Monday, October 05, 2015, 10:19, Anders Mjos, Conditioning Station, Maintenance, , , Chiller maintenance
|
will be performed Tuesday October 6th
Tuesday, October 06, 2015: Maintenance re-schedlued for Wednesday October 7th |
Tuesday, May 25, 2021, 16:20, Anders Mjos, Conditioning Station, Maintenance, , , Chiller maintenance
|
A contractor on site today for chiller maintenance. CP2 and CP3 circuit is leaking and shall not be used. CP1 can still be used. The contractor will contact Plant Group with a quote for repair and upgrades. |
Thursday, May 23, 2013, 14:07, Bevan Moss, Conditioning Station, Repair, , , Chiller Unit Repaired
|
ESC came today and "repaired" the chiller. There was something wrong with the VFD controller. The were able to get it to start and run correctly again but were not able to recreate the problem. At this point it appears that it has magically disappeared. |
Tuesday, April 23, 2013, 16:11, Bevan Moss, Conditioning Station, Maintenance, TM3, N/A, Chiller Fault 2
|
During Testing it was noticed that Fault 2 was indicated and one of the compressors would not run. Fault 2 does not indicate what the issue was and during inspection nothing could be detected. It had something to do with TCS:CHILCP3 and possibly CP2. CP1 could still be operated and was controlled manually to keep the temperature in the correct range. This was not required but it does affect the conductivity. The main power switch on the chiller unit was turned on and off and the fault was cleared. As far as I know this indicated either a freeze protect, flow, or refrigerant pressure fault. I will ask for TCS:TS6 and TCS:DIF2 to be added to the archiver so this can be further investigated in the future. |
Tuesday, August 06, 2019, 01:13, Carla Babcock, Conditioning Station, Repair, TM4, Dummy HP SIS target, Checks on EE line leak fix and window line leak (not fixed)
|
TM4 has developed 4 leaks so far:
- Line B - seems to be solved with an indium gasket (some testing already done)
- Line D - seems to be solved with an indium gasket (some testing already done)
- EE - indium gasket installed, preliminary tests are good
- Window cooling line - David found with 70 psi helium, leak detector response went from 3E-7 atm.cc/sec to 4E-4torr atm.cc/sec in 1 min and stayed there. When water was put through the circuit, there was an initial vacuum increase to about 1E-6, then a couple hours later it began to fall and has been falling for ~14hrs, now in the 7E-7 range for IG1.
Testing indium seals on lines B, D, EE. No repair has been done for window line. Ramping heaters to TGHT=450A, TBHT=200A. Everything behaving normally.
Wednesday, ramped up BIAS, EZL and EE to 36kV, 17kV, 1.5kV. Sparking at about 1 spark per 20 - 30 mins. Bias current somewhere between 66uA and 78uA, varying with the chiller ON/OFF.
Thursday morning around 2am everything tripped off. No spark visible on strip tool, seems this is from an increase in the window water leak. Vacuum recovered on its own and heaters were ramped back up. |
Thursday, September 28, 2017, 15:34, Anders Mjos, Conditioning Station, Development, TM2, , Changes to MP3 startup
|
Due to problems with the regulating valve WPV1, the VFD (Variable Frequency Drive) for the pump has been programmed to do a slow (2 min) ramp up. WPV1 has been bypassed and left fully opened. Work was done by Dave Morris |
Wednesday, July 05, 2017, 11:18, Anders Mjos, Conditioning Station, Maintenance, TM4, Ta#52, Changed electrical configuration to cathode bias
|
John Chow configured TCS to cathode bias mode (IRH1538). The anode P/S is in positive mode. |
Monday, January 16, 2012, 09:30, David Wang, ITE, Maintenance, , , Changed all old inducion coils for flow sensors in ITE
|
I had changed all old induction coils for flow sensors in ITE .I checked all ITE water signals on control boards in electrical room.They are all very stable and constant.All ITE inductions coils work fine now. |
Thursday, January 24, 2019, 10:34, David Wang, ITW, Maintenance, , , Changed 24VDC plugs of TP solenoid valves in ITW
|
3 damaged 24VDC plugs of TP solenoid valves are replaced. Inspected other plugs. All of them are in good condition now. |
Wednesday, November 14, 2012, 11:04, David Wang, ITE, Repair, TM4, , Change ITE dump water circiut flow wheel
|
I changed ITE dump water circuit flow wheel due to its poor performance. The new flow wheel works fine. The signal on electrical board is strong and constant. One shielding block on ITE was moved out for the job, and it has been moved back after the job.The ITE is ready to take proton beam. Travis was with me when i did the job. |
Wednesday, September 28, 2022, 12:58, Matthew Gareau, North Hot-Cell, Repair, , , Chad repaired the right operator side manipulator   
|
On 26/Sept/2022
Chad disassembled the right operator side manipulator, and noticed that gears in the handle were quite tight especially when compared to the left operator side manipulator.
Once a dry grease was added, and the handle reassembled all seemed to be in working order.
There was noticeable wear on a shaft and Chad has suggested to order some spare parts for the wrist and handle. |
Monday, April 27, 2015, 16:12, Keith C Ng, South Hot-Cell, Development, TM2, , Ceramic Standoffs in TM2 source tray steerer assembly
|
On drawing ITA6008 for the Encole 0.5" ceramic standoffs there is a note to match pairs of ceramics to within +/-0.001". This step was missed on the current build of TM2 source tray (ceramics were not measured).
Measured the lengths of the rest of the ceramic standoffs in inventory and they range from 0.5035" to 0.4950" in length. The ceramics have been sorted by length and grouped into bags.
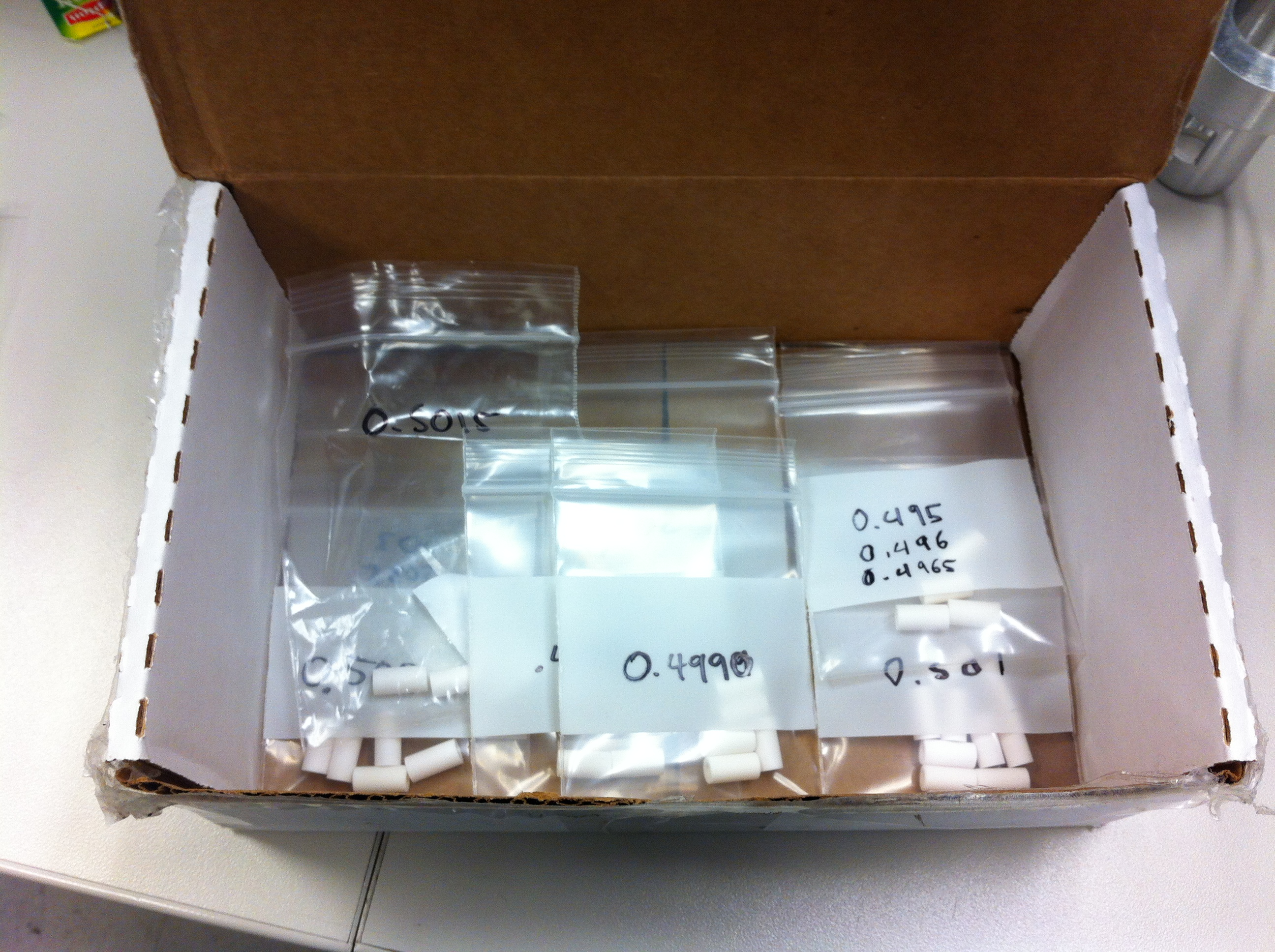 |
Tuesday, November 24, 2015, 13:54, chad fisher, South Hot-Cell, Repair, , , Cell Decon
|
Decon/removal of large solid waste was performed on Wednesday November 18th."Hot" activated items included containment box cover from TM2, Febiad coil line remnants from TM4 (the hottest ends were previously cut off and disposed of), some target conductor bolts, steerer plugs from TM2, target material remn.
Drum containing these solid items is 2.5mSv/hr at 1/2m.
Drum is stored in the north hot cell temp.
Compressible waste will require another drum.
Swipes were taken of the window... 170k counts per minute of cont. |
Wednesday, November 25, 2015, 14:16, chad fisher, South Hot-Cell, Repair, , , Cell Decon 
|
Cell (table) was systematically cleaned with a swiffer and resulting piles of contaminated waste placed in pail with spent Ta target. |
Tuesday, October 22, 2013, 16:52, Bevan Moss, Conditioning Station, Repair, , , Canbus base card for BIAS
|
The base card in the canbus BIAS module was determined to be faulty. Dave Morris removed a card VECC to repair the conditioning station. |
Monday, May 27, 2013, 16:01, Bevan Moss, Conditioning Station, Repair, , , CanBUS card
|
During HV conditioning of TM4 with Ta#40 there was a spark at ~43 kV that caused the Bias card to "fry". Dave Morris has been contacted and has said he will replace it tomorrow. |
Thursday, November 06, 2014, 13:43, David Wang, Conditioning Station, Development, TM3, , CS vacuum system has been connected to TM3.
|
CS vacuum system has been connected to TM3 for control system test(Dave.Morris). |
Wednesday, November 19, 2014, 11:12, David Wang, Conditioning Station, Standard Operation, TM4, , CS roughing pump is started.
|
CS roughing pump is started for TM4 and UCX 11 target. |
Wednesday, July 17, 2013, 10:10, David Wang, Conditioning Station, Development, TM3, , CS cooling and vacuum system have been turned off
|
CS water cooling and vacuum system have been turned off at 10:00 AM this morning.The TM3 will be disconnected and moved to silo tomorrow morning. |
Thursday, November 20, 2014, 14:13, David Wang, Conditioning Station, Standard Operation, TM4, UCx11, CS and TM4 was vented with Argon gas
|
CS and TM4 was vented with Argon gas this morning before it was moved from CS to ITE. |
|