ID |
Date |
Author |
Operational Mode |
Subject |
195
|
Wed May 2 16:28:16 2007 |
Doug Preddy | Normal Running | Energizing solenoid to 500 amps |
Power supply initially would not ramp up. I exercised the rate control
selector switch and found that the power supply would ramp up at only the
30 minute setting. It is ramping up at a rate of about 60 minutes. |
203
|
Sat Jun 16 15:05:03 2007 |
Doug Preddy | Normal Running | Solenoid power lead temp problem |
Power lead temps rippling and increasing. I asked an operator to cycle
HIC142. This seems to have fixed the problem (for now). |
205
|
Sun Jul 1 16:09:37 2007 |
Doug Preddy | Normal Running | M9B:DP2 tripped off |
Diffusion pump tripped off and vacuum (and power lead temps) going up. I
had an experimentor cycle HIC 142 at 4:15 this morning. When I got in
today I restarted the pump and it is back to 6.0 x 10-7. Power lead temps
also are going down. |
207
|
Thu Jul 5 03:04:50 2007 |
Doug Preddy | Normal Running | Power lead problems |
The power leads temps are starting to cycle again. Earlier today M9
experimentor cycled HIC142 to stablize the oscillations. They started
again early this morning, so cycled HIC142 again. Oscillations died back,
but are still present. Will try and warm the power leads later today when
the experiment's sample is changed. |
212
|
Tue Jul 31 07:53:57 2007 |
Kevin Trithardt | Normal Running | cycled power leads |
got a page for the power lead temp
came down and cycled the power leads.. did not seem to make a difference..
Kevin |
215
|
Tue Aug 14 12:55:12 2007 |
Doug Preddy | Normal Running | Strip tool saves |
There are two strip tools saved:
coils
powerlead |
224
|
Tue Oct 2 13:02:37 2007 |
Doug Preddy | Normal Running | PLC problems |
While downloading new code for 2A PLC the M9 and M15 vacuum systems were
shut off. This is due to the two systems piggybacking onto the 2A PLC.
When M9 Epics came back up there was no controls. Eventually I reset the
local/remote switch (thumbwheel #100) to button #1 being on. Mike Leross
added a text and light on the epics vacuum page that says "EPICS works
only when green". If this light is not green, dial thumbwheel #100 and
push button #1. Make sure the light comes on and you should have EPICS
control back.
This caused a glitch in the refrigerator system. It did not trip it off,
but it would have if the solenoid was energised. The panel showed
compressor fault and the temps for TI121, and the powerleads all jumped.
This may be a cause for some of our unknown problems. |
237
|
Fri Nov 23 08:35:37 2007 |
Doug Preddy | Normal Running | power lead problems |
About 10 hours ago the power lead temperatures started to fluctuate and
climb.
I cycled CV142 and the Temps have dropped and stablized. |
238
|
Fri Nov 23 08:41:45 2007 |
Doug Preddy | Normal Running | screen grab of powerlead temps |
|
Attachment 1: Capture.jpg
|
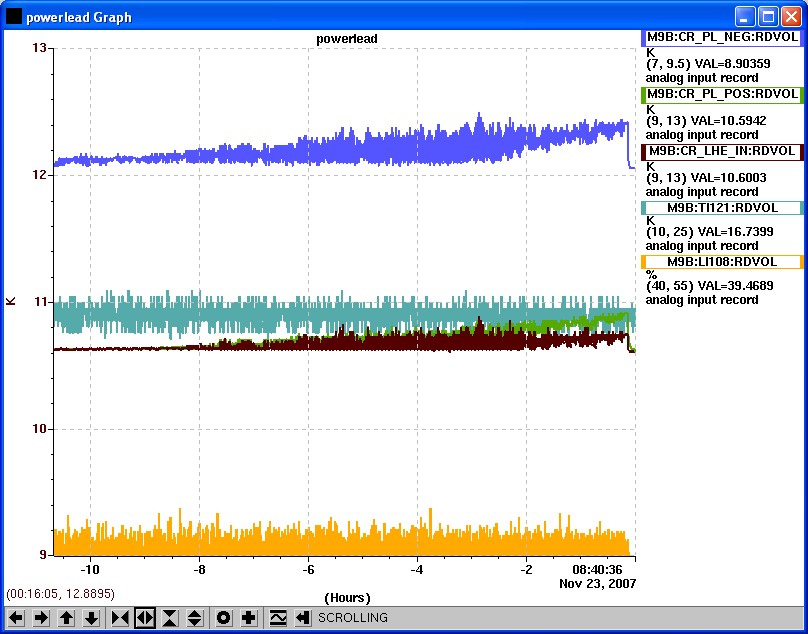 |
239
|
Mon Nov 26 09:45:43 2007 |
Doug Preddy | Normal Running | power lead problems |
Power lead temperatures were rippling yesterday afternoon. I asked one of
the operators to cycle CV142.
The temperatures were rippling again this morning, so I cycled CV142. |
240
|
Tue Nov 27 21:02:08 2007 |
Doug Preddy | Normal Running | power lead ripples |
power leads were oscillating tonight. John K. came down and cycled CV142.
(Thanks John!) Temps settling out. |
244
|
Wed Apr 16 15:12:01 2008 |
Doug Preddy | Normal Running | graphs to load |
There are three strip tools saved:
coils
powerlead
startup |
248
|
Mon Apr 28 09:03:22 2008 |
Doug Preddy | Normal Running | power leads warmed during weekend |
The power lead temperatures suddenly rose on Sunday morning. No rippling occured before the woarm up.
I shut flow off this morning for about 10 minutes (until the LHe in went up to 30K) and then open the flow back up. The temperature seem to be recovering. |
250
|
Tue Jul 15 08:47:13 2008 |
Doug Preddy | Normal Running | Screen grab of normal running |
Solenoid was recovered on Sunday July 13. The power leads started to ripple slightly this morning, so I cycled HIC142. No real change. |
Attachment 1: july_15_08_0841.jpg
|
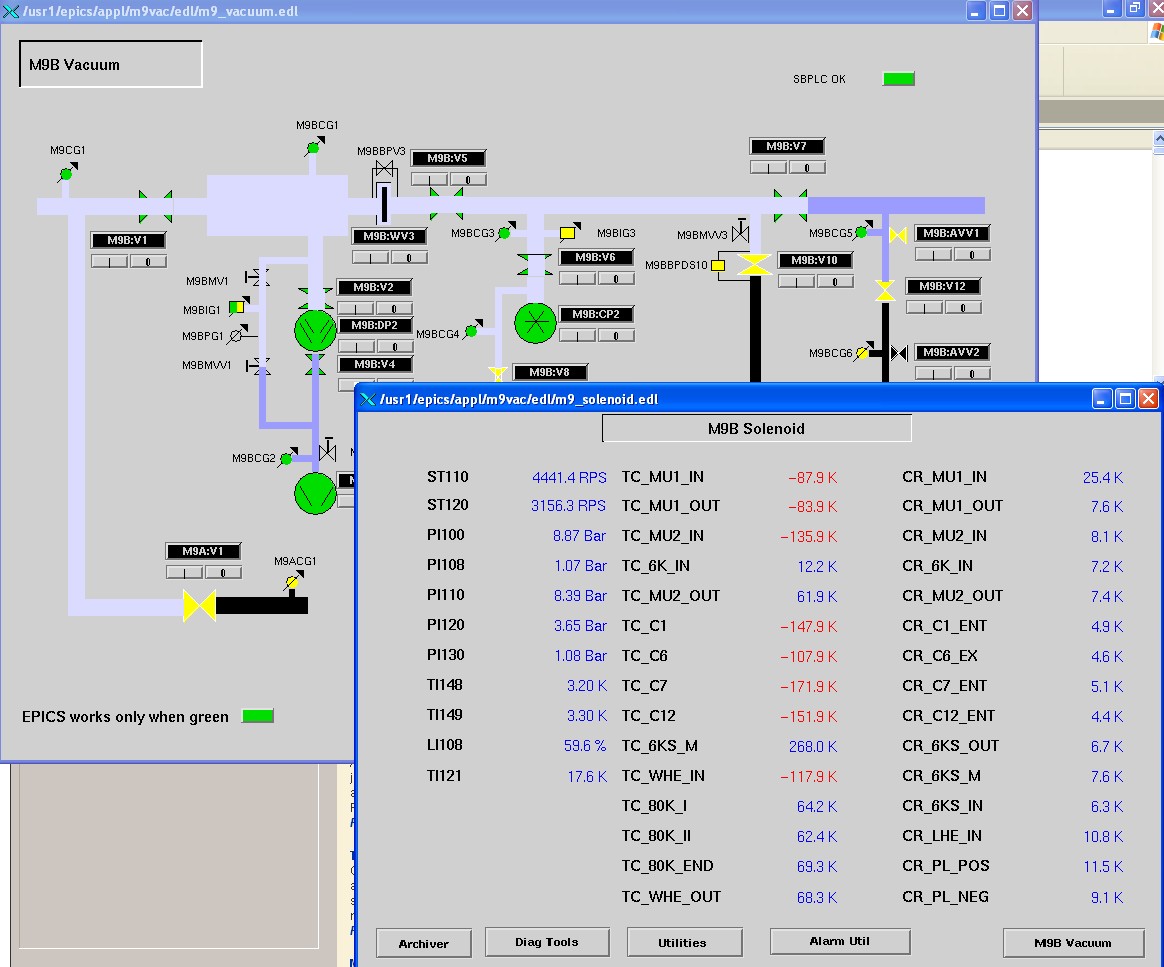 |
Attachment 2: july_15_08_0846.jpg
|
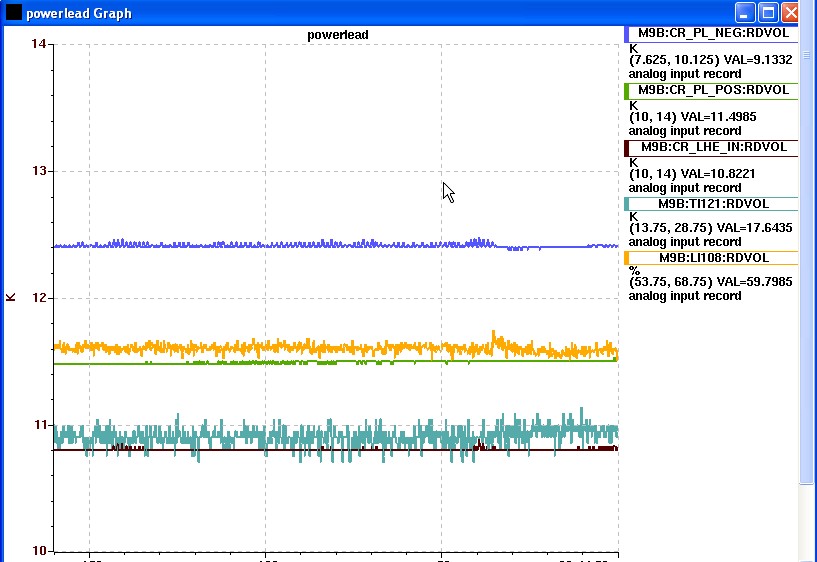 |
257
|
Thu Sep 4 10:02:55 2008 |
Doug Preddy | Normal Running | ramping down solenoid |
Solenoid power supply will be turned off for Fall shutdown. |
262
|
Sun Oct 5 11:12:48 2008 |
Doug Preddy | Normal Running | M9B:V1 interlocks and a IOC crash |
M9A:V1 was removed this shutdown. It's "in" limit is required to allow M9B:V1 to be opened. I have bypassed the interlocks on M9B:V1 until the M9A:V1 limits can be jumpered. Don Dale and George Clark have been informed.
Also an IOC crashed so the data pages were not updating. Evgeny rebooted the IOC. All is now fixed. |
264
|
Wed Nov 5 16:33:52 2008 |
Doug Preddy | Normal Running | sbplc light out |
On main menu the sbplc light was black. All vacuum systems looked good, but there was no control of any device. Jane reset the IOC. It is hosted by sundance. |
273
|
Mon Oct 5 11:54:58 2009 |
Doug Preddy | Normal Running | Switched TIC121 into auto mode |
|
286
|
Fri Nov 12 16:54:50 2010 |
Doug Preddy | Normal Running | Solenoid ramped up |
|
2
|
Fri Dec 19 13:07:25 2003 |
Willy Andersson | Maintenance | To-Do list for M9SOL |
I had distributed this list by email earlier this month. I have added
a few items at the bottom. I am posting it on the M9SOL Elog under
Maintenance. Some of the items may not be achievable or practical but
I thought it would be a useful first attempt at a To-Do list. |
Attachment 1: M9Blist3.txt
|
To-do and To-consider items for M9B superconducting
solenoid/refrigeration system.
- New pressure guages for the Mycom compressor panel. The
present guages are damaged from vibration and do not read
properly. The new guages should be isolated somehow from
vibration.
- Investigate designing and building a compressor oil
heater/conditioner. The helium compressor should be topped up
with "conditioned" oil.
- Have contractor check allignment of compressor motor to
compressor and check flex coupling condition. MYCOM to
recommend contractor. Check condition of and re-grease
compressor motor bearings.
- Replace missing and unreadable identification tags on
valves, piping, and instrumentation throughout the system.
- Identify, catalog and label stored spare parts and equipment
and provide proper storage.
- Provide "Lamp Check" button for main compressor panel.
- Investigate LED type replacement bulbs ( Base Style 24XX )
for Sulzer control panel.
- Update and improve operation manual and maintenance instructions.
- Provide computer control for solenoid power supply to
simplify operation and make it less prone to operator
error.
- Re-arrange locations of vacuum computer and X displays so
that the opportunity of accidently bumping into buttons on Sulzer
panel is reduced.
- Re-write solenoid power supply logic to require that both powerlead
temperatures must be stable and below XX? Kelvin for 60 minutes before
enabling arming the solenoid power supply.
- Increase computer security. Restrict physical access ?
Virus scanner ?
- Look into using Ultra-VNC with encryption for security. Stop
Commute modem access but route Commute access through hard wired
serial connection to PC running Ultra-VNC. Or keep modem access
but use call back method.
- Set up procedure and pipe in convenient sample points for
dewpoint, N2/O2, oil content readings. Sample readings should be
documented prior to starting turbine cooling.
- Upgrade LN2 fill equipment for Purifiers. Can both puifiers
be operated in parallel during a cool down ? Auto-isolation of
purifiers' from helium system when LN2 runs out or fails or
power failure.
- Provide dedicated LN2 line to M9B compressor building ? Guy Stanford
has info on relatively inexpensive efficient foam covering for LN2
lines instead of vacuum jacketed piping.
- Can anything be done about the epoxy fumes from the buffer tank ?
A charcoal/molecular seive filter in the buffer tank line
check-valved for free flow to buffer but filtered flow from buffer ?
- Fix back-up air compressor system.
- Remove any unauthorized taps off of the M9B compressed air line to
other non M9B systems.
- Clean-up of compressor building and clean-up around Sulzer panel.
- Route turbine defrost circuits to outside of shielding blocks.
- Clean-up area behind solenoid power lead flowmeters and pressure
gauge panel. Remove all unused tubing and cables.
- Harden Sulzer control panel against water damage from water leaks
overhead.
- pipe in precision flow control valve and pressure guages on powerlead
flow to main compressor suction line.
- pipe in manual bypass circuit around main coldbox HE in and out
valves.
- New vacuum controller for Sulzer panel. Repair old one for a spare.
- Add in some smart logic to prevent system trip on solenoid vacuum
during a quench recovery cooldown. When solenoid power supply is
not armed solenoid vacuum should be allowed to degrade slightly
( within limits ) from contamination defrosting into solenoid vacuum.
As soon as solenoid power supply is armed then solenoid vacuum trip
set to high vacuum again. Solenoid vacuum trip logic should be re-worked.
- provide vacuum gauge between solenoid vacuum diffpump and BV2.
- provide computer readable indication for:
- CV204 position
- LHe heater reading
- turbine 1 entrance temp.
- Buffer tank line pressure
- air pressure
- position signal to CV211 and CV212
- position of CV151
- position of CV141
- 80K shield heater setting
- purifier LN2 status
- backup air compressor OK
- solenoid vacuum
- solenoid current
- solenoid power supply armed ?
- others ?????
- check oil levels, drive belts etc for system mechanical, diff, and
cryo pumps.
- check calibration of system pressure and temperature sensors.
- repairs and upgrades to Sulzer Control panel instrumentation and
relays
- re-charge TI148 and TI149
- follow-up on improvement requests for X displays for vacuum and solenoid
data.
- compressor water package maintenance and repairs.
- repair compressor building roof leak.
- inspect and clean system air filters and coalesers and water filters.
- buffer tank clean-up and re-paint.
- train more system operators for M9B and ISAC II helium refrigeration
systems ?
- Vacuum gauges on cold box transfer lines ? Or build small portable LN2
trapped vacuum pump station ( probably very usefull for many other
areas at TRIUMF including purifier regeneration in compressor building )
- Should we buy Don Dales' first trip logger ? It is a PLC that is networkable
and may be used for other functions ? Is it obsolete or outdated ?
- Develope a system using a residual gas analyzer for helium gas purity
measurements ?
_____________________________________________________________________________
Items added Dec 19,2003 :
- Sniffer Leak check of piping, especially powerlead insulators.
- Top up gas to system. The lowest helium relief valve setting is
SV45 set at 5 kg/cm^2 Gauge (71.12 psig) so it would be reasonable
to fill the system to 60 psig.
- re-work purifier plumbing, add purge ports at flowmeter. Make
purifiers portable ?
- Make small portable circulation helium compressor + ORS skid ?
- Schedule quarterly steady state vibration measurments for MYCOM
compressor. (Tom Ries has vibration measurement equipment)
_______________________________________________________End of list for now !
|