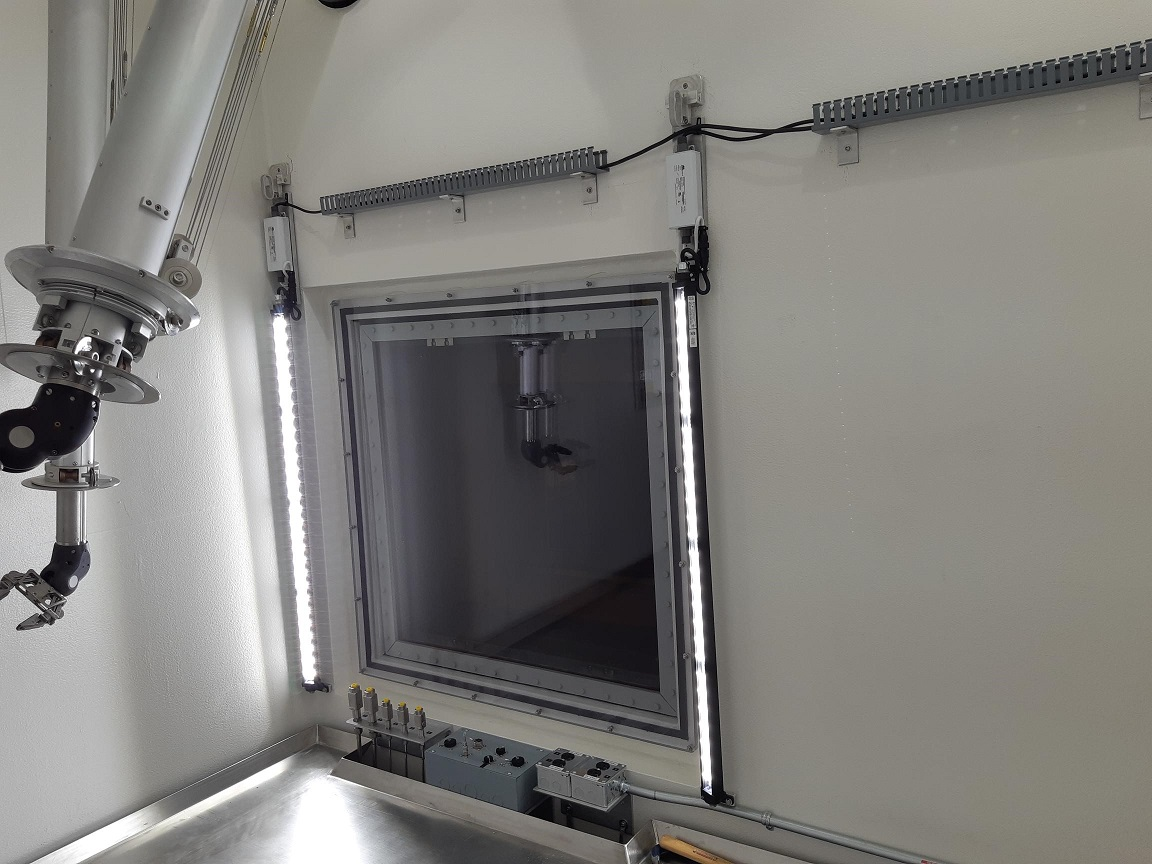
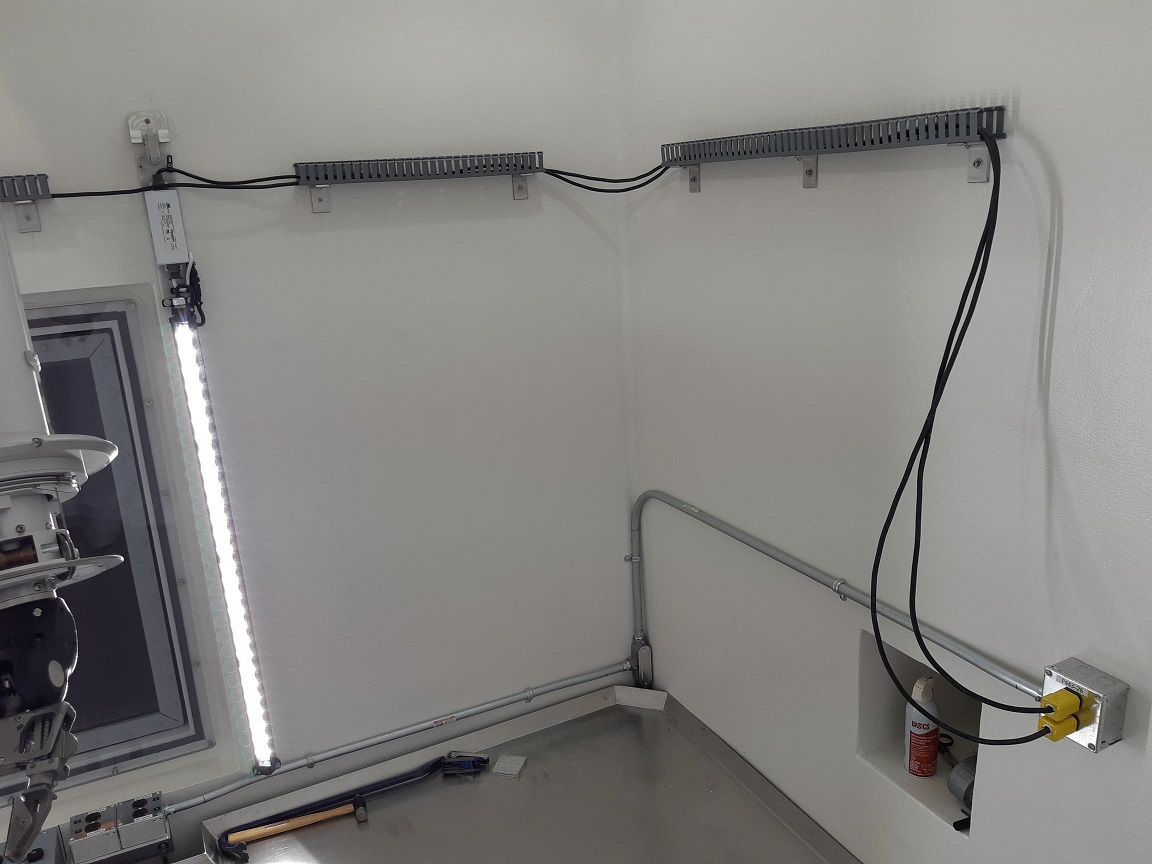
|
Thursday, September 13, 2018, 16:57, Isaac Earle, North Hot-Cell, Development, , , NHC grounding and mili-ohm testing
|
The following equipment has been connected to the building ground located in the Target Hall by the TCS using 1/2" flat bonding strap:
- NHC roof structure
- NHC/TCS partition wall
- NHC work table
The following equipment has been connected to the building ground by connecting to the work table inside the NHC using 1/2" flat bonding strap:
- Air and gas supply line mounting bracket inside NHC
- Receptacle box mounting bracket inside NHC
- Diagnostic signal box mounting bracket inside NHC
The resistance between the following locations and the copper grounding plate located at the base of the NHCSA north wall were measured. The resistance of the wire used was 258.10mΩ, and has been subtracted from the following results.
Measurements taken in NHCSA:
- Control panel below viewing window (base plate of box): 4.67mΩ
- Oil window frame (bare metal drain valve): 55.34mΩ
- Left manipulator (ground plate near e-stop button): 73.46mΩ
- Right manipulator (ground plate near e-stop button): 202.58mΩ
- Air and gas supply line mounting bracket: 40.68mΩ
- Diagnostic connector box: 12.15mΩ
- Steel conduit for 110V supply to hot cell interior: 4.81mΩ
Measurements taken inside NHC:
- Work table: 4.51mΩ
- Pre-filter bolted to partition wall: 4.84mΩ
- Table hatch lid: open load
- Left manipulator thru tube: 515.8mΩ
- Right manipulator thru tube: 342.0mΩ
- Left manipulator (slave boot plate bolt): 885.9mΩ
- Right manipulator (slave boot plate bolt): 1444.0mΩ
- Grounding strap for air/gas plate: 4.84mΩ
- Outside of SHV connector on diagnostic signal box: 4.56mΩ
- Exterior of 110V electrical conduit: 3.88mΩ
- Male Staubli connector for 1st gas line: 53.7mΩ
- Welded stud for window cover panel: 6.06mΩ
- Grounding strap for partition wall: 4.39mΩ
- Roof structure (measured inside un-painted bolt hole): ~0mΩ
- Stainless steel module flange: ~0mΩ
Dedicated grounding will be added in the near future for the oil window frame and the manipulator thru-tubes. Testing will then be repeated for those items.
Dec 18, 2018 update:
The oil window frame and both manipulators (where they bolt to the thru-tubes) were connected to the building ground using 1/2" flat bonding strap connected at the cold side of each piece of equipment, and running to the grounded copper sheet located in the NHC service area at floor level. The connection is made inside the electrical racks located directly west of the NHC operator area on the cold side. This work was done by Travis Cave in October 2018.
Mili-ohm testing for these items has not yet been repeated.
Jan 14, 2019 update:
Grounding was added from the metal plate near the e-stop button on the master arm of both manipulators. The same 1/2" flat bonding strap was used which was tied into other bonding strap which runns to the grounded copper sheet in the NHCSA.
Mili-ohm testing was repeated for the following items:
- Oil window frame (bare metal drain valve): 13.6mΩ
- Left manipulator (ground plate near e-stop button): 16.1mΩ
- Right manipulator (ground plate near e-stop button): 16.5mΩ
|
Thursday, November 22, 2018, 14:38, Isaac Earle, North Hot-Cell, Development, , , NHC design approved by High Voltage Engineer
|
To satisfy RS 101 from the NHC requirements specification (Document-131915) Tomislav Hurskovec was consulted regarding high voltage safety. After a verbal discussion on various aspects of the NHC design he confirmed that the design satisfies high voltage safety concerns.
A copy of his confirmation e-mail is attached in PDF format.
|
Monday, December 10, 2018, 15:31, Isaac Earle, North Hot-Cell, Development, , , NHC remote connection testing with manipulators
|
The following tests have been successfully completed using the NHC manipulators:
- Ventilation pre-filter (mounted on the NHC/TCS partition wall) removed and re-installed using the manipulators
- Electrical plugs (two total) for operator-level LED lighting located on east wall of cell interior plugged in, and un-plugged using the manipulators
- Electrical plug inserted into and removed from each of the 120V outlets (four total) located in front of the viewing window using the manipulators
- All diagnostic service connections removed and reinstalled using the manipulators (six total, see IRH1765)
- All Staubli air and gas connections removed and reinstalled using the manipulators (five total, see IRH1749)
These tests were performed at various different times over the last several months by Isaac Earle and/or Chad Fisher. |
Tuesday, December 18, 2018, 11:13, Isaac Earle, North Hot-Cell, Development, , , NHC manipulator slave-end swap, RH test, and various other work
|
The following North Hot Cell work was completed over the last week under work permit I2018-12-12-1:
Thurs Dec 13th:
- Prepared master side according to removal manual (noticed screwing in the right side locking screw was not as smooth to go in as normal; left side was smooth like normal)
- Removed manipulator roof block and set down in yellow frame (required some stacked wood to prevent light from bottoming out)
- Removed steel side plates in NHC manipulator hatch
- Removed the slave end (SN: 9764) – noticed “Right Elevation/Twist Coupler” off of vertical by around 30 degrees
- Wrist elevation of removed slave end was not locked, lifted it slightly and this brought the coupler to the vertical position and it locked with a click
- Suspected the thru-tube also would be misaligned, confirmed by inspecting visually in hot cell (Unsure why this misalignment occurred considering we followed the removal procedure properly. One theory is that when we accidentally left the timing screw in the master side handle cable drum last time it may have caused things to get a little out of alignment)
Friday Dec 14th:
- Un-did the right side locking screw on the master
- Then could turn coupler on the thru-tube to the vertical position from within the hot cell
- Re-locked the right side locking screw (this time it went in smoothly)
- With all couplers on thru-tube vertical we then installed the replacement slave (SN: 9352) as per instructions
- For future slave end changes should use some sort of long chain or sling instead of having the auxiliary crane hook block within the hatch (some sort of T-hook type lift feature replacing the bail may work better as well)
- Evaluated the manipulator: seemed to be working normally, Chad tested plugged in LED lamp plug and also opened and closed the work table hatch
- Noticed Z motion tape on slave end loose when fully extended in Z (nice and tight when retracted) – this seems to be normal
- Confirmed manipulators can reach all surfaces of the table
- Then tested remote handling of LED light fixtures from the Target Hall using pole tools through the manipulator roof hatch
- Started with both LED light plugs un-plugged
- Used 9’ standard beam lines RH pole tool (this worked fine, but 10-12’ would be better)
- Curved hook end attachment
- First lifted cables out of all cable tray sections (the wall mounted Panduit)
- Then removed the East light fixture assembly (IRH1800) - lifted from designated lift loop (IRH1796) – This went smoothly
- Hoisted up into the Target Hall, then lowered back down to re-install
- To reinstall had to hook the assembly at a lower point due to flex of the pole from the weight of the assembly (hooked just below the ballast for installation). Using this method reinstalling the fixture went smoothly. I will update the design to move the designated lift point (or add an additional one) at this location.
- Once the light fixture was on the bracket, replaced the cables in the cable tray using the pole tool. The final section on the east wall before the outlets was a little tricky, but by viewing and reaching from the north-west corner of the hatch it was do-able
- Confirmed visually that remote removal and installation of the west fixture can be done using the same procedure as the east
- Replaced lamp block (stored lifting hardware for hatch side plates above block, below hatch cover)
Monday Dec 17th:
- Left side slave-end boot was installed as per manual instructions. It was done with two people inside the cell this time which went much smoother than just one last time (the boot was not installed on the slave prior to moving it into the hot cell because we wanted to inspect the tape and cables after installation and the boot would prevent that)
- The condition of both boots was checked. Both appear to be in new condition with no signs of degradation. The material seems pliable and strong.
- Chad Fisher, ISAC Hot Cell Operator, checked the light level from the cold side of the hot cell and confirmed that it is acceptable. However, without the operator level LED lighting it was too dim.
Tuesday Dec 18th:
- Lift bails for both manipulator slave ends set to farthest north position which results in face that mates with thru-tube to be close to vertical when hanging from lift bail
- Work table, stairs, entrance floor area, pre-filter assembly, tool port, window cover, and hot side service connection panel vacuumed and wet wiped to remove dirt and dust.
- NHC inlet damper (located in Target Hall) adjusted to set NHC depression to around 1.05”wc (the NHC damper is currently not responding to the NVCS and needs to be investigated and repaired by Controls Group and/or Mechanical Services)
|
Friday, January 04, 2019, 14:38, Isaac Earle, North Hot-Cell, Development, , , NHC cameras tested  
|
The NHC module support flange cameras (4 total) as well as the NHCSA camera were tested today and confirmed to be working properly. All cameras were angled and focused properly, and displaying clearly on the monitors in the ISAC RH Control Room. Photos of the control room monitors are attached below.
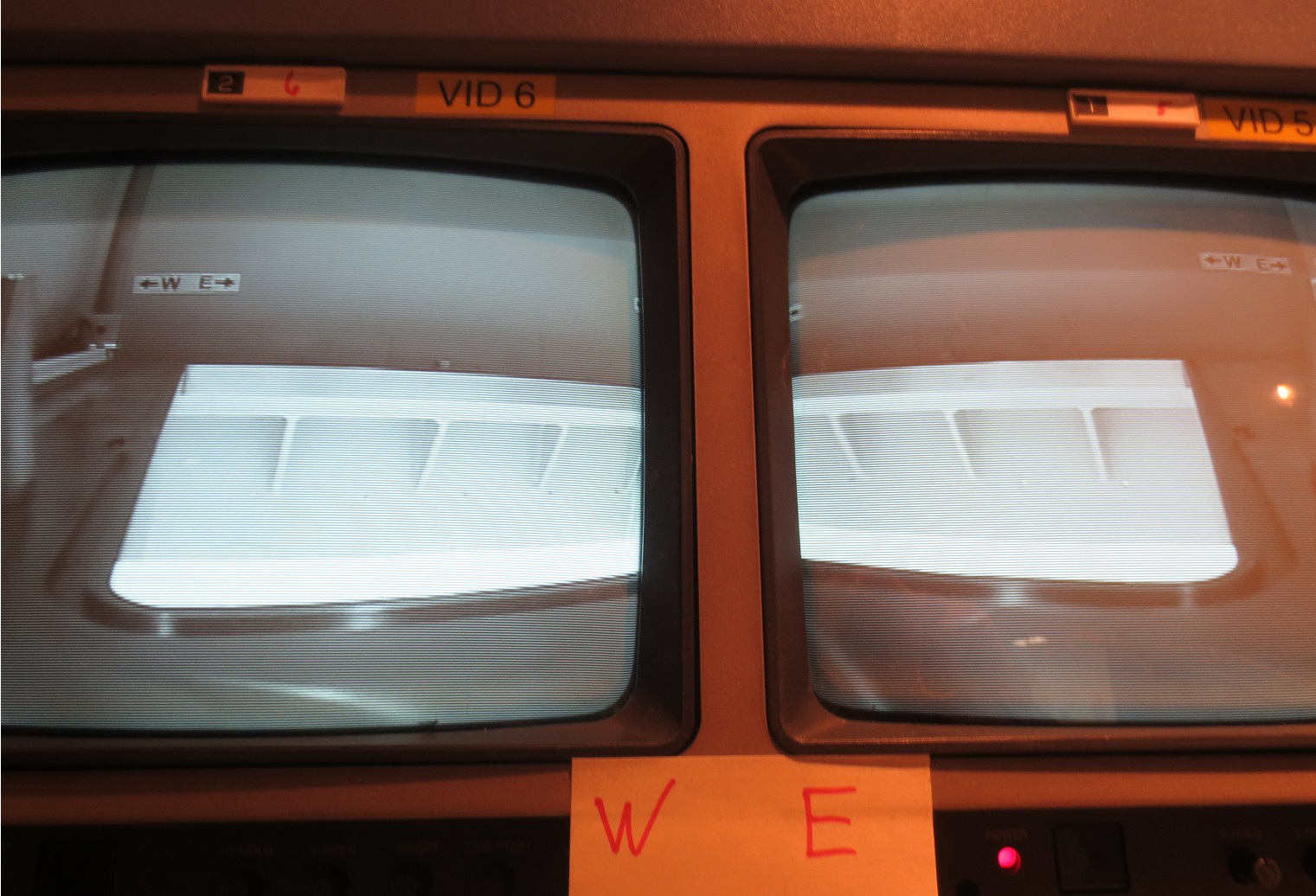
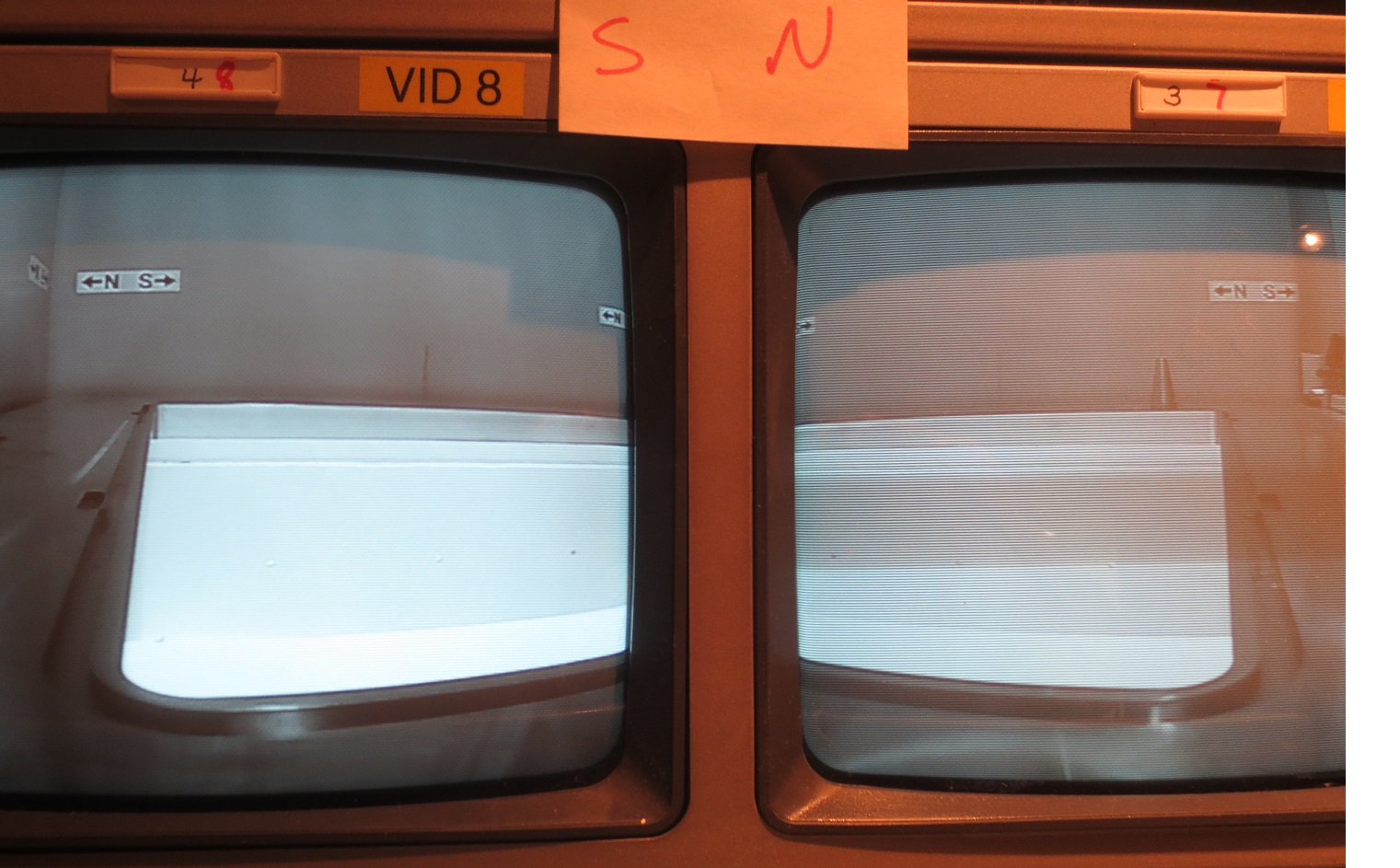
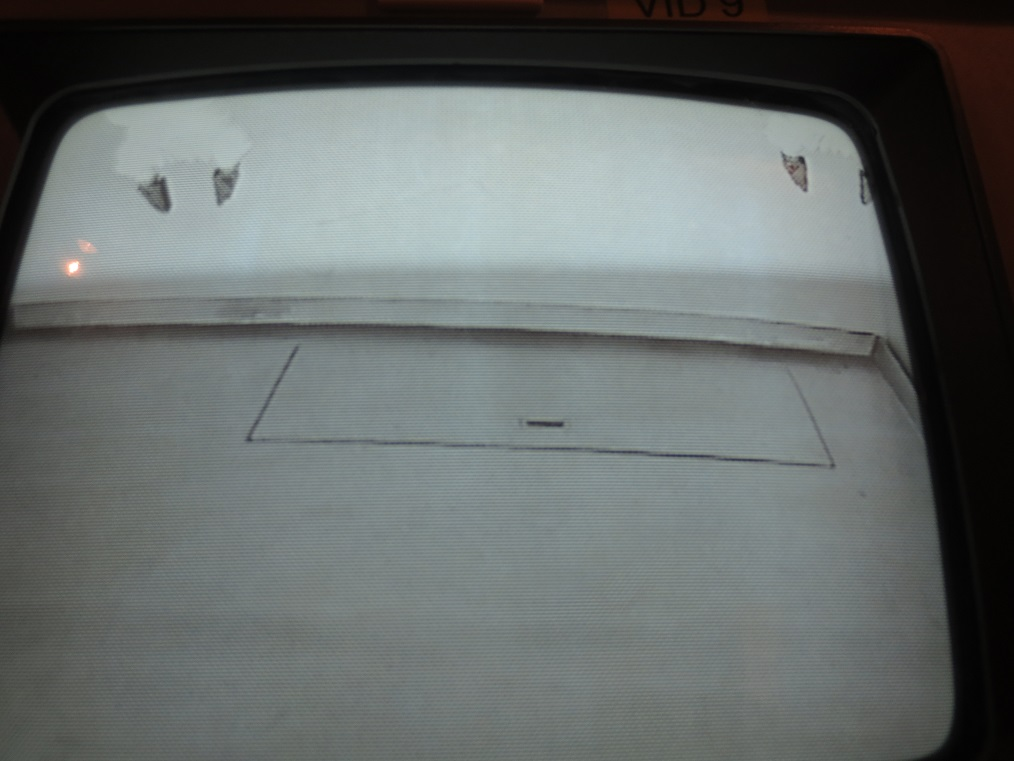 |
Friday, January 11, 2019, 13:59, Isaac Earle, Safe Module Parking, Development, , , SMP motor selection decision
|
SMP drivetrain design work is currently underway. Alejandro has selected a suitable 1200:1 reducer which will give a vessel rotation speed of 0.21rpm with a 1725rpm motor (deemed sufficiently close to the SHC rotation speed of 0.17rpm). The reducer however is only rated for 0.33hp, and Allon's analysis recommended we use a motor of at least 0.4hp
From his calculations the expected power required to turn the loaded vessel is 0.2hp (see Document-161943, p3). The higher figure of 0.4hp in his final recommendations comes from the power rating of a 40 tooth sprocket (the driver sprocket) with a No. 50 roller chain operating at 10rpm (the lowest speed shown on the table) - meaning this driver sprocket arrangement can handle up to 0.4hp. We discussed this on the phone on January 4th and agreed that a 1/3hp motor could be used which will match the reducer Alejandro selected, and will supply sufficient power given that calculations indicate only 0.2hp is required.
Once the vessel is installed in the shield box a test will be performed to determine the actual torque (and power) required to turn the vessel. If the value differs significantly from the calculated value the design will be revisited. |
Friday, January 18, 2019, 10:26, Isaac Earle, North Hot-Cell, Development, , , NHC sealing improvements and repeat of RH test for LED lights
|
The following NHC development work was completed under WP I2019-01-09-4:
- Location of RH feature on operator level LED lighting updated to match IRH1800 Rev B design
- Remote Handling test of the LED fixtures was repeated using a 9' pole with hook attachment through the manipulator slave hatch from the Target Hall: both LED fixtures were removed and reinstalled successfully with relative ease
- Tool port seal replaced to address an audible air leak: the 1/4" foam seal was removed and replaced with adhesive backed 5/8" wide hollow foam rubber seal (McMaster Carr PN: 93085K81). Prior to the change DPG4 was at 0.63"wc, after the change wit was 0.73"wc with all system variables constant.
- NHC manipulator access block seal was replaced, likewise to address an audible air leak: the 1/4" foam seal was removed and replaced with adhesive backed 1/2" thick BunA-N rubber strip (McMaster Carr PN: 9023K85). DPG4 was at 0.94"wc prior to the change, and 1.07"wc after with all system variables constant
|
Monday, January 21, 2019, 16:27, Isaac Earle, North Hot-Cell, Development, , , NHC in-cell camera wired to right side monitor
|
The NHC right side monitor has been wired to display the signal from the in-cell camera. This was tested using a snake camera on both of the CPC-4 connectors.
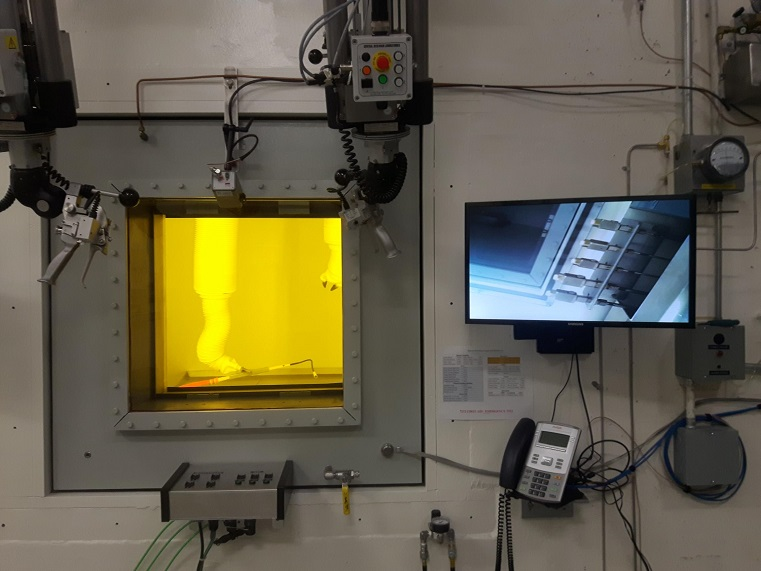
|
Thursday, January 31, 2019, 14:16, Isaac Earle, North Hot-Cell, Development, , , NHC grounding approval
|
Franco Mammarella was consulted regarding electrical grounding of the NHC design (RS103 of Document-131915). After discussing the design, and having grounding inspected by Randy Boehm, Franco approved the design and advised that the grounding system should be inspected periodically. This task has been added to the Remote Handling inspection index on an annual schedule. A PDF copy of the e-mail correspondence with Franco is attached. |
Monday, February 11, 2019, 10:26, Isaac Earle, Safe Module Parking, Development, , , SMP shield box and vacuum vessel moved to Target Hall 6x
|
On February 8th the SMP shield box (IRH1675) and the vacuum vessel (IRH1806) were both raised from a horizontal to vertical orientation in the ISAC-1 Experimental Hall. Hamilton "Mini-Mite" S-MM2-43FS caster wheels were then installed on the base of the shield box and it was lowered down the hatch to the B2 level. The vacuum vessel was then lowered into the shield box, supported by the rollers, as designed. The shield box and vessel combination were then moved south along the steel plated floor until positioned under the hatch leading to the Target Hall. Movement along the floor was achieved by pushing the back of the vessel with an electric fork truck and pulling from the front with a cable winch attached to a plate mounted in the floor in the SHC service area, centered east/west between the Ante Room doors. The fork truck alone was sufficient to move the assembly on the smooth section of the plates, but the winch was needed on the section paitned with textured grit. The vacuum vessel was then lifted into the Target Hall and placed in a temporary storage location in the silo area. The shield box was then lifted, casters removed, and then lifted up into the Target Hall. It was a very tight fit with the tubing which has been installed on the SHC and NHC ducting for the new flow meters, but the move was completed without causing damage. The shield box was placed on the B2 level in the Target Hall where some final tapped holes will be added on the exterior before moving to the final installation location.
|
Thursday, February 21, 2019, 15:10, Isaac Earle, Safe Module Parking, Development, , , Seismic requirements for SMP
|
Dragan Mitrovic, TRIUMF structural engineer, was consulted earlier this week regarding seismic requirements for the SMP assembly. Installation location, overall dimensions, total weight, and the center of mass for assembly IRH1670 were provided to him by e-mail. On Feb 20th he communicated verbally that he had analyzed the assembly for seismic loads, and concluded that this equipment does not require anchoring or any other form of seismic restraint.
Update (May 30, 2019): Confirmed with Dragan that the approach he used for analysis was that specified in the BC Building Code (both 2012 edition and updated 2018 edition). |
|