ID |
Date |
Author |
Target Material |
Target Oven W.O# |
Source |
Status |
Subject |
156
|
Tuesday, September 23, 2014, 15:02 |
Laura Lambert | Empty | 40282-5 | TARGET BOAT | In progress | Sintering Ta target boat with TaC coating | Tuesday, September 23, 2014, 15:00
A new target boat [new design with no end caps] was sprayed with TaC coating and let dry.
The target boat is wrapped with 3-layers of Ta-heat shield.
The boat was installed in EVAP2, chamber is currently being pumped down.
|
157
|
Tuesday, September 23, 2014, 18:32 |
John Wong | Empty | 40282-5 | TARGET BOAT | Done | Sintering Ta target boat with TaC coating (with Temp measurement) |
Laura Lambert wrote: |
Tuesday, September 23, 2014, 15:00
A new target boat [new design with no end caps] was sprayed with TaC coating and let dry.
The target boat is wrapped with 3-layers of Ta-heat shield.
The boat was installed in EVAP2, chamber is currently being pumped down.
|
Tuesday, September 23, 2014, 18:31
Chamber was pumped down to 2.5e-6 Torr.
HS water valve open; no leaks detected.
Stepping up TGHT to 40A - pressure is increasing...
Tuesday, September 23, 2014, 19:05
Auto-ramping TGHT to 580A at 0.5A/min. Temperature will be measured and TGHt will be adjusted accordingly.
Wednesday, September 24, 2014, 11:57
Pressure is stable at 2.2-6 Torr as TGHT is ramping up. Increase ramping rate to 2.0A/min. Currently TGHT at 540A.
Wednesday, September 24, 2014, 15:36
TGHT at 580A for 2 hrs. Inner tube temp (left side wall, viewing from the window port) ~1800C (measured with Mikron = 1550C +250C em. correction); Vac @ 1.67e-6 Torr.
Temperature measurement distance from the window to Mikron = 45cm.
Increase TGHT to reach 2000C (Mikron @ 1750C)
Wednesday, September 24, 2014, 18:14
TGHT has gone up to 725A/13.2V. Temp measured at 1740C (+250C = ~2000C). Pressure gone up to 5.5e-6 Torr and it's coming down slowly.
Will continue heating at this temperature for a few hours; then cool down afterward.
Wednesday, September 24, 2014, 18:56
Temperature is pretty stable at 1740C on Mikron, and pressure is still coming down, currently at 2.9e-6 Torr.
Slow ramping down TGHT at 1.0A/min. The chamber should be ready for venting tomorrow.
Target boat will be inspected.
Thursday, September 25, 2014, 17:25.
The boat was inspected and it turned out great! The coating was fully sintered and there is no sign of damage on the boat.
See the link for photos.
https://www.dropbox.com/sh/m7ycqhkj4avfull/AABHVTweTsP4ajeWZ6uoY010a?dl=0
|
158
|
Thursday, September 25, 2014, 17:35 |
John Wong | Endcaps | 40282-5 | TARGET BOAT | Done | Sintering Ta-coated endcaps (temp measured) | Thursday, September 25, 2014, 17:32
Target boat is filled with Ta-coated endcaps. The caps are stacked together. In between each cap, a piece of graphite foil is used for separation so the Ta caps would not fused.
See link for photos:
https://www.dropbox.com/sh/rydtdho6ggh4l3l/AAAYmvqT0mVQ_pnz4iecS4ksa?dl=0
The boat is wrapped with 3-layers of heatshields. The chamber is currently being pumped down.
TGHT will be ramped up to 580A and the temperature will be measured.
Monday, September 29, 2014, 11:12
TGHt was stepped up to 40A on last Friday and chamber continues to pump down over the weekend.
Vac @ 2.56e-6 Torr, mp @ 19mTorr.
Ramping up TGHT 580A at 1.0A/min.
Monday, September 29, 2014, 11:50
TGHT tripped off at 53A. Reduce ramping rate to 0.5A/min for now.
Monday, September 29, 2014, 16:17
Vacuum is coming down to 9.5e-7 Torr. Increased ramping rate to 1.0A/min.
Tuesday, September 30, 2014, 11:59
TGHT reached to 580A/10.18V. Target has been heated at that current for almost 12 hrs. Vac @ 4.9e-7 Torr.
Local temp measured with Mikron = (1500C + 250 C correction) = 1750C
Cooling down at 2A/min.
Thursday, October 02, 2014, 11:13
The coating is fully sintered; no sign of any damage on the endcaps.
Process is successful.
|
160
|
Thursday, October 02, 2014, 11:52 |
Laura Lambert | Empty | 40282-5 | LP-SIS | In progress | Sintering TaC coating container for UCx#11 | Thursday, October 02, 2014, 11:51
Target container sprayed with TaC, currently drying in fume hood
Monday, October 06, 2014, 12:11
Target container & back block is wrapped with 3 layers of Ta-heat shield. The chamber has been pumped down over the weekend.
Pressure currently at 2.23e-7 Torr.
HS water valves open; no leaks detected.
TGHT will be ramped up to 580A at 0.2A/min
TBHT will be ramped up to 230A at 0.2A/min.
|
162
|
Monday, October 06, 2014, 12:17 |
John Wong | Empty | 40282-5 | LP-SIS | In progress | Sintering TaC coating container for UCx#11 (temp measured with OMEGA 2IR) |
Laura Lambert wrote: |
Thursday, October 02, 2014, 11:51
Target container sprayed with TaC, currently drying in fume hood
Monday, October 06, 2014, 12:11
Target container & back block is wrapped with 3 layers of Ta-heat shield. The chamber has been pumped down over the weekend.
Pressure currently at 2.23e-7 Torr.
HS water valves open; no leaks detected.
TGHT will be ramped up to 580A at 0.2A/min
TBHT will be ramped up to 230A at 0.2A/min.
|
Monday, October 06, 2014, 12:16
Stepped up both TGHT/TBHT to 35A.
Tuesday, October 07, 2014, 12:54
TBHT reached to 230A/3.7V and TGHT is still ramping up, currently at 303A/4.5V. Temp measured with Omega-IR2 = 1165C with e'=0.85
Pressure @ 5.2e-7 Torr.
Increase ramping rate to 2A/min.
Tuesday, October 07, 2014, 16:21
TGHT is now at 580A and TGHT at 230A.
Temperature is measured with OMEGA-IR2, MIKRON, and analog pyrometer - All the measurements are agreed at 1700C (without the tantalum emissivity correction of 250C)
The OMEGA-IR2 slope has changed to 0.97 for the correction - The real temperature reading from the display is showing 1935C.
Now... attempting to low TBHT to see any temperature change.
Tuesday, October 07, 2014, 17:01
TGHT @ 580A.
TBHT = 180C, Temp = 1925C
TBHT = 130C, Temp = 1920C
Not much of change in the temperature on the target tube...
Tuesday, October 07, 2014, 17:07
Attempting to increase the temperature to 2000C
TGHT = 600A, Temp = 1955C
TGHT = 620A, Temp = 2000C
Target will continue heating at this temperature overnight... Will continue to monitor.
Tuesday, October 07, 2014, 20:59
After almost 4 hours of heating at 620A on TGHT, the temperature has dropped to 1980C.
Pressure is coming down to 1.17e-6 Torr.
Increased TGHT to 630A to maintain temp @ 2000C
|
163
|
Wednesday, October 08, 2014, 11:51 |
Laura Lambert | Empty | 40282-5 | LP-SIS | Done | Sintering TaC coating container for UCx#11 (temp measured with OMEGA 2IR) |
John Wong wrote: |
Laura Lambert wrote: |
Thursday, October 02, 2014, 11:51
Target container sprayed with TaC, currently drying in fume hood
Monday, October 06, 2014, 12:11
Target container & back block is wrapped with 3 layers of Ta-heat shield. The chamber has been pumped down over the weekend.
Pressure currently at 2.23e-7 Torr.
HS water valves open; no leaks detected.
TGHT will be ramped up to 580A at 0.2A/min
TBHT will be ramped up to 230A at 0.2A/min.
|
Monday, October 06, 2014, 12:16
Stepped up both TGHT/TBHT to 35A.
Tuesday, October 07, 2014, 12:54
TBHT reached to 230A/3.7V and TGHT is still ramping up, currently at 303A/4.5V. Temp measured with Omega-IR2 = 1165C with e'=0.85
Pressure @ 5.2e-7 Torr.
Increase ramping rate to 2A/min.
Tuesday, October 07, 2014, 16:21
TGHT is now at 580A and TGHT at 230A.
Temperature is measured with OMEGA-IR2, MIKRON, and analog pyrometer - All the measurements are agreed at 1700C (without the tantalum emissivity correction of 250C)
The OMEGA-IR2 slope has changed to 0.97 for the correction - The real temperature reading from the display is showing 1935C.
Now... attempting to low TBHT to see any temperature change.
Tuesday, October 07, 2014, 17:01
TGHT @ 580A.
TBHT = 180C, Temp = 1925C
TBHT = 130C, Temp = 1920C
Not much of change in the temperature on the target tube...
Tuesday, October 07, 2014, 17:07
Attempting to increase the temperature to 2000C
TGHT = 600A, Temp = 1955C
TGHT = 620A, Temp = 2000C
Target will continue heating at this temperature overnight... Will continue to monitor.
Tuesday, October 07, 2014, 20:59
After almost 4 hours of heating at 620A on TGHT, the temperature has dropped to 1980C.
Pressure is coming down to 1.17e-6 Torr.
Increased TGHT to 630A to maintain temp @ 2000C
|
Wednesday, October 08, 2014, 11:46
Temperature readout from omega-IR2C = 2054C
TGHT = 11.14V, 628.0A
TBHT = 2.01V, 129.8A
IGP1 = 8.2e-7Torr
Initiating auto-cool for TGHT @ 2A/min, TBHT @ 1A/min
Thursday, October 09, 2014, 16:00
vented in air and opened up this morning
target container looks good!
|
165
|
Thursday, October 09, 2014, 16:37 |
John Wong | Empty | 40282-5 | LP-SIS | Done | Sintering TaC coating container for UCx#11 (temp measured with OMEGA 2IR) |
Laura Lambert wrote: |
John Wong wrote: |
Laura Lambert wrote: |
Thursday, October 02, 2014, 11:51
Target container sprayed with TaC, currently drying in fume hood
Monday, October 06, 2014, 12:11
Target container & back block is wrapped with 3 layers of Ta-heat shield. The chamber has been pumped down over the weekend.
Pressure currently at 2.23e-7 Torr.
HS water valves open; no leaks detected.
TGHT will be ramped up to 580A at 0.2A/min
TBHT will be ramped up to 230A at 0.2A/min.
|
Monday, October 06, 2014, 12:16
Stepped up both TGHT/TBHT to 35A.
Tuesday, October 07, 2014, 12:54
TBHT reached to 230A/3.7V and TGHT is still ramping up, currently at 303A/4.5V. Temp measured with Omega-IR2 = 1165C with e'=0.85
Pressure @ 5.2e-7 Torr.
Increase ramping rate to 2A/min.
Tuesday, October 07, 2014, 16:21
TGHT is now at 580A and TGHT at 230A.
Temperature is measured with OMEGA-IR2, MIKRON, and analog pyrometer - All the measurements are agreed at 1700C (without the tantalum emissivity correction of 250C)
The OMEGA-IR2 slope has changed to 0.97 for the correction - The real temperature reading from the display is showing 1935C.
Now... attempting to low TBHT to see any temperature change.
Tuesday, October 07, 2014, 17:01
TGHT @ 580A.
TBHT = 180C, Temp = 1925C
TBHT = 130C, Temp = 1920C
Not much of change in the temperature on the target tube...
Tuesday, October 07, 2014, 17:07
Attempting to increase the temperature to 2000C
TGHT = 600A, Temp = 1955C
TGHT = 620A, Temp = 2000C
Target will continue heating at this temperature overnight... Will continue to monitor.
Tuesday, October 07, 2014, 20:59
After almost 4 hours of heating at 620A on TGHT, the temperature has dropped to 1980C.
Pressure is coming down to 1.17e-6 Torr.
Increased TGHT to 630A to maintain temp @ 2000C
|
Wednesday, October 08, 2014, 11:46
Temperature readout from omega-IR2C = 2054C
TGHT = 11.14V, 628.0A
TBHT = 2.01V, 129.8A
IGP1 = 8.2e-7Torr
Initiating auto-cool for TGHT @ 2A/min, TBHT @ 1A/min
Thursday, October 09, 2014, 16:00
vented in air and opened up this morning
target container looks good!
|
Thursday, October 09, 2014, 16:36
Photos for the OMEGA-IR2C temp measurement can be found on this link (see also the subfolder for the heating process):
https://www.dropbox.com/sh/n5sxcepg7e847xw/AACMubuKW1idd49D1Nz_0diNa?dl=0 |
195
|
Monday, May 25, 2015, 17:08 |
John Wong | Empty | 40282-5 | TARGET BOAT | In progress | Sintering TaC coating on Ta target boat |
Laura Lambert wrote: |
Friday, May 22, 2015, 11:43
A target boat was sprayed with TaC coating and let dry yesterday.
The target boat is wrapped with 3-layers of Ta-heat shield.
The boat was installed in EVAP2, chamber is currently being pumped down.
Friday, May 22, 2015, 14:22
HS water valves opened, no leaks detected.
IGP1 = 2.4e-6 Torr.
Tapping up manually...
Friday, May 22, 2015, 14:33
Tapped up to 20A.
Vacuum jumped up to 7e-6 Torr.
Backed off to 5A before vacuum started to drop again.
IGP1 = 5e-6 Torr.
Tapping up manually again...just more slowly...
Friday, May 22, 2015, 15:31
Tapped up to 12A, unable to tap up very fast due to volatile content in coating.
IGP1 = 3.6e-6 Torr.
Initiating auto-ramp at 0.1A/min with a max current of 580A.
Monday, May 25, 2015, 09:03
IGP1 = 3e-7 Torr.
TGHT = 397.5A, 6.43V
Increasing ramping rate to 1.0A/min.
|
Monday, May 25, 2015, 17:06
TGHT at been at 580A for over 4 hours. Cooling down in process at 1A/min.
|
196
|
Tuesday, May 26, 2015, 13:05 |
Laura Lambert | Empty | 40282-5 | TARGET BOAT | Done | Sintering TaC coating on Ta target boat |
John Wong wrote: |
Laura Lambert wrote: |
Friday, May 22, 2015, 11:43
A target boat was sprayed with TaC coating and let dry yesterday.
The target boat is wrapped with 3-layers of Ta-heat shield.
The boat was installed in EVAP2, chamber is currently being pumped down.
Friday, May 22, 2015, 14:22
HS water valves opened, no leaks detected.
IGP1 = 2.4e-6 Torr.
Tapping up manually...
Friday, May 22, 2015, 14:33
Tapped up to 20A.
Vacuum jumped up to 7e-6 Torr.
Backed off to 5A before vacuum started to drop again.
IGP1 = 5e-6 Torr.
Tapping up manually again...just more slowly...
Friday, May 22, 2015, 15:31
Tapped up to 12A, unable to tap up very fast due to volatile content in coating.
IGP1 = 3.6e-6 Torr.
Initiating auto-ramp at 0.1A/min with a max current of 580A.
Monday, May 25, 2015, 09:03
IGP1 = 3e-7 Torr.
TGHT = 397.5A, 6.43V
Increasing ramping rate to 1.0A/min.
|
Monday, May 25, 2015, 17:06
TGHT at been at 580A for over 4 hours. Cooling down in process at 1A/min.
|
Vented in air and opened up this morning.
Target boat looks good! fully sintered!  |
197
|
Tuesday, May 26, 2015, 13:57 |
Laura Lambert | Endcaps | 40282-5 | TARGET BOAT | In progress | Sintering TaC coating on Ta endcaps | Tuesday, May 26, 2015, 13:06
Endcaps were sprayed with TaC coating and let dry.
Each endcap is wrapped separately with a sheet of graphite foil and stacked in the target boat [see image]
The target boat is wrapped with 3-layers of Ta-heat shield.
The boat is installed in EVAP2, chamber is currently being pumped down.
Wednesday, May 27, 2015, 08:50
HS water valves opened, no leaks detected.
Stepped up manually to 35A.
Initiated auto-ramp at 0.2A/min yesterday afternoon.
TGHT = 254A, 3.56V.
IGP1 = 5.9e-7 Torr.
Increasing ramping rate to 1.0A/min with a max setpoint of 400A.
|
198
|
Wednesday, May 27, 2015, 17:58 |
John Wong | Endcaps | 40282-5 | TARGET BOAT | In progress | Sintering TaC coating on Ta endcaps |
Laura Lambert wrote: |
Tuesday, May 26, 2015, 13:06
Endcaps were sprayed with TaC coating and let dry.
Each endcap is wrapped separately with a sheet of graphite foil and stacked in the target boat [see image]
The target boat is wrapped with 3-layers of Ta-heat shield.
The boat is installed in EVAP2, chamber is currently being pumped down.
Wednesday, May 27, 2015, 08:50
HS water valves opened, no leaks detected.
Stepped up manually to 35A.
Initiated auto-ramp at 0.2A/min yesterday afternoon.
TGHT = 254A, 3.56V.
IGP1 = 5.9e-7 Torr.
Increasing ramping rate to 1.0A/min with a max setpoint of 400A.
|
Wednesday, May 27, 2015, 17:51
TGHT has been at 400A for almost 6 hours. Temp at 1500C.
Cooling down to 0A at 1A/min.
Chamber will be vented to inspect the caps.
May have to remove the graphite foil wrapped on the caps and re-sintered the caps to 1800C.
|
199
|
Thursday, May 28, 2015, 10:23 |
Laura Lambert | Endcaps | 40282-5 | TARGET BOAT | Problems | Sintering TaC coating on Ta endcaps - not fully sintered |
John Wong wrote: |
Laura Lambert wrote: |
Tuesday, May 26, 2015, 13:06
Endcaps were sprayed with TaC coating and let dry.
Each endcap is wrapped separately with a sheet of graphite foil and stacked in the target boat [see image]
The target boat is wrapped with 3-layers of Ta-heat shield.
The boat is installed in EVAP2, chamber is currently being pumped down.
Wednesday, May 27, 2015, 08:50
HS water valves opened, no leaks detected.
Stepped up manually to 35A.
Initiated auto-ramp at 0.2A/min yesterday afternoon.
TGHT = 254A, 3.56V.
IGP1 = 5.9e-7 Torr.
Increasing ramping rate to 1.0A/min with a max setpoint of 400A.
|
Wednesday, May 27, 2015, 17:51
TGHT has been at 400A for almost 6 hours. Temp at 1500C.
Cooling down to 0A at 1A/min.
Chamber will be vented to inspect the caps.
May have to remove the graphite foil wrapped on the caps and re-sintered the caps to 1800C.
|
Thursday, May 28, 2015, 08:13
Vented in air and opened up this morning.
Not fully sintered [see pictures]
|
200
|
Thursday, May 28, 2015, 11:36 |
Laura Lambert | Endcaps | 40282-5 | TARGET BOAT | In progress | Sintering TaC coating on Ta endcaps - round 2 | Thursday, May 28, 2015, 11:34
Endcaps were sintered [see elog#199]
A Ta foil is placed in the target boat with separate slots for each endcap [see image]
The target boat is wrapped with 3-layers of Ta-heat shield.
The boat is installed in EVAP2, chamber is currently being pumped down.
Thursday, May 28, 2015, 14:01
HS water valves opened, no leaks detected.
IGP1 = 1.4e-6 Torr.
Initiating manual tap up.
Thursday, May 28, 2015, 15:10
Manually tapped up TGHT to 108A, 1.1V
Initiating auto-ramp at 2.0A/min with a max setpoint of 300A
Thursday, May 28, 2015, 15:22
Hoping to speed up the process...
IGP1 = 1.0e-6 Torr.
Increasing ramping rate to 4.0A/min with a max setpoint of 500A
Final desired temperature = 1800C
|
201
|
Thursday, May 28, 2015, 17:50 |
John Wong | Endcaps | 40282-5 | TARGET BOAT | Done | Sintering TaC coating on Ta endcaps - round 2 |
Laura Lambert wrote: |
Thursday, May 28, 2015, 11:34
Endcaps were sintered [see elog#199]
A Ta foil is placed in the target boat with separate slots for each endcap [see image]
The target boat is wrapped with 3-layers of Ta-heat shield.
The boat is installed in EVAP2, chamber is currently being pumped down.
Thursday, May 28, 2015, 14:01
HS water valves opened, no leaks detected.
IGP1 = 1.4e-6 Torr.
Initiating manual tap up.
Thursday, May 28, 2015, 15:10
Manually tapped up TGHT to 108A, 1.1V
Initiating auto-ramp at 2.0A/min with a max setpoint of 300A
Thursday, May 28, 2015, 15:22
Hoping to speed up the process...
IGP1 = 1.0e-6 Torr.
Increasing ramping rate to 4.0A/min with a max setpoint of 500A
Final desired temperature = 1800C
|
Thursday, May 28, 2015, 17:42
TGHT at 500A. Temp at 1780C.
Increased TGHT to 580A (online operating current), Temp 1945C, vac 2.9e-6 torr and coming down. Will remain at that current for the sintering process.
Cooling it down later this evening.
Thursday, May 28, 2015, 21:27
Temp stabilized at 1960C with TGHT at 580A for almost 4 hours. Vacuum at 1.8e-7 Torr.
Cooling down initiated at 2A/min.
|
202
|
Friday, May 29, 2015, 11:18 |
Laura Lambert | Endcaps | 40282-5 | TARGET BOAT | Done | Sintering TaC coating on Ta endcaps - round 2 |
John Wong wrote: |
Laura Lambert wrote: |
Thursday, May 28, 2015, 11:34
Endcaps were sintered [see elog#199]
A Ta foil is placed in the target boat with separate slots for each endcap [see image]
The target boat is wrapped with 3-layers of Ta-heat shield.
The boat is installed in EVAP2, chamber is currently being pumped down.
Thursday, May 28, 2015, 14:01
HS water valves opened, no leaks detected.
IGP1 = 1.4e-6 Torr.
Initiating manual tap up.
Thursday, May 28, 2015, 15:10
Manually tapped up TGHT to 108A, 1.1V
Initiating auto-ramp at 2.0A/min with a max setpoint of 300A
Thursday, May 28, 2015, 15:22
Hoping to speed up the process...
IGP1 = 1.0e-6 Torr.
Increasing ramping rate to 4.0A/min with a max setpoint of 500A
Final desired temperature = 1800C
|
Thursday, May 28, 2015, 17:42
TGHT at 500A. Temp at 1780C.
Increased TGHT to 580A (online operating current), Temp 1945C, vac 2.9e-6 torr and coming down. Will remain at that current for the sintering process.
Cooling it down later this evening.
Thursday, May 28, 2015, 21:27
Temp stabilized at 1960C with TGHT at 580A for almost 4 hours. Vacuum at 1.8e-7 Torr.
Cooling down initiated at 2A/min.
|
Friday, May 29, 2015, 11:16
Vented in air and opened up this morning.
Endcaps look great! 
Sintering was spot on [see pictures]
|
230
|
Monday, July 13, 2015, 11:54 |
Laura Lambert | Endcaps | 40282-5 | TARGET BOAT | Problems | Sintering TaC coating on Ta endcaps | Monday, July 13, 2015, 11:53
A Ta foil is placed in the target boat with separate slots for each endcap [same as elog 200]
The target boat is wrapped with 3-layers of Ta-heat shield.
The boat is installed in EVAP2, chamber is currently being pumped down.
Monday, July 13, 2015, 15:00
Opened HS water valves, no leaks detected.
IGP1 = 2.7e-6 Torr.
Tapping up manually.
Monday, July 13, 2015, 15:41
Tapped up manually to 30A
TGHT = 30A, 0.05V
IGP1 = 7e-6 Torr.
Initiating auto-ramp at 0.2A/min up to 480A with a final desired temperature of 1800C
Tuesday, July 14, 2015, 09:12
IGP1 = 7.8e-7 Torr
TGHT = 241A, 3.3V
OMEGA = 1010C
Increasing auto-ramp to 2.0A/min
Tuesday, July 14, 2015, 11:12
Reached final setpoint of TGHT = 480A, 8.43V
OMEGA = 1667C
IGP1 = 3.3e-6 Torr.
Tapping up manually to reach final desired temperature of 1800C.
Tuesday, July 14, 2015, 11:33
Reached TGHT = 500A, 8.8V by tapping up manually.
OMEGA = 1714V
IGP1= 3.5e-6 Torr.
Re-initiating auto-ramp at 2.0A/min with a final setpoint of 580A.
New final desired temperature min of 1900C
Tuesday, July 14, 2015, 13:16
TGHT = 577A, 10.74V
OMEGA = 1938C
IGP1 = 3.2e-6 Torr
Endcaps have been at this temperature for just over an hour.
Spikes in vacuum started ~430A - this is due to the green TaC coating reacting with the Ta foil, the carbide is reacting directly with the Ta foil [see picture]
Stopping sintering early before endcaps break -> initiating auto-cool at 2.0A/min.
Wednesday, July 15, 2015, 11:33
Vented in air and took out this morning.
Endcaps sintered on top side but not fully sintered on inner edge.
Inner edge is peeling off and unsintered green TaC.
The coating peeling off did not shrink, as seen with previous tests done, one would expect a shrinkage in the coating when heated.
The peeling is most likely due to the way to endcaps were placed in the slots of the Ta foil.
This may have cause the foil to be hotter than the inside of the endcaps and subsequently the Ta foil and TaC coating on the inside reacted - with the Ta foil extracting the carbide from the coating.
This would cause the outer edges of the inside of the endcap to peel/curl inwards as it was heated [like a cast, as the cast dries the outer edges curl inwards].
See photos attached for clarification.
Endcaps will be re-coated and sintered again via a different procedure.
|
380
|
Wednesday, July 19, 2017, 13:55 |
Marla Cervantes | | 40282-5 | TARGET BOAT | Done | Sintering La(OH)3/C discs | Wednesday, July 19, 2017, 13:44
Discs previously casted by Marla and Pauline and weighed.
Discs are placed inside a small graphite container.
Graphite container with discs loaded with 30 discs was loaded into Ta-boat previously coated with TaC.
Ta-boat is wrapped with 3 Ta heat shields.
Loaded in evaporator 2.
Chamber currently pumping down.
Thursday, July 20, 2017, 16:07
HS water valves were opened in the morning, no leaks were detected.
Perform water test to confirm paddle wheels are working well.
Current was tapped manually to 40 A.
Read out on meter confirmed paddle wheels are registering
Tap back down to 20 A, tripped off system on purpose by closing HS water valves.
TGHT tripped off as expected.
Water flow test was good, initiating ramp up of samples.
Taped manually to 40 A.
After the stabilization of the vacuum auto ramping was set up to 0.2 A/min.
Up to a final set up point of 250 A.
Final desired temperature ~1800 C.
Friday, July 21, 2017, 10:20
Final set up from July 20 was reached.
Current reading: 244.6 A.
Voltage reading: 3.82 V.
Temperature reached: 1105 C.
Final set up was change to 1500 A.
The temperature reached at 6 pm was 1936 C so the current was decreased to 488 A.
The final temperature after 30 min was 1800 C.
The set up stayed the same for the weekend.
Monday, July 24, 2017, 13:06
Temperature reading in the morning was 1856 C.
TGHT: 487.87 A, 9.07 V
TGHT power supply:
IGP1: 3.75e-7 Torr
IGP2: 3.51e-7 Torr
Started to ramp down at 1 A/min rate.
Initiating auto cooling at 1.0A/min for TGHT.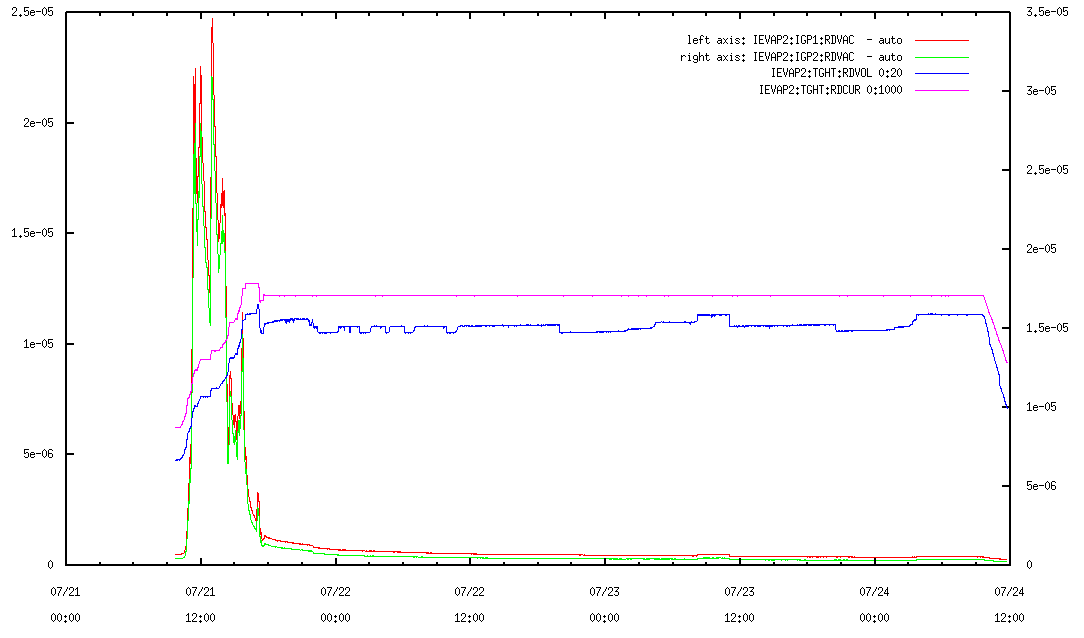
Tuesday, July 25, 2017, 09:27
LaC2/C discs were taken off of evap2.
LaC2/C discs were brought in to glove box.
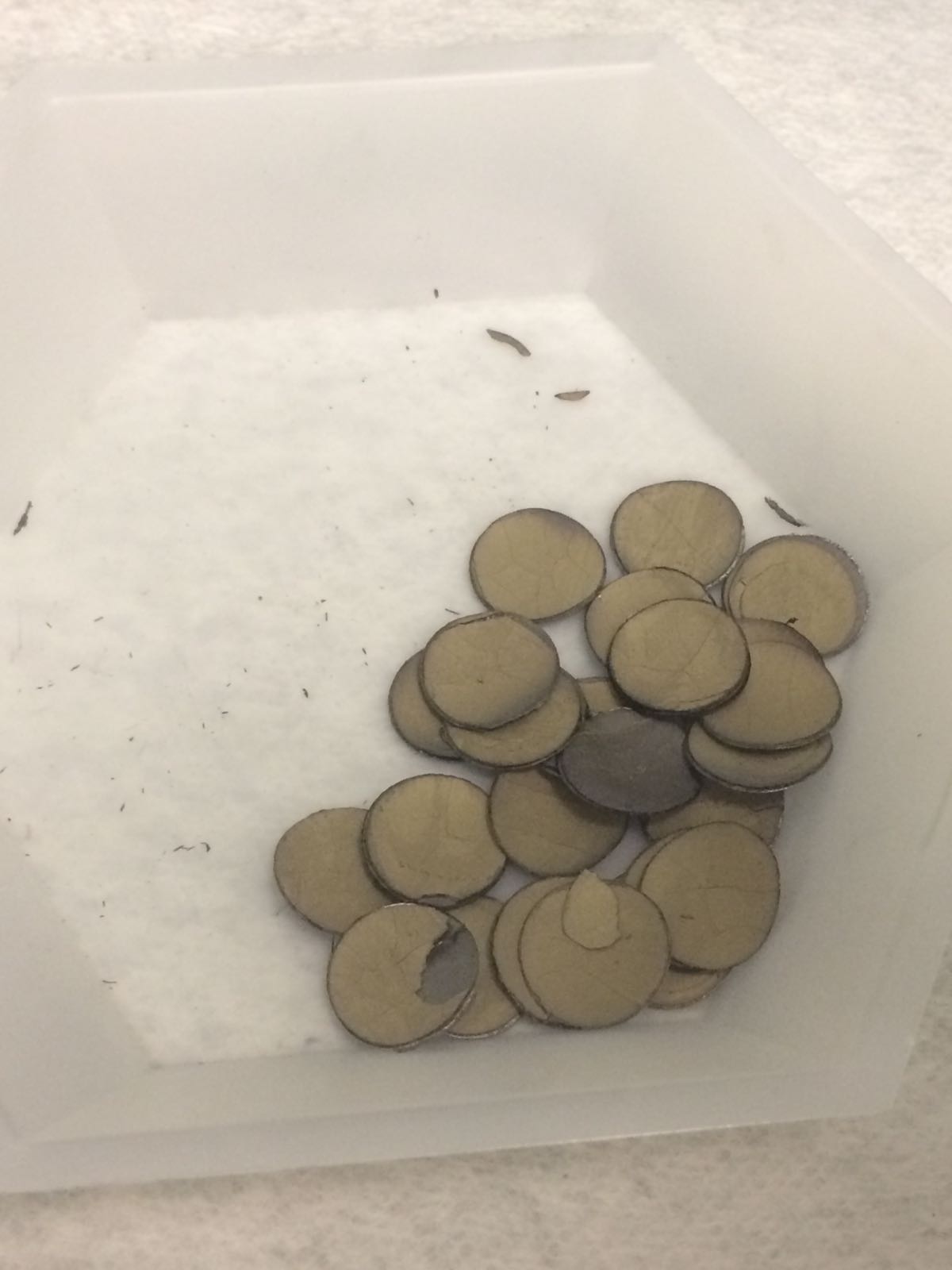
|
382
|
Wednesday, August 02, 2017, 16:12 |
Marla Cervantes | | 40282-5 | | Done | Sintering La(OH)3/C pellets | Monday, July 31, 2017,
Pellets previously pressed by Marla and Pauline.
Pellets are placed inside a small graphite container.
Graphite container loaded with 5 pellets was loaded into Ta-boat previously coated with TaC.
Ta-boat is wrapped with 3 Ta heat shields.
Loaded in evaporator 2.
Tuesday, August 01, 2017,
Chamber pumping down.
Wednesday, August 02, 2017, 16:03
HS water valves were opened, no leaks were detected.
Current was tapped manually to 40 A.
After the stabilization of the vacuum auto ramping was set up to 0.5 A/min.
Up to a final set up point of 300 A.
Final desired temperature ~1700 C.
|
383
|
Friday, August 04, 2017, 10:52 |
Laura Lambert | | 40282-5 | TARGET BOAT | Problems | Sintering La(OH)3/C pellets |
Marla Cervantes wrote: |
Monday, July 31, 2017,
Pellets previously pressed by Marla and Pauline.
Pellets are placed inside a small graphite container.
Graphite container loaded with 5 pellets was loaded into Ta-boat previously coated with TaC.
Ta-boat is wrapped with 3 Ta heat shields.
Loaded in evaporator 2.
Tuesday, August 01, 2017,
Chamber pumping down.
Wednesday, August 02, 2017, 16:03
HS water valves were opened, no leaks were detected.
Current was tapped manually to 40 A.
After the stabilization of the vacuum auto ramping was set up to 0.5 A/min.
Up to a final set up point of 300 A.
Final desired temperature ~1700 C.
|
Friday, August 04, 2017, 10:20
evap2 tripped twice yesterday.
1st trip) there was a power bump which caused a trip at ~4:20pm, this can be seen in the striptool image attached.
-TGHT spiked to zero, but immediately went back to the ~420A it was sitting at at the time.
-This did not initiate a full trip of everything, but a visual spike in the system can be seen
-Oddly this was not picked up in archives - happened so fast and must have been in the small time frame it was not picking up information
-Did TGHT actually drop to zero followed by then applying an immediate 420A?
-Or did it simple not register a reading due to power bump?
2nd trip) IGP1 stopped communicating at ~5:45pm, this can be seen in both the archives, striptool and evap2 control screenshot images attached
-IGP1 was fine, vacuum was good
-Registering good vacuum in epics - can see in screen shot vacuum was still good but IGP1 turned yellow as if turned off
-This resulted in TP followed by BV tripping off due to no longer getting a vacuum reading making the TP think there was a bad vacuum.
-Possible miscommunication with PLC?
-This is the same scenario that happened on mon - see elog i.d. 381
Will follow up when more information acquired...
|
384
|
Friday, August 04, 2017, 14:09 |
Laura Lambert | | 40282-5 | TARGET BOAT | Done | Sintering La(OH)3/C pellets |
Laura Lambert wrote: |
Marla Cervantes wrote: |
Monday, July 31, 2017,
Pellets previously pressed by Marla and Pauline.
Pellets are placed inside a small graphite container.
Graphite container loaded with 5 pellets was loaded into Ta-boat previously coated with TaC.
Ta-boat is wrapped with 3 Ta heat shields.
Loaded in evaporator 2.
Tuesday, August 01, 2017,
Chamber pumping down.
Wednesday, August 02, 2017, 16:03
HS water valves were opened, no leaks were detected.
Current was tapped manually to 40 A.
After the stabilization of the vacuum auto ramping was set up to 0.5 A/min.
Up to a final set up point of 300 A.
Final desired temperature ~1700 C.
|
Friday, August 04, 2017, 10:20
evap2 tripped twice yesterday.
1st trip) there was a power bump which caused a trip at ~4:20pm, this can be seen in the striptool image attached.
-TGHT spiked to zero, but immediately went back to the ~420A it was sitting at at the time.
-This did not initiate a full trip of everything, but a visual spike in the system can be seen
-Oddly this was not picked up in archives - happened so fast and must have been in the small time frame it was not picking up information
-Did TGHT actually drop to zero followed by then applying an immediate 420A?
-Or did it simple not register a reading due to power bump?
2nd trip) IGP1 stopped communicating at ~5:45pm, this can be seen in both the archives, striptool and evap2 control screenshot images attached
-IGP1 was fine, vacuum was good
-Registering good vacuum in epics - can see in screen shot vacuum was still good but IGP1 turned yellow as if turned off
-This resulted in TP followed by BV tripping off due to no longer getting a vacuum reading making the TP think there was a bad vacuum.
-Possible miscommunication with PLC?
-This is the same scenario that happened on mon - see elog i.d. 381
Will follow up when more information acquired...
|
Friday, August 04, 2017, 14:05
Vented in air and transferred to glove box today.
Container did not break.
Some wires in PLC were not creating a good contact - could be problem re: IGP1 tripping off.
Wires replaced by Gelo.
Put back under vacuum with nothing loaded over weekend to see how things run...
|
|