|
ID |
Date |
Author |
Category |
Type |
Subject |
|
22
|
Tuesday, March 19, 2013, 19:17 |
Grant Minor | Elevation Jack | Standard Operation | Re-indexing of all jack station "zero" yoke elevations | The dimension between the yokes and the Cyclotron upper structure primary beams was set to .25" nominal at all jack stations today.
At each station:
- The jacks were jogged manually upwards until the yokes hard-stopped on a piece of .25" nominal shim stock (see attached reference photo, measured accurate within .005").
- The dial indicator was set and zeroed, and the station was backed off by .005" to 0.010" in order to remove the .25" reference stock (except at station 4 where the dial indicator mount was damaged).
- After the adjustment, the mechanical counter was decoupled from the output shaft of the jack (without affecting the synchro) and set to "00100".
This work was performed by Maico Dalla Valle and Daniel Wright in co-ordination with Dan Louie.
The defective mechanical counters at stations 5 and 9 were replaced, with a brand new counter at one station and a used repaired counter at the other station.
The yokes at all jacking stations should now be .250" +/- .015" from the upper structure.
|
|
21
|
Monday, March 18, 2013, 15:12 |
Isaac Earle | Cyclotron | Maintenance | Cyclotron Magnet Face Gap Measurements | Measurements of the cyclotron magnet face gap were taken on March 15, 2013 at two locations around the tank with the cyclotron lid in the fully raised position (the lid had been raised until the upper limit switches caused the control system to stop travelling). The purpose of the measurements is to establish an independent means of verifying correct lid height before beginning in-tank remote handling activities at the start of a shutdown period.
The height of the lid at the time of measurement was confirmed to be adequate for the bridge to perform a full orbit without any interference between the bridge or cable tray and devices on the lid.
Measurement locations were labelled using permanent marker. A plumb-bob was used to ensure the measurement location on the upper and lower faces were aligned vertically. The measurements were performed using a tape measure hung from the upper magnet face and read at the lower magnet face as shown.
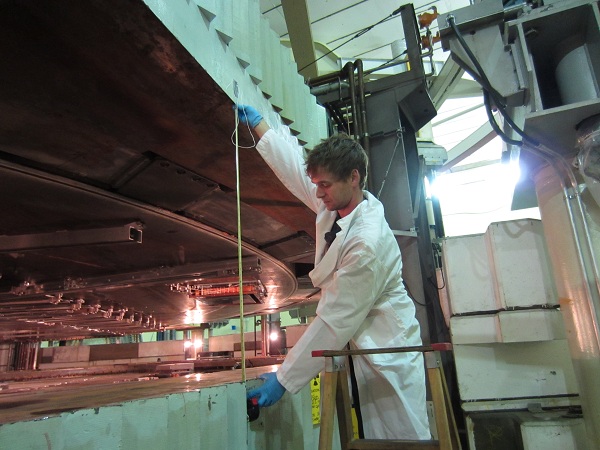
Location #1: RH bridge entry/exit point (~50° position), Measured gap: 46-1/2" +/- 1/16"
Location #2: East side of jack station #1 (~215° position), Measured gap: 46-9/16" +/- 1/16"
Photographs of the upper limit switches on jack stations #1 and #10 were taken as shown below:
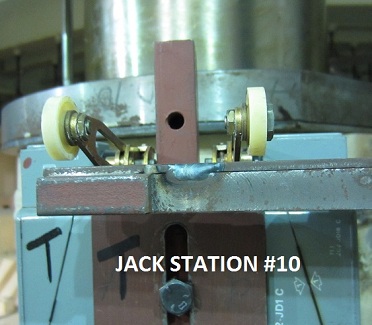
At this lid height, the reference stick on the top of the cyclotron lid was found to be touching the concrete ceiling, but was not bowed. See photo below.
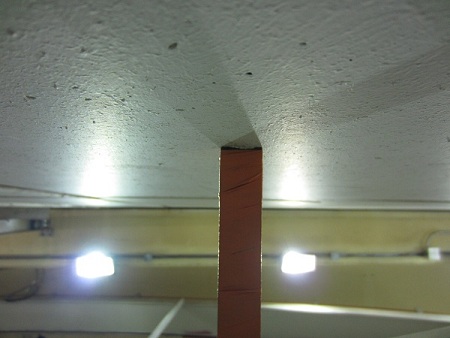
The distance between the cyclotron tank lid and the RH bridge was then measured using a meter stick attached to the lift trolley. The trolley was moved into the tank, and the stick raised until it contacted the tank lid. This position was recorded, the stick was lowered, the trolley was removed from the tank, then the stick raised again to the recorded position. A piece of aluminum angle was used to translate the measurement from the center of the trolley to the edge of the bridge as shown below:
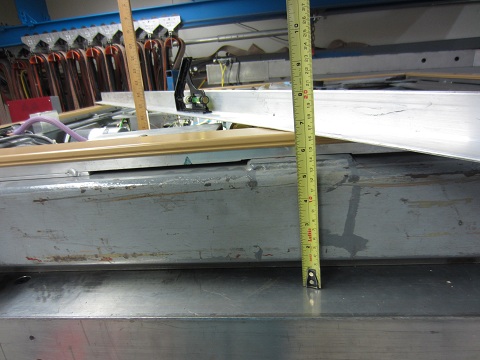
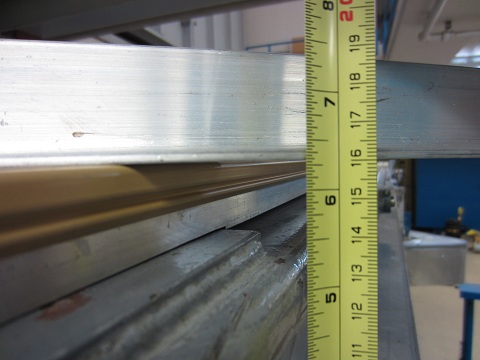
Total Distance from RH Bridge Rail to Cyclotron Tank Lid: 15-7/16" + 6-5/16" = 21-3/4" +/- 1/8"
|
|
20
|
Friday, March 15, 2013, 15:18 |
Grant Minor | Cyclotron | Standard Operation | Lid Down Successful - Mechanical Counter Readings | Prior to the lid-down operation today, the Cyclotron was lowered by 0.75" and then raised again to confirm that the upper limit switches were working. Dan Louie confirmed this from the control racks.
Maico and Grant walked around the perimeter of the cyclotron to inspect each station and ensure that there were no interferences, e.g. dial indicator rods, tread plates, etc.
The lid was lowered successfully by Gord Roy and Dan Louie.
Mechanical counter numbers recorded after lid down are shown below:
Station |
Count |
1 |
00093 |
2 |
00093 |
3 |
00091 |
4 |
00082 |
5 |
83401 |
6 |
00103 |
7 |
00092 |
8 |
00097 |
9 |
64855 |
10 |
00094 |
11 |
00086 |
12 |
00087 |
|
|
19
|
Friday, March 15, 2013, 08:39 |
Don Jackson | Cyclotron | Standard Operation | Pre Lid Down In Tank Video Survey | In tank survey completed. A few items of interest were found. Ladders need to moved manually outboard to #5 resonators and the items noted in attached document need to be addressed. |
|
18
|
Thursday, March 14, 2013, 19:57 |
Grant Minor | Cyclotron | Repair | Tank lid upper / over travel limit check | Today Grant Minor, Dan Wright, Arthur Leung, and Dan Louie checked the height difference between the tank lid upper travel limit switch and the tank lid over travel limit switch at both stations 1 and 10.
In the attached photos, the upper travel limit is the lever on the right. The over travel limit is the lever on the left.
The over travel limit is a safety switch designed to halt the system and lock it out if there is some problem with the upper travel limit.
The following tasks were performed:
- The new reference positions for the brackets after the March 11th adjustment of 0.25" (see previous e-log) were scribed onto the mounting posts for Stations 1 and 10
- The brackets at both Station 1 and Station 10 were unbolted and raised up completely to disengage the switches. This had to be done due to mechanical hysteresis in the switches. Dan Louie confirmed when the upper limit / over travel limit signal lamps had turned off at the control rack.
- The Station 1 bracket was bolted up higher temporarily so that both switches were disengaged at that Station.
- The Station 10 bracket was positioned back at the new scribed reference line from step 1.
- A 1/8" nominal machinists parallel was slid under the lever arm of the over-travel limit switch at Station 10, and Dan Louie confirmed that the over travel lamp had turned on.
- The Station 10 bracket was unbolted and raised to disengage both switches, and bolted in this higher position.
- The Station 1 bracket was then positioned back at the reference line from step 1.
- Step 5 was repeated for Station 1, confirming that the over travel lamp engaged after the 1/8" parallel was inserted under the switch.
- Both brackets were positioned back at the reference positions from step 1 and bolted in place.
This procedure confirmed that the over travel limit switches at both stations 1 and 10 engage less than 1/8" higher than the upper limit switches.
|
|
17
|
Monday, March 11, 2013, 19:43 |
Grant Minor | Cyclotron | Repair | Adjustment of tank lid upper limit by 1/4" upwards | This morning Don Jackson commented to Grant Minor that he believed the tank lid was still not raised high enough to safely operate the Remote Handling bridge and trolleys, despite it having been raised 0.5" yesterday to the point of engaging the limit switches (see e-log from yesterday). Don said he believed this to be the case as a result of a visual inspection with binoculars from the outside of the tank, as well as from the views achievable with the remote cameras.
Don also believed he had caused further damage to the equipment inside the tank by orbiting with the bridge.
After a teleconference with Klaus Reiniger after lunch (Yuri Bylinski, Dan Louie, Don Jackson, Grant Minor present), the following was confirmed:
- There is a complete set of limit switches at station 1, and duplicate set at station 10 for redundancy.
- Both stations 1 and 10 have an operator upper limit switch, as well as an over-travel limit set slightly higher than the upper limit.
- The lid has traditionally been raised to the point of the upper limit switch tripping, then the lift procedure stops there.
- The wooden stick was traditionally set to just touch the roof beams with the lid at the upper limit. This means if the stick is contacting the roof beams within 1/32nd inch or so and the upper limit trips, the lid has been raised fully.
- Klaus could only remember one incident of the lid being raised so high before tripping the upper limit that the wooden stick actually bowed under pressure from the roof beams. In other words, this was not a normal occurrence.
- Klaus also reminded us that the limit switches have some mechanical hysteresis and need to be actuated through their full range of motion to reset them.
Don Jackson indicated that another 1/4" of clearance would be adequate to safely operate the RH equipment in his opinion.
At around 5pm Grant Minor and Ron Kuramoto reset the upper limit switches at both stations 1 and 10 by adjusting the block that both upper limit and over-travel are mounted to, see attached photos.
- A line was scribed in the primer paint to mark the original position of the limit switch mounting block.
- The bolt was loosened, and the block was raised fully to reset the switches, and then set 1/4" higher than the scribed line, measured with a Starrett scale accurate within about 1/64"
- The bolt was re-tightened.
Dan Louie and a shift operator reset the wooden stick 1/4" lower than the roof beams, this was double checked by Grant.
Dan Louie started up the system and confirmed the limit switches were properly reset. He then raised the lid until the limit switches tripped again, confirmed by checking the illumination of the upper limit lamp (see attached photo).
After the raising of the lid, the wooden stick was confirmed to be contacting the roof beams by Grant Minor.
Dan Louie also confirmed that the master synchro counter had advanced almost exactly 250 counts (proportional to about 250 thousands of an inch).
Mechanical counter readings at each station (where accessible) were taken before and after this 1/4" rise by Dan Wright and Grant Minor:
Station |
Before 1/4" rise |
After 1/4" rise |
1 |
47231 |
47491 |
2 |
47240 |
47505 |
3 |
47223 |
47486 |
4 |
47230 |
47486 |
5 |
49448 |
70102 |
6 |
47248 |
47512 |
7 |
47215 |
47474 |
9 |
00523 |
02533 |
10 |
47239 |
47496 |
11 |
47229 |
47490 |
12 |
47232 |
47497 |
Grant Minor had dosimeter 208 today, which was signed out at 0.61 mSv and signed in at 0.69 mSv. Thus elevating system assessments and adjustments resulted in approximately 0.08 mSv dose. |
|
16
|
Friday, March 08, 2013, 18:42 |
Grant Minor | Cyclotron | Repair | Tank lid not at upper limit and resulting effects | This morning during routine service bridge work in the Cyclotron tank, it was observed by Travis Cave that the cable tray for the Remote Handling service bridge was catching on something on the top inside surface of the Cyclotron tank. The cable tray was observed to visibly snag on this protrusion and then bounce around.
Isaac Earle and Grant Minor conducted an inspection from the edge of the Cyclotron tank with cameras and binoculars. The contact point was identified and photos and video were recorded (see attached).
After a meeting with Yuri Bylinski it was identified that the item interfering with the cable tray was a beam scraper foil (part of the Resinator D Gap), close to the center post area.
A number of causes for the snag were suspected:
- The upper tank lid might not have been at its upper limit (i.e. not raised completely by the elevation jacking system)
- The center post bearing for the service bridge might not be seated properly
- The cable tray mounting bracketry or air cylinder may have been displaced
After inspections of the service bridge before and after removal from the tank, it was determined that neither 2 nor 3 were the cause of the problem.
It was observed by the Remote Handling group that the upper limit switches located at stations 1 and 10 had not advanced high enough to mechanically "click", even though their wheels were contacting the reference surface. There was about 0.5 to 0.75 inch of travel remaining in these switches (see attached photos) before clicking.
It was also observed that the wooden stick normally set flush with the Cyclotron roof beams at max height was about 0.5" below the roof beams (measured with a Starrett scale by Grant Minor).
After further assessment, it was also determined by Dan Louie and Yuri Bylinski that the limit switch lamp on the elevating control system was actually not lit, even though it appeared so. The dull glow in the lamp was due to the neon style of the bulb, which can glow a small amount even at very low voltages and appear to be lit. A test of raising the switches while watching the lamp revealed that the lamp switched on brighter after the limit clicked.
The upper tank lid was raised around 6pm by Dale N. with Yuri Bylinski and Grant Minor present. The stick advanced upwards about 0.5" almost completely to the ceiling (see attached photos).
Until a systematic method of measurement of the vertical displacement of the system is developed (this may be the purpose of the dial indicators at each station, but requires further investigation), this problem can be avoided again by always checking both the limit switches and the distance from the calibrated "wooden stick" to the cyclotron roof beams. |
|
15
|
Tuesday, March 05, 2013, 14:11 |
Travis Cave | Cyclotron | Standard Operation | Setup and the Installation of the HE 1 probe. | Setup of the HE 1 probe is difficult has we have no mockup of it to properly setup cameras and equipment for it. This is problem for both extraction and installation of the probe. Also with the setup some of the broken micro switch from the HE 1 was found on the HE 1 probe jig after the jig was deconned and moved up the B2 level. Also for setup required camera adjustment to be made with the heavy contaminated probe being very close to the person setting up the cameras.
Now installation of the probe worked but it was very fiddly and touchy feely on the install, which something one doesn't want for remote installation. It required lots of movements and adjustment and a little luck and the probe went in, even with a air cylinder that did decide to work in the end.
On the extraction of HE 1 was mess and was damaged upon extraction, this was due to improper camera setup (no mock up of probe), and to the fact that removal is very fiddly and not east to the current design of the jig, and the way the probe is locked in place on the lid.
Note on contamination on extraction the probe jig was contaminated with about 20 000 cpm in spots it was removable and the jig cleaned. Contamination was also found on the jig for the installation of the jig it was about 800 cpm jig was cleaned again. Plastic was also laid on the platform of the upper ressonator trolley as to prevent the spread of contamination to the trolley, this appeared to work. AS A NOTE NONE OF REMOTE HANDLING'S TROLLEYS AND CYCLOTRON EQUIPMENT WAS DESIGNED TO HANDLE CONTAMINATION. If the trolley ever get or contamination is ever found on them they will be impossible to clean. |
|
14
|
Wednesday, February 27, 2013, 12:08 |
Travis Cave | Cyclotron | Standard Operation | Installation of 2C | 2C has been installed located on all QDLs and all the numbers, continuity check done and passed. Bridge has been removed from the cyclotron tank. |
|
13
|
Wednesday, February 13, 2013, 08:55 |
maicodallavalle | Service Bridge | Repair | Service Bridge/Carrier Hydraulic Jacks | On Monday February 4TH the Service Bridge was being lifted into the Cyclotron with the Carrier. It was noticed that one of the two Hydraulic Jacks was leaking. All work stopped and the Service Bridge and Carrier were moved to the Remote Handling B2 level for repair. The Service Bridge and Carrier were separated and the Hydraulic Jacks were inspected. It was noticed that both Hydraulic Jacks were leaking. Two overhaul kits were ordered. Two other Hydraulic Jacks were found and replaced. Work continued in the Cyclotron with the Bridge and Carrier. The two Leaking Hydraulic Jacks were overhauled. Once most of the work in the Cyclotron was done and there was time that the Service Bridge and Carrier were out of the Cyclotron and not in use the two overhauled Hydraulic Jacks would be replaced. They were tested without the Service Bridge and then with the Service Bridge. There were no leaks and all operation was back to normal. |
|
12
|
Wednesday, February 06, 2013, 18:07 |
Grant Minor | Elevation Jack | Maintenance | Lid-down yoke gap measurements from 1994 | Attached is a scan of a handwritten record from 1994 showing yoke-to-upper-structure gap measurements from 1994, both L and R sides, with tank under vacuum and vented.
The measurements appear to be made with a 0.25" shim and 0.01" pieces of shim stock as they are only in increments of 10 thou.
The 1994 gap appears to vary from 0.25" to 0.33" (80 thou max variation) under vacuum, and from 0.29" to 0.33" vented (40 thou max variation).
Our 2013 measurements, made with a 0.25" piece of stock and a feeler gauge, varied from 0.265" at Station 1 to 0.445" at Station 11, (180 thou max variation, see Jan 28 e-log).
I have not yet found any other records of this measurement but I will keep searching. The gaps may have varied by as much as 180 thou for many years.
I recommend checking the clearance at all stations and jogging individual stations such that the gaps are within a 40 thou band prior to the next lift.
|
|
11
|
Wednesday, February 06, 2013, 17:50 |
Grant Minor | Elevation Jack | Maintenance | Service records compiled by G. Minor | Attached is a compiled record showing the years of service of the jacks, upper bearing, and gear reducers, prepared by Grant Minor on December 17 2012. |
|
10
|
Wednesday, February 06, 2013, 17:42 |
Grant Minor | Elevation Jack | Maintenance | In-situ jack power screw lubrication inspection - Stations 9, 10, 11, and 6 | Due to concerns raised regarding the state of the lubrication of the power screws at Station 9, the lubrication was visually inspected by me and Ron Kuramoto on February 4th.
Photos are attached.
The power screws for these stations were serviced and re-lubricated on the following dates:
Station 9 - 1996
Station 10 - 2001
Station 11 - 1997
Station 6 - 2011
There did not appear to be any major visual differences in the lubrication between any of these stations. The grease at Station 9 appeared to coat the power screw uniformly through its range of travel, and there were no major signs of drying, hardening, or separation of the constituents relative to the other stations inspected.
There is a slight apparent difference in the opacity of the grease between Station 9 and Station 6 in the photos attached, but this may be due to the lighting and camera flash at the angle taken.
There did not appear to be any flecks of metal, contaminants, or other signs of abnormal wear in the grease.
The mechanical properties of the grease at Station 9 vs. virgin grease would have to be assessed by a tribologist in a laboratory setting from samples.
Samples of the grease were not collected at this time, but could possibly be collected in the future when Station 9 is removed for service.
|
|
9
|
Monday, February 04, 2013, 13:52 |
Grant Minor | Service Bridge | Repair | Hydraulic cylinder failure on service bridge | The hydraulic cylinder on the West side of the service bridge (used to raise the bridge for insertion into the Cyclotron) failed this morning, leaking oil in the vault tunnel. Most likely this was due to a failed seal or gasket.
Maico Dalla Valle has removed both the East and West cylinders for refurbishment and is pursuing repair kits from Hyseco.
The purple coloured cylinder on the East side has been slowly leaking oil for some time. A gasket in the West cylinder (yellow) seems to have failed and a broken piece of the gasket was removed during the disassembly, shown in the photo "Hydraulic Cylinder Gasket 4 Feb 2013 008.jpg" attached.
Cylinder model number is ENERPAC RC-254.
http://www.hyseco.com/
|
|
8
|
Wednesday, January 30, 2013, 14:44 |
Grant Minor | Elevation Jack | Standard Operation | Further lid-up notes from Dan Louie | Dan Louie's e-mail comments from 30 Jan 2013 are attached.
- Grant |
|
7
|
Tuesday, January 29, 2013, 18:49 |
Grant Minor | Elevation Jack | Standard Operation | Lid-up complete - summary notes | Lid-up was first attempted yesterday (Jan 28th) by Dan Louie, Arthur Leung, and Maico Dalla Valle. They experienced problems with Station 9 continually tripping the system and were not successful.
This morning again there were problems raising the lid above ~1 inch due to tripping at station 9. It was observed that the mechanical counter at Station 9 was increasing about 5 to 6 times faster than the counters at the other stations. There may be a mechanical problem with the gear reduction for this counter. However, the mechanical counter is just a readout and does not control any aspect of the lid up. Comparisons between stations 9 and 10 at the 1 inch trip point are shown below. Station 10 is representative of the other stations within about 100 counts.
~ 1-inch trip |
Station 9 counter |
Station 10 counter |
Attempt 1 from fully lowered |
6976 |
1814 |
Attempt 2 from fully lowered |
5899 |
1397 |
The lid was lowered fully and the gap between the yoke and the upper structure primary beams was measured by Maico at one spot per station with 1/4" stock and feeler gauges (see attached reference photo from 2012).
Station |
Gap (inch) |
1 |
.265 |
2 |
.295 |
3 |
.378 |
4 |
.270 |
5 |
.390 |
6 |
.290 |
7 |
.274 |
8 |
.345 |
9 |
.373 |
10 |
.393 |
11 |
.445 |
12 |
.356 |
Not much could be concluded from the measurements. The control system is supposed to keep the jacks parallel within about 50 thou, however Stations 1 and 11 appeared to be out by 180 thou. It is difficult to say without further study whether this larger discrepancy is due to overshoot at each station after the lower limit switches are reached.
Grant Minor, Dan, Maico, and Arthur met in the Main Control Room at around 1:30pm to assess. Dan commented that Station 9 was continually lagging in the system and causing the ~1 inch trip. The decision was made to drive the whole system to the ~1inch trip point and then jog Station 9 manually to bring it back into the "go" band of tolerance, and continue on this way until the "sticky" portion of travel was overcome. In Grant's opinion, the transmission system at each station (motor, reducers, jacks, and upper bearing) sits dormant in one position for a full year each year and settles in a single position. Some asymmetry in the static and dynamic friction from station to station is expected after such a long idle period. Additionally, the lubrication at station 9 has not been serviced since 1996 (18 years). Grant also felt that jogging the system in small increments to bring it back into the tolerance band should not damage the jacks, motors, or reducers provided they were carefully monitored for abnormal noises or overheating.
The sequence of events following the 1:30pm meeting is outlined below:
- The system tripped as expected around 1 inch.
- Station 9 was jogged upwards 20 thou, measured with the dial indicator. Station 9 counter increased from 9255 to 9429.
- The entire system was run upwards by about another inch with several more trips, some from Station 9 and some from other stations. Dan reset the system after each trip.
- At around 2 inches, Station 9 was jogged again. Maico reset the dial indicator and attempted to jog manually but the dial did not move. This might have been due to the lag at Station 9 creating some amount of backlash before the load was taken again. He reset the dial again and this time measured a jog of 25 thou. Dan asked us to back off by 20 thou, then he reset the system and we continued to raise.
- The system was raised to about 3" in small increments with several more trips, each time reset by Dan. Station 9 was jogged 3 more times during this period by 10 thou each time, at approx. counter readings 16 362, 16 802, and 17 134.
- The system then ran properly for quite some time and tripped at around 6 inches. We stopped to inspect the tank seal, which was OK.
- The system was reset by Dan and run again to about 10 inches, at which point station 1 tripped. Station 9 counter read 60 775, Station 11 counter read 10 829 (again a factor of 6 discrepancy).
- Dan requested a jog of 10 thou at Station 1, and then we continued to run. The system ran with only a couple of trips up to about 1 foot from the upper limit.
- At around 1 foot from the upper limit, Station 7 started to cause tripping. It was jogged 10 thou and we continued all the way to the upper limit.
(Total travel is approximately 48 inches or 4 feet).
During the course of the work, it was observed that the motor at station 9 was getting hot early (around 2 to 3 inches of travel), but the motors at other stations (e.g. Station 11, Station 1) reached about the same temperature to touch after the system was running properly.
Report by Grant Minor, P.Eng.
|
|
6
|
Thursday, October 25, 2012, 13:58 |
maicodallavalle | Service Bridge | Maintenance | Orbit Drive | It was observed during the last time the Cyclotron service bridge was used the orbit drive chain had a lot of slack. The drive motor had to be shimmed to tighten the slack in the chain. |
|
5
|
Tuesday, September 25, 2012, 08:57 |
maicodallavalle | Elevation Jack | Maintenance | 2012 Service Maintance of #4 Station Jacking System | Shut down work for 2012.Replaced serviced Jacking Station #6. Tapered alignment pins were damaged. They were skimmed and checked and installed. Station #4 was removed and the spare Station was put in its place.Station # 4 Upper Bearing was inspected and serviced.Station #4 had a problem with the Jack on the right side.The coupling hub than joins the Jack to the High Field was installed backwards.(Not sure how long the hub has been like this maybe 15-20 years?). The coupling and hub had to be cut/split apart to get them off of the Jacks shaft. A new coupling and hub was machined and installed. Anew shaft seal was installed next to the new coupling hub. All the old grease was removed from the Jack. The Jack was inspected and then new grease was replaced. The left Jack was also serviced. It was taken apart and the old grease was removed. The Jack was inspected. The shaft seal on the other side of the coupling hub was replaced. New grease was replaced. The two High Fields had the oil drained. They were inspected and new oil was replaced. #4 Stations motor has four mounting bolt holes and two tapered pin holes for alignment. The one tapered pin hole in the front right side of the motor had a small hairline crack. The paint was removed in the area where the crack was so it could be welded.(The motor base is made of Cast Iron). The crack was welded with 309L SS welding rod. After welding the tapered pin hole was checked with the tapered pin.(It was OK). The #4 motor was bolted to the service area work bench. An Electrician hooked the motor up for testing. The motor was greased and then it was started. It ran nice and smooth. |
|
4
|
Friday, February 17, 2012, 15:07 |
Don Jackson | Trolley | Repair | Video Trolley Failed in Cyclotron Tank | All control to the video trolley was lost during remote photographing of components in the cyclotron. The control system and cameras on the trolley were still operational leading to the suspicion that a power cable was broken either on the trolley or the bridge festooning. Two trips into the tank were made to evaluate the problem and attempt to push the trolley out of the tank. Pushing the trolley only managed to move the trolley a few feet before jamming. A lift mechanism was used to raise the drive wheel without any success. This device was modified and used successfully to remove trolley completely from the tank.
Three trips by two persons were required to remove the trolley. There was a total dose of 0.5 mSv was received by the two persons going into the tank. An additional 0.18mSv was receive by 3 persons outside of the tank.
The trolley will not be used in the cyclotron until the problem is diagnosed and repaired. This trolley is not critical to any upcoming remote handling operations. |
|
3
|
Tuesday, February 14, 2012, 15:40 |
Grant Minor | Trolley | Standard Operation | 2C Removal - all 4 QDLs were actuated remotely this year! | Today Remote Handling staff (Maico Dalla Valle, Travis Cave) used the Remote Handling 2C probe removal trolley to remove the probe assembly from inside the Cyclotron. This is a regular yearly MRO task that is done every shutdown.
This task involves lining up the 2C trolley on the service bridge with the 2C probe assembly remotely with cameras, using a set of alignment markings on the trolley and probe assembly. Once the trolley is lined up with the probe assembly, a set of solenoids are fired to disengage a corresponding set of four QDLs (quick disconnect latches) at different locations on the probe assembly. A complete procedure is documented by Remote Handling staff.
The four QDLs are actuated by a set of four solenoid actuators on the 2C removal trolley, numbered 3, 4, 5, and 8.
Traditionally in the past, the QDL actuated by solenoid 8 has jammed and does not automatically disengage when hit with the solenoid actuator. A member of Probes or Remote Handling has had to suit up with a respirator, run into the Cyclotron tank, and tap this QDL by hand to free it from it's jammed state. This has been done every year for quite some time, as long as Don Jackson can remember (around 30 years)!
However, today, Remote Handling staff (Travis and Maico) were able to disengage all four QDLs remotely using the solenoid actuators on the trolley!
A few things were done differently this year compared to previous years, which may have contributed to this success:
a. The centre post bearing on the service bridge was disassembled, cleaned, and lubricated (see previous e-log from this shutdown)
b. The "AXIAL A" alignment tab on the 2C removal trolley was intentionally misaligned with the felt pen markings on the 2C assembly (see attached picture that points out this "gap").
c. The solenoids were fired in the following order: 8 (no success on disengagement), 5 (success), 4 (success), 3 (success), then 8 again (success).
After all four QDLs were disengaged, and the probe assembly was lowered away from its fixture points, it was observed that the assembly moved slightly laterally, indicating a slight stress or misalignment between all four QDL pins and their corresponding receptacles in the Cyclotron tank. The "gap" labelled in the attached picture, shrunk a small amount after this lateral movement.
Don Jackson remarked that in his entire tenure here, he had never witnessed successful remote disengagement of all four QDLs! This is quite a positive result, as it lowers the expected dose and time required to remove the 2C probe assembly. This approach to the task should be repeated next year and video documented (unfortunately we were not video recording the successful attempt this year).
Cheers,
Grant Minor, Remote Handling
|
|