Thursday, March 13, 2014, 16:23, Keith C Ng, ITE, Repair, , , 2a3 window - inspection 
|
Video inspected 2a3 window joint this morning.
Screenshots from video showing debris forming around aluminum cradle and brown/red dust on top of beam pipe.
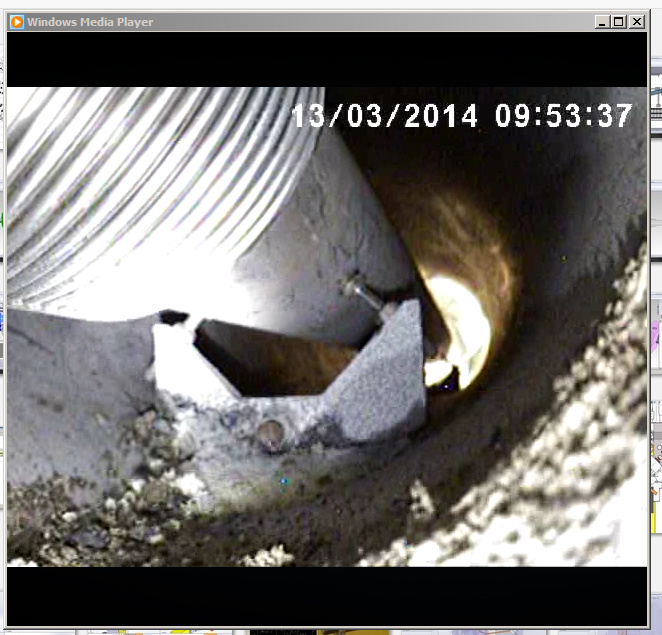 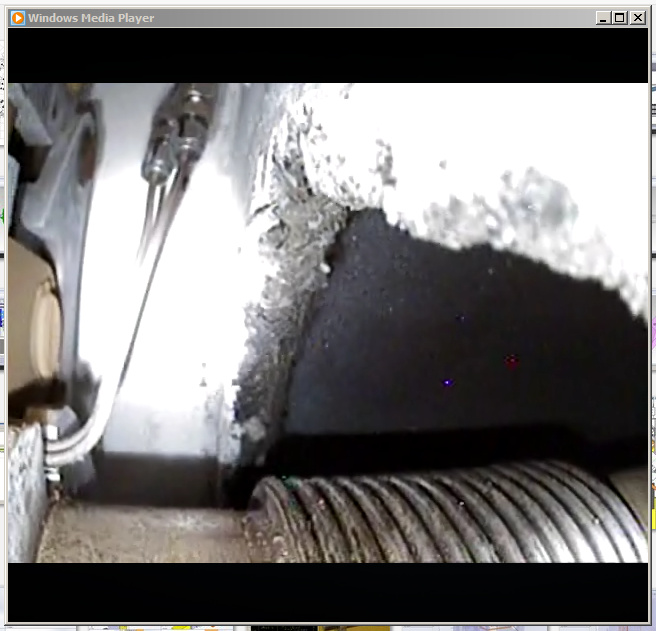
Inspection video can be seen in its entirety at \\trwindata\groups\remote handling\Videos\2014\2014_2A3window |
Thursday, March 13, 2014, 07:35, David Wang, ITW, Standard Operation, TM4, , TM4 and ITW turbo pumps have been started
|
I connected ITW vacuum system to TM4. TM4 and ITW turbo pumps have been started successfully. The pumping down is good so far. |
Wednesday, March 12, 2014, 16:33, Keith C Ng, ITE, Repair, , , 2A3 window removal and replacement    
|
prep'ed area for work:
- removed shield plug from window clamp area
- inspected clamp from tunnel side and from top of target station: video recorder was not working, will try again tomorrow.
- corrosion seen on beam pipe cradles, see photos. corrosion also seen on beampipe, clamp and vacuum tank. will try to vaccuum loose rust tomorrow.
note: gamma spec of rust, white powder from RPG located in \\trwindata\groups\remote handling\Documents\2014\2A3 Window folder (added pdfs as attachments 2014 mar 4)
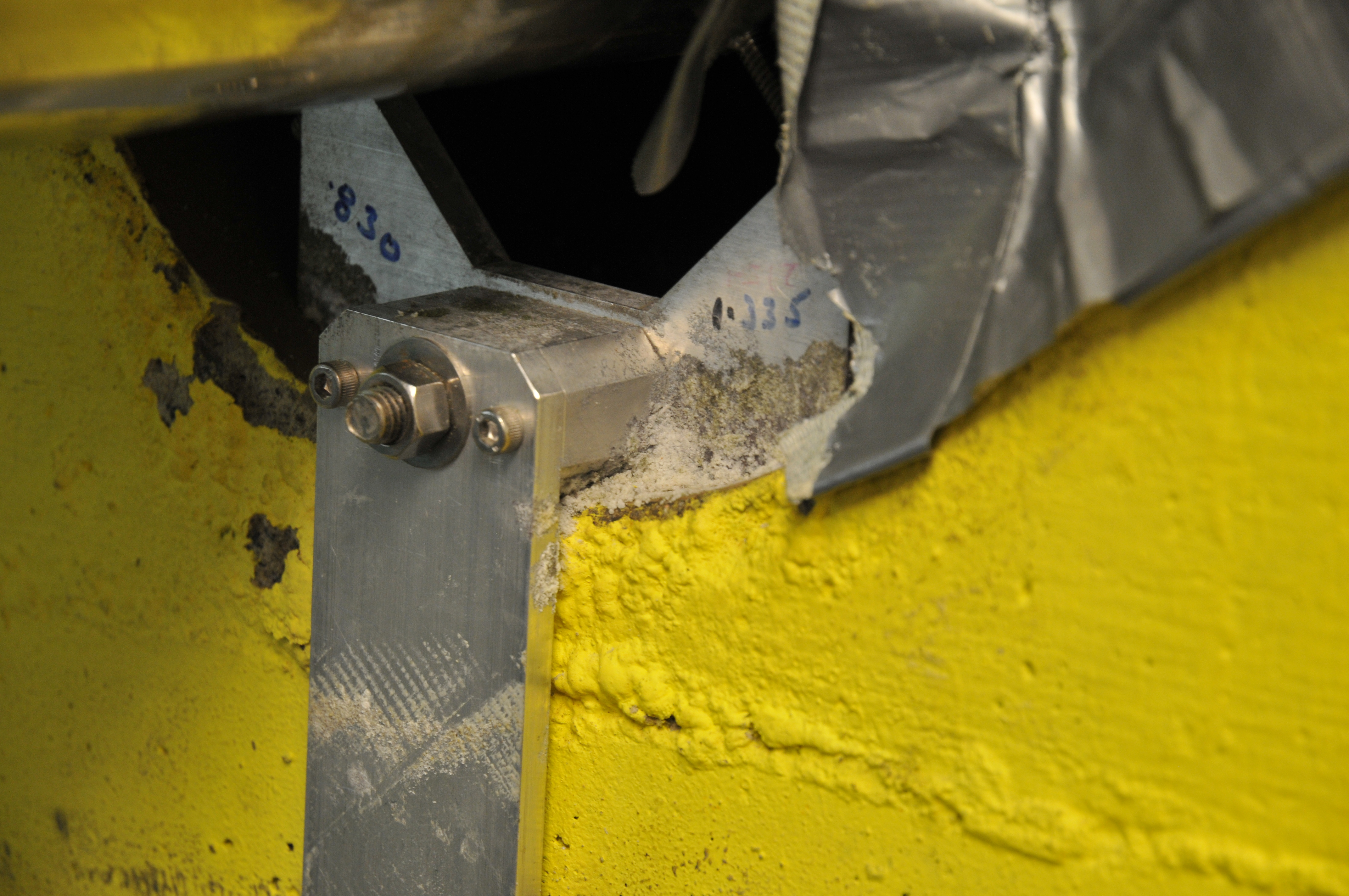

|
Wednesday, March 12, 2014, 09:45, Travis Cave, ITW, Standard Operation, TM4, no target, module move
|
TM#4 has been moved from the north west silo to the west target station. |
Tuesday, March 11, 2014, 10:47, Travis Cave, ITE, Repair, , , entrance module move
|
ITE entrance module has been moved from the east station to the south east silo. |
Monday, March 10, 2014, 09:39, Travis Cave, ITE, Standard Operation, TM3, no target, module move
|
TM#3 with no target has been moved from the east target station to the south west silo. |
Friday, March 07, 2014, 12:45, David Wang, ITE, Standard Operation, TM3, , TM3 and ITE air to vacuum leak check and TM3 water lines helium test.    
|
With TM3 located in ITE, All air to vacuum seals on ITE primary and secondary vacuum vessel have been leak checked with leak detector hooked directly on the TM3 service cap.The base LR :00xE-9atm.cc/sec. The ITE IG1 was 1.6xE-6 torr which was good. No leak has been found during the checking.Also, the TM3 water lines(except HS) had been pressurized with 70 psi helium on each for 2 minutes. There was no response during the test. The ITE and TM3 are good on leak checking.See attachment pictures |
Thursday, March 06, 2014, 14:12, David Wang, Conditioning Station, Standard Operation, TM1, , TM1 air to vacuum and water lines leak check at CS. 8x
|
TM1 air to vacuum and water lines leak check at CS are finished this afternoon. The leak detector is hooked directly to TM1 service cap so the base LR at LD is 0.0xE-9 atm.cc/sec. I sprayed helium to all air to vacuum seal on the service cap, also applied 70 psi to all water lines(except HS) for 2 minutes each. There is no any tiny response had been found on LD. So All TM1 water lines(except HS) and air to vacuum seals are leak free. The HS circuit can not be tested at this time since the VCR caps are not installed. The turbo pumps at CS and TM1 will be turned off before I leave. See attachment pictures. |
Thursday, March 06, 2014, 12:59, David Wang, Conditioning Station, Maintenance, TM1, , Restart TM1 and CS TPs
|
Restarted TM1 and CS turbo pumps after the power off. Everything is fine . |
Thursday, March 06, 2014, 06:58, David Wang, ITE, Maintenance, TM3, , ITE vacuum and leak check on ITE BL2A window flange.
|
ITE and TM3 Turbo pumps have been started successfully yesterday. The vacuum reading on all ITE high vacuum gauges are at low E-6 range after one night pumping down which are good so far. There is no any sign of leak on BL2A window and the flange seal on ITE side. Yesterday afternoon, Ron , Edi ,and I did a leak check on the ITE BL2A window flange(2aTunnel side). The leak detector was hooked onto BL2A in tunnel. Ron and I supplied helium from TH to the helium test line(located in ITE pit) which we have on ITE BL2A window flange. The helium test line end nozzle is just located under the bottom of the 2A window flange. Edi was in BL2A tunnel checking the leak detector. We supplies 10- 15 psi helium 3 times to the test line. Each time for 10 seconds. The helium flow was checked twice and they were good. The LD base LR was 2.2xE-5 atm.cc/sec, After 70 seconds , The leak rate on LD was increased to 5.3 xE-5 atm.cc/sec. The leak rate reading recovered after 20seconds. There is no obviously conclusion where the leak is. At that moment, Ron said, he and Edi would like to do some further leak check in 2A tunnel,and I went back to my job. |
Thursday, March 06, 2014, 06:28, David Wang, Conditioning Station, Maintenance, TM1, , TM1 had been moved from silo to CS
|
TM1 has been successfully moved from silo to CS. The CS vacuum system is connected to TM1. Turbo pumps on TM1 and CS have been started yesterday afternoon . The starting of TM1 turbos was easy. The pumping down over night is good so far. |
Wednesday, March 05, 2014, 10:07, Travis Cave, Conditioning Station, Standard Operation, TM2, no target, module move
|
TM#2 with no target or source tray has been moved from the conditioning station to the north east silo. TM#1 with no target has been moved into the conditioning station. |
Tuesday, March 04, 2014, 10:19, Travis Cave, ITE, Standard Operation, TM3, no target, module move
|
TM#3 has been moved from the silo to the east target station. |
Tuesday, February 25, 2014, 10:00, David Wang, Conditioning Station, Repair, TM2, , helium pressure test on TM2 tube heater (+) water line with blank off(C-seal) installed on WB. 10x
|
I did the helium pressure test on TM2 tube heater (+) water line with blank off(C-seal) installed on water block at CS.The leak detector was hooked directly to the top of the module this time. So base leak rate and base pressure were at the bottom scale on LD. 30 -80 psi helium was applied to the D lines(both side) with10 psi increasing each time. There is no any tiny response hasbeen found during the test. The lines are perfectly sealed. Also i sprayed the helium on the top of the service cap .All air to vacuum seals on the top are good either. See attachment pictures. |
Tuesday, February 25, 2014, 06:53, David Wang, South Hot-Cell, Repair, TM2, , Leak check on TM2 tube heater (+) water line with blank off(C-seal) installed on WB.
|
Chad and I did the leak check on TM2 tube heater (+) water line with blank off and C-seal installed on WB at South Hot Cell.The line was easy to pump down to 0.0xE-9atm.cc/sec and 0.0XE-4 torr on leak detector. Chad flushed lot helium around the water block (10 sec spray). No response had been found on leak detector. |
Monday, February 24, 2014, 13:52, Travis Cave, South Hot-Cell, Standard Operation, TM2, no target, module move
|
TM#2 moved from the south hot cell to the conditioning station. |
Monday, February 24, 2014, 12:09, chad fisher, South Hot-Cell, Repair, TM2, , C-seal blank off test
|
Circuit D has passed the vacuum leak check. Jig has been removed and containment box re-installed for move to conditioning station. |
Monday, February 24, 2014, 11:05, chad fisher, South Hot-Cell, Repair, TM2, , Circuit D blank off
|
The blank off with the o-ring has been removed, manipulator fixed, circuit D water block sealinhg surfaces cleaned and blank off with c-seals installed and torqued. Leak check will occur shortly. |
Thursday, February 20, 2014, 11:04, chad fisher, South Hot-Cell, Repair, TM2, , Readying TM2 for C-Seal Leak Check
|
Containment box has been removed and water block jig installed. |
Thursday, February 20, 2014, 09:45, Travis Cave, Conditioning Station, Standard Operation, TM2, no target, module move
|
TM#2 has been moved from the conditioning station to the south hot cell. |
|