Tuesday, May 14, 2024, 15:27, Carla Babcock, ITE, Development, TM3, UCx#44, TM3 conditioning and testing in ITE
|
Tuesday, May 14, 2024, 10:26 :
Ramping up bias/EE/EL on ITE - will see if the HV cage in the pit can hold 60kV or not.
At around 50kV the bias read current starts to get jumpy. Doesn't look like its an issue for the voltage, but definitely instability increases.
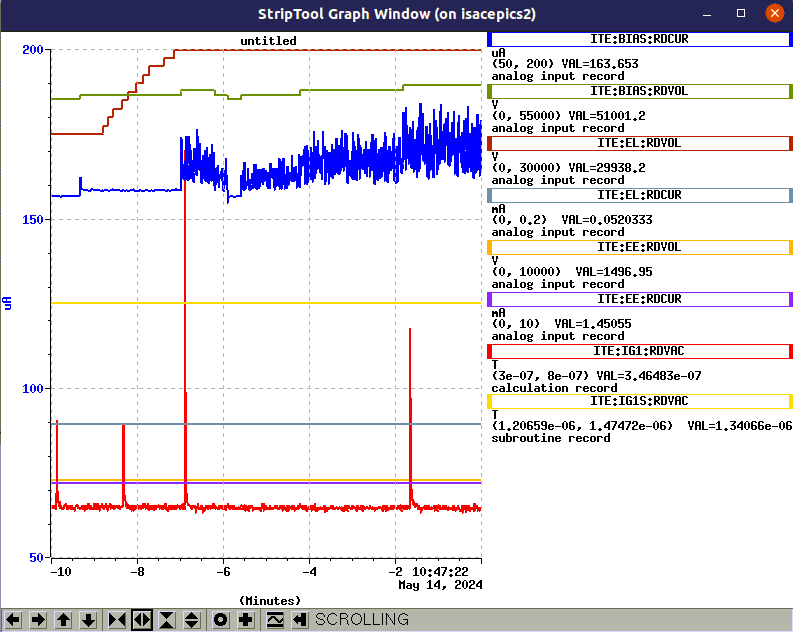
Occasional sparks seem to increase the EL current significantly...
David heard some sparks in the target hall. Looks like from heat shield feed through to the top of the cage. Several sparks heard in the TH also changed the einzel lens draw current significantly. These feethroughs are not far from each other so could be related.
Apparently the sparking also tripped off all the optics and heaters in ITW, by changing the state of the water flow interlock. Interesting and not seen ever before. Will test again with the cage off, rather than risk tripping ITW again.
Tried ramping up the voltage on just the EE. Seems the limit is 7kV - at that level it gets sparky and unstable. Should be investigated (should hold 10kV) but not critical for module function.
Wednesday, May 15, 2024, 10:05 :
HV cover was removed this morning and the MAA was locked out.
Started ramping things up, was very easy until around 58kV. At 59.5kV a spark tripped off the EL. Canbus controller had to be power cycled to fix it. Bias current is much more stable in this configuration.
Ramped up again while listening from the TH to see if it was sparking outside. Went slowly to 60kV (left EL at 29kV) and didn't see any outside sparks in the first 10 mins, couple sparks in vacuum. But after 15 mins a spark seems to have fried the EL canbus card. We were not in the TH so not sure if it was on the outside or not.
After 2 hours a spark tripped off both ITE and ITW. Looks like it makes a water interlock go bad momentarily, but after the trip the interlocks seem fine.
Tuesday, May 28, 2024, 16:41
Running TM3 at any voltage in ITE produces fairly destructive sparks. There are not many but so far they have tripped off all optics in ITW, the water flow interlocks (later forced on to prevent this), the EL (generally comes back but killed the canbus card once), destroyed two vacuum gauge controllers, and may have contributed to the cathode short on ITE-TM3-UC44-LP-FEBIAD.
The conditioning process seems to go as planned, but the occassional inevitable spark still trips things, which is making it difficult to run stable.
Will continue with regular HV conditioning to see if this helps. Control over the current limit on the ITE:BIAS supply would also help, but seems a complicated thing to add according to Roberto.
TM3 sat fine at 53kV overnight and at 58kV for several hours. The EZL trips off maybe once every 2-3hrs or so, which is not ideal but liveable. This was with the TGHT and CHT power supplies forced, so not sure if we would know if they would have tripped...
CONCLUSIONS:
- TM3 has been commissioned for beam delivery after one week of delivery of UF to TITAN using a FEBIAD ion source in anode bias mode. Cathode mode was also used, so all functionality of the target except IGLIS current/voltage delivery through the mutlipin has been tested successfully.
- TM3 still requires commissioning at high voltage with protons to be considered fully commissioned, this will be done July 2 2024 due to problems with the cyclotron.
|
Thursday, September 08, 2016, 16:28, David Wang, Conditioning Station, Repair, TM3, , TM3 blue insulators have been replaced.
|
All TM3 blue insulators except Gas,EL, and 60 KV common on top of the module have been replaced with new designed insulators. The new blue insulator for gas line need to be modified to fit for the bent on the gas line. EL, and 60KV common blue insulators were replaced during last time TM3 refurbishment so they are relative new, and not replaced this time. All seals related to the blue insulators are changed to new seals. The o- r-ing surfaces for o-ring 221 inside the new insulators are rougher than old parts. The module top need to be leak checked. |
Friday, March 07, 2014, 12:45, David Wang, ITE, Standard Operation, TM3, , TM3 and ITE air to vacuum leak check and TM3 water lines helium test.    
|
With TM3 located in ITE, All air to vacuum seals on ITE primary and secondary vacuum vessel have been leak checked with leak detector hooked directly on the TM3 service cap.The base LR :00xE-9atm.cc/sec. The ITE IG1 was 1.6xE-6 torr which was good. No leak has been found during the checking.Also, the TM3 water lines(except HS) had been pressurized with 70 psi helium on each for 2 minutes. There was no response during the test. The ITE and TM3 are good on leak checking.See attachment pictures |
Friday, June 14, 2024, 11:55, David Wang, South Hot-Cell, Standard Operation, TM3, UCx#44, TM3 UCx#44 after operation electrical check at SHC
|
TM3 UCx#44 after operation electrical check at SHC . see attachment.
Carla: Looks like the short on the cathode observed while trying to operate the FEBIAD in cathode-bias mode is still there. Will do investigations in the hot cell during disassembly. |
Monday, October 20, 2014, 09:13, David Wang, Conditioning Station, Development, TM3, , TM3 TP2 failed
|
TM3 TP2 stopped working this morning at 4:00 AM. I tried to start it but failed. On normal start mode , It could not pass 6K RPM. On soft start mode , the pump cant pass 17KRPM. Talked with Anders, We are not going to replace this pump since we are not going to run this module for a while. I will stopped all vacumm pumps on CS and TM3 this morning. |
Wednesday, April 24, 2013, 11:48, chad fisher, South Hot-Cell, Repair, TM3, , TM3 Source Tray Removal
|
Work on TM3 source tray removal started at 10:40 am today.
The containment box has been removed, and disconnection of the optics tray is 90 complete.
Pictures can be found in the April Refurb Work Folder in the tm3 rev3 refurb pictures folder. |
Tuesday, April 30, 2013, 07:47, chad fisher, South Hot-Cell, Repair, TM3, , TM3 Source Tray Removal
|
The source tray has sucessfully been removed from TM3.
I will put a report in the TM3 rev 3 docushare directory as there were some items of note during this procedure. |
Thursday, August 08, 2024, 13:58, David Wang, South Hot-Cell, Standard Operation, TM3, SiC #46, TM3 SiC#46 electrical check at SHC with target on (After operation)
|
ABCD is short to 60KV bias. Othjer are ok. see attachment.
Found afterwards that this short was due to sparking through the multipin wire insulation where the wires pass behind the TBHT block "C". See fault 17265. |
Wednesday, April 26, 2017, 17:55, Aurelia Laxdal, South Hot-Cell, Repair, TM3, no target, TM3 Schedule updates at the South Hot Cell and CS 
|
Please see TM3's Updated Schedule (the current schedule) at the SHC and TCS.
For the record I am uploading TM3's Initial Schedule at the SHC and TCS. |
Tuesday, July 02, 2013, 09:37, chad fisher, South Hot-Cell, Development, TM3, , TM3 Rev.2 Source Tray Disposal
|
Tm3 Rev.2 source tary has been transfered to the vault tunnel storage. |
Thursday, August 22, 2013, 19:38, Grant Minor, South Hot-Cell, Repair, TM3, , TM3 Rev 3 source tray - water blocks connected and torqued 6x
|
After a great struggle with the water block jigs, the TM3 source tray was finally advanced fully into the service tray and all water blocks were connected and torqued to spec in the hot cell by Chad Fisher.
Notes and description of problems encountered during the installation:
- The water lines for the optics tray interfered with the module-side water block jig, and had to be bent out of the way to clear while advancing the tray (see attached photos)
- The water block jig on the source tray side was too low relative to the module side, and had to be eventually unbolted completely from it's mounting bracket in order to raise it up into alignment
- A piece of aluminum plate was placed under the jig, and the pneumatic table was raised in order to move the jig upwards
- After many repeated attempts to engage the blocks by pressing the jigs together, it was discovered that some of the blocks had rotational misalignment with their respective counterparts on the module side, preventing the pins from engaging properly
- By looking through the bolt holes on several of the blocks, it was possible to determine which direction they had to be rotated
- Chads polishing tool was used to apply some torque to rotate the source-tray-side water blocks slightly so proper alignment of the pins could be achieved
- See the attached photo which indicates which blocks had to be rotated (blocks 5, 6, 9, 10, and 11)
- The blocks had the bolts installed and were also torqued in the numbered order shown in the attached photo
Next steps are to remove the water block jigs, re-connect the loosened brackets for the remaining water lines (entrance window, optics tray), re-install the containment box and associated VCR connectors, video inspect, and leak check. |
Tuesday, August 27, 2013, 17:18, Grant Minor, Conditioning Station, Repair, TM3, no target, TM3 Rev 3 source tray - prelminary leak check results at CS 
|
David Wang started a helium leak check on TM3 at the CS this morning.
David will create an e-log once his check is complete, but here are the preliminary results:
- target oven +/- OK
- mounting support plate OK
- ionizer tube heater +/- OK
- extraction electrode OK
A large leak was found in the heat shield circuit:
- The module pumped down with the leak rate stabilizing at 4.8xE-9 atm.cc/sec
- 60 psi helium was applied to the heat shield fitting on the right side of the Y-shaped connector (see attached sketch, each side of the "Y" is separated by a face to face metal contact only, i.e. no o-ring seal separates supply and return water)
- The maximum leak response was detected in 10 seconds, with base pressure rising from 2.0E-2 torr to 2.8xE-2 torr
- The helium was vented from the line by using an allen wrench to open the valve on the water quick-connect (see attached photo)
- The module continued pumping down, and after some time, the allen wrench was used again to open the valve, but air rushed inside, indicating vacuum was being drawn inside the water line through the leaking interface
- As the module continued to pump, this vacuum vent air rush inside the water line could not be reproduced by opening the valve again with the allen key
The module is currently pumping down at the Conditioning Station. We will leak check the remaining lines tomorrow with whatever base leak-rate we have achieved, and then move TM3 to the Hot Cell for further diagnosis. |
Friday, August 23, 2013, 18:32, Grant Minor, South Hot-Cell, Repair, TM3, , TM3 Rev 3 - steerer wire broken from connector on module side    
|
While continuing on the TM3 Rev 3 source tray installation, Chad noticed today that one of the steerer wires is broken and has come out of the thermocouple-style connecter block (see attached photos).
From drawing ITA2826 (Rev D02 attached) it is likely that this is for either the "upper" or "right side" steerer plate. |
Monday, August 26, 2013, 18:22, Grant Minor, South Hot-Cell, Repair, TM3, , TM3 Rev 3 - all connetions made except steerers, IMG, and entrance window 8x
|
Today Chad finished making all connections to the new source tray, except for:
- steerers - broken wire, must be repaired at a later date
- IMG gauge - bracket required, old bracket thrown out with previous tray by accident, see ITA3301, must be installed at a later date
- entrance window - the window lines on module side were left blanked-off for leak checking, containment box must be removed in the next few days to complete steerer repairs so these lines were not connected to save work from having to be repeated
The containment box was replaced, and TM3 was moved to the CS for pump-down and leak checking (see other e-log). David reported at 6:15 pm that the turbos were turned on at the CS and the vacuum looked normal (so far).
As stated above, Chad realized today that he had thrown out the old IMG gauge bracket with the previous source tray, and a new one must be manufactured. The assembly is described by ITA3301. Three components must be manufactured (ITA3302, ITA3303, and ITA2673). A stock split-ring clamp for ITA2673 (MDC #716001) was graciously donated by Dimo Yosifov. Grant Minor submitted a work order to the machine shop today for 2 each of ITA3302 and ITA3303. |
Thursday, June 21, 2012, 14:30, chad fisher, South Hot-Cell, Repair, TM3, N/A, TM3 Refurbishment Start
|
Started refurb of TM3.
Planned activities:
Inspection
Water line blank off
Started 1:00pm
- Video inspection before containment box removed - noticed discoloration on top right (if looking from h/c window) 4" insulator
- Containment box cover removed
- Containment box removed
As I am much older, wiser and handsomer then last time I removed this style of box, I realised there was a better, safer procedure for the removal...I will be updating the doc. accordingly.
End 2:25 pm
|
Wednesday, April 24, 2013, 14:09, chad fisher, South Hot-Cell, Repair, TM3, , TM3 Refurbishment E.O.D.
|
Optics tray has been removed from module.
Waterblock jig installation has commenced. Of note, jig installation on TM3 has proven more dificult than the previous installation on TM2. Many of the waterblock assemblies are skewed (not perpendicular to plane that they should be...perpendicular to).
As I am away tomorrow, jig installation willl continue on Friday. With the source tray hopefully being removed on Monday. |
Monday, June 25, 2012, 07:53, chad fisher, South Hot-Cell, Repair, TM3, N/A, TM3 Refurb. Work
|
On Friday, June 22 the following work was carried out.
- Further inspection of the source tray.
- Testing of existing tray removal and installation tool...it works fine, there was just a specific method for proper coupling to the target module. There was no documentation for this tool, so it took a little bit of insight with the drawings and a little trial and error. A document should be written for this tool so its proper use is documented...I will do this.
- Blank-offs installed on heat shield water lines.
- New gaskets installed on window water lines.
- Containment box re-installed.
Pictures can be found at: http://documents.triumf.ca/docushare/dsweb/View/Collection-8639
|
Tuesday, April 16, 2013, 11:20, chad fisher, South Hot-Cell, Repair, TM3, , TM3 Referb. start 
|
Front containment box cover has been removed and heat shield circuit blank offs removed in preparation for installation of dummy target.
image #1 - initail view after front panel removal.
image #2 - Heat shield circuit blank offs removed.
Ready for baseline electrical tests and 9 pin cinnector tests. |
Wednesday, April 12, 2017, 12:51, David Wang, South Hot-Cell, Repair, TM3, , TM3 Ram readings @ SHC
|
We have a ram installed on SHC pole which is 0.5 meter to module shielding block surface. the readings we got today during TM3 move:
at containment box center (highest reading): 3.14 msv/hr.
at bottom of shielding blocks: 960 usv/hr.
at 1/4 of shielding blocks height from bottom :700usv/hr.
at 1/2 of shielding blocks height from bottom: 340usv/hr.
at 3/4 of shielding blocks height from bottom:140u/sv/hr.
The Ram is behind the pole and measured the surface which is 90 degree right side of that opened service tray side. |
Wednesday, June 20, 2012, 11:39, Grant Minor, South Hot-Cell, Development, TM3, N/A, TM3 Planned Activites at South Hot Cell Jun 20 to 29 2012
|
(Copy of e-mail correspondence sent June 20th 2012)
After some discussions this morning I’ve decided on the following best path forward for TM3 at the Hot Cell leading up to the Canada Day long weekend.
General Goals:
- Blank-off TM3 water line terminations (coil, heat shield, water-cooled window)
- Test sliding tray removal tool to determine fit on TM3 chassis
We will skip the Conditioning Station leak tests and return TM3 directly to a silo for the following reasons:
- We will have a visitor next week and this will impact Chad’s time available to do Hot Cell work
- Helium pressure leak checks on the blanked-off circuits are only one small portion of a large set of diagnostic tests (leak, electrical, HV, etc.) that must ultimately be performed on TM3 to determine its fitness. This full set of tests must be carefully documented in a procedure and executed systematically when there is adequate time at the CS to do all of them, with results recorded. There is currently not adequate time for this work between now and Canada Day.
- If we were to detect a leak from one of these tests, it would not tell us anything about where the leak is in that given circuit (there are multiple possible points). The service cap would have to be opened regardless, which we don’t have time for.
- The aforementioned bullets above lead me to conclude that the extra work required for two module moves for one set of partial leak checks is not a value-added exercise: In other words, the module will have to go back to the CS, regardless of what we do over the next week for more tests. The time savings of trying to squeeze it in next week are really negligible and it makes for a tight schedule for not much benefit.
Chad: Please prepare a detailed work plan for your hot cell jobs including a list of the tools required and what leak checks you will do specifically after you have installed the blank-offs. You may refer to existing procedures if you already have these written. I would like to review this plan and I am expecting that an e-log will be filed daily and this work plan should be referred to as an attachment.
Proposed Schedule Jun 20 to 29
Wednesday Jun 20 (1 working day)
- Setup for TM3 move from Silo to HC (Travis, David)
Thursday Jun 21 (1 working day)
- TM3 moved from silo to HC (Travis, Don Dale, David)
Friday Jun 22 to Wednesday Jun 27 (4 working days)
- Chad performs the following HC work on TM3:
· Removes containment box
· Installs water-line blank-offs
· Checks Sliding Tray Removal Tool Fit
- Vacuum leak checks of blanked-off lines at the HC (Chad, David, VG)
- Chad buttons up TM3
- In parallel - David performs block moves as required
Thursday Jun 28 (1 working day)
- TM3 moved from HC to Silo (Travis, Don Dale, David)
Friday Jun 29 (1 working day)
- Contingency
RH Group: Please move ahead with the work as outlined above. Please comment if you have any concerns or proposed changes to this plan. Thanks very much to all for your assistance,
Grant
-------------------------------------------------
Grant Minor, M.A.Sc., P.Eng.
TRIUMF Remote Handling Group Leader
Nuclear Engineer
4004 Wesbrook Mall, Vancouver
BC, Canada, V6T2A3
gminor@triumf.ca
(604) 222-7359
http://www.triumf.ca/profiles/4557
------------------------------------------------- |
|